齒輪傳動具有功率范圍大、傳動效率高、傳動比準確等特點,在傳動設備中廣泛應用。由于輪齒受載后產生的彈性變形以及制造、安裝誤差的存在,漸開線圓柱齒輪在嚙合過程中會產生基節偏差,使實際的嚙合點偏離理論位置。同時嚙合接觸齒對的變化,導致在齒輪副嚙入嚙出過程中會產生沖擊,從而產生振動噪聲,比較突出的問題就是齒輪的嘯叫。齒輪嘯叫不僅降低了系統的聲學舒適性,還存在潛在的性能和耐久性問題。
解決齒輪嘯叫的傳統方法有改變齒輪箱設計、調整齒輪材料、提高加工或裝配精度。雖然這些方法已顯示出一定的有效性,但它們需要對齒輪箱系統進行大量的修改,增加了齒輪箱的復雜性和生產成本。為了克服這些缺點,研究人員和工程師進行了大量的研究,探索出了齒廓修形這一方法,作為減少齒輪嚙合噪聲的解決方案。
齒廓修形在保持齒輪的基本參數不變的同時,沿齒高方向在齒面上微量修整齒廓。這種方法有助于改善齒面的載荷分布,減小單齒嚙合到雙齒嚙合過渡期的載荷波動,使齒輪在完整嚙合周期內平穩運行,降低齒輪噪聲,進而提升了齒輪箱整體的 NVH(Noise,Vibration and Harshness,NVH)性能。基于其實施的簡單性、成本效益和對現有齒輪系統的改造能力等優勢,齒廓修形正受到越來越多的關注。
盡管齒廓修形在降低齒輪嚙合噪聲方面大有可為,考慮到齒廓修形對齒輪強度、性能參數和降噪潛力的影響,仍需要進行全面的研究。有必要對不同的齒廓修形方案進行系統的比較,并在實際應用中驗證其有效性。
本文基于KISSsoft軟件進行齒輪副建模及齒輪齒廓修形優化,首先分析比較修形前后嚙合沖擊力、齒輪強度及齒輪性能參數,然后確定齒廓修形量及修形長度,并形成用于齒形檢測“K”形圖。提出的齒廓修形方案,可有效地改善某齒輪箱第 4 檔齒輪副的嚙合狀態,從而達到控制齒輪副嘯叫,降低齒輪箱噪聲的目標。
1、齒輪箱臺架噪聲測試
在中國一拖集團有限公司進行齒輪箱臺架加載試驗,試驗現場如圖1所示。
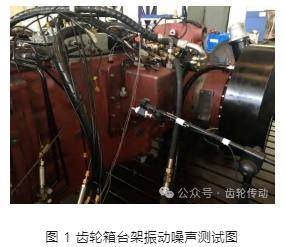
從臺架輸入軸測取齒輪箱轉速,采集齒輪箱在 760~2 300 r/min 轉速范圍內 30 s 升速工況的振動噪聲信號。數據采集系統為B&K公司生產的LANXI 模塊,4189 型 1/2 英寸傳聲器和 4504A 型三向振動加速度傳感器安裝在齒輪箱左側,采用階次追蹤法分析齒輪副的振動噪聲信號。根據齒輪箱內齒輪副之間的嚙合關系和齒數,計算各個齒輪副間的嚙合階次。第四檔齒輪副的嚙合階次(31.4 階)及其倍頻與圖2中的振動階次吻合,因此,第4檔齒輪副嚙合噪聲是齒輪箱產生嘯叫的根源。
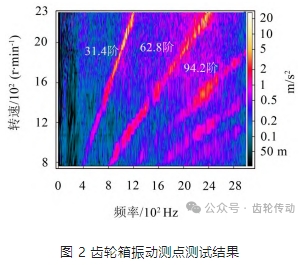
輪齒相當于懸臂梁,在齒輪系統傳動過程中,齒輪副嚙合齒面的輪廓相互接觸過程中產生的作用力,使齒面發生了彈性形變。加之在齒輪制造過程中產生的加工誤差,造成了齒輪副的實際嚙合線偏離理論嚙合線,受載齒輪嚙合過程中的傳遞誤差引起并通過頻率的調諧產生了齒輪的嘯叫噪聲。本文將對第四檔齒輪副的齒廓進行微觀修形,以改善齒面的嚙合誤差,并減小傳遞誤差的幅值和波動,從根源上降低了齒輪的嘯叫。
2、齒輪嚙合振動模型
根據圖 3 所示兩個齒輪之間的嚙合關系,利用牛頓運動定理建立漸開線直齒圓柱齒輪副的一維振動模型。
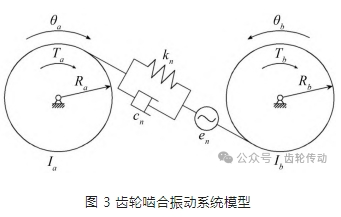
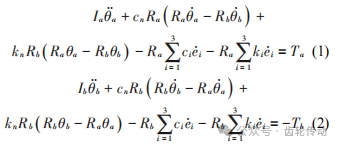
其中定義在兩輪齒嚙合線上的相對位移是 x = Ra θa - Rbθb。cn為該齒輪副的嚙合阻尼系數;
kn 為該齒輪副的綜合剛度;ci(i = 1, 2, 3)為第 i 對齒輪的嚙合阻尼系數;ki(i = 1, 2, 3 )為第 i 對齒輪的綜合嚙合剛度;ei(i = 1, 2, 3)為第 i 對齒輪的傳遞誤差;Ti(i = a, b)為作用在兩個齒輪上的外載荷力矩;θi( i = a, b) 為主動輪和從動輪的角位移;θi, θi(i = a, b)為主從動齒輪的角加速度;Ii(i = a, b) 為主從動齒輪的轉動慣量;Ri(i = a, b)為主從動齒輪的基圓半徑。
齒輪副的單自由度的力學振動模型為:

式中:me,ce,ke,F0和Fe分別為齒輪嚙合振動系統模型中的等效質量、等效阻尼、等效剛度、等效外載荷力和等效嚙合力。結合以上公式可以得到:
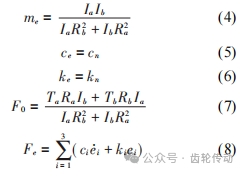
當齒廓修形后,接觸區僅覆蓋齒輪副的部分齒面。輪齒進入嚙合時,實際嚙入點并不是從齒頂開始,而是從齒面上的某一點開始。因此,嚙入沖擊力的計算關鍵是準確求得嚙入點的位置。
嚙合剛度隨著嚙合位置的變化而不斷變化,表示為嚙合點壓力角的函數。采用解析法計算單對齒嚙合剛度:
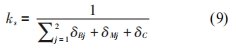
式中:δBj為齒輪j輪齒本身的變形;δC為輪齒之間的接觸變形;δMj為齒輪j輪體附加變形。
嚙合齒輪副的轉動慣量為:
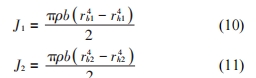
將兩嚙合齒輪的轉動慣量轉化為瞬時嚙合線上的誘導質量:
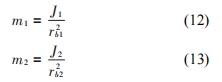
式中:J1和J2分別為小齒輪和大齒輪的瞬時轉動慣量;b為齒寬;ρ為齒輪材料密度;rh1和rh2分別是兩齒輪輪轂內孔半徑;rb1 和 rb2 分別是大小輪的基圓半徑。
齒輪副嚙入沖擊點的沖擊動能為:

式中:vs 為大小輪齒面在初始接觸點的相對法向速度。
由于沖擊作用,使得輪齒之間產生沖擊變形量 δs,與之相對應的沖擊力 Fs 則為最大沖擊力。沖擊動能Ek、沖擊變形量δs以及沖擊力Fs之間有如下的關系:
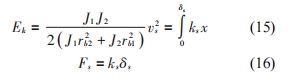
最終得到初始嚙入沖擊點的嚙入沖擊力表達式:

式中:ks 為大小輪齒面在初始接觸點的嚙合剛度。
3、齒廓修形量對齒輪的影響
齒廓最大修形量的計算
齒廓修形方式分為齒頂修形和齒根修形兩種。影響齒廓修形的三大要素主要有:最大修形量Δmax、齒廓修形曲線、修形曲線長度hmax,如圖4所示。
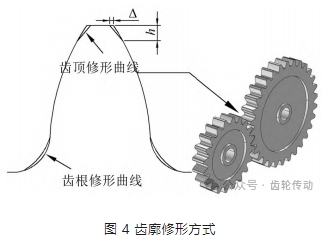
線性修形是最常用的修形類型,根據ISO 6336 標準,對主動、從動齒輪進行齒廓修形時,最大的修形量計算公式為:

其中:KA為使用系數;Ft為圓周力,N;b為齒輪工作齒寬,mm;εα 為端面重合度;Cγ 為輪齒綜合剛度,N/(mm·μm)。
通常情況下,齒廓的修形量在 0.000 7~0.03 mm 之間。由于修正量很小,要求齒輪的制造誤差要低于齒廓修形量才能取得改善嚙合條件的實際效果。
根據最大齒廓修形量公式,計算某齒輪箱第 4 檔齒輪副最大齒廓修形量,其結果如表1所示。
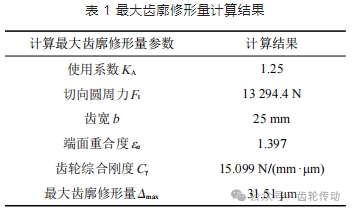
齒輪齒廓修形量方案
為了能夠確定齒廓修形量,本文采用 3 種不同齒廓修形量的修形量方案,具體方案如下:
(1)齒輪副未修形;
(2)主、從動齒輪齒頂和齒根各修形5 μm;
(3)主、從動齒輪齒頂和齒根各修形10 μm。
齒廓修形量對齒輪強度的影響
齒輪強度是齒輪傳動計算中的重要指標,可靠的齒輪強度能夠提高齒輪承載能力、延長齒輪使用壽命。下面計算某齒輪箱第4檔齒輪副在不同齒廓修形量影響下的法向力和齒輪強度,如表 2 和表 3 所示。
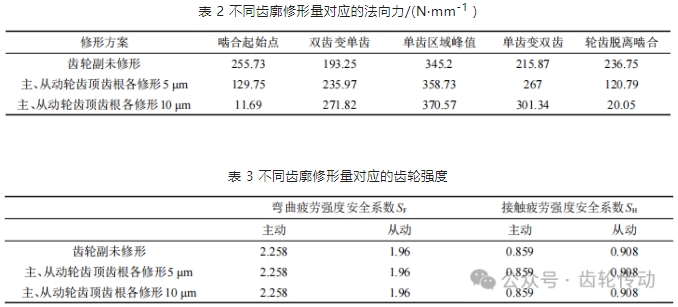
齒輪副嚙合時,主動齒輪齒根推動從動齒輪齒頂進入嚙合,主動齒輪從齒根處進入嚙入,從齒頂處脫離嚙合,而從動齒輪恰好相反。對主動齒輪進行齒頂修形,只能減小其嚙出沖擊。而對從動齒輪進行齒頂修形,降低的是它的嚙入沖擊。因此,同時對主動齒輪和從動齒輪進行齒廓修形,才能夠減小齒輪副的嚙入、嚙出沖擊,使齒輪傳動更平穩,有助于減小齒輪副的嚙合噪聲。如表 2 所示,齒輪未修形時,嚙入、嚙出點的受力較大,最大法向力為255.73 N/mm。進行齒頂和齒根處齒廓修形之后,嚙入、嚙出點的受力隨著修形量的增加逐漸減小。修形量為 5 μm時,嚙入、嚙出點最大法向力為129.75 N/mm。當齒廓修形量增加到10 μm時,嚙入及嚙出點的法向力進一步減小至 11.69 N/mm。但隨著齒廓修形量的增加,單齒區域的法向力變大。因此,齒廓修形量不宜過大。
表 3 是對該齒輪副進行的疲勞強度分析,齒輪強度并未受到齒廓修形量的影響,不同的齒廓修形量沒有使齒輪強度發生改變。
齒廓修形量對齒輪性能參數的影響
重合度是衡量齒輪嚙合性能的重要參數之一,用來判斷齒輪傳動連續性及傳遞載荷的均勻性。重合度越大,同時參與嚙合的輪齒對數越多,齒輪傳動越平穩。不同的齒廓修形量對負載下的齒輪副重合 度將會產生一定的影響,第 4 檔齒輪副重合度的計算結果如表4。

從計算結果的趨勢來看,重合度隨著齒廓修形量的增加逐漸減小,這對于齒輪的嚙合性能是不利的。因此,齒廓修形量不宜過大,齒根應力如表 5 所示。
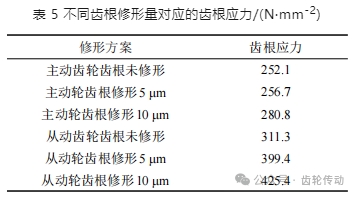
表 5 表明,齒輪齒根應力隨修形量增加呈現增大趨勢。綜合考慮不同齒廓量對齒輪嚙合沖擊力、重合度及齒根應力的影響,5 μm修形量既可以降低嚙合沖擊力,又不至于過多降低齒輪副的齒根強度和重合度。
4、齒廓修形曲線長度的計算
齒頂修形長度計算公式:

齒根修形長度計算公式:

式中:LCa* 指齒頂修形長度系數,LCf* 指齒根修形長度系數,mn指模數。
對齒輪箱第4檔齒輪副齒頂和齒根分別進行齒廓修形5 μm,計算的齒廓修形長度如表6所示。

基于上述齒廓修形量、修形長度的計算,繪制了用于齒形檢測的“K”形框圖,如圖5所示。
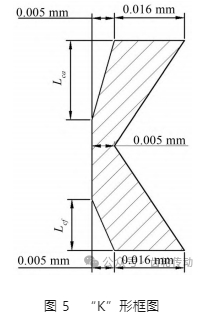
5、試驗驗證
振幅表示齒輪嚙合過程中發生的振動的大小或強度,它與產生的噪聲水平直接相關。圖 6 代表了不同階次的振動振幅分布,它對應于齒廓修形后第 4 檔齒輪副嚙合過程中的諧波成分。
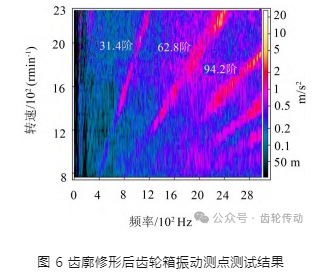
試驗結果表明,與圖2相比,在對產生齒輪箱嘯叫噪聲的第 4 檔齒輪副實施齒廓修形后,與該齒輪副嚙合階次相關的31.4階及其倍頻的振動幅值有明顯下降。振動振幅的減少表明齒輪副的齒寬載荷分布、動態嚙合性能有了很大的改善,說明了齒廓修形在解決與嘯叫齒輪相關的振動問題方面的有效性。反映到噪聲方面,就是降低了與之相關的齒輪箱的噪聲聲壓級,如圖7所示。
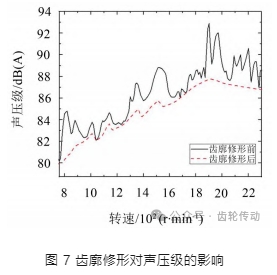
齒輪箱聲壓級隨著輸入軸轉速的升高近似呈線性增加趨勢。這是因為沖量定理m ⋅ Δv = F ⋅ Δt中, Δv是由于齒輪誤差引起的速度改變。齒輪噪聲對于轉速的變化比較敏感,其工作轉速是影響齒輪箱噪聲的主要因素之一。同時,隨著齒輪轉速的升高,齒輪與齒輪之間的嚙合時間縮短,增加了齒輪的振動加速度和動能,齒輪副向空氣中輻射了更多的噪聲。
圖7表明,在進行齒廓修形之前,齒輪箱的噪聲聲壓級曲線在不同轉速下表現出相對較高的幅值。對第4檔齒輪副的齒頂、齒根修形后,不同速度下的聲壓級曲線有明顯的降低。其中,在齒輪箱最大噪聲所在的1 900 r/min工況下,齒廓修形后的齒輪箱聲壓級下降了 5.1 dB(A)。在 820、1 350、1 520 和 1 970 r/min有較明顯聲壓級峰值的工況下,亦產生了2.6~4.4 dB(A)的降噪效果。
綜上所述,以上試驗結果證明了齒廓修形在降低齒輪箱嘯叫噪聲方面的有效性,具有提高齒輪箱聲學舒適性和整體NVH性能的潛力,為解決各行業齒輪箱應用中的嘯叫噪聲問題提供了參考。
6、結語
本文計算了不同齒廓修形量方案對應的嚙合沖擊力、齒輪強度及齒輪性能參數,驗證了齒廓修形對齒輪箱降噪的有效性。主要結論包括以下幾方面:
(1)分別對齒輪齒頂和齒根進行齒廓修形,能夠同時減小齒輪嚙入、嚙出的沖擊,使齒輪平穩傳動,達到減振降噪的效果。
(2)隨著齒廓修形量的增大,嚙合沖擊力逐漸減小,重合度也隨之減小,齒根應力隨之增大。綜合考慮,齒廓修形量不宜過大,5 μm 修形量既可以減小嚙合沖擊力,降低齒輪噪聲,同時對齒根強度和重合度的影響也不至于過大。
(3)基于齒廓修形量、修形長度、齒形公差繪制了用于齒輪齒形檢測的“K”形圖。
(4)在齒輪箱最大噪聲所在的1 900 r/min工況下,聲壓級下降了 5.1 dB(A),修形后的齒輪嚙合噪聲相對于修形前有明顯降低。
參考文獻略.