隨著航空工業的快速發展,高強度鋼、超高強度鋼在航空制造業中得到廣泛應用,尤其是飛機的重要受力構件大多選用高強度鋼。而鋼的氫脆敏感性或氫致后斷裂敏感性隨其強度增大而升高,尤其抗拉強度大于 1000 MPa 的高強度鋼對氫脆問題更加敏感。
當金屬材料在加工制造過程以及使用環境中受到氫的侵入,氫會在材料中擴散并聚集,使材料的承載能力降低,塑性下降,在經過一段時間后,材料在低于屈服強度的拉應力作用下突然發生斷裂的現象稱為氫脆。氫脆是一種瞬間發生的脆性開裂,往往呈現出批次性特征,且以現有的手段難以檢測,因此這種斷裂的危害性極大,嚴重威脅著鋼制件的使用安全。
半個多世紀以來,國內外研究人員從機理、損傷表現、影響因素以及工程控制等方面對氫脆進行了大量研究,形成了氫壓、表面吸附、弱鍵、氫與位錯交互作用等理論。李星國對金屬的氫脆及其產生機制進行了研究,總結并提出了消除應力、表面噴丸等提高材料韌性的措施來減少氫脆現象。付雷分析了高強度鋼焊接后的充氫對其斷裂位置的影響,發現充氫的電流密度越大,拉伸條件下斷裂位置從母材區向焊接熱影響區轉移趨勢越明顯。目前,對氫脆的研究主要是如何避免工作過程中氫脆的發生,對于零件制造過程及加工方式引起的表面殘余應力狀態改變及其對氫脆的影響研究還較少開展。
18 件減速小錐齒輪在內徑鍍鉻位置經磨削工序后進行磁粉檢測時,發現其中 17 個零件在鍍鉻區與焊縫區域中間位置存在沿齒輪軸線方向分布的磁痕顯示。減速小錐齒輪組件由軸套和減速小錐齒輪慣性摩擦焊焊接而成,材料均為 18CrNi4A,其軸套內徑表面鍍鉻,鍍層厚 0.12~0.17 mm。
本研究通過宏微觀觀察、硬度測試、殘余應力測試、氫含量分析等手段,開展工藝試驗,分析鍍鉻工序對氫含量的影響,以及焊接區域加工方式對表面殘余應力狀態的影響,判斷減速小錐齒輪組件裂紋性質和原因,提出改進措施,以避免故障的再次發生。
1、試驗過程與結果
宏觀觀察
故障件宏觀形貌見圖 1。磁痕顯示位于故障件內孔槽鍍鉻過渡區與摩擦焊接區之間的基體表面(圖 1a 中虛線區域),沿軸向分布(圖 1b),未見其他異常損傷痕跡。
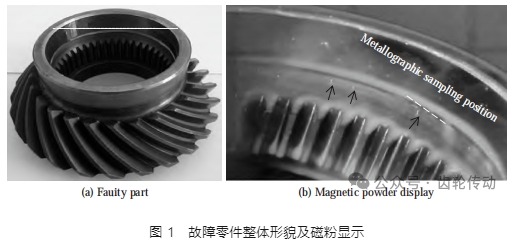
微觀觀察
沿裂紋處打開,在掃描電鏡下觀察斷面,形貌如圖 2 所示。由圖 2 可見,裂紋斷面與人工斷口界限明顯,形貌差異明顯,裂紋深約 0.52 mm。裂紋斷面大致與零件表面垂直,斷口整體干凈,呈沿晶形貌,未見變色、腐蝕等跡象(圖 2a);人工斷口呈明顯的韌窩特征(圖 2b),兩部分斷口。
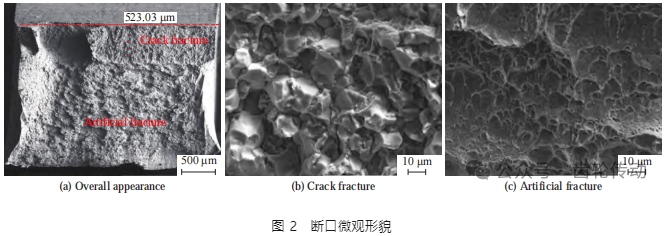
金相組織分析
垂直于裂紋制取橫向金相試樣(切取圖 1b 中虛線標識截面),可觀察到 2 條裂紋,其延伸方向均大致與試樣表面垂直。兩裂紋均呈沿晶擴展特征,兩側未見氧化、脫碳及腐蝕現象。其中一條裂紋由試樣表面向內部延伸,長度為 0.36 mm(圖 3a);另一條則位于試樣內部,未在表面開口,長度為 0.33 mm(圖 3b)。
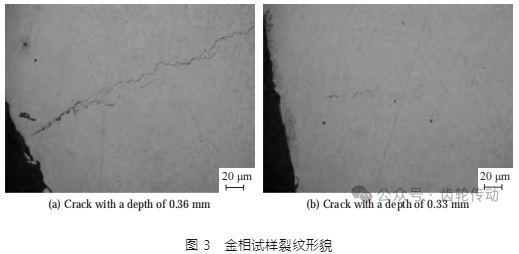
裂紋附近金相組織為低碳馬氏體+少量鐵素體,未見異常(圖 4a)。沿零件軸向切取金相試樣,故障件裂紋區與鍍鉻區基體以及花鍵區心部組織均為回火馬氏體+鐵素體,組織未見異常(圖 4b)。
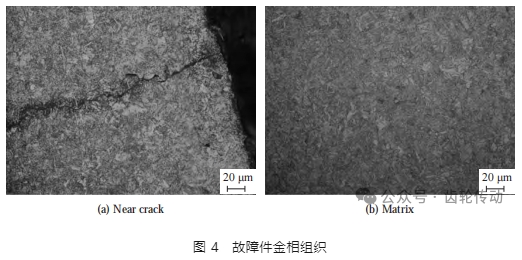
縱向切取故障件內孔槽位置制取金相試樣,腐蝕后觀察可見,裂紋位置距焊接熱影響區約 2.30 mm,距離鍍鉻區約 0.35 mm(圖 5)。焊接熔合區及熱影響區未見明顯冶金缺陷。
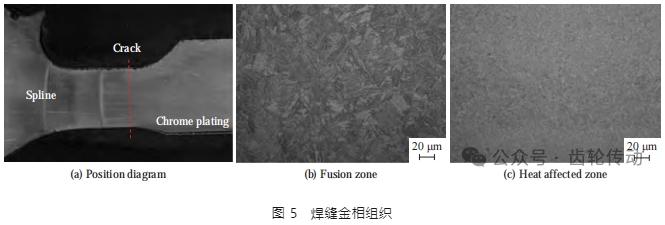
能譜分析
對裂紋斷面和人工斷口表面進行能譜測試,結果見表 1。材料成分符合 18CrNi4A 的技術要求,斷口表面除基體元素外,未見其他異常元素。

顯微硬度測試
在金相試樣上對鍍鉻區心部、裂紋區域、花鍵區域分別進行顯微硬度測試,按 GB/T 1172— 1999 將維氏硬度轉換成洛氏硬度,結果見表 2。可見各區域硬度差別不大,符合技術要求。
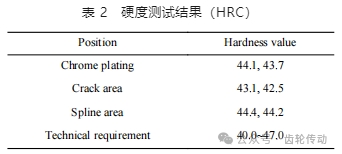
氫含量分析
對零件鍍鉻區、鍍鉻過渡區、裂紋區、焊接區和花鍵區分別取直徑為 1 的試樣,使用氫分析儀測試氫含量,結果見表 3。
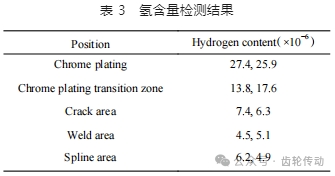
殘余應力測試
分別對故障件內孔槽裂紋區、焊接區以及花鍵區進行殘余應力測試,結果見表 4。可見零件該區域均為殘余拉應力。
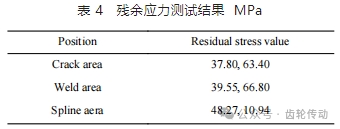
2、分析與討論
故障件金相組織未見異常,心部硬度符合技術要求,主要合金元素含量基本符合 18CrNi4A 技術要求。焊接熔核區及熱影響區未見裂紋、氣孔、未焊合等冶金缺陷。
故障件裂紋位于內孔槽鍍鉻過渡區與焊接區之間的基體表面,均沿軸向大致平行分布;裂紋金相及斷口均呈沿晶特征,兩側未見氧化、脫碳、腐蝕等現象,并存在萌生于亞表面的裂紋;斷口表面干凈,能譜分析也未見異常元素。以上結果顯示,該裂紋特征與氫致裂紋特征相符。
故障件各部位的氫含量測試結果顯示,鍍鉻區、鍍鉻過渡區以及裂紋區域的氫含量均超過 6×10−6。對于一般鋼來說,氫含量達到 5×10−6 以上就可能會引起氫致裂紋的產生。因此,對于故障件裂紋部位來說,過高的氫含量為裂紋在該部位萌生提供了內部條件。從應力測試結果來看,零件裂紋區域、焊接區域表面均為拉應力,該位置的表面應力狀態為裂紋萌生提供了外部條件。
故障件材料為 18CrNi4A,抗拉強度超過 1300 MPa,屬于對氫脆敏感性高的高強鋼;故障件的軸套內徑鍍鉻,鍍鉻工藝本身屬于析氫量較高、氫脆傾向大的工藝;該組件為焊接組合件,經過多道的車削、磨削、拋光、酸洗等工序,零件本身承受的殘余應力和內部應力相對較大。由此來看,故障件本身的結構和加工工藝特點決定其具有產生氫脆的 3 方面要素,如果過程控制不當,就易引發氫脆。
綜上所述,故障件裂紋性質為氫致裂紋,裂紋部位附近過高的氫含量和表面殘余拉應力狀態的共同作用導致裂紋在該部位萌生。
3、工藝排查及試驗
工藝排查
從引入氫元素和表面拉應力狀態兩方面排查整個加工過程。主要有以下工序:
1)零件內徑經鍍鉻和酸洗。該工序中都是充氫過程,如果工藝控制不當,就會產生氫致裂紋和氫壓裂紋。
2)焊接。焊接工藝不合適,引入過量的 H,冷卻至室溫后會出現焊接冷裂紋,其本質也是氫壓裂紋。從檢查結果來看,裂紋未發生在焊接區,可排除焊接因素。
3)零件加工。裂紋所在零件區域經焊接并拋光后的粗糙度要求為 0.8,經復測該位置的粗糙度符合要求。但觀察零件實物,該區域存在明顯的圓周方向的加工刀痕,無拋光痕跡,判斷該區域未進行拋光工序。經復查原技術要求,拋光工序為關鍵過程,要求仔細進行拋光,但拋光工序的作用不明確。
復查工藝要求,零件內軸徑焊縫區域共經歷 3 道磨削工序,每次磨削后均要進行消除應力處理。核對該零件加工過程,實際采用以車代磨的連續加工工序,合并單道車削工序后進行消除應力。
綜合以上分析,通過開展工藝試驗確定鍍鉻時間及鍍鉻工藝本身對零件不同位置氫含量的影響,確定加工過程中不同工序對表面殘余應力狀態的影響,從而確定更加合理的工藝路線和工藝參數,避免氫脆現象的發生。
工藝試驗及結果
1)鍍鉻工藝、鍍鉻時間對氫含量的影響
在鍍鉻工序前后分別對零件不同區域的氫含量進行測試,結果見圖 6。
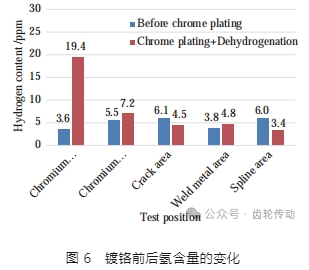
經不同鍍鉻時間后,鍍鉻區域的氫含量測試結果見圖 7。
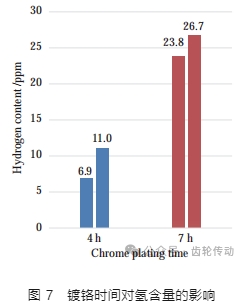
由圖 6 可知,在鍍鉻工序前,零件基體不同區域的氫含量差別不大且水平較低,最高僅為 6.1×10−6 ;經過鍍鉻工序后,鍍鉻區域的氫含量明顯升高,由 3.6×10−6 上升到 19.4×10−6 ,且遠高于非鍍鉻區。由圖 7 可知,隨著鍍鉻時間的延長,零件鍍鉻區域的氫含量也明顯升高。由此可知,鍍鉻工序會將 H 引入零件基體,故在滿足鍍層厚度要求的基礎上,應嚴格控制鍍鉻時間,以減少該工序過程中引入的 H。
2)焊接前后殘余應力影響試驗
慣性摩擦焊工序前后,分別對零件焊接區域及其附近進行表面殘余應力測試,結果見圖 8。由圖 8 可知,經焊接工序后,焊接區域及其附近表面應力狀態均由壓應力轉變為拉應力;而遠離焊接位置的區域表面殘余應力值與焊接前相當,未發生明顯變化。因此,焊接后若殘余拉應力消除不及時或不徹底,都會對零件后續應力狀態產生不利影響。
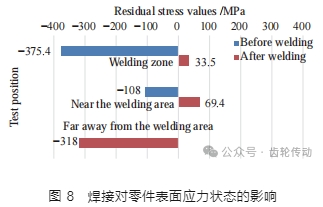
3)拋光、車削工藝對焊縫區域殘余應力影響對比試驗
對零件的焊接區域在經歷焊接、消除應力、車削加工以及拋光工序后,分別進行表面殘余應力測試,結果見圖 9。由圖 9 可知,焊接工序后的表面拉應力達到最大值 528.0 MPa;消除應力工序后,拉應力明顯降低至 258.0 MPa,說明消除應力工序可有效降低零件應力水平。每次車削工序后,零件表面應力狀態約為拉應力 150.0 MPa。零件僅在每次經歷拋光工序后,表面應力狀態由拉 應力轉變為壓應力,表明拋光工序可有效改變基體表面應力狀態,預防氫脆現象的發生。
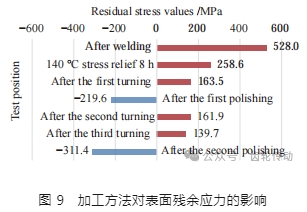
參考以上工藝試驗結果,為了避免零件氫脆現象的發生,采取如下措施:控制鍍鉻的時間;焊接后及時進行消除應力;嚴格按照工藝規程要求進行拋光工序。采用改進后的工藝進行了 2 批次共 40 件零件的生產,所有零件鍍鉻磨削后均未再出現磁痕顯示。
4、結論
1)減速小錐齒輪組件裂紋性質為氫致脆性裂紋。
2)裂紋部位附近過高的氫含量和表面殘余拉應力狀態的共同作用導致裂紋的萌生。
3)控制鍍鉻的時間,及時除氫和消除應力,控制焊接位置加工方式,可有效避免氫脆故障的發生。
參考文獻略.