一體化電機(jī)模組是機(jī)器人領(lǐng)域的重要發(fā)展方向,它省去了中間傳動(dòng)部件,將電機(jī)和減速器集成為一個(gè)模組整體,機(jī)器人的動(dòng)力傳動(dòng)系統(tǒng)結(jié)構(gòu)得以簡(jiǎn)化,使得動(dòng)力傳動(dòng)系統(tǒng)更緊湊。
傳動(dòng)效率是機(jī)器人一體化電機(jī)模組的重要指標(biāo),較高的傳動(dòng)效率不僅可以減小動(dòng)力組件的體積和質(zhì)量,而且還能降低整機(jī)的能耗,增加待機(jī)時(shí)間。
另外,在關(guān)節(jié)機(jī)器人應(yīng)用領(lǐng)域,很多場(chǎng)合通過(guò)檢測(cè)電機(jī)電流從而對(duì)外力進(jìn)行估計(jì),減速器傳動(dòng)效率越高,則減速器的機(jī)械阻抗就越小,外力和電機(jī)之間的力傳遞就越透明。因此,高傳動(dòng)效率的減速器,能實(shí)現(xiàn)機(jī)器人關(guān)節(jié)更高精度的基于電機(jī)電流環(huán)的外力感知。
本文主要針對(duì)一體化電機(jī)模組中的減速器進(jìn)行傳動(dòng)效率計(jì)算和優(yōu)化分析,現(xiàn)有齒輪減速器效率優(yōu)化方法過(guò)于復(fù)雜,需要進(jìn)行復(fù)雜的前處理,不便于在設(shè)計(jì)初期快速確定減速器關(guān)鍵參數(shù)。本文基于傳動(dòng)效率精確計(jì)算公式,推導(dǎo)了 3K 行星齒輪系統(tǒng)精確的效率計(jì)算公式,并提供了一種通過(guò)調(diào)整齒輪組中心距和齒輪變位系數(shù)來(lái)獲得該減速器最高嚙合效率的方法,只需要輸入齒輪模數(shù)、各齒輪齒數(shù)、齒頂高系數(shù)和標(biāo)準(zhǔn)壓力角,便可以計(jì)算得到效率最高時(shí)的減速器關(guān)鍵參數(shù)(最優(yōu)中心距和最優(yōu)變位系數(shù)),有助于設(shè)計(jì)者在設(shè)計(jì)初期快速確定減速器齒輪系統(tǒng)的關(guān)鍵參數(shù)。
1、一體化電機(jī)模組機(jī)械設(shè)計(jì)
本文所研究的一體化電機(jī)模組結(jié)構(gòu)如圖 1 所示,包括減速器、殼體、電機(jī)、編碼器。電機(jī)轉(zhuǎn)子通過(guò)平鍵與減速器太陽(yáng)輪連接,將動(dòng)力傳遞到減速器輸入端,編碼器用于獲取電機(jī)轉(zhuǎn)子位置,外部驅(qū)動(dòng)器(未圖示)用于對(duì)該一體化電機(jī)模組進(jìn)行控制。該模組將電機(jī)和減速器高度集成為模組形式,可以顯著減小傳動(dòng)系統(tǒng)的體積和質(zhì)量,有利于提升機(jī)器人系統(tǒng)的功率密度。
減速器原理如圖 2 所示,為 3K 型減速器,齒輪 A 為輸入端太陽(yáng)輪,齒輪 C 為一級(jí)行星齒輪,齒輪 B為一級(jí)內(nèi)齒圈,齒輪 D 為二級(jí)行星齒輪,齒輪 E 為二級(jí)內(nèi)齒圈(動(dòng)力輸出齒圈)。該類型減速器可以在有限的空間實(shí)現(xiàn)較大速比傳動(dòng),相比其他類型的齒輪減速器,能夠有效減小模組的體積和質(zhì)量,從而提高模組的功率密度。
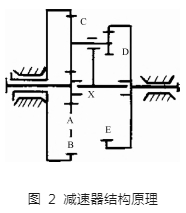
2、減速器嚙合效率精確計(jì)算
目前計(jì)算減速器嚙合效率的方法主要有以下兩種:
(1)日本學(xué)者兩角宗晴公式:
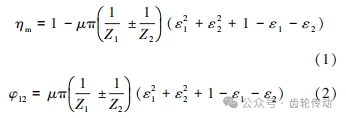
式中:ηm 是嚙合效率;μ 是摩擦系數(shù);Z1,Z2 分別是齒輪 1 和齒輪 2 的齒數(shù);ε1,ε2 分別是嚙入重合度和嚙出重合度;φ12 為齒輪副的嚙合效率損失。
(2)蘇聯(lián)學(xué)者庫(kù)德略采夫公式:
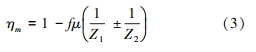
式中:f 是與齒輪齒頂高系數(shù) h∗a 相關(guān)的系數(shù);當(dāng) h∗a ≤m 時(shí),f= 2. 3,當(dāng) h∗a=(1. 0~1. 8)m 時(shí),f = 3. 1,m 為齒輪模數(shù)。
兩角宗晴的公式較為精確,而我國(guó)工程技術(shù)人員多采用庫(kù)德略采夫的公式。根據(jù)庫(kù)德略采夫的公式,齒輪嚙合效率只跟摩擦系數(shù) μ、兩個(gè)齒輪的齒數(shù) Z1 和 Z2 、齒頂高系數(shù) h∗a 有關(guān),而實(shí)際上,不同的中心距及不同的齒輪變位系數(shù)也會(huì)影響齒輪嚙合效率。
本文主要基于兩角宗晴的嚙合效率公式,詳細(xì)推導(dǎo)出齒輪嚙合效率與齒輪中心距和齒輪變位系數(shù)的關(guān)系,并給出最高嚙合效率對(duì)應(yīng)的最優(yōu)齒輪中心距和最優(yōu)齒輪變位系數(shù)確定的方法。
本文采用的 3K 行星減速器齒輪系的嚙合效率:
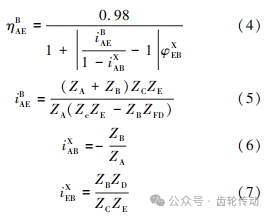
式中:ηBAE是 3K 行星減速器齒輪系的嚙合效率;iBAE 為齒輪 B 固定、齒輪 A 輸入、齒輪 E 輸出的減速比;iXAB為支架 X 固定、為齒輪 A 輸入、齒輪 B 輸出的減速比;iXEB為支架 X 固定、齒輪 E 輸入、齒輪 B 輸出的減速比;ZA ,ZB ,ZC ,ZD ,ZE 分別為齒輪 A,B,C,D,E 的齒數(shù);φ X EB 為支架 X 固定、齒輪 E 輸入、齒輪 B 輸出時(shí)傳動(dòng)機(jī)構(gòu)中各齒輪副嚙合損失系數(shù)之和。
減速器各齒輪齒數(shù)由傳動(dòng)比需求和結(jié)構(gòu)限制確定后,減速器齒輪系的嚙合效率中唯一的未知數(shù)為式(4)中的 φ XEB ,其計(jì)算公式 :

式中:φXBC 為支架 X 固定、齒輪 B 輸入、齒輪 C 輸出時(shí)齒輪副嚙合損失系數(shù);φ X DE 為支架 X 固定、齒輪 D 輸入、齒輪 E 輸出時(shí)齒輪副嚙合損失系數(shù)。
根據(jù)式(2),式(8)中齒輪副嚙合損失系數(shù) φ XBC 和 φXDE 的計(jì)算公式:
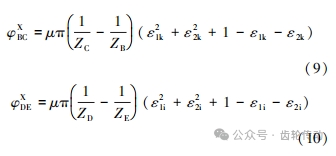
式中:ε1k 為齒輪 B、齒輪 C 嚙入重合度;ε2k 是齒輪 B、齒輪 C 嚙出重合度;ε1i 為齒輪 D、齒輪 E 嚙入重合度;ε2i 是齒輪 D、齒輪 E 嚙出重合度。
φXBC 和 φXDE 為兩對(duì)齒輪副嚙合損失系數(shù),其計(jì)算方法是一樣的,下面以 φXBC 的計(jì)算為例進(jìn)行公式推導(dǎo),φXDE 公式推導(dǎo)方法跟 φXBC 相同。
式(9)中齒輪 B、齒輪 C 嚙入重合度 ε1k,齒輪B、齒輪 C 嚙出重合度 ε2k 計(jì)算公式如下:
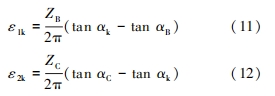
式中:αk 是齒輪 B 和齒輪 C 的嚙合壓力角;αB 是齒輪 B 齒頂壓力角;αC是齒輪 C 齒頂壓力角;αk 、αB 、 αC 計(jì)算公式如下:
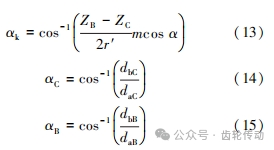
式中:m 是齒輪模數(shù);α 是變位之前的標(biāo)準(zhǔn)壓力角,取值為 20°;r′ 是齒輪 B 和齒輪 C 的實(shí)際中心距;dbC 和 dbB 分別是齒輪 C 和齒輪 B 的基圓直徑;daC 和 daB 分別是齒輪 C 和齒輪 B 的齒頂圓直徑。dbC , dbB,daC,daB 計(jì)算公式如下:
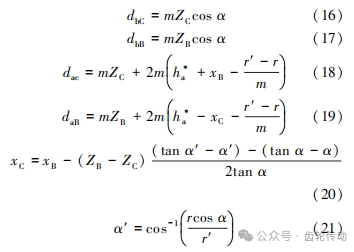
式中:h∗a 為齒頂高系數(shù),取值為 1;xB ,xC 分別為齒輪 B、齒輪 C 的變位系數(shù);r為理論中心距;r′ 為實(shí)際中心距;α′ 為變位后分度圓端面壓力角。
至此,綜合式(4)~ 式(19),3K 行星減速器齒輪系的嚙合效率計(jì)算公式中的已知量為:齒輪 A,B,C,D,E 的齒數(shù) ZA,ZB ,ZC ,ZD,ZE;變位之前的標(biāo)準(zhǔn)壓力角 α;理論中心距 r;齒頂高系數(shù) h∗a;齒輪模數(shù) m;未知的變量為:實(shí)際中心距 a′;齒輪 B 變位系數(shù) xB;齒輪 E 變位系數(shù) xE 。
綜上,要使齒輪系嚙合效率最高,則需要選擇最優(yōu)的中心距 a′ 和變位系數(shù) xB 和 xE 。
3、減速器最大效率優(yōu)化方法
由前述可知,在減速器的速比和尺寸根據(jù)設(shè)計(jì)需求已經(jīng)確定的情況下,齒輪模數(shù)和各齒輪的齒數(shù)也已經(jīng)確定,在此條件下,要使減速器齒輪傳動(dòng)系統(tǒng)實(shí)現(xiàn)最大的嚙合效率,可以調(diào)整的變量只有三個(gè):齒輪實(shí)際中心距 a′;齒輪 B 變位系數(shù) xB、齒輪 E 變位系數(shù) xE。
本文設(shè)計(jì)方案中的標(biāo)準(zhǔn)減速器參數(shù)如表 1,各齒輪均不變位。

根據(jù)前述效率精確計(jì)算方法,按照標(biāo)準(zhǔn)減速器參數(shù),計(jì)算得到的減速器嚙合效率為 78. 2%。
效率優(yōu)化開始前,先根據(jù)減速器齒輪系設(shè)計(jì)原則和實(shí)際結(jié)構(gòu)設(shè)計(jì)約束,確定中心距、齒輪 B 變位數(shù)、齒輪 C 變位系數(shù)可以變動(dòng)的的范圍。本文方案中,中心距可變動(dòng)范圍為 18. 5 ~ 20. 5 mm,齒輪 B 變位系數(shù)可變動(dòng)范圍為-0. 7~1. 0,齒輪 E 變位系數(shù)可變動(dòng)范圍為-0. 6~1. 0。
在中心距可變動(dòng)范圍內(nèi),每間隔 0. 1 mm 進(jìn)行一次齒輪效率的計(jì)算,在每個(gè)中心距下,齒輪 B 變位系數(shù)和齒輪 E 變位系數(shù)也間隔 0. 1 進(jìn)行排列組合。本文方案中,中心距有 21 個(gè)可選值,每個(gè)中心距下,齒輪 B 和齒輪 E 的變位系數(shù)有 306 種組合, 一共能計(jì)算得到 6 426 個(gè)不同的排列組合,從中選出效率最大點(diǎn)對(duì)應(yīng)的中心距、齒輪 B 變位系數(shù)、齒輪 E 變位系數(shù)。
表 2 為中心距為 20 mm 時(shí)的減速器嚙合效率數(shù)據(jù),圖 3 為對(duì)應(yīng)的嚙合效率圖。
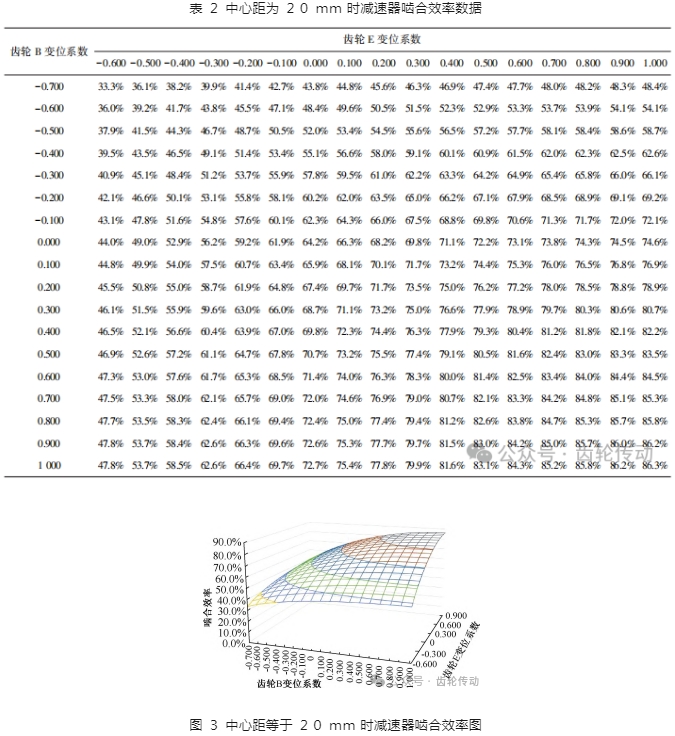
在20 mm中心距情況下,當(dāng)齒輪 B 變位系數(shù)為 1、齒輪 E 變位系數(shù)為 1 時(shí),減速器嚙合效率最高為 86. 3%。以此類推,可以得出在中心距可變動(dòng)范圍為 18. 5~20. 5 mm內(nèi),每間隔 0. 1 mm 中心距對(duì)應(yīng)的最大效率,最后對(duì)選取所有中心距下最大效率值和對(duì)應(yīng)的變位系數(shù)參數(shù)作為最終的設(shè)計(jì)參數(shù)。
本方案中,最終選擇得到的效率最優(yōu)時(shí)的減速器參數(shù)如表 3 所示。當(dāng)中心距等于 20 mm、齒輪 B 變位系數(shù)等于 1、齒輪 E 變位系數(shù)等于 1 時(shí),效率最大為 86. 3%,最終設(shè)計(jì)采用改組參數(shù)作為減速器的設(shè)計(jì)參數(shù)。
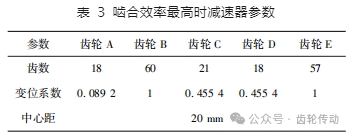
根據(jù)前述,按照標(biāo)準(zhǔn)減速器參數(shù),計(jì)算得到的減速器嚙合效率為 78. 2%,比前述經(jīng)過(guò)效率優(yōu)化后的減速器嚙合效率 86. 3%低 8. 1%,說(shuō)明經(jīng)過(guò)效率優(yōu)化后,減速器的理論嚙合效率有效提高。
計(jì)算得到減速器軸承系統(tǒng)效率 ηB 為 96%,攪油效率 ηS 為 97%,因此,最終減速器的傳動(dòng)效率 η 為 80. 3%。

4、試驗(yàn)驗(yàn)證
根據(jù)前述效率優(yōu)化后的減速器參數(shù)進(jìn)行樣機(jī)設(shè)計(jì),并進(jìn)行減速器傳動(dòng)效率測(cè)試,如圖 4 所示,用于減速器傳動(dòng)效率測(cè)試的樣機(jī)為未裝入電機(jī)的模組。
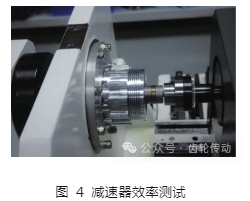
在額定載荷 90 N·m、額定輸入轉(zhuǎn)速2 000 r/ min 條件下,進(jìn)行減速器效率測(cè)試,結(jié)果如表 4 和圖 5 所示。測(cè)得的最大傳動(dòng)效率為 79. 7%,與前述減速器理論傳動(dòng)效率 80. 3%接近。
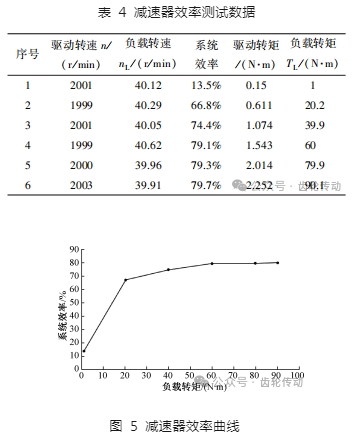
5、結(jié)語(yǔ)
本文推導(dǎo)出了 3K 減速器精確的效率計(jì)算公式,并基于該公式提出了一種提高減速器嚙合效率的優(yōu)化方法。
基于本文所提及的優(yōu)化方法,進(jìn)行了樣機(jī)的設(shè)計(jì)及測(cè)試,測(cè)試結(jié)果表明,該優(yōu)化方法計(jì)算得到的減速器效率跟實(shí)測(cè)值吻合。
對(duì)于其他類型的齒輪減速器,也可以采用本文所提及的單對(duì)齒輪嚙合效率計(jì)算方法計(jì)算得出嚙合效率,并代入相應(yīng)減速器效率計(jì)算公式進(jìn)行減速器齒輪系嚙合效率的計(jì)算。
參考文獻(xiàn)略.