軸齒類零件在工業技術中有著非常廣泛的應用。工業機器人減速器輸入軸零件結構復雜,其一端為齒形結構,另一端具有盲孔,孔內設有鍵槽,其主要作用是傳動扭矩,且工作條件較為苛刻,要求其具有優良的耐磨性、抗接觸疲勞強度和抗彎曲疲勞性能。滲碳淬火是使工件表面獲得高硬度以提高服役可靠性和耐磨性的常用熱處理工藝。為了使工業機器人減速器軸齒類零件獲得良好的耐磨性能,同樣需要對其進行滲碳淬火處理。此類軸齒類零件最常用的滲碳工藝為氣體滲碳,如中國專利“一種減小齒輪軸鍵槽變形 的熱處理工藝”介紹,采用氣體滲碳工藝,在保護氣氛環境中進行升溫保溫滲碳處理,具有滲碳成本低、速度快、滲碳質量穩定、滲碳氣氛容易控制、滲碳層表面質量易于控制等優點。然而,在傳統氣體滲碳工藝中,通常采用氮-甲醇作為載氣,由于甲醇低溫裂解存在爆炸的安全隱患,因此用可控氣氛多用爐或井式爐實施氣體滲碳時,在 750 ℃ 以下工件不能實現保護氣氛下的預熱和保溫,通常需要快速升溫至 800 ℃ 以上才能進行滲碳處理。這就導致從低溫階段升溫過程中 工件可能發生加熱畸變。在這種情況下,工業機器人減速器軸齒類零件的鍵槽變形和齒形畸變量甚至可達到 0.03 ~ 0.05 mm,這對于精密機械來說,已不能滿足其熱處理技術要求。并且,氣體滲碳工藝無法保證在零件盲孔內形成足夠的滲層深度,滲碳質量不易控制。
真空低壓滲碳是傳統氣體滲碳工藝的升級,是熱處理高質量發展和低碳化發展的必然趨勢。利用乙炔真空滲碳技術和高壓氣淬技術對鋼制零件表面進行滲碳淬火處理,不僅沒有碳排放,而且由于可 使用更高的滲碳溫度,使零件滲碳速度加快,快速達到預定的深度從而提高滲碳淬火零件的生產效率,具有安全、低碳、高效和環保等特點,并且零件的盲孔滲碳可以有效避免滲層表面出現內氧化是真空低壓滲碳所特有的優勢。工業機器人減速器的軸齒類零件精 度要求非常高,其齒形畸變量要求控制在 0.015 ~ 0.025 mm之內,而現有真空低壓滲碳技術對此類鍵槽和齒形畸變量過大的問題沒有現成的解決方案。因此,根據此類軸齒類零件的結構特點和精度要求,有必要對現有的真空低壓滲碳工藝進行針對性開發,開展典型機器人用軸齒類零件的少無畸變真空低壓滲碳、高壓氣淬熱處理工藝研究,優化熱處理工藝,完成典型機器人用軸齒類零件的真空低壓滲碳、高壓氣淬工藝示范應用,同時達到減少碳排放的目標。
1、試驗材料與方法
試件材料及技術要求
試驗零件為機器人行星減速器中的輸入軸,材料為 SCM420 鋼,主要化學成分見表 1,符合JIS G 4053- 2008 Low-alloyed steels for machine structural use 要求。圖 1 為輸入軸簡圖和齒部畸變檢測位置。
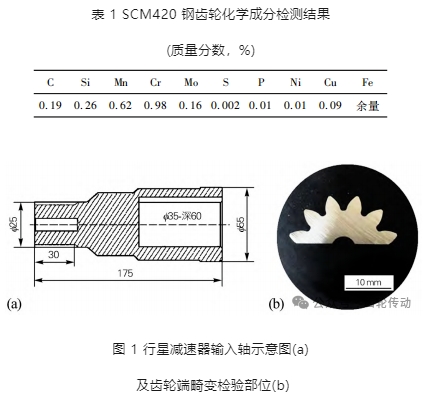
輸入軸制造工藝流程為: 下料—粗車—正火—檢驗—機加工—滲碳淬回火—檢驗—拋丸—磨齒—檢驗—清洗—包裝入庫。該齒軸的最終熱處理為滲碳淬火,要求硬化層深度為 0.425 ~ 0.725 mm,表面硬度為 58 ~ 62 HRC,心部硬度為 30 ~ 40 HRC。顯微組織檢驗按照 GB /T 25744—2017《鋼件滲碳淬火回火金相檢驗》進行。
此外還要求,馬氏體、殘留奧氏體、碳化物和心部組織級別均為 1 ~ 2 級,齒輪精度要求達到 JISN3 級 ( JIS B1702) ,齒溝振動≤0.028 mm,齒形、齒筋變形量 ≤0.015 mm。圖 2 為該輸入軸滲碳淬火畸變測試取樣爐內位置圖。
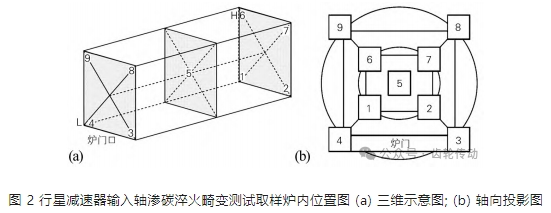
試驗工藝
試驗裝備為國產雙室真空低壓滲碳高壓氣淬真空爐,滲碳淬火工藝如圖 3 所示。在升溫階段,爐內真空度控制在1 Pa 以下,依次將工件升溫至(300 ±5) ℃,均溫 30 min; 升溫至(480 ± 5) ℃,均溫 30 min; 升溫至 (680 ± 5) ℃,均溫 30 min; 升溫至(780 ± 5) ℃,均溫 30 min; 升溫至(850 ±5) ℃,均溫 30 min; 升溫至 950 ℃, 經過多段升溫和均溫后進行滲碳。
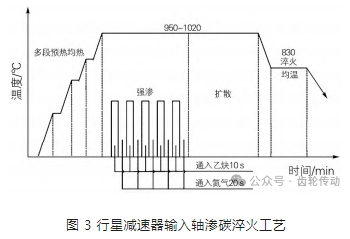
在滲碳階段,將爐壓控制在 850 ~ 880 Pa,強滲階段通入乙炔氣體保持 10 s 后再通入氮氣 20 s,作為一個滲碳脈沖周期,整個強滲階段由 5 個滲碳脈沖周期組成,在強滲階段利用氮氣對爐內產生的廢氣進行排氣。滲碳結束,在爐內冷至 830 ℃ ,用氮氣進行淬火,壓力為 1.8 MPa (18 bar) 。淬火流體流向、流速、過程變換等由真空滲碳高壓氣淬爐附帶軟件自動控制。
測試方法
將真空低壓滲碳高壓氣淬后的試樣研磨拋光,用體積分數 4% 的硝酸酒精溶液侵蝕,依 GB /T 9450— 2005《鋼件滲碳淬火硬化層深度的測定和校核》和 GB /T 25744—2010《鋼件滲碳淬火回火金相檢驗》測定有效硬化層深度、碳濃度及滲碳層組織、滲層馬氏體、殘留奧氏體和碳化物級別等。滲層硬度用 MVA- 40ETS 型顯微硬度計檢測,滲層和心部組織用 LV150NL 型顯微鏡觀察分析,淬火齒輪精度、齒溝振動和齒形畸變等用 TTi-300E 型齒形測試儀參照 JIS B 1702《圓柱齒輪 ISO 精度體系》在圖 1( b) 所示的實體工件上測量。
2、試驗結果與分析
碳濃度、有效硬化層深度、表面硬度與心部硬度
采用真空低壓滲碳和高壓氣淬技術對機器人減速器輸入軸進行熱處理,對處理后的零件進行抽檢。9 點測試表面碳含量在 0.65% ~ 0.68% 范圍,符合 0.66% ± 0.05% 的要求。有效硬化層深度為 0.61 ~0.69 mm (550 HV0.3) ,9 點測試偏差范圍在 0.03 ~ 0.08 mm,滲碳層深度偏差≤ ± 0.05 mm,符合設定滲層 0.65 mm的要求。9 點測試表面硬度為59.6 ~60.0 HRC,平均值為 59.7 HRC(滿足 58 ~ 62 HRC 的要求) ,硬度 偏差≤ ± 1 HRC,心部硬度和有效滲碳層深度均值分別為 38. 6 HRC 和 0. 681 mm,符合技術要求。圖 4 為滲碳層硬度分布曲線和相應的碳濃度分布曲線,兩條曲線保持一致,各項指標均達到或超過技術要求。
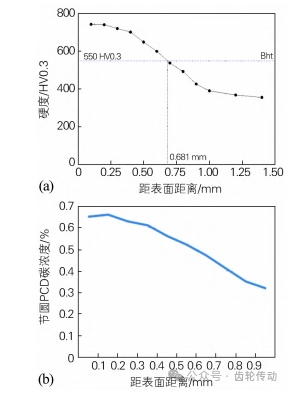
圖 4 行星減速器輸入軸滲碳層硬度分布曲線(a) 和相應的碳濃度分布曲線(b)
滲層組織
圖 5 為輸入軸齒部節圓處的滲層組織和碳化物分布形貌。如圖 5 所示,輸入軸滲碳層中的馬氏體為 1 級,殘留奧氏體和碳化物為 1 ~ 2 級,達到優質產品的技術要求。
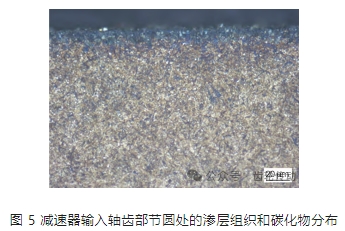
圖 6 為輸入軸齒部節圓處滲層表層的晶間氧化 (IGO) 情況。晶間氧化又稱內氧化,研究認為是由 Cr、Mn、Si 等易氧化元素與氣氛中微量的氧結合形成氧化物,使晶界附近基體合金元素貧化,常出現在可控氣氛滲碳過程中。產生內氧化及合金元素的貧化后,會使其附近奧氏體的穩定性降低,淬透性不足,在隨后的淬火過程中極易發生分解,形成屈氏體和貝氏體等混合組織,一般 ME 級精密齒輪對其都有嚴格的限制。如圖 6 所示,真空低壓滲碳和高壓氣淬的輸入軸在齒部滲層表面未出現晶間氧化情況。
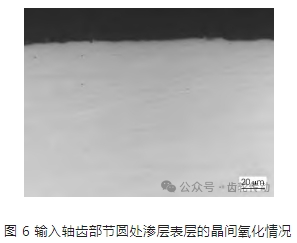
圖 7 為輸入軸齒部節圓處的心部組織照片。如圖 7 所示,輸入軸滲碳淬火后心部組織級別為 1 ~ 2 級。
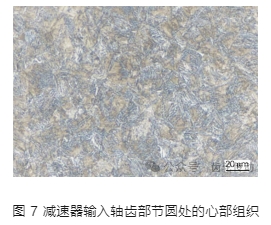
齒形畸變
表 2 為輸入軸真空低壓滲碳高壓氣淬后齒形的畸變情況。由表 2 可見,該軸齒類零件在圖 2 所示的各測試點,畸變量全部控制在 0.005 ~ 0.015 mm 之內。
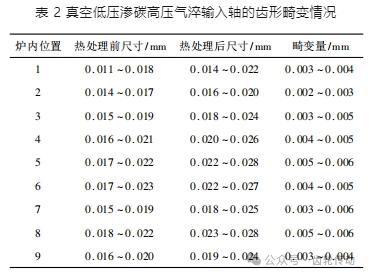
3、討論
多階段預熱
由于真空加熱的換熱特點,真空爐內進行低壓滲碳一般在爐溫到達滲碳溫度之后仍需保持一段時間,這個階段稱為“均熱(Soaking) ”,它有兩個作用,一是使工件本身均溫,另外實現裝料間的均溫; 二是利用真空加熱特點清理工件表面,以便于隨后滲劑與工件間均勻接觸,這對帶深孔盲孔等不易清洗部位的工件尤其重要。當用乙炔作為滲碳介質時,工件均溫時間一般為: 低于 955 ℃時每 25 mm 約 1 h; 高于 955 ℃ 時每 25 mm 40 ~ 45 min。鑒于此,本試驗設計了更加合理的均溫工藝措施,采用了多階段升溫均溫的辦法,一方面使工件升溫速度更加平穩,有利于消除輸入軸前期多道次復雜加工的殘余應力和升溫的熱應力,另外,有利于縮短工件在高溫時的均溫停留時間。數據表明,多階段升溫均溫的辦法對于提高滲層均勻性和減少工件畸變都是有益的。
乙炔滲碳
乙炔的結構式為 H-C≡C-H,為不飽和烴,由一個三鍵將兩個碳原子相連。乙炔在真空及滲碳溫度下的分解反應如下:
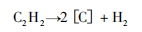
該反應為吸熱反應。乙炔裂解反應有兩個主要特征,一是一個乙炔分子可分解出兩個活性碳原子; 二是乙炔分解必須借助于熾熱的金屬表面。在真空爐內滲 碳高溫下,乙炔不會發生聚合反應生成焦油等物質。故不難看出乙炔較丙烷作為滲碳介質有突出優點,首先乙炔可供的碳量遠大于丙烷,用乙炔作滲碳介質可在很低的壓力下進行; 乙炔要借助于工件表面裂解,工件表面的潔凈程度直接決定了裂解的完全程度和滲碳的均勻程度,故在強滲階段,工件表層奧氏體可在極短時間內達到完全飽和,隨即進行擴散,擴散后表層所需富化的碳量由后續脈沖補上,補充量根據鋼材種類和滲碳溫度進行計算。
碳利用率和碳勢控制
由于沒有多余的碳向滲碳環境逸出,乙炔在低壓滲碳過程碳的利用率極高,在合理計算的脈沖工藝參數下,可完全消除碳黑的形成,同時有利于復雜幾何形狀零件包括盲孔深孔件的滲碳。只要裝爐量和裝料布局合理,可解決滲層均勻性及密集裝料等生產實際問題。
不同于氣氛滲碳,真空乙炔滲碳系統中沒有含氧反應氣體,如 CO2和 H2O,也不存在單純的氧氣,所有傳統氣體滲碳的碳勢測量和控制措施都不能在真空滲碳過程發揮作用,故真空低壓滲碳沒有所謂“碳勢”控制的問題。在這種情況下,最重要的參數是碳質量流的密度,定義為單位表面積和單位時間內進入材料的碳量。在零件表面上獲得的碳濃度就是由該參數作為供氣量、擴滲程度、界面層質量傳輸系數和材料內的擴散速度的函數確定的。如前所述,所有這些變量都和滲碳鋼材種類和滲碳溫度有關。通過在滲碳溫度下周期式地向工件表層傳輸滲碳介質、飽和滲入,再經過擴散,達到設計的碳濃度分布。即根據工件要求的滲層厚度、材料特性、裝料總面積及裝料量等用計算機模擬軟件程序來控制通入爐內的滲碳介質的傳輸量,來達到控制滲層的目的。故目前真空滲碳有兩種基本模式: 一種是氣體交替,壓力不變,乙炔-氮氣循環充入,用于一般工件的低壓滲碳; 另一種是壓力脈沖,乙炔氣充入-反應廢氣抽出。如此重復,通過壓力調節,用于盲孔與深孔工件的滲碳,脈沖滲碳的滲層均勻性更好,故采用了后者。
碳化物及殘留奧氏體
由于滲碳劑的供給經過了嚴密的計算和按需控制,真空低壓滲碳工件表面的碳濃度容易實現產品圖紙要求的目標控制,從而有效控制工件表層的碳濃度及碳化物的形成和數量。經過多次反復工藝試驗確定的滲碳過程參數獲得了滿意的結果。由于控制了工件表面的碳濃度,殘留奧氏體量也得到了有效的控制,從輸入軸滲碳淬火回火后的硬度及實際測量結果都可以看出,本零件不存在殘留奧氏體超標的問題。
滲碳速度
根據滲層深度 δ 和滲碳時間 τ 的關系 δ = A·τ1/2 ,滲碳溫度每提高 10 ℃,滲碳常數 A 提高 1.06 倍。由 930 ℃提高到970 ℃,滲碳常數 A 提高1.26 倍,由930 ℃ 提高到 1000 ℃,滲碳常數 A 提高 1.43 倍,由 970 ℃提高到 1000 ℃,滲碳常數 A 提高 1.14 倍。同時,與以往滴注式可控氣氛滲碳相比,滲碳時間大幅度縮短。以 1.2 mm 滲碳層深為例,采用可控氣氛滲碳及擴散時間一般在 8 h 左右,而采用真空高溫低壓滲碳爐滲碳僅需 5 ~ 6 h。在 930 ℃ 真空低壓滲碳,當有效滲碳層深度為 0.8 mm 時,可節省滲碳時間 31% ; 在 960 ℃,當滲碳層深度為 1.6 mm 時,可節省滲碳時間 21%。本項目中實際采用的真空低壓滲碳溫度為 950 ℃ 以上,比可控氣氛滲碳高出 20 ℃ 以上,在本項目要求的滲碳層深度 0.425 ~ 0.725 mm 范圍內,實際工藝時間縮短約 30% 。
高壓氣淬
高壓氣體淬火與有物態變化的液態冷卻介質(油或水) 相比,最大的區別在于高壓氣體淬火只有對流一種換熱方式,淬火冷卻時熱交換過程穩定,工件淬火的熱應力和組織應力也就變得相對穩定,而且氣壓、氣流速度、方向柔性可調,增加了對不同工件和裝料方式的冷卻適應性,降低了液體淬火介質蒸氣膜、沸騰和對流 3 階段因換熱特點、換熱效率不同及冷卻速度突變和不穩定等給工件帶來應力狀態復雜多變,而增加工件畸變的風險。輸入軸經穩定壓力的 1.8 MPa (18 bar) 高壓氮氣淬火后,工件表面在處理前后光亮如一,清潔免洗,有效控制了滲碳輸入軸的淬火齒形畸變。同時,消除了原來油淬的碳排放,做到了清潔生產。
4、結論
機器人減速器輸入軸采用真空低壓滲碳和高壓氣淬技術,經滲碳淬火后其滲層組織、硬度、畸變量等結果如下:
1) 輸入軸經真空低壓滲碳高壓氣淬后滲碳層中馬氏體為 1 級,殘留奧氏體和碳化物為 1 ~ 2 級,心部組織為 1 ~ 2 級; 滲碳層偏差≤ ± 0.05 mm,完全滿足GB/T 25744—2010 滲碳層深度應在 0.1 ~ 0.2 mm 的要求。同時,經真空低壓滲碳后,零件表面無內氧化,滲碳質量明顯提高。
2) 滲碳時間比可控氣氛滲碳縮短 30%,免除了清洗工序,生產用電、用氣成本和總工時都得以降低,效益明顯。
3) 與油淬相比,輸入軸采用高壓氣體進行淬火,硬度達標,畸變量小。全爐 9 點測試表面硬度均值為 59.7 HRC,心部硬度均值為 38.6 HRC,有效硬化層深度均值為 0.681 mm。9 點檢測畸變量全部控制在 0.005 ~ 0.015 mm。
參考文獻略.