為了提高滲氮件的承載能力和挖掘滲氮的強化潛力,開發了深層滲氮硬化技術。人們過去認為滲氮層很淺類似于“蛋殼”,有很多誤解,經過多年來滲氮件的應用和滲氮技術的開發,深層滲氮、新滲氮鋼和新滲氮方法的不斷出現,使滲氮工藝在很多場合可以與滲碳工藝相媲美,而且正在發揮著獨特的優勢。
1.深層滲氮硬化技術
深層滲氮和深層硬化相結合,形成了深層滲氮硬化的技術方案,不僅把常規滲層深小于0.4mm提高到0.6~1.0mm,同時實現滲氮表面下0.3~0.5mm處硬度提高到500HV以上,硬度梯度平緩。解決的途徑是采用特殊工藝強化滲氮次表層和提高滲氮基體硬度(強度)。
為此,研發了兩種時效硬化鋼:20CrNi3Mn2Al和20Cr3MnMoV(見表1),開發了深層滲氮硬化工藝。提出了深層滲氮硬化技術的三個相關條件:滲氮層深0.6mm以上,滲氮表面下0.4mm處硬度大于600HV和滲氮基體硬度大于400~450HV(42~46HRC)。
(1)時效硬化鋼
采用時效硬化鋼作為滲氮基體材料,取代常規的調質結構鋼,可以實現不需油淬調質,采用空冷固溶處理代替調質淬火,滲氮和時效兩個工序合一,在滲氮過程中,同時實現滲氮層硬化和基體時效硬化,滲氮表面硬度大于900HV,滲氮基體硬度大于400HV(42HRC)。簡化工藝,顯著提高了滲氮基體硬度。
表1 試驗鋼的化學成分(質量分數)(%)
(2)深層滲氮硬化
為了實現滲氮層深層硬化,必須將時效硬化鋼滲氮硬化和時效硬化兩種機制正確地混合,改變恒溫滲氮為變溫滲氮,滲氮前期以滲氮固溶強化和彌散硬化為主,后期為滲氮硬化和時效硬化疊加。采用離子滲氮工藝,可以充分利用離子轟擊和陰極濺射造成的滲氮表面活化與不斷出現的大量晶體缺陷,有效的加速氮原子的擴散,加快滲氮速度。
以時效硬化鋼20CrNi3Mn2Al為例,與滲氮鋼38CrMoAl普通滲氮和滲碳鋼20CrMnTi常規氣體滲碳淬火的硬化進行對比,如附圖所示,其中20CrNi3Mn2Al鋼經過870℃×3h空冷固溶處理+520~540℃×80h深層離子滲氮,38CrMoAl鋼經過520~530℃×50h離子滲氮,20CrMnTi鋼經過930℃滲碳+850℃油淬。三種材料不同工藝處理結果可以看出,時效硬化鋼20CrNi3Mn2Al深層離子滲氮表面硬度高,表層強化效果顯著,基體硬度高,與滲碳鋼相當,高于38CrMoAl滲氮鋼。表明時效硬化鋼滲氮后有很高的承載能力。
2.齒輪受力分析
齒輪是在接觸疲勞和彎曲疲勞的復雜應力條件下工作,滲氮層次表層承受最大的剪切應力,滲氮層剝落和疲勞破壞往往發生在次表層,因此充分強化滲氮次表層是提高齒輪承載能力的關鍵。
大量國內外試驗研究結果證明,隨著滲氮硬化層層深增加和齒輪心部硬度提高,齒輪接觸疲勞強度和彎曲疲勞強度隨之提高。深層離子滲氮硬化技術,采用時效硬化鋼和深層滲氮硬化,對滲氮齒輪滿足重載復雜應力條件工作是重要保證。
試驗表明,20CrNi3Mn2Al鋼深層離子滲氮后,滲氮表面下0.4mm處硬度大于600HV,滲氮基體硬度為400HV(42HRC)以上。如表2所示。
表2 20CrNi3Mn2Al鋼深層離子滲氮后的硬度和層深
3. 應用展望
推薦20CrNi3Mn2Al鋼作為時效硬化滲氮齒輪鋼,采用深層滲氮硬化技術可滿足滲氮齒輪工作條件的更高要求。
普通調質結構鋼42CrMo、35CrMoV、25Cr2MoV等制造滲氮齒輪,基體硬度低(28~38HRC),次表層硬度低(表面下0.4mm處不超過400~500HV)。時效硬化鋼20CrNi3Mn2Al鋼固溶處理后硬度為30~36HRC,深層離子滲氮后,表面硬度高于900HV,滲氮表面下0.4mm處硬度為600~650HV。基體硬度為40~46HRC,滲層深度為0.7mm以上。
展望用時效硬化鋼制造滲氮齒輪,可以預期有廣闊應用前景。現有調質結構鋼制造的滲氮齒輪,模數不超過10mm,由于時效硬化鋼采用了深層滲氮硬化技術,大大強化了滲氮層和基體,明顯提高了齒輪的承載能力。可以期望時效硬化鋼滲氮齒輪模數會超過10mm,可用來制造重負載高性能齒輪。
1.深層滲氮硬化技術
深層滲氮和深層硬化相結合,形成了深層滲氮硬化的技術方案,不僅把常規滲層深小于0.4mm提高到0.6~1.0mm,同時實現滲氮表面下0.3~0.5mm處硬度提高到500HV以上,硬度梯度平緩。解決的途徑是采用特殊工藝強化滲氮次表層和提高滲氮基體硬度(強度)。
為此,研發了兩種時效硬化鋼:20CrNi3Mn2Al和20Cr3MnMoV(見表1),開發了深層滲氮硬化工藝。提出了深層滲氮硬化技術的三個相關條件:滲氮層深0.6mm以上,滲氮表面下0.4mm處硬度大于600HV和滲氮基體硬度大于400~450HV(42~46HRC)。
(1)時效硬化鋼
采用時效硬化鋼作為滲氮基體材料,取代常規的調質結構鋼,可以實現不需油淬調質,采用空冷固溶處理代替調質淬火,滲氮和時效兩個工序合一,在滲氮過程中,同時實現滲氮層硬化和基體時效硬化,滲氮表面硬度大于900HV,滲氮基體硬度大于400HV(42HRC)。簡化工藝,顯著提高了滲氮基體硬度。
表1 試驗鋼的化學成分(質量分數)(%)
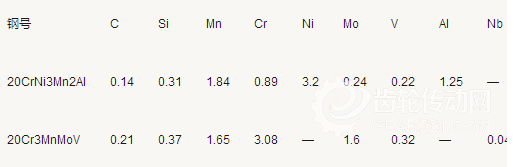
(2)深層滲氮硬化
為了實現滲氮層深層硬化,必須將時效硬化鋼滲氮硬化和時效硬化兩種機制正確地混合,改變恒溫滲氮為變溫滲氮,滲氮前期以滲氮固溶強化和彌散硬化為主,后期為滲氮硬化和時效硬化疊加。采用離子滲氮工藝,可以充分利用離子轟擊和陰極濺射造成的滲氮表面活化與不斷出現的大量晶體缺陷,有效的加速氮原子的擴散,加快滲氮速度。
以時效硬化鋼20CrNi3Mn2Al為例,與滲氮鋼38CrMoAl普通滲氮和滲碳鋼20CrMnTi常規氣體滲碳淬火的硬化進行對比,如附圖所示,其中20CrNi3Mn2Al鋼經過870℃×3h空冷固溶處理+520~540℃×80h深層離子滲氮,38CrMoAl鋼經過520~530℃×50h離子滲氮,20CrMnTi鋼經過930℃滲碳+850℃油淬。三種材料不同工藝處理結果可以看出,時效硬化鋼20CrNi3Mn2Al深層離子滲氮表面硬度高,表層強化效果顯著,基體硬度高,與滲碳鋼相當,高于38CrMoAl滲氮鋼。表明時效硬化鋼滲氮后有很高的承載能力。
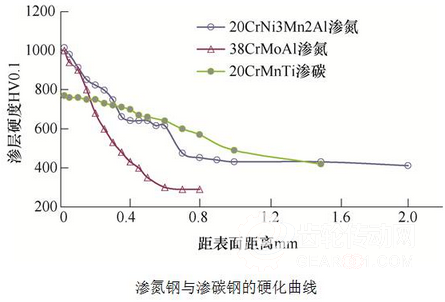
2.齒輪受力分析
齒輪是在接觸疲勞和彎曲疲勞的復雜應力條件下工作,滲氮層次表層承受最大的剪切應力,滲氮層剝落和疲勞破壞往往發生在次表層,因此充分強化滲氮次表層是提高齒輪承載能力的關鍵。
大量國內外試驗研究結果證明,隨著滲氮硬化層層深增加和齒輪心部硬度提高,齒輪接觸疲勞強度和彎曲疲勞強度隨之提高。深層離子滲氮硬化技術,采用時效硬化鋼和深層滲氮硬化,對滲氮齒輪滿足重載復雜應力條件工作是重要保證。
試驗表明,20CrNi3Mn2Al鋼深層離子滲氮后,滲氮表面下0.4mm處硬度大于600HV,滲氮基體硬度為400HV(42HRC)以上。如表2所示。
表2 20CrNi3Mn2Al鋼深層離子滲氮后的硬度和層深
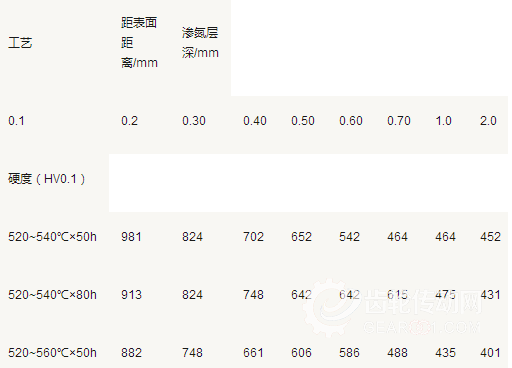
3. 應用展望
推薦20CrNi3Mn2Al鋼作為時效硬化滲氮齒輪鋼,采用深層滲氮硬化技術可滿足滲氮齒輪工作條件的更高要求。
普通調質結構鋼42CrMo、35CrMoV、25Cr2MoV等制造滲氮齒輪,基體硬度低(28~38HRC),次表層硬度低(表面下0.4mm處不超過400~500HV)。時效硬化鋼20CrNi3Mn2Al鋼固溶處理后硬度為30~36HRC,深層離子滲氮后,表面硬度高于900HV,滲氮表面下0.4mm處硬度為600~650HV。基體硬度為40~46HRC,滲層深度為0.7mm以上。
展望用時效硬化鋼制造滲氮齒輪,可以預期有廣闊應用前景。現有調質結構鋼制造的滲氮齒輪,模數不超過10mm,由于時效硬化鋼采用了深層滲氮硬化技術,大大強化了滲氮層和基體,明顯提高了齒輪的承載能力。可以期望時效硬化鋼滲氮齒輪模數會超過10mm,可用來制造重負載高性能齒輪。