蝸桿通常與蝸輪配合使用組成交錯軸齒輪副,可作為減速裝置的重要傳動結構。為得到較高的傳動效率,蝸桿要求表面硬度和加工精度相對較高,若蝸桿熱處理和加工工藝不恰當,容易在蝸桿齒面形成裂紋,影響蝸桿齒面的疲勞強度。某批次蝸桿材料選用 17CrNiM06,是某動力傳動減速機的主要傳動部件,在磨齒加工過程中在其齒根、齒面發現多條不同程度的裂紋,大部分在粗磨工序出現裂紋,其中一件在精磨工序出現裂紋,裂紋主要表現為齒根塊狀剝落、齒面靠近齒根線狀裂紋及由齒根到齒頂散射的線狀裂紋形式,裂紋肉眼可見,觸感明顯,嚴重位置有爆裂現象,如圖1~ 2所示。
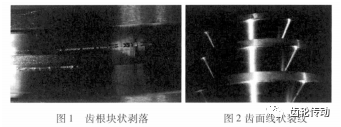
為有效開展蝸桿齒面裂紋原因分析,本文針對蝸桿在加工中出現齒面裂紋的問題,采用故障樹的方法, 建立了以蝸桿齒面裂紋為頂事件的故障樹,從設計、鍛件毛坯、熱處理、磨削加工等方面自頂向下對故障樹進行展開,完成故障樹的建立;隨后按照自底向上的方法對故障樹中可能造成蝸桿齒面裂紋的原因即底事件進行了逐一分析和問題排查,在對故障機理進行深入分析的基礎上通過問題復現等手段對故障進行了定位,并給出了相應的解決措施,通過實踐驗證了措施的有效性,有效解決了蝸桿磨削產生裂紋的問題。本文對如何建立故障樹、通過故障樹分析解決實際問題及開展類似齒面裂紋的故障原因分析,提供解決方案等都具有實際的指導意義。
一、故障原因分解
故障樹圖一般指的是一種性質十分特殊的倒立式的樹狀邏輯因果關系圖,主要通過事件符號、邏輯門符號和轉移符號表述故障事件之間的因果關系。建立故障樹時,應從頂事件出發,逐級向下分解,找出造成頂事件的直接原因即中間事件,重復上述步驟直至中間事件不能再次分解或者在實際分析過程中沒必要再次進行分解,最底層的輸入事件即所要分析的底事件。通過該方法建立以蝸桿齒面裂紋為頂事件的故障樹如圖3所示。
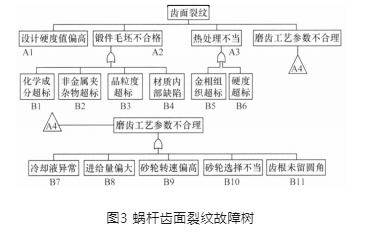
二、故障原因分析
蝸桿齒面裂紋故障樹中已經列出了可能造成蝸桿齒面裂紋的所有原因即底事件,根據已經建立的蝸桿齒面裂紋故障樹,通過對該故障樹中所有底事件進行逐一分析和排除,對蝸桿齒面裂紋問題進行故障定位,找到造成本批次蝸桿齒面裂紋的真實原因。
設計原因分析:蝸桿齒面裂紋蝸桿表面蝸桿材料為17CrNiM06,按 GB/T3480.5規定要求滲碳鍛鋼表面硬度660—800 HV或 HRC58—64,圖紙設計滲碳淬火后表面硬度為HRC58— 62。符合國家標準要求。對比同類產品蝸桿,其滲碳淬火后表面硬度設計值與該要求值吻合,故可排除設計硬度值偏高A1。
鍛件毛坯分析:(1)針對鍛件化學成分的排查,根據鍛件廠家提供的自查記錄及鍛件化學成分表,蝸桿化學成分符合 17CrNiM06技術要求,不存在超標情況,如表1所示,可排除鍛件化學成分超標B1。
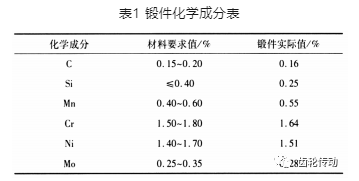
(2)針對鍛件非金屬夾雜物進行檢測,沿蝸桿軸向取樣,按GB/T10561—2005《鋼中非金屬夾雜物含量的測定標準評級圖顯微檢驗法》進行非金屬夾雜物檢測,非金屬夾雜物主要為D類球狀氧化物,非金屬夾雜物級別為:A0,B0,c0,D0.5,DS0,放大100倍后如圖4 所示。同時根據鍛件廠家自查情況,蝸桿鍛件非金屬夾雜物級別符合鍛件技術要求及相關的國家標準,不存在超標情況,可排除鍛件非金屬夾雜物超標B2。

(3)對鍛件晶粒度的排查,根據鍛件廠家自查情況,蝸桿鍛件本質晶粒度及實際晶粒度均為6級,符合鍛件技術要求,不存在超標情況,可排除鍛件晶粒度超標B3。
(4)針對鍛件內部缺陷的排查,根據鍛件廠家自查情況,蝸桿鍛件在完成鍛造出廠前進行了超聲波探傷,探傷報告顯示該鍛件產品合格,可排除鍛件材質內部缺陷B4。
綜上所述,可排除鍛件毛坯不合理A2。
熱處理分析:(1)針對滲碳淬火后金相組織超標的排查,在拋光狀態下觀察,齒根位置有一處裂紋開口較大,裂紋沿平行于齒面方向向節圓擴展,裂紋長度約8 mm,如圖5所示。在節圓表面存在數條微裂紋,裂紋垂直于齒面,在表面開口較大,向內逐漸變窄,裂紋尾部較尖銳,深度約 1 mm。
腐蝕后對齒部進行金相組織檢測,在齒面沿齒高方向約90%的齒面有二次淬火組織(未回火馬氏體組織), 深度約為0.01 mm。二次淬火組織的分布與齒面磨削燒傷檢測觀察的磨削燒傷位置基本一致,如圖6所示。心部組織為板條馬氏體,晶粒度為6.5級,如圖7所示。齒頂未見二次淬火組織,通過對齒頂進行硬度檢測,在距齒頂表面距離0.6 mm的范圍內硬度為HRC54~57,越靠近齒頂表面的地方硬度值越低,在距離齒頂表面大約 0.6 mm的地方硬度值達到最高值,由此判斷0.6 mm為滲碳淬火層厚度,蝸桿齒頂部位在磨削加工過程中發生回火。齒頂硬度檢測數值如表2所示。
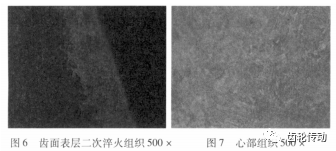
表2 齒頂硬度檢測數值
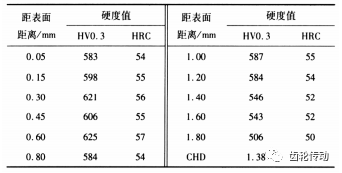
齒根未磨區域表面組織為:細針狀馬氏體+彌散顆粒狀碳化物+少量殘余奧氏體,碳化物級別:1級,馬氏體級別:2級,殘余奧氏體級別:2級,滿足技術要求。可排除滲碳淬火后金相組織超標B5。
(2)針對滲碳淬火后硬度超標的排查,根據現場各熱處理工藝車間人員現場的自查分析記錄情,滲碳淬火熱處理完成后的試樣表面硬度保持在HRc59.2~59.7,芯部硬度為HRc34~35.6,該硬度符合相關標準,無其他硬度超標問題,可以大致排除該試樣滲碳淬火硬化處理結束后試樣表面硬度存在的明顯超標B6。
綜上所述,可排除滲碳淬火處理不當A3。
磨齒工藝參數不合理分析:按照GB/T17879—1999對蝸桿齒面進行侵蝕檢驗,觀察發現整個齒高方向,有約90%的區域呈白亮色,顯示二次淬火磨削燒傷特征,剩余10%齒面呈深灰色,顯示回火燒傷特征,如圖8所示。
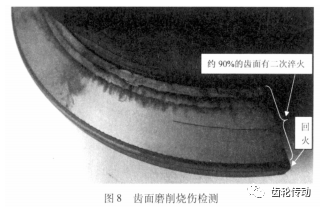
(1)針對磨齒時冷卻液異常的排查,通過查閱生產車間的工藝記錄,該機床工作正常,冷卻液正常,可排除磨齒時冷卻液異常B7。
(2)針對磨齒時進給量偏大的排查,通過查閱生產車間的工藝記錄,磨齒時單次進給量不超過0.02 mm,將磨齒單次進給量降低至0.01 mm后,裂紋變得極其細微,不能排除磨齒時進給量偏大B8。
(3)針對磨齒時砂輪轉速偏高的排查,通過查閱生產車間的工藝記錄,磨削加工時砂輪轉速為 1800m/min,將砂輪轉速降為1200m/min后,沒有出現肉眼可見的裂紋;不能排除磨齒時砂輪轉速偏高B9。
(4)針對磨齒時砂輪選擇不當的排查,更換砂輪磨削后仍然出現裂紋,可以排除磨齒時砂輪選擇不當B10。
(5)針對齒根未加工圓角的排查,在齒根處加工圓角后進行磨削仍然出現了裂紋,可以排除齒根未加工圓角B11。
綜上所述,無法排除磨齒時進給量偏大B8、砂輪轉速偏高B9的故障影響,進而無法排除磨齒工藝參數不合理A4故障原因。
故障定位:通過故障樹分析,蝸桿齒面裂紋原因為磨齒工藝參數不合理A4,具體原因為磨齒時進給量偏大B8、砂輪轉速偏高B9。
三、故障機理分析
蝸桿的齒面是螺旋表面,磨齒時齒面直接受到砂輪磨粒面的旋滑刮擦、耕犁和切削。由于砂輪速度高,磨削砂輪的磨削過程發熱量大,磨削熱量不能很快散去,而是在極短時間內傳到整個齒輪零件結構體系中。零件在磨削加工時會產生淬火效應,零件被加工表面因磨削會產生大量的熱,使整個被磨削表面內部金屬的奧氏體溫度會迅速升高,如果此時熱量不能被冷卻液迅速帶走,很容易在表面產生不同程度的燒傷。淬火效應使零件組織中殘余的部分工件表層金屬組織重新開始出現了奧氏體化,并可以通過再次磨削淬火重新成為馬氏體,陔馬氏體的組織應力和磨削熱應力的綜合應力一旦超過了淬火后材料所允許承受的最大機械強度極限,便很可能容易產生磨削性裂紋。
蝸桿采用17CrNiM06鋼材質,滲碳硬化后的表面碳含量可達0.96%,有極好的熱淬透性和熱淬硬性,在冷卻環境差溫升快溫度高的情況下,局部較易出現過熱。當溫度超過滲碳后回火溫度但低于相變溫度時,齒面發生不同程度的回火;當瞬時溫度超過鋼的Acl點轉變溫度時,隨后遇冷卻液迅速冷卻,便在表層形成二次淬火馬氏體組織,而表層下由于溫度梯度大,時間短,會形成高溫回火組織,表層與次表層之間形成拉應力,當表層薄而脆的二次淬火馬氏體承受不了時,便產生裂紋。局部溫度越大,奧氏體轉變為馬氏體,脆性變大,更容易繼續使裂紋變大。
從磨削表面金相組織熱處理情況異常及工件表面硬度異常等各項檢測結果可知,輪齒表面發生了低溫氧化回火和高溫二次淬火。磨削后產生的裂紋也總是與高溫二次淬火以及工件表面氧化燒傷等熱處理現象同時出現。蝸桿在用高溫淬火處理或淬火加低溫回火處理后,其表面組織的正常及微觀組織情況一般看成是低溫氧化回火馬氏體層和高溫熱處理殘余奧氏體,表面應力一般呈壓應力狀態。當蝸桿表面進行磨削時,金相基體組織結構已由原來回火后的馬氏體結構逐漸變成了高溫回火索氏體結構或低溫回火的屈氏體,表面也會因此產生一些拉應力,蝸桿表面組織變化越大,拉應力就越大,應力影響深度越大,蝸桿表面燒傷越嚴重。當磨削表面發生回火和二次淬火后,雖然最外層表面奧氏體殘余應力呈壓應力狀態,但表層非常薄,次表面索氏體或屈氏體殘余應力呈拉應力狀態,表面奧氏體層與次表面索氏體或屈氏體層形成了兩個硬度差別較大的應力梯度,從而較為容易在該處產生裂紋。
四、改進措施及驗證情況
改進措施:對蝸桿工藝進行相應調整,熱處理工藝按硬度下限進行控制,磨削參數按以下驗證工藝參數進行,具體如下:
(1)蝸桿磨削加工前增加兩次230℃×20 h回火處理,控制蝸桿齒面硬度約為58~59 HRC;
(2)觀察齒面噴丸情況,如噴丸不良可重新噴丸或手工打磨處理直至符合要求;
(3)將蝸桿表面清理干凈后,對蝸桿齒面先進行磁粉探傷,然后進行著色探傷,并出具相應探傷報告;
(4)探傷合格后,以蝸桿齒根圓找正校正減小彎曲變形的影響,同時通過打表齒面校正減小齒面扭曲變形,再精車蝸桿兩端軸徑至規定尺寸;
(5)磨削工藝參數調整,砂輪轉速控制在1 200 m/min 以下,采用SG磨料、粒度46、硬度H、陶瓷結合劑砂輪,單次進給量控制在0.01mm。
驗證情況:對3件滲碳淬火后蝸桿進行兩次230℃×20 h回火,首件按制定的措施磨削后,齒頂硬度HRc58~59,齒面著色探傷無裂紋,后續兩件加工后表面也未出現裂紋,質量穩定,證明調整后的蝸桿工藝措施有效,磨削過程中蝸桿齒面沒有裂紋產生,該問題得到解決。
五、結束語
蝸桿磨削后表面回火的浸蝕檢驗顯示蝸桿齒面有明顯的二次淬火磨削燒傷特征和回火燒傷特征,可判定為磨削工藝不當造成的齒面裂紋。通過降低磨削砂輪轉速、減少砂輪磨削進給量、優選砂輪材質等方法,減少蝸桿齒面磨削加工時產生的熱,避免了蝸桿磨削表面發生二次淬火和回火而產生裂紋,試驗驗證措施有效。
對于蝸桿齒面裂紋這種涉及材料選用、設計、熱處理及加工等多個領域的復雜問題。采用故障樹分析方法,通過故障樹建立、故障原因排查、故障定位、故障機理分析、故障復現及改進措施驗證,找到了該批次蝸桿齒面裂紋的原因,并通過齒面硬度控制及磨削參數優化等措施解決了該問題,為通過故障樹分析方法解決復雜系統問題提供了思路和方法。
參考文獻略.