齒輪是現代機械中最重要的傳動機構。據統計,在各種機械故障中,齒輪失效占失效總數的 60%以上。因此,針對齒輪各種失效模式的研究是有必要的。在各種失效模式中,齒面磨損、點蝕、膠合、剝落和斷裂是最常見的幾種模式。從發力狀態進行分析,這幾種失效模式可以歸為兩大類:一種是齒面接觸應力超載失效,另一種是齒根彎曲應力超載失效。其中,磨損、點蝕、膠合和剝落主要是因為齒面接觸應力超載造成的,而斷裂主要是因為齒根彎曲應力過載造成的。
在齒輪整個制造過程中,大致會經過如下工序:a)鍛造,改善組織,細化晶粒,獲得致密的微觀結構,提高材料的整體性能;b)齒胚制造,經車、銑等方式去除部分材料,使零件初步的成形, 獲得良好的制造基準,為后續加工做好準備;c)齒輪開齒,采用滾齒、插齒和銑齒等工藝方法,使輪齒初步成形;d)熱處理,經加熱、滲碳和淬火等化學方法與工藝,大幅度提高齒輪表面的物理、化學性能,提高齒輪表面的硬度、機械性能和抗磨性能;e)齒輪磨削加工,最終齒輪成形,獲得良好的幾何精度及表面粗糙度,提高齒輪使用時嚙合運動的平穩性、準確性、壽命和可靠性。具體參數和加工方法精確地模擬出齒形,對傳動系統中的強度、可靠性計算具有重要的參考意義。
在上述幾個環節中,開齒留量,齒根過渡圓弧與模數比值,齒根為磨齒準備的沉切量,齒根在熱處理過程中整體脹大、齒輪扭曲變形、橢圓變形、錐度變形對磨齒的影響,所成形的不同磨削臺階高度,磨削圓弧半徑,都對齒輪齒根最終彎曲強度影響極大。
本文模擬常見的幾種齒輪滲碳淬火變形狀態、磨削圓弧半徑和臺階高度等幾個維度,并建模,使用有限元計算方法,對計算后的彎曲應力云圖進行分析,并給予一定假設與解釋,與同行共同探討。
1、齒根過渡圓弧結構模擬與彎曲應力分布
分析軟件及方法
選用 UG NX12 仿真分析軟件,模擬了齒輪滲碳淬火過程中的不同變形量,砂輪不同過渡圓角條件下,形成的不同高度齒根臺階分別進行建模。每組樣本統一建模,統一劃分網格,統一約束,統一受力方向,統一受力點,統一受力值。
分析對象
a)分析對象:某風電增速齒輪箱二級行星輪,嚙合中心距 a=498 mm,五分流;
b)分析對象的具體參數:模數 m=12.8、齒寬 B=275 mm、分度圓 d=530.628 mm;
c)分析對象受力狀態:分度圓上切向力為 735 601.9 N。
模擬維度
模擬以下 6 個維度,即:
a)熱處理后脹大量,符號為 d,單位為 mm;
b)齒面扭曲變形量,符號為 L,單位為 mm;
c)成品齒根沉切,符號為 Spr,單位為 mm;
d)成品保留滾齒圓弧,符號為 ρF,單位為 mm;
e)成品磨削圓弧,符號為 ρg,單位為 mm;
f)成品磨削臺階,符號為 tg,單位為 mm。
模擬方案及計算結果
第一種模擬方案為理想狀態,熱處理后齒輪無脹大無變形,齒輪在磨削時不產生磨削臺階、無磨削圓弧,結構參數如表 1 所示, 其中齒根彎曲應力符號為 δ,單位為 N/mm2 。應力云圖如圖 1 所示,從圖 1 可以看出高應力區居中,兩側應力逐漸遞減。
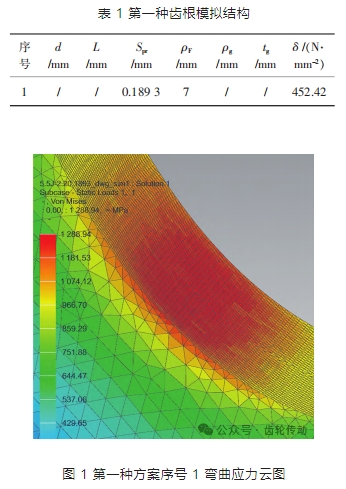
第二種模擬方案為滲碳淬火后直徑脹大,齒向無扭曲變形,磨齒會產生凸臺,磨削圓弧由大變小,產生不同高度的磨削臺階,模擬結構參數如表 2 所示,應力云圖如圖 2~5 所示。
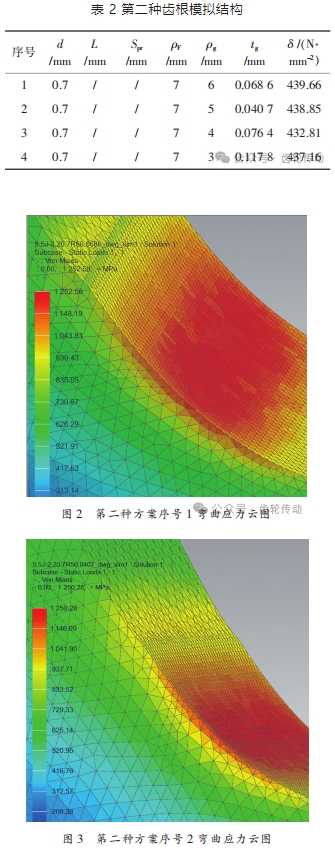
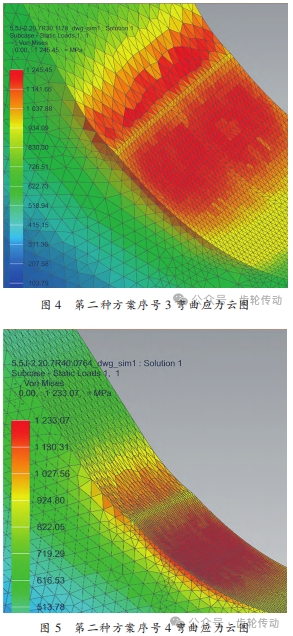
圖 2 中高應力區居中兩側應力逐漸遞減;圖 3 中高應力區居中,兩側非對稱遞減,磨削臺階在遞減區域中應力進一步下降;圖 4 中高應力區分布在磨削臺階兩側,高應力區兩側及磨削臺階為次高應力區;圖 5 中高應力區分布在磨削臺階兩側,主要集中在磨削臺階下部區域,高應力區兩側及磨削臺階為次高應力區。
第三種模擬方案為滲碳淬火直徑脹大,齒向有一定扭曲變形,磨齒會產生凸臺,磨削圓弧由大變小,產生不同高度的磨削臺階因扭曲而進一步增大,模擬結構參數如表 3 所示,應力云圖如圖 6~9 所示。
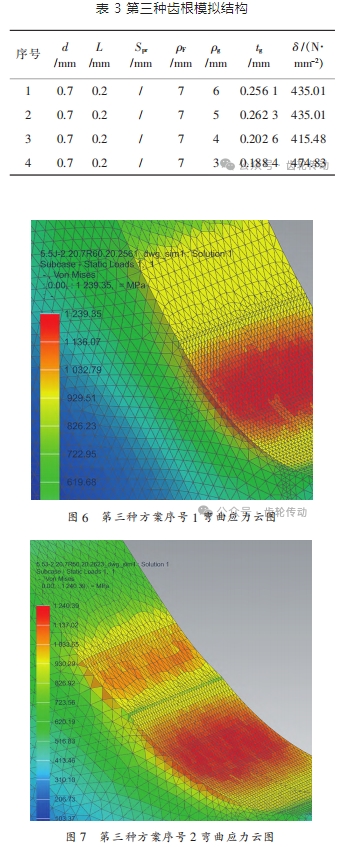
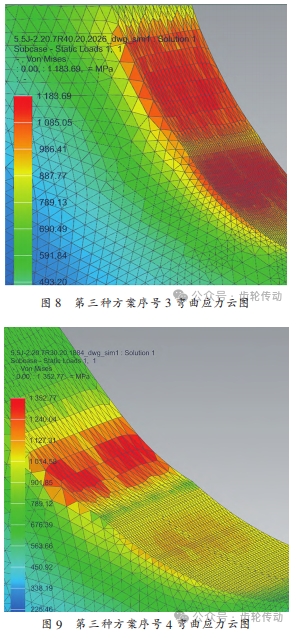
圖 6 中高應力區居中,磨削臺階位于上部次高應力區;圖 7 中高應力區分布在磨削臺階兩側,主要集中在磨削臺階下部區域,磨削臺階為低應力區,高應力區兩側為次高應力區;圖 8 中磨削臺階位于高應力區中部,且高應力區面積占比較大,次高應力區位于兩側,面積占比較小;圖 9 中磨削臺階為低應力區,上部高應力區面積占比較小,下部次高應力區面積占比較大。
第四種模擬方案為滲碳淬火直徑脹大,齒向進一步增大扭曲變形,磨齒會產生凸臺,磨削圓弧由大變小,產生不同高度的磨削臺階因扭曲而再一次增大,模擬結構參數如表 4 所示,應力云圖如圖 10~13 所示。
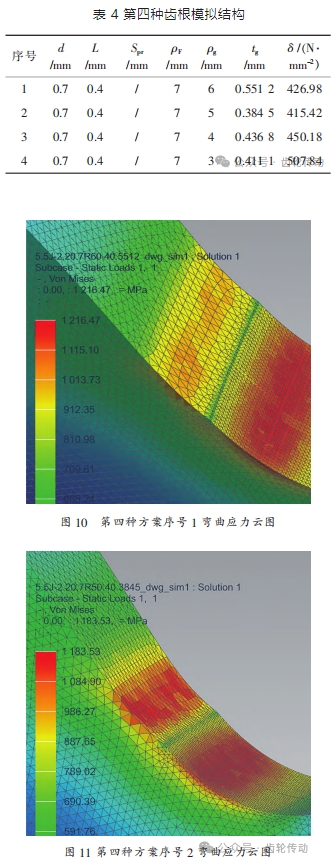
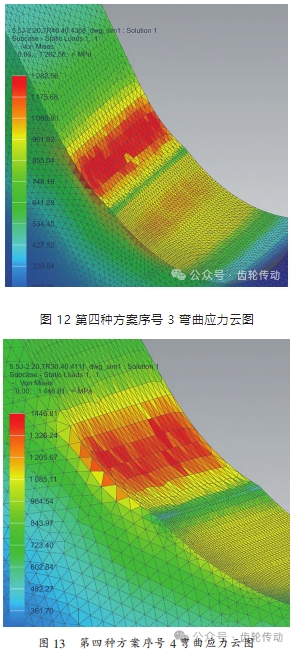
圖 10 中高應力區位于下部,上部次高應力區面積較大,磨削臺階位于低應力區;圖11 中磨削臺階為低應力區,次高應力區過渡, 兩側為高應力區,面積較大,高應力區兩側為次高應力區,面積較小;圖 12 中高應力區位于磨削臺階上部,區域較小,磨削臺階為低應力區,齒根大部分為次高應力區;圖 13 中高應力區位于磨削臺階上部,區域較小,磨削臺階為低應力區,齒根大部分為次高應力區。
齒根結構變化與應力云圖規律總結
a) 齒輪工藝安排為開齒—滲碳淬火—磨齒工序方案條件下,開齒采用留磨量滾刀如圖 14 所示的情況下,因齒根沉切等原因,其彎曲應力并不是最小的。這可從 GB/T 3480-1997 標準 47~48 頁式 (207) ~ (208) 推導出來,因為過大的齒根沉切量減小了 SFn 齒根危險截面齒厚。

b)在經滲碳淬火熱處理直徑脹大,齒根開齒沉切量消失后,齒根彎曲應力與磨削圓弧成不規則的反拋物線形狀,磨削圓弧與模數比值大約在 0.32~0.4 區域最小,如圖 15 所示。

c)在經滲碳淬火熱處理直徑脹大,齒根開齒沉切量消失并有一定齒向扭曲時,齒面扭曲增大了磨削臺階,應力隨磨削圓弧增大而降低,如圖 16~17。
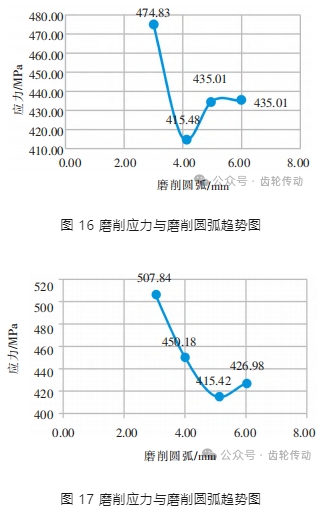
2、產生的疑問及理論解釋
齒面在經磨削成品產生磨削臺階時,根據標準 GB/T 3480-1997,對凸臺測量的方式如圖 18 所示。
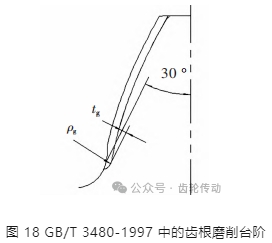
輪齒經磨削,出現齒根磨削圓弧與磨削臺階后,齒根彎曲應力評估及計算為:
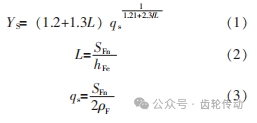
式(1) ~ (3) 中:
YS——齒形系數 YF 聯用的應力修正系數;
SFn——齒根危險截面齒厚;
hFe——彎曲力臂;
qs——齒根圓角參數;
ρF——30 °切線切點處曲率半徑。齒根有磨削臺階齒輪的應力修正系數 Ysg 可計算為:
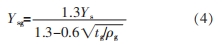
一般認為,產生了齒根磨削圓弧與磨削臺階時,齒根彎曲應力會高于未產生臺階時的應力,與我們上述部分數據不符,因此產生如下疑問。
疑問一:為什么第一種模擬方案相對于第二種模擬方案的應力較大,尤其是對比序號 1?
分析原因為在沒有熱處理脹大時,其存在的沉切 (0.189 3),實際上減小了 SFn 齒根危險截面齒厚,因此彎曲應力大。在經脹大變形后,消除了沉切,實際上增大了危險截面齒厚,齒厚增加應力相應下降。
疑問二:表 2~4 中,在產生磨削臺階的情況下,為什么不是最大磨削圓弧與最小磨削臺階處應力最小?
分析原因為從彎曲應力云圖上可以明顯看出,合適的磨削圓弧與磨削臺階,對齒根最大彎曲應力區域進行了分散與擴張,讓更大的區域共同承擔應力,因此最大應力會適當下降,這一點從應力云圖 2~5 中可以清晰看出,同樣的情況,在應力云圖 6~9 和圖 10~13 中也一樣存在。
還可以從幾何構圖上推導,合適的磨削圓弧 ρg 與凸臺,可以與原滾齒 ρF 在更大區域內形成虛擬齒根圓弧 ρx(如圖 19 所示),增大了 30 °切線切點處實際受力的曲率半徑;隨著曲率半徑的增大,彎曲應力降低。
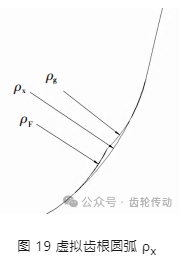
3、在可靠性制造上的運用
可以利用本文的模擬磨削方法,在齒輪熱處理變形后,采用齒輪計量儀或者磨齒機在線檢測儀,在磨齒之前,檢測齒輪熱處理脹大量、齒面扭曲量和齒面磨削余量等數據,分析磨削至尺寸預計產生的磨削臺階高度值,合理設計磨削圓弧半徑來設計磨齒方案,并經有限元建模分析,驗證磨削方案的正確性,以此來提高齒輪制造的可靠性。
在圖 15~16 中,≈0.6,應力最小;在圖 17 中,
≈0.7,應力最小;當 ρg 向 ρF 趨近時,應力會變大,但不會超過無磨削臺階時的應力。
當滿足≈0.6,
≤0.11,且磨削臺階又相對較小時,虛擬齒根圓弧理論成立,設計磨削方案時可以借鑒。
值得注意的是,當臺階超過 0.03 倍模數,且磨削圓弧 ρg 過小時,會引起高應力區向磨削圓弧區迅速集中,會超過無磨削臺階時的應力。
4、結束語
齒輪熱處理變形,對齒根最終成品的可靠性制造至關重要,齒輪磨齒參數的選擇與設置對可靠性的貢獻同樣不可忽視,對既有的已經產生嚴重滲碳淬火變形的齒輪進行事先分析,設計磨削方案,控制磨削圓弧半徑與高度,可以最大限度地提高齒輪的可靠性。本文得到以下結論:
a)零件直徑在一定程度上脹大,磨削后齒根應力比理論計算值會有所降低;
b)磨齒時設置的齒根圓弧及磨齒凸臺的大小,與齒根應力值并不呈線性關系;
c)人為控制磨削圓角半徑,磨削臺階高度的大小可有效地降低齒根應力。
本文僅從結構上進行了分析,下一步可分析滲碳淬火對齒根危險截面處因壓應力增加的貢獻值及影響量,更進一步地反饋齒根的真實應力。
參考文獻略.