重載齒輪傳動在運行時承受較高的應力,這容易引發疲勞斷裂。非金屬夾雜物的存在是滲碳齒輪鋼疲勞斷裂的主要原因之一,且夾雜物的尺寸越大,齒輪鋼的疲勞壽命越短。研究表明,鋼中總氧含量與夾雜物數量呈正相關,氧含量越高,夾雜物越多,檢測的夾雜物尺寸就越大,從而顯著降低齒輪的疲勞壽命。隨著全球生產技術的進步,齒輪鋼氧質量分數已從 25×10-6 降至 11×10-6,使得齒輪鋼的接觸疲勞強度提升了 4 倍。因此,日本將齒輪鋼鍛件的技術標準中氧質量分數要求調整為不超過 15×10-6,歐美等國家也將標準修訂為 20×10-6 以內,我國同樣將齒輪鋼的氧質量分數要求限制在 20×10-6 以內。然而,隨著國內齒輪制造業的激烈競爭,齒輪設計者越來越注重齒輪的極限壽命,安全系數的選擇也不再像過去那樣保守,這導致齒輪制造商對鍛鋼件技術協議中氧含量的要求日益提高。
鋼中的氧含量主要以夾雜物的形式存在,鋼水經過 LF 和 RH 精煉后,夾雜物成分、形貌、數量等都會發生變化,整個精煉過程對夾雜物控制有顯著作用。Zhang 等研究不同初始鋁氧濃度積對鋼包精煉過程的最終氧含量過程的影響,鋼中的溶解鋁含量越高,精煉后鋼中的溶解氧含量越低。Wang等研究發現當鋼中的 Al 質量分數為 0.03%時,鋼中溶解氧質量分數可以達到(3~5)×10-6,T.O 質量分數可以控制在(11~12)×10-6。董文亮等對 28MnCr5 鋼中鎂鋁尖晶石夾雜物的平衡條件進行研究,認為 SiO2 是鋼中氧含量的主要來源,當低碳齒輪鋼的氧質量分數達到 10×10-6 以下時,滿足超低氧鋼的要求。
研究表明,VD+IC(investment casting,模鑄)工藝在超低氧齒輪鋼的生產中并不常見,這可能與模鑄規模有限、冶煉過程控制復雜、澆鑄過程中與耐火材料的接觸時間較長等因素有關。鑒于此,本文開發了一種采用“EBT+LF+VD+IC”流程的低碳重載齒輪鋼生產方法,旨在為超低氧純凈鋼的冶煉提供技術指導。
1、冶煉工藝設備及鋼種
生產設備及工藝流程
主要生產設備:50 t EBT 電弧爐、60 t LF 以及 60 VD 真空精煉裝置及氬氣保護模鑄。
在原工藝流程中,EBT 電弧爐出鋼的控制要求為:w(C)≥0.05% 、w(O)≤550×10-6、w(P)≤0.003 %,并添加鋁錠,其用量為 60 kg/t。在 LF 精煉階段結束前 10 min 進行增碳處理,確保成分符合鋼種內控標準要求后,將鋼水送入 VD 裝置進行真空脫氣。脫氣完成后,按 1.5 kg/t 的比例加入碳化稻殼,隨后進行取樣、測溫、定氫、定氧等操作,待成分合格后進行軟吹。當鋼水溫度達到 1 560~1 580 ℃時,啟動全程氬氣保護澆鑄,完成后檢測鋼錠的氧含量。
鍛鋼件技術條件
重載齒輪鋼鍛件驗收標準對鋼種化學成分要求如表 1 所示,重載齒輪鋼對氣體氧含量及鋁含量要求很低,其它成分冶煉技術難度不高。非金屬夾雜物按照 GB/T3480.5—2021 標準中滲碳淬火鍛鋼 ME 級要求,夾雜物檢測指標較低,工藝能滿足檢測指標要求。

2、氧含量偏高原因分析
通過對優化之前 50 爐的重載齒輪鋼鍛件氧含量統計分析(見圖 1),發現鍛件氧質量分數的波動符合正態分布函數,其中樣本均值為 11.1×10-6,標準差 4.11。當鍛件氧質量分數要求 9×10-6 以下時,不合格爐數占比為 56%,冶煉工藝無法穩定滿足鍛鋼件標準的氧含量要求,需要進一步分析氧含量波動的原因,并重新開發新的冶煉工藝流程。
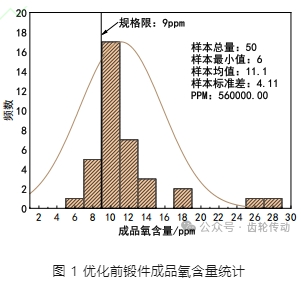
電爐冶煉對氧含量的影響
在實際生產中發現,電爐出鋼的溶解氧含量與出鋼碳含量之間存在一定關聯,根據圖 2 關系表明,當出鋼 w(C)=0.02%~0.16%時,隨著碳含量的增加,氧含量呈下降趨勢,但下降速率逐漸減緩。利用簡單方程描述了這種關系,其 R2 值為 0.984 09,顯示模型與數據之間高度相關。觀察曲線下降速率可知,當出鋼 w(C)>0.065%時,氧含量降低速度減緩;當 w(C)>0.12%時,氧含量基本不再變化。因此,將原工藝出鋼 w(C)≥0.05%優化為 w(C)=0.065%~0.12%,以減少出鋼氧含量。此外,降低出鋼氧含量可減少鋁錠的加入量,減少鋼液夾雜物含量,提高鋼液中溶解鋁含量,降低鋼包內鋼水溶解氧,實現降低最終產品氧含量的目標。
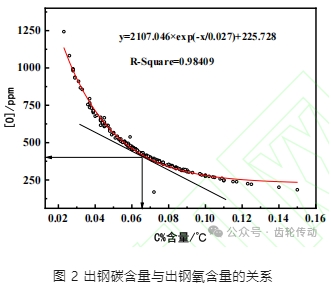
精煉過程對氧含量的影響
通過使用 LECO 氧氮氫分析儀和賀利氏在線定氧儀,對精煉過程、VD 真空精煉過程以及鋼錠氧含量進行了詳細分析(見圖 3)。分析不同時間段的 T.O 數據,精煉過程的 w(T.O)在(9~11)×10-6 波動,整體波動較小。在整個取樣過程中,出現了兩次波動。第一次波動發生在鋼包精煉結束后進入 VD 真空精煉爐階段;第二次波動發生在成品氧含量檢測階段。
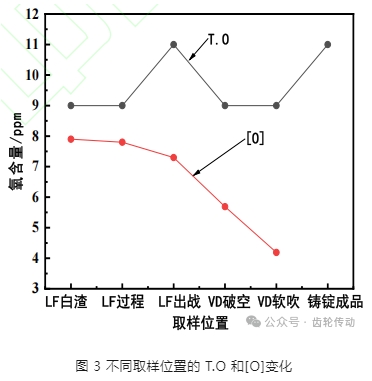
第一次 T.O 含量波動的主要原因包括:在出鋼之前,碳含量未滿足鋼種成分要求,需要補加碳粉,并通過氬氣強力攪拌使碳粉快速溶解,導致鋼液中夾雜物增加,從而使得 T.O 含量升高。另外,增碳時,碳會漂浮在鋼渣表面,需要增大電流提高渣液面的攪動,使表面碳粉快速溶解,碳在溶解過程中與爐渣中的礦物質發生反應,生成新的夾雜物,導致鋼中的氧含量增加。第二次 T.O 含量波動可能是由幾個因素造成的,包括澆鑄過程中的二次氧化、耐火材料的侵蝕產物以及鋼錠模內卷渣等。
因此,針對以上兩次 T.O 含量波動采取如下措施:在第一次真空脫氣后返回 LF 精煉工位,更換鋼液面的部分爐渣,并重新造渣,調整溫度后再次進入 VD 真空脫氣,以提高爐渣的吸附能力并促進夾雜物的去除。同時,為了減少出鋼液面的波動并降低夾雜物的產生,建議將 LF 鋼包結束前的增碳方式由加碳粉改為喂碳線。
爐渣成分對夾雜物的影響
利用掃描電鏡對鍛件成品試樣中 10μm 以上的夾雜物進行掃描,掃描結果如圖 4 所示,夾雜物主要為鋁鈣復合型夾雜物,占比在 82%左右,其最主要形式為 12CaO·7Al2O3、CaO·Al2O3、CaO·2Al2O3 和 CaO·6Al2O3,夾雜物的總數為 48 個。導致鋁鈣型夾雜物偏多可能與爐渣中氧化鈣的含量有關,爐渣中的 CaO 含量高,導致鋼中的 Ca 含量增大。從式(1)~式(4)可知,溶解 Ca 含量增加就會導致鋼中相應類型的夾雜物的生產,利用 XRF 爐渣分析儀對鋼渣的成分進行分析,爐渣 w(CaO)=71.86%,而理論 w(CaO)應該控制在 49%~56%。

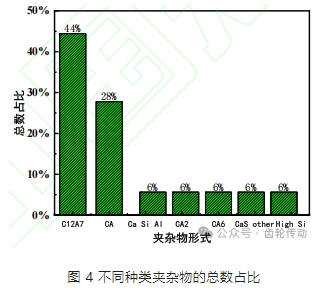
3、工藝優化前后對比
優化方案
優化工藝的主要目的是降低 EBT 出鋼的氧含量,減少鋼中夾雜物的產生;改變 LF 精煉爐渣成分,提高爐渣的吸附性,促進夾雜物上浮。因此在原生產工藝基礎上進行了改進,包括:在 EBT 電弧爐出鋼時控制氧含量,將 LF 精煉的增碳方式從加碳粉改為喂碳線,并在精煉中增加 1 次 LF 換渣和 1 次 VD 真空脫氣操作。LF 鋼包精煉結束后,鋼水包進入 VD 爐進行真空脫氣,抽真空時間控制在 10 min 左右,真空壓力在 63 Pa 以下,真空結束后,鋼水包被吊回 LF 精煉工位換渣、加熱、脫氧,并在達到規定溫度后喂鋁線深脫氧。精煉結束以后,鋼水包會再次進入 VD 進行 20 min 的二次真空脫氣冶煉,壓力依然保持在 63 Pa 以下,結束后進行測溫、定氧、定氫、成分調整和氬氣流量的調節,軟吹時間應控制在 15~30 min。具體見表 2。

取樣方案及試樣分析方法如下。
1)全生產過程氧含量取樣方案:分別在 EBT 出鋼后、LF 脫硫結束后、LF 換渣前、第 2 次 LF 精煉結束、第 2 次 VD 破空、VD 后軟吹結束后和鑄錠取樣。將試樣進行線切割加工成 Φ3~4 mm 的試棒,再利用 LECO 氧氮氫儀對試樣的氧含量進行分析。
2)10 t 鋼錠開坯成 400mm×400mm 的方坯,經兩次墩粗+兩次拔長鍛造工藝,將鋼錠鍛造成 400 mm×400 mm 的方坯。試樣的取樣方式如圖 5 所示。根據 ASTM E2283-08(2019)標準,選取 6 塊試樣,并使用砂紙打磨并拋光試樣表面,確保表面光滑。然后,使用全自動夾雜物掃描儀 Aspex 對每個試樣進行 3 次檢測。每次檢測的面積必須大于 150 mm²,并檢測夾雜物尺寸大于 10 μm。最后,共需要對 24個面進行檢測,打磨的厚度須大于 0.3 mm。
3)利用 XRF 對精煉爐渣中的礦相組成進行分析。
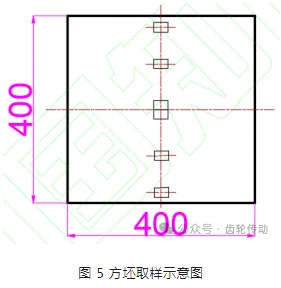
優化效果
1. 氧含量對比
圖 6 為不同工序位置的氧含量,提高入爐廢鋼碳含量配比后,EBT 出鋼的氧質量分數從 530×10-6 降至 290×10-6 。LF 精煉渣白化后,總氧質量分數降至 10×10-6 ,并在 LF 出站時降至 8×10-6 。盡管 VD 處理后 T.O 質量分數有所上升,但軟吹后降到 5×10-6 ,表明優化后的工藝在夾雜物吸附效果上更優。換渣改變了爐渣成分,增強了鋼渣吸附鋁鈣復合夾雜物的能力,并通過機械攪拌作用提升鋼渣與夾雜物的反應動力學條件,使得優化后工藝在 VD 破空后的氧含量控制上優于優化前。
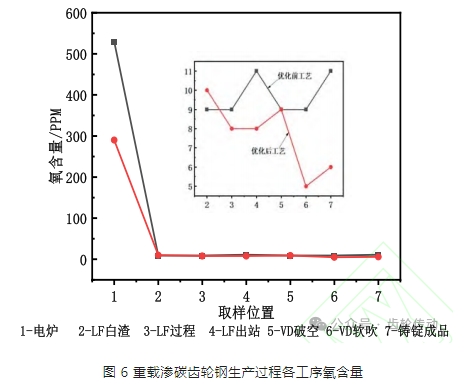
2. 夾雜物成分對比
對工藝優化后鍛件中夾雜物的類型進行分析,發現夾雜物的類型與優化前有所不同,如圖 7 所示。工藝優化后主要以鎂鋁復合型夾雜物為主,而優化前主要以鋁鈣復合型夾雜物為主。鎂鋁尖晶石的產生與頂渣中 MgO 含量增大有關,可能冶煉時間、高 Al 含量導致鋼包的內襯被侵蝕,生成厚度不均的鎂鋁尖晶石層,并逐漸脫落進入鋼液中,導致 MgO·Al2O3尖晶石的大量生成。
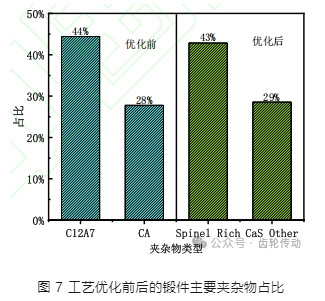
工藝優化前后鍛件夾雜物的成分見圖 8,從圖 8 可知,優化后工藝夾雜物尺寸大于 10μm 以上夾雜物的數量遠遠小于優化前,而且夾雜物中的 Ca 含量較優化前更低。優化工藝中,夾雜物中 Ca 含量的降低可歸因于爐渣中鈣活性的減少,這導致鋼液中鈣含量的下降,從而減弱了鈣置換鋁氧化物夾雜物的能力,使得復合型夾雜物中的鈣含量減少。此外,由于鋁鈣復合型夾雜物缺乏尖角,當其包裹在氣泡內部時,不易刺破氣泡,因此更易于通過脫氣過程被去除。相反,鎂鋁尖晶石夾雜物由于其尖角結構,容易刺破氣泡,在鋼液運動過程中難以被有效去除。
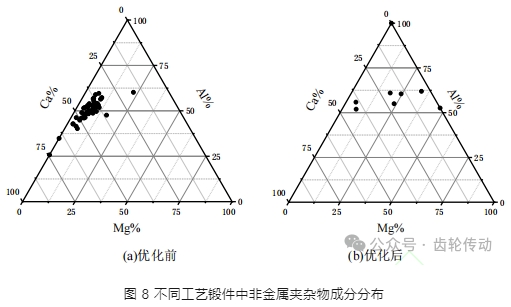
3. 爐渣成分分析
根據表 2 的 LF 爐渣成分檢測結果發現,優化后鋼包精煉爐爐渣中的 CaO 質量分數在 49%~56%,平均為 52.99%,達到設計要求。同時工藝優化后 MgO 含量高于優化前。當液態渣相溫度在 1500~1700℃ 時,液態渣相中飽和 MgO 的溶解度在 4.0%~7.7%,總體趨勢是溫度越高,渣中 MgO 的溶解度越高。一旦鋼液溫度低于1650℃,鋼渣中的MgO含量超過檢測上述范圍,將導致鋼渣中MgO處于飽和狀態。當鋼渣處于飽和狀態時,其中的氧化鎂會分解并進入鋼液中,與鋼中的氧化鋁結合形成尖晶石類夾雜物。這進一步證實了優化后工藝中大型夾雜物的主要為鎂鋁尖晶石夾雜物原因。通過相似相容原理,頂渣中的氧化鋁含量越高,爐渣的熔點越低,越有利于鋁鈣型復合夾雜物的去除。
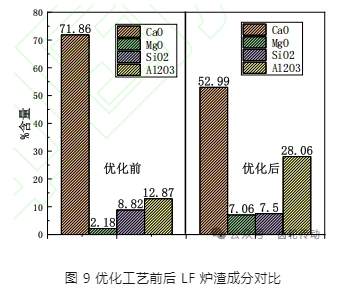
4. 鍛件最大夾雜物對比
當鋼中氧達到一定含量后,工藝優化前金相法采用標準 GB/T10561—2023 的 A、B、C、D、DS 分類標準對純凈鋼的評判已經受到一定限制,現在普遍采用標準 GB/T40281—2021 標準通過小試樣尺寸預判大體積鋼中的最大夾雜物尺寸。一般其分布滿足 Gumbel 的分布函數。

式中:x 為檢測平面最大夾雜物尺寸;λ為位置函數;δ為標準差。
利用等效代換將式(6)帶入到式(5)中,函數轉化為式(7)和式(8),可見最大夾雜物與 y 之間存在線性關系。但須指出 λ、δ、y 都是未知數,而 λ、δ 是隨著試樣數量及檢測面的數量的變化而變化。
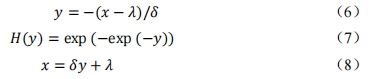
式(7)中 H(y)是一個連續的函數,利用樣本方差和位置函數代表連續函數的方差和位置函數,為了避免與 H(y)混淆,因此將樣本的函數用 F(y)表示,將公式寫成式(9)的形式,其中 Rel.Var(reduced variate)為約減變量。

式中:N=24;i 為最大夾雜由小到大的排列的順序號(1~N),因此整個方程變成求解 λ、δ 未知數的方程。GB/T40281—2021 標準提了 3 種求解方法,分別為截距法、矩陣法和最小二乘法,其中截距法最為簡單實用。
利用截距法對兩種不同工藝的鍛件中最大夾雜物檢測尺寸進行預測,結果見圖 10。從圖 10 可知,優化后工藝掃描得到鍛件的非金屬夾雜物尺寸全部小于 40μm,而優化前全部大于 40μm。優化后工藝預測可能出現單點最大夾雜物的尺寸為 51.2μm,而優化前為 137.5μm。可見優化后工藝通過換渣操作大幅度提升爐渣對夾雜物的吸附能力,對非金屬夾雜物評估值的降低幫助很大,優化后工藝對夾雜物的控制效果遠遠優于優化前。
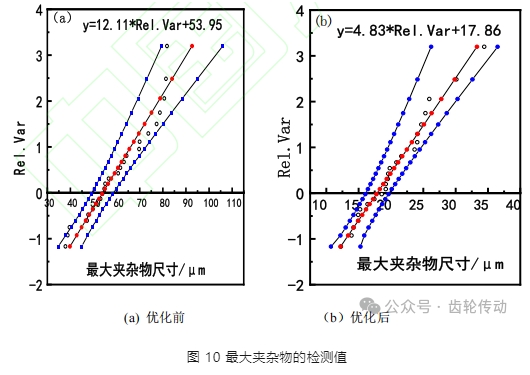
4、結論
1)通過對現場試驗的數據分析發現,重載滲碳齒輪鋼電爐出鋼氧含量與出鋼碳含量存在一定的關系,隨著出鋼碳含量增加,氧含量呈現下降的趨勢,但下降的速率隨著碳含量增加逐漸降低,因此出鋼的碳質量分數控制在 0.065%~0.120%,鋼中氧含量最合理。
2)利用掃描電鏡對不同工藝生產重載滲碳齒輪鋼中夾雜物進行掃描分析,結果發現優化工藝后的鍛件中夾雜物數量及主要類型有所不同,主要以鎂鋁尖晶石為主,而優化前生產工藝的夾雜物類型主要以鋁鈣復合型夾雜物為主。
3)利用截距法對兩種不同工藝的鍛件中最大夾雜物檢測尺寸進行預測,優化工藝的最大夾雜物尺寸預測值為 51.2μm,而原工藝的最大夾雜物預測值為 137.5μm,優化工藝可以有效降低鋼中的最大夾雜物尺寸的檢測值。
4)通過對電弧爐出鋼過程控制參數的優化,LF 和 VD 爐精煉過程的改進以及模鑄過程氬氣保護效果的提升,使得工藝優化后重載滲碳齒輪鋼中的鍛件氧質量分數可達到 6×10-6 ,滿足鍛鋼件的技術協議 9×10-6 以下的要求。
參考文獻略.