作為機械零件中的基礎件,齒輪承擔著傳遞運動和動力的關鍵任務。傳統齒輪主要采用合金鋼滲碳強化等處理方法來獲得高耐磨表面硬化層和強韌化綜合性能,滲碳熱處理工藝的水準直接決定了齒輪的力學和服役性能。在齒輪制造過程中,齒面精度要求也越來越高,然而滲碳淬火過程中產生組織應力和熱應力會導致齒輪變形,降低齒輪精度。為了保證齒輪的高精度成形,必須在滲碳淬火后對齒面進行磨削處理,以提高齒輪尺寸精度和表面質量。
齒面磨削加工中,60%~95%的磨削熱量會直接傳到齒面,超過臨界值的熱量可將齒面溫度瞬時升至奧氏體溫度并造成奧氏體轉變,在磨削液的淬火作用下出現齒面熱損傷。在齒輪滲碳淬火等熱處理工序后進行齒面磨削時,如存在原材料缺陷、組織中有粗大網狀或大塊狀碳化物、殘余奧氏體含量高、畸變較大等問題,磨削熱損傷加之不合理的磨削砂輪種類、砂輪硬度及粒度、進給量、沖程速度、冷卻條件等因素的共同作用下,都會加大齒面開裂風險。
20CrMnTi 是一種制備大齒輪的常用滲碳合金鋼,具有淬透性較高、低溫沖擊韌性好、抗疲勞性能優異的特點。滲碳過程使零件的表面形成高碳濃度層,可獲得高硬度和高耐磨性,而心部碳含量較低,韌性較好。零件滲碳回火后再進行淬火和低溫回火,以進一步提高其強度和韌性。本文針對 20CrMnTi 鋼大齒輪加工過程出現的齒面異常開裂問題,從滲碳熱處理工藝分析、理化檢驗和磨削加工角度探討了齒面開裂的原因,為優質 20CrMnTi 鋼大齒輪的生產加工提供科學依據。
1、20CrMnTi 鋼大齒輪齒面開裂情況
大齒輪(直齒外齒輪)模數 m=16 mm。該齒輪的主要工藝流程:鍛造→熱(正火)→車→熱(正火)→車→鉆→鏜→滾(滾齒)→熱處理→車(切碳)→熱(淬火)→車→磨齒→探傷→插齒→鉗→入庫。齒輪鋼 20CrMnTi 的主要熱處理工藝如圖 1 所示。
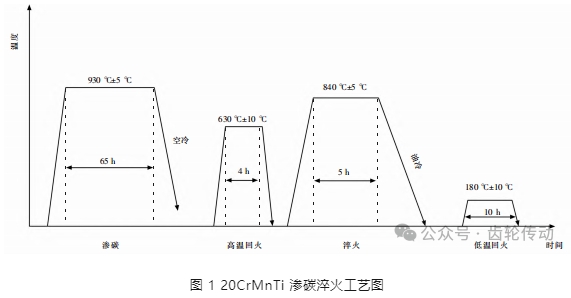
大齒輪出現裂紋的齒面宏觀形貌如圖 2 所示,出現裂紋的部位在圖 2(a)箭頭所示的區域。切開發現裂紋存在齒輪表面,類似剝落,通過外力分開后斷口見圖 2(b),裂紋沿距齒面 1~1.3 mm 下進行擴展,擴展面與滲層平行。齒面裂紋均位于節圓下方,由縱向裂紋與橫向裂紋交織構成,呈半網格形。裂紋擴展方向與齒輪的軸向方向基本一致,即與齒輪的磨削方向基本一致,且第 12 齒靠近齒根位置均存在沿磨削方向垂直的規律性裂紋。
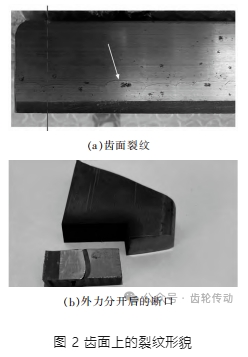
2、檢驗結果與分析
(1)化學成分與非金屬夾雜物檢驗
對大齒輪材料進行化學成分檢驗,其化學成分如表 1 所示。由表 1 可知,大齒輪材料各元素成分與 20CrMnTi 成分標準吻合較好。

經非金屬夾雜物分析,發現該齒輪非金屬夾雜物 A 類為 0.5 級,B 和 C 類都為 0 級,D 和 DS 類都為 0.5 級,符合非金屬夾雜物要求。
(2)金相檢驗
將該齒輪垂直于開裂齒面切開,制取齒寬方向的金相試樣,裂紋齒面金相組織如圖 3 所示。
由圖 3(a)可看出,裂紋開口處向外呈錯開狀,接近尾部呈鋸齒狀,深度約為 1.5 mm。用 4%的硝酸酒精腐蝕后如圖 3(b)所示,裂紋中部表層有亮白色組織,深度約 135 μm,緊鄰亮白層組織的為深灰色組織,深度約 550 μm。其中,亮白色組織為淬火馬氏體,深灰色組織為回火組織。
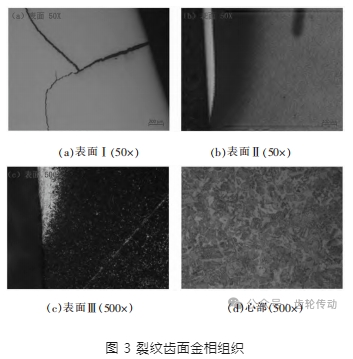
由圖 3(c)可看出,亮白色組織為淬火隱針馬氏體區,表面發生了磨削淬火燒傷,淬火層深度約為 150 μm。表面磨削時產生過多的磨削熱,使齒面溫度升到奧氏體轉變溫度 825 ℃以上,在切削液的冷卻作用下,使表面發生產生二次淬火馬氏體轉變,此時體積增大,組織應力增大,使表層出現拉應力,而次表層由于溫度在奧氏體轉變溫度之下,使低溫回火馬氏體轉變為中高溫馬氏體回火組織(回火索氏體、回火屈氏體),組織應力、熱應力和切削力作用疊加產生裂紋。如圖 3(d)所示心部組織為鐵素體和貝氏體。
(3)硬度檢驗
分別對裂紋齒面與無裂紋齒面的有效硬化層硬度梯度進行檢測,梯度曲線如圖 4 所示,齒輪表面硬度 58~62 HRC,從圖 3(b)可測出表層淬火區厚度為 135 μm,硬度約 855 HV(相當于 65.7 HRC),由梯度可看出硬度是高-低-高的順序,可判斷表層產生了 淬火燒傷,緊接著產生了回火燒傷。大齒輪有效硬化層深度技術要求為 2.5~2.9 mm,滾齒時預留磨齒余量為 0.4~0.45 mm,經檢測,無裂紋齒面的有效硬化層深度為 2.75~2.8 mm,這表明了滲碳淬火工藝合格。
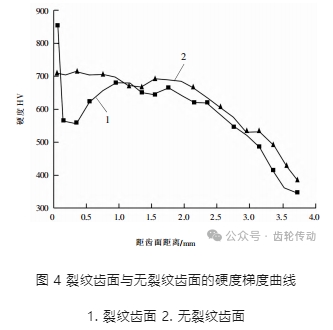
(4)裂紋形貌
對剝離的裂紋碎片進行掃描電鏡形貌分析,裂紋處的掃描電子形貌如圖 5 所示。觀察結果顯示裂紋普遍呈現出典型的沿晶開裂特征,明顯表現出晶間脆性的特征。通過將表面與內部的斷口掃描電鏡照片對比發現,表面晶間斷裂遠遠多于內部,且有少量解理裂紋。
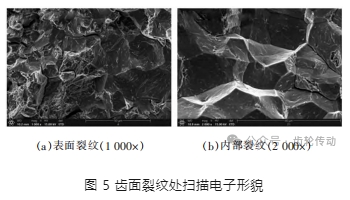
由圖 5 可以看出,裂紋是在距齒輪表面 1~1.4 mm 處產生,同時在齒輪表面發現有沿磨削方向垂直的規律性裂紋,而這些特征通常是磨削裂紋的特征。裂紋是在磨削過程中產生,在磨削后發展,并且磨削留下的殘余應力對裂紋的擴展起到促進作用。
3、結語
對工藝過程進行復盤,20CrMnTi 大齒輪化學成分和非金屬夾雜物級別符合要求。有效硬化層金相組織符合要求,說明熱處理工藝沒有問題。在檢查磨齒參數時,發現滲碳淬火齒輪的齒面磨削參數不合理(尤其是在粗磨階段,砂輪進給量設置過大),導致在齒表面形成二次淬火亮白層,這種亮白層組織硬度高達 65 HRC,呈拉應力狀態;同時,次表層的磨削回火層硬度會顯著降低,大約下降 12 HRC。從硬度梯度分布來看,呈現出高-低-高的典型磨削淬火燒傷特征。
建議磨齒時應降低進給量,選擇合理的磨齒參數,在磨齒后進行探傷。經調整磨削參數后,后續加工的大齒輪經探傷后未出現齒面裂紋。
參考文獻略.