1、研究背景
隨著汽車制造技術的不斷發展,汽車舒適性,尤其是振動和噪聲改善成為客戶的重要訴求之一。而動力總成是純電動汽車的動力來源,其振動與噪聲性能和指標是影響汽車舒適性的關鍵因素。在工程實踐中,通過 NVH 測試分析并配合以工程驗證的方式能夠快速識別純電動車的噪聲振動問題,并形成動力總成標準設計優化的流程。“NVH”是噪聲(noise)、振動(vibration)、聲振粗糙度(harshness)的英文縮寫合稱,其通常采取的研究范式是:在一定的物理的環境下,以物體的自然頻率和共振作為重要指標,在時間域和頻率域進行數據采集、分析、計算(包括預測),而后進一步加以評價,并向工程實踐進行反饋和優化建議。常見的 NVH 研究方法有多體系動力學、有限元、邊界元、統計能量分析等方法。
電動車的發展與傳統的內燃機車相比,在動力系統上具有顯著的優勢。同時變速箱作為電動車的重要組成部件,其工況下的振動控制水平直接影響到電動車整車的振動噪聲表現狀況。有效的減緩或者控制電動車變速箱振動噪聲是一項系統性工程,需要充分考慮電動車電動機和變速箱振動噪聲產生的根本機理,同時在此基礎上積極探索優化電動車動力總成的合理設計,包括重點關注齒輪嚙合設計、保證變速箱的動剛度設計,這樣才能有效地減小整車的振動噪聲表現。本文研究了一種考慮整車行駛工況從而指導電動車動力總成設計方法,使電動機、電控及變速箱在整個轉速工況區間與整車 NVH 工況高度適配,有效地抑制了振動噪聲并提升了動力總成系統的綜合效率。
下面以某一款電動重卡動力總成產品試驗型號為例,通過基于整車最佳工況效率的匹配要求,主動避開動力總成結構的共振區間,合理設計優化變速箱的擋位速比和電動機電磁設計,使整個動力總成在滿足整車動力性能要求和減速箱速比基本不變的情況下,通過調整齒輪的齒數,達到基于整車工況的動力總成效率提升、成本的最優設計和 NVH 的最佳狀態表現的工程開發實踐目的。
本案例研究的動力總成為一款針對電動重卡的雙高速電動機匹配四擋變速箱的驅動總成試驗方案。優化前,電動機及原變速箱的參數見表 1 和表 2。為了全面了解雙電動機動力總成原變速箱的振動噪聲表現,本文在實驗室的測試臺架開展了 NVH 試驗測試。

2、NVH 試驗測試臺架
測試臺架主體為電封閉背靠背加載測試臺架,包含主試驅動電動機和變速箱、陪試負載電動機和陪試變速箱、電壓可調的雙向電源、轉矩傳感器以及上機系統。其和傳統電動機對托臺架不同的是,驅動和負載系統由電動機變成了電動機和變速箱構成的動力總成。因此,NVH 試驗測試臺架既可以將電動機或者變速箱作為獨立的被測對象,也可以將電動機、變速箱看作機電耦合系統,作為整體被測對象。
3、測試設備的選擇
高精度數據采集系統使用某品牌 8 通道 ICP 動態信號采集模塊,加速度傳感器應該符合 GB/T 3785.1-2023《電聲學聲級計 第一部分:規范》規定的 1 級儀器要求,其測量儀器頻率范圍至少為 10 ~ 10000Hz。振動加速度計的測量裝置選擇 B02B01,頻響范圍±5%:1~10000Hz,靈敏度±5%:10mV/g,量程 peak:±500g。
本次試驗的高精度數據采集器選擇 140kHz 采樣率,振動加速度傳感器在測量前都進行了標定。測量前后,儀器按照規定進行校準,兩次校準值不應超過 1dB。
振動加速度傳感器的測點位置如圖 1 所示。在臺架上的實際測試測點如圖 2 所示。
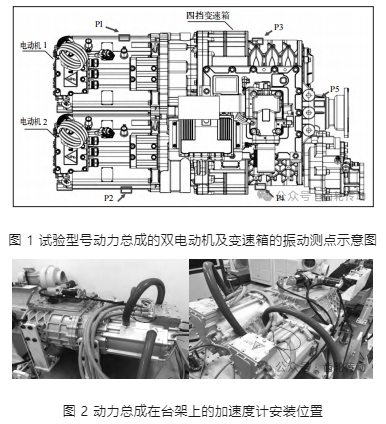
由于在臺架測試房半消聲室的測試環境暫未完成設置,當前評估動力總成的振動特征,為了確定動力總成的固有頻率,在測試臺架上由靜止狀態等步長啟動電動機,主觀評價發現動力總成在電動機轉速 7000 ~ 8300r/min 區間有明顯間歇性抖動,且能聽到持續轟鳴顫抖聲。
因為動力總成是雙電動機、雙中間軸變速箱的對稱結構設計,振動特性差異不大,所以試驗選取了 P1、P4、P5 三個測點的振動信號進行分析,重點分析電動機從 0 ~ 11000r/min 的 P1、P4 及 P5 振動測試點升速過程瀑布圖,3 個測點的振動瀑布云圖(時頻圖)分別如圖 3、圖 4、圖 5 所示。
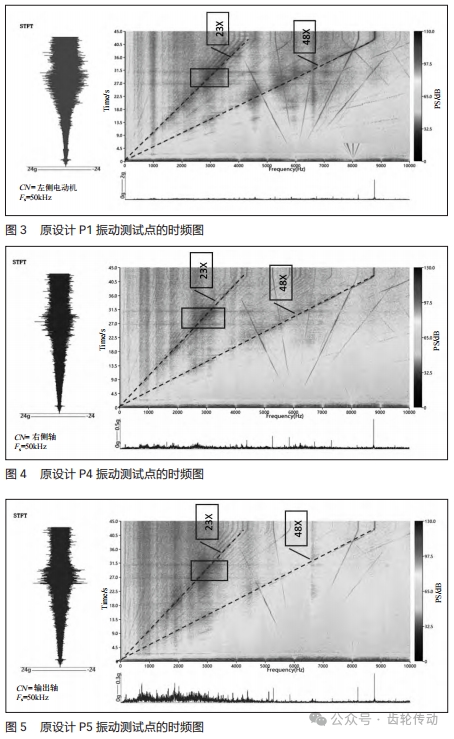
根據圖 3 ~ 圖 5,可以明顯發現在 7000 ~ 8300r/min 轉速區間的升速運行工況,動力總成在測試臺架上的狀態有很明顯的間歇性振動抖動。同時,動力總成組件在 2900 ~ 3200Hz 有一個明顯的結構共振帶。經比對發現,電動機 24X 電磁諧波與減速箱 23X 齒輪箱嚙合頻率的激勵信號剛好在 7000 ~ 8300r/min 與該組件的共振帶有相遇。所以,動力總成整機表現出通過該轉速區間的振動抖動加劇。
4、優化設計的思路與優化措施
為了解決上述加速過程在 7000 ~ 8300r/min 轉速區間的間歇性振動抖動明顯加劇的情況,本文在不去改變電動機電磁設計的條件下,對變速箱的齒數做了優化設計,具體齒輪箱優化設計的思路與優化措施如下。
優化措施
(1)為了避開動力總成組件在 2900 ~ 3200Hz附近的結構件共振帶,調整齒輪的齒數及相應的嚙合階次。在保證現有速比不變的前提下調整齒數:
①原方案齒輪箱輸入級齒輪組的齒數是23齒和88齒,減速比為 88/23=3.826 ;
②優化后齒輪箱輸入級齒輪組的齒數是28齒和107齒,減速比為 107/28=3.821,接近 3.82,基本保證速比基本不變。
本優化措施能達到以下增益效果:在不改變速比的前提下將輸入齒輪齒數調整到 28 齒,能遠離電動機的 24X 階主諧波階次及其倍數階次,避免關鍵諧波振幅的疊加。
(2)在保證現有速比和中心距 不變的前提下,提升齒輪的嚙合重合度同時減小齒側間隙,以減小傳遞誤差來降低動力總成傳動機構的振動噪聲幅值:為提升齒輪嚙合重合度,將齒輪模數由原來的 2.5 改為 2.03,同時將齒頂高和齒根高系數由原來的 1.2/1.4 提升到 1.3/1.5,螺旋角由 22°增大到 24°,法向側隙區間由原來的 0.135 ~ 0.227mm 改成 0.117 ~ 0.206mm。
本優化措施能達到以下增益效果:在保證現有速比和中心距不變的前提下將齒輪嚙合重合度由原來的 3.251 提升到了 4.204,提升 29% ;傳遞誤差差值,由原來的 0.8849μm(–17.1837–(–18.0686))降低到了 0.2109μm(–17.8162–(–18.0271)),降低了 76% ;接觸強度安全系數由 1.165 提升至 1.252。
原方案、優化后齒輪嚙合重合度及彎曲和接觸強度安全系數分別如表 3 和表 4 所示。原方案、優化后的傳遞誤差曲線分別圖 6 和圖 7 所示。
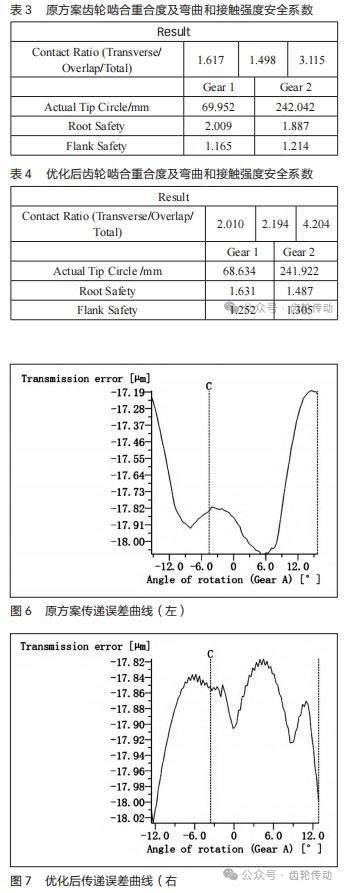
把電動機齒數換為 28 齒進行測試,為了保證速比沒有太大變化,嚙合齒數換成 107 齒,優化變速箱的傳動設計參數變速箱參數如表 5 所示。
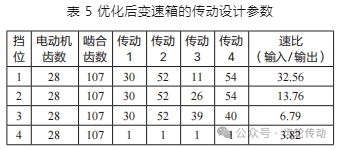
為了驗證上述減速箱優化設計的效果,把換齒后動力總成在臺架上復測上訴同條件的加速測試。試驗依然選取了 P1、P4、P5 三個測點的振動信號進行對比分析。換齒后的動力總成從 0 ~ 11000r/min 的 P1、P4 及 P5 振動測試點升速過程瀑布圖分別如圖 8、圖 9、圖 10 所示。
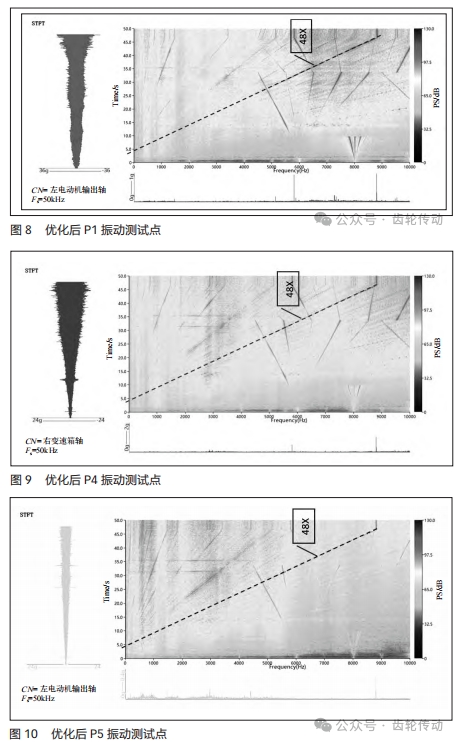
為了驗證減速箱設計優化后在 7000 ~ 8300r/min 轉速區間的振動抖動情況是否有改善,本文對 7500r/min 時刻 P1、P4、P5 三個測點對應的 FFT 曲線進行優化前后對比,分別如圖 11、圖 12、圖 13 所示。
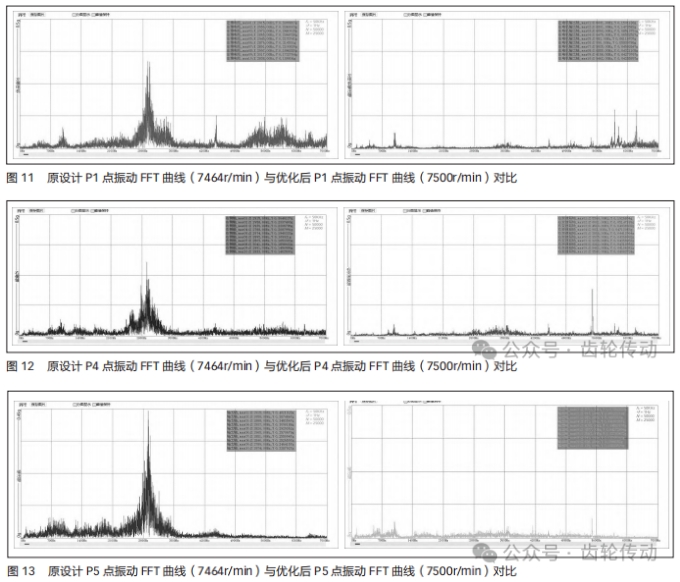
各關鍵諧波階次的振動幅值及振動有效值對比列表如表 6 所示。
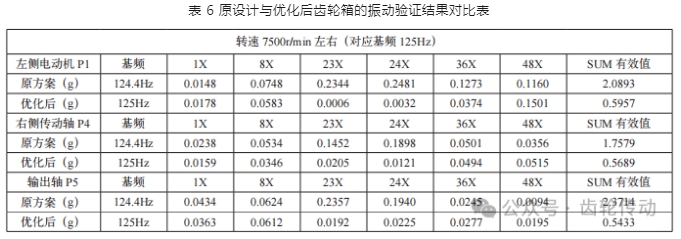
齒輪優化設計前后的改善分析結論
(1)從表 6 可以看出,齒輪齒數從 23X 調整到 28X 后,不但各個關鍵諧波階次的振動幅值有下降,振動的有效總值也有明顯的下降改善;
(2)齒輪齒數的改變,使齒輪嚙合階次遠離電動機的電磁諧波 24X 階,減小了加速過程中引發共振的概率,間接降低了動力總成的振動和噪聲;
(3)重合度增大和齒側間隙減小,使齒輪的傳遞誤差減小一半以上(0.8849μm 降低至 0.2109μm),傳遞誤差的減小可以直接降低齒輪的嚙合振動和噪聲;
(4)經過上述優化后,齒輪接觸疲勞強度更強(安全系數由 1.165 提升到 1.252)。
5、結語
本文通過某一款電動重卡動力總成產品試驗型號在實驗室測試臺架上的 NVH 測試分析及數據對比,詳細研究了動力總成產品在等步長升速 過程間歇性振動抖動對應問題點的振動噪聲頻譜特征,提出了避開結構共振帶的齒輪設計優化方案的改善分析路線,并實施了變速箱齒輪齒數與相 關優化控制策略優化。動力總成完成齒輪箱換齒后的上臺架復測結果表明:該款試驗型號動力總成各個關鍵諧波階次的振動幅值均有明顯下降,振動有效值也有明顯下降。
參考文獻略.