端面齒輪作為新能源汽車上的核心傳動零件, 在變速器、差速器和傳動軸等裝置中承擔著調(diào)整發(fā)動機輸出軸轉(zhuǎn)速、調(diào)節(jié)不同輪胎間的速度差異以及實現(xiàn)高效轉(zhuǎn)動傳遞的作用。端面齒輪的主要受載區(qū)域位于齒輪端面, 與其他類型的齒輪相比, 具有結(jié)構(gòu)簡單、傳動效率高以及適用于高速高負載等優(yōu)點。隨著新能源汽車轉(zhuǎn)速的大幅提升, 普通模鍛和數(shù)控加工技術(shù)因變形不充分和切斷了材料流線, 削弱了齒強度, 影響其服役性能。端面精壓是成形高性能端面齒輪的有效方法, 相比于傳統(tǒng)閉式模鍛, 雖然可以借助材料分流顯著降低成形力, 但冷溫成形時易導(dǎo)致模具磨損嚴重, 降低模具使用壽命, 因此需要借助有限元模擬技術(shù)對成形過程中的載荷、應(yīng)力和應(yīng)變等進行分析, 優(yōu)化端面精壓的工藝方案和工藝參數(shù)。
符云龍等利用 Deform-3D 軟件對直齒面齒輪的熱滾軋過程進行數(shù)值模擬, 分析了輪齒的成形過程, 以突耳為指標, 考慮溫度、轉(zhuǎn)速、進給量以及滾軋輪倒角等因素, 利用正交試驗得出了最合理的工藝參數(shù)組合。張繼方等借助 DEFORM 軟件和 Archard 模型對齒輪閉式溫鍛成形過程進行模擬分析, 預(yù)測了凹模磨損最嚴重區(qū)域, 并利用響應(yīng)曲面法建立了齒輪溫鍛凹模磨損量編碼因子方程, 得到了對應(yīng)的最優(yōu)參數(shù)組合。VARELA S 等通過旋轉(zhuǎn)鍛造和傳統(tǒng)工藝相結(jié)合的混合鍛造方法制造凈成形齒輪, 實現(xiàn)了局部增量變形, 與傳統(tǒng)機械加工相比, 該方法可以節(jié)約 15% 的原材料, 并且所需設(shè)備的負荷不到傳統(tǒng)鍛造工藝所需的 50%。分析發(fā)現(xiàn), 成形工藝參數(shù)對成形質(zhì)量、模具壽命和設(shè)備噸位等影響顯著, 響應(yīng)面法不僅可以分析多參數(shù)協(xié)同作用下的成形規(guī)律, 還能得到不同參數(shù)的影響顯著順序, 對于齒輪成形的多目標優(yōu)化具有一定的指導(dǎo)意義。
本文采用 DEFORM-3D 有限元分析軟件模擬端面齒輪的端面精壓成形過程, 選取摩擦因數(shù)、成形速度和坯料溫度作為優(yōu)化參數(shù), 以最大成形載荷及變形均勻系數(shù)作為優(yōu)化目標, 分析了各參數(shù)對載荷和變形均勻系數(shù)的影響規(guī)律, 結(jié)合響應(yīng)面理論, 獲得了合理的工藝參數(shù)組合, 能夠為高性能端面齒輪的端面精壓成形和產(chǎn)業(yè)化制造提供一定的理論價值和技術(shù)支持。
1、建模及仿真
工藝方案設(shè)計
圖 1 為新能源汽車中某型號端面齒輪坯料與零件三維圖, 材料為 GCr15 軸承鋼, 具有高硬度、高耐磨和高疲勞強度等特點。此端面齒輪屬于空心類環(huán)形零件, 坯料內(nèi)外圈半徑分別為 43 和 49 mm, 高度為 11. 5 ~ 13. 5 mm; 端面上有 16 個齒形, 齒頂高 H = 8. 75 mm, 齒根高 h = 6. 65 mm, 齒形高度差為 2. 1 mm。
采用傳統(tǒng)閉式模鍛工藝雖然可以精確成形齒形, 但模具型腔易應(yīng)力集中開裂且下料精度要求高。基于金屬流動控制原理, 采用端面精壓工藝方案, 不但可以有效降低成形載荷、改善模具受力狀況, 而且可以保證齒形成形精度, 成形后僅齒輪內(nèi)圈需通過機加工切除多余部分。
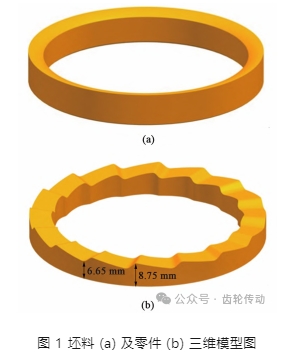
有限元建模及響應(yīng)面試驗設(shè)計
采用 NX12. 0 有限元軟件建立坯料與上下模的三維模型, 以 . stl 格式導(dǎo)入 DEFORM-3D 軟件前處理中。圖 2 為端面齒輪精鍛成形的有限元模型, 在材料庫中選擇 AISI-52100 材料, 由于齒形為主要成形區(qū)域, 因此將坯料上半部分網(wǎng)格局部細化, 網(wǎng)格數(shù) 15×104 個; 凸凹模材料為 H13 模具鋼, 設(shè)置為剛體, 劃分 5×104 個網(wǎng)格。
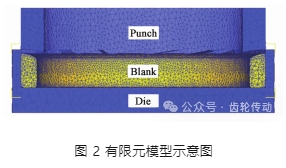
采用 Design Expert 軟件中的 Box-Behnken Design (BBD) 方法進行響應(yīng)面試驗方案設(shè)計, 并結(jié)合實際鍛造情況, 選取摩擦因數(shù) A、成形速度 B 和坯料溫度 C 作為優(yōu)化變量, 以最大成形載荷 F 和變形均勻系數(shù) α 作為響應(yīng)目標, 各變量的因素水平在模擬參數(shù)中的設(shè)置如表 1 所示, 坯料與空氣和模具之間的熱交換系數(shù)分別為 0. 02 和 11 N·(s·mm·℃ ) -1 。
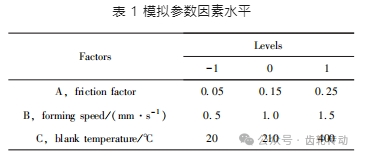
其中, 變形均勻系數(shù) α 為齒形變形的均勻程度, 其計算公式如式 (1) 所示。

式中: εmax、εmin 和εave 分別為單個齒截面 20 個節(jié)點 (圖 3) 的最大、最小和平均等效應(yīng)變。α 越小, 表明變形越均勻。
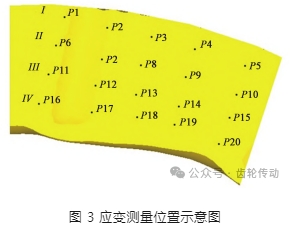
2、基于響應(yīng)面法的參數(shù)優(yōu)化
響應(yīng)面試驗結(jié)果
使用 Design Expert 軟件中的 BBD 方法進行試驗方案設(shè)計, 通過 DEFORM-3D 模擬并進行數(shù)據(jù)處理后獲得到各組參數(shù)試驗方案的最大成形載荷與變形均勻系數(shù), 最終試驗方案及模擬結(jié)果如表 2 所示。
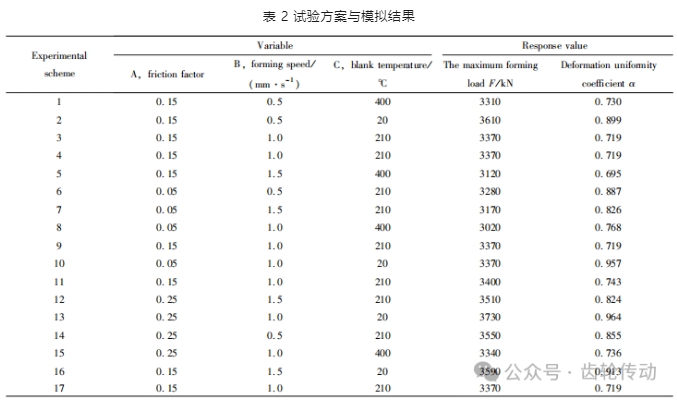
通過方差分析 (Analysis of Variance, ANOVA) 來判斷模型的顯著性和有效行, 方差分析結(jié)果及擬合參數(shù)信息分別如表 3 和表 4 所示。
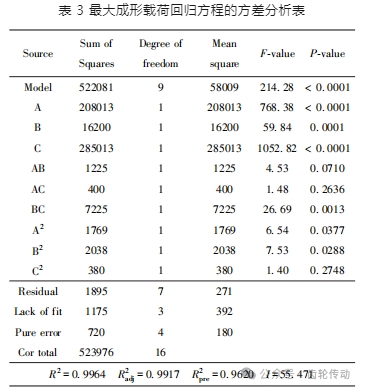
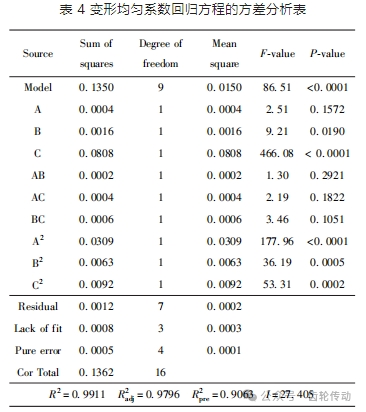
運用最小二乘法對各方案的最大成形載荷和變形均勻系數(shù)結(jié)果進行擬合分析, 獲得的關(guān)于最大成形載荷、變形均勻系數(shù)分別與摩擦因數(shù)、成形速度、坯料溫度的二階響應(yīng)面模型分別為:
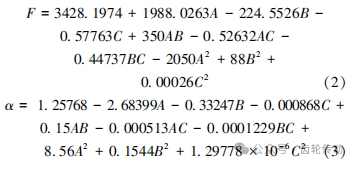
通過 F 檢驗可知: 二者 P 值均小于 0. 0001 (P< 0. 05 為模型顯著), 說明兩種響應(yīng)面模型均具有顯著性; 由 F 值可判斷出各因素對最大成形載荷的影響大小依次為: 坯料溫度>摩擦因數(shù)>成形速度, 對變形均勻系數(shù)的影響大小依次為: 坯料溫度>成形速度>摩擦因數(shù) (F 值越大, 則該因素更顯著); 最大成形載荷和變形均勻系數(shù)的復(fù)相關(guān)系數(shù) R2 分別為 0. 9964 和 0. 9911, 修正的復(fù)相關(guān)系數(shù) R2adj 分別為 0. 9917 和 0. 9796, 說明各模型的 R2 與 R2adj 吻合較好, 模型的相關(guān)性較好, 因此表明響應(yīng)面模型是有效的; 最大成形載荷和變形均勻系數(shù)的響應(yīng)模型的信噪比 I 分別為 55. 471 和 27. 405 (通常 I>4, 則判斷該模型具有良好的分辨能力), 表明模型具有足夠的分辨能力。
擬合結(jié)果分析
圖 4 所示為最大成形載荷關(guān)于不同設(shè)計變量的響應(yīng)面圖。從圖中可以看出, 成形載荷受坯料溫度和摩擦因數(shù)的影響較大, 受成形速度的影響很小, 當成形速度保持在中心水平時, 最大成形載荷隨著坯料溫度的升高而顯著降低, 降幅約為 10. 6%, 隨著摩擦因數(shù)的減小明顯降低, 但降幅略低, 約為 9. 7%。當摩擦因數(shù)為 0. 05、坯料溫度為 400 ℃ 時, 最大成形載荷達到極小值, 此時成形力和模具磨損最小。
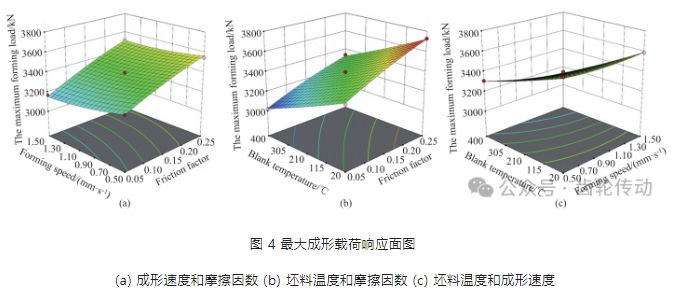
圖 5 所示為變形均勻系數(shù)關(guān)于不同設(shè)計變量的響應(yīng)面圖。由圖可知, 坯料溫度對變形均勻性的影響顯著大于成形速度和摩擦因數(shù), 坯料溫度越高, 變形均勻系數(shù)越小, 即齒輪在成形時變形越均勻; 當坯料溫度保持在中心水平時, 變形均勻系數(shù)受到摩擦因數(shù)和成形速度的影響趨勢一致, 都隨著變量的增加呈現(xiàn)出先減小后增大的趨勢。當摩擦因數(shù)保持在中心水平, 成形速度為 1. 5 mm·s-1 、坯料溫度為 400 ℃時, 變形均勻系數(shù)達到極小值, 此時齒形變形最均勻。
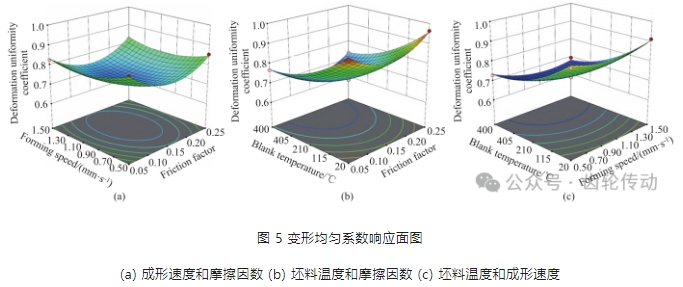
多目標優(yōu)化
以上驗證了最大成形載荷和變形均勻系數(shù)的響應(yīng)面擬合模型。在端面齒輪成形過程中, 最大成形載荷越小, 在實際生產(chǎn)中所需要的設(shè)備噸位越小, 對模具的磨損等損傷也越小; 另一方面, 變形均勻系數(shù)越小, 表明齒形在成形時應(yīng)變分布越均勻, 成形質(zhì)量越好。因此, 綜合考慮各參數(shù)之間的交互影響, 使用響應(yīng)面模型進行優(yōu)化, 以找到使目標函數(shù)最優(yōu)化的輸入變量組合。該優(yōu)化問題可描述為如式 (4) 所示的數(shù)學問題。
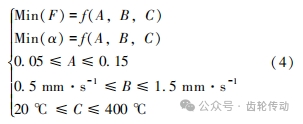
通過 Design Expert 對其進行求解, 獲得的最優(yōu)化參數(shù)組合為: 摩擦因數(shù) 0. 11、成形速度 1. 38 mm·s -1 、坯料溫度 400 ℃ 。按最優(yōu)參數(shù)組合進行仿真, 得到了最大成形載荷和變形均勻系數(shù)的數(shù)值。在相同優(yōu)化條件下, 理論優(yōu)化和數(shù)值模擬的最大成形載荷分別為 3060 和 3100 kN, 變形均勻系數(shù)分別為 0. 695 和 0. 685。數(shù)值模擬與理論優(yōu)化之間的誤差分別為 1. 31%和 1. 44%, 表明數(shù)值模擬與理論優(yōu)化結(jié)果吻合較好。
3、成形過程多物理場分析
在傳統(tǒng)閉式模鍛成形過程中, 載荷前期變化平緩, 隨著下壓量的逐漸增大, 成形載荷由于縱向飛刺的形成急劇升高, 嚴重影響模具壽命。而本文采用端面精壓工藝, 在端面齒輪鍛壓成形過程中不同下壓量下的速度場矢量圖和成形載荷如圖 6 所示。
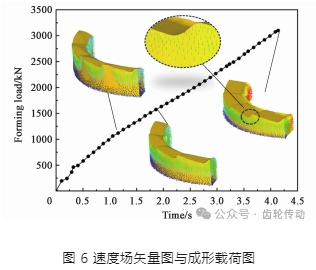
由圖可知, 凸模在接觸坯料后, 坯料主要沿軸向發(fā)生流動, 變形首先發(fā)生在齒形外圓的齒根部位; 隨著凸模下行, 齒形端面逐漸形成, 且由于坯料內(nèi)部無模具限制, 在齒形充填過程中,坯料沿徑向向內(nèi)部流動的趨勢明顯增加; 在成形后期, 齒形端面基本成形, 齒形高度逐步增加, 多余金屬徑向流動顯著。由于模具對坯料內(nèi)徑無約束, 成形載荷始終增長緩慢, 成形較為穩(wěn)定。
圖 7 為不同下壓量下鍛件的等效應(yīng)力分布情況。在成形初始階段, 齒根部位優(yōu)先發(fā)生屈服變形, 等效應(yīng)力由 770 MPa 沿軸向遞減至約 440 MPa; 隨著下壓量增大, 齒形端面的等效應(yīng)力分布逐漸趨于一致, 齒根處的等效應(yīng)力始終高于齒頂處, 成形結(jié)束時的等效應(yīng)力分別約為 976 和 870 MPa。
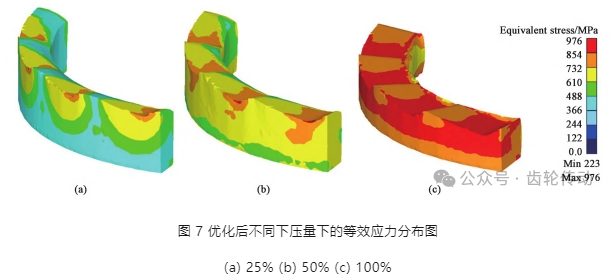
圖 8 為不同下壓量下鍛件的等效應(yīng)變分布情況。成形初期, 齒根處優(yōu)先發(fā)生塑性變形, 等效應(yīng)變約為 0. 55, 此時齒頂基本沒有變形; 隨著齒形端面不斷形成, 等效應(yīng)變自齒根到齒頂、自端面到底面均逐漸增大; 成形結(jié)束時, 齒形端面的等效應(yīng)變約為 0. 54~1. 15, 最大等效應(yīng)變集中在齒形嚙合處, 鍛件整體在成形過程中發(fā)生較為均勻的變形。
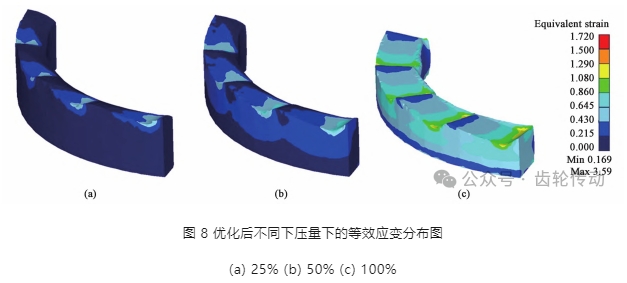
成形過程中, 坯料流動方向有序, 無折疊缺陷; 成形結(jié)束時, 齒形充填完整, 無明顯應(yīng)力集中, 無開裂傾向, 齒形端面應(yīng)變分布比較均勻, 如圖 7c 和 圖 8c 所示, 表明經(jīng)優(yōu)化后的工藝參數(shù)得到的鍛件成形質(zhì)量良好。
4、試驗驗證
采用上述優(yōu)化后的工藝參數(shù)進行試驗生產(chǎn), 獲得的鍛件如圖 9 所示, 可見鍛件成形效果良好, 齒形飽滿, 未發(fā)現(xiàn)明顯成形缺陷。表 6 為試驗鍛件和模擬鍛件 16 個齒形的尺寸平均值, 齒頂高和齒根高的尺寸誤差分別為 0. 69%和 0. 45%, 表明模擬結(jié)果具有可靠性。
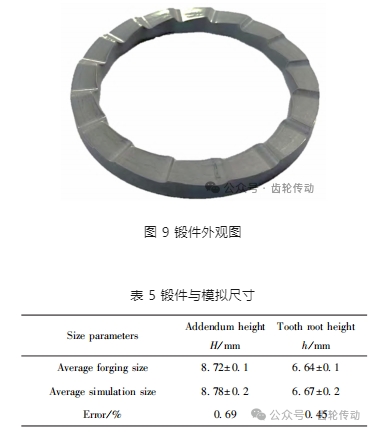
參照圖 3 應(yīng)變測量位置對鍛件齒形端面進行維氏顯微硬度測試, 測試載荷 500 g, 保壓時間 15 s, 結(jié)果如圖 10 所示。齒形外圓的平均顯微硬度約為 (168. 4±3. 9) HV, 明顯高于內(nèi)圓的顯微硬度, 且隨著距齒根距離的增加, 顯微硬度逐漸降低, 這與齒形端面等效應(yīng)變的分布規(guī)律一致。齒形端面的平均顯微硬度達到 (162. 1±8. 4) HV, 比初始坯料顯微硬度提升了 8. 1%, 表明采用端面精壓成形工藝可以有效提升端面齒輪的力學性能。
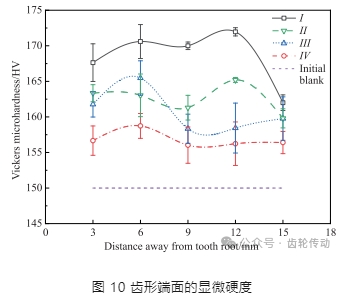
5、結(jié)論
(1) 基于 DEFORM-3D 數(shù)值模擬和響應(yīng)面法, 選取摩擦因數(shù)、成形速度和坯料溫度作為優(yōu)化參數(shù), 建立了最大成形載荷和變形均勻系數(shù)的響應(yīng)面模型,獲得了最佳參數(shù)組合方案: 摩擦因數(shù)為 0. 11, 成形速度為 1. 38 mm·s-1 , 坯料溫度為 400 ℃ 。
(2) 優(yōu)化后工藝參數(shù)的模擬結(jié)果表明, 坯料流動方向有序, 優(yōu)先在齒根部位發(fā)生塑性變形, 在成形過程中齒形端面的等效應(yīng)力和等效應(yīng)變分布均勻性不斷提高, 成形質(zhì)量良好。
(3) 根據(jù)最優(yōu)工藝參數(shù)試驗得到的鍛件成形效果良好, 未有明顯成形缺陷, 且與模擬結(jié)果基本一致, 與初始態(tài)相比, 此時的齒形端面顯微硬度提升了 8. 1%, 表明經(jīng)響應(yīng)面法獲得的最優(yōu)工藝參數(shù)能夠為端面齒輪的端面精壓成形和產(chǎn)業(yè)化制造提供一定的理論價值和技術(shù)支持。
參考文獻略.