隨著齒輪結(jié)構(gòu)的優(yōu)化改進(jìn),弧齒錐齒輪也被廣泛使用,因其具備高承載強(qiáng)度、穩(wěn)定動力傳輸、使用壽命長的優(yōu)勢,目前已在汽車機(jī)械動力系統(tǒng)等方面發(fā)揮了不可替代的作用。弧齒錐齒輪在使用階段最容易發(fā)生齒面磨損的現(xiàn)象,從而導(dǎo)致運(yùn)行故障。當(dāng)形成齒面磨損時(shí),將會造成齒輪系統(tǒng)出現(xiàn)明顯振動、噪聲和無法滿足齒輪系統(tǒng)間精確傳動的技術(shù)要求,最終增大了傳動的誤差。
目前已有較多研究人員開展了直齒圓柱齒輪齒面的磨損因素分析,并探討了動態(tài)傳動誤差的變化情況。高洪波等從動態(tài)嚙合剛度、摩擦、齒側(cè)間隙、偏心等層面進(jìn)行分析,為單級直齒圓柱齒輪傳動結(jié)構(gòu)建立了 6 自由度的耦合模型,分別研究了全齒發(fā)生均勻與偏心磨損時(shí)的特征。結(jié)果顯示,逐漸提高齒面的磨損程度后,形成了均值與波動性更大的動態(tài)傳動誤差。王彥剛等針對含齒面磨損故障建立了二級齒輪箱傳動誤差分析模型,經(jīng)測試表明,動態(tài)傳動誤差信號與傳統(tǒng)形式的齒輪箱振動響應(yīng)信號相比可以獲得更大信噪比,并且可以更好地適應(yīng)變速變載運(yùn)行工況,提升了整體穩(wěn)定性。此外,還可以根據(jù)動態(tài)傳動誤差準(zhǔn)確識別復(fù)雜結(jié)構(gòu)齒輪在初期階段發(fā)生齒面磨損情況。但是這些研究內(nèi)容都是針對直齒圓柱齒輪的,對于復(fù)雜齒形結(jié)構(gòu)的弧齒錐齒輪則沒有建立明確的傳動誤差分析方法,而且以上提出的齒輪動力學(xué)模型基本都是屬于集中參數(shù)模型,在實(shí)際建模階段無法完全確定齒輪系統(tǒng)參數(shù),對最終精度造成較大影響,并且實(shí)際計(jì)算過程也過于復(fù)雜。
根據(jù)以上分析,本文對服役期間的弧齒錐齒輪齒面磨損進(jìn)行了深入研究,針對各個(gè)載荷與磨損狀態(tài)下單齒和全齒磨損的齒輪構(gòu)建了傳動誤差曲線,由此判斷載荷與磨損程度引起的弧齒錐齒輪動態(tài)傳動誤差變化情況。
1、齒面磨損模型
將傳動誤差理解為齒輪副在嚙合線方向上產(chǎn)生的相對位移 δ,表達(dá)式如下:

式中:Rp與 Rg分別為主動輪與從動輪半徑;θp、θg 分別為主、從動輪沿軸心線發(fā)生扭轉(zhuǎn)的自由度。
本文針對剛性支撐條件的弧齒錐齒輪構(gòu)建了純扭振模型,以探討齒面磨損故障引起的齒輪系統(tǒng)傳動誤差變化情況。
弧齒錐齒輪扭轉(zhuǎn)振動模型
圖 1 給出了弧齒錐齒輪扭振模型。以 x 軸與 y 軸表示主動輪與從動輪的軸心線位置,原點(diǎn)位于兩軸的交點(diǎn)處,構(gòu)建得到 O-xyz 坐標(biāo)系。進(jìn)行仿真分析時(shí),假定 2 個(gè)齒輪都位于理論坐標(biāo)處,將齒輪軸視為一個(gè)沒有質(zhì)量的剛體,通過質(zhì)量與轉(zhuǎn)動慣量集中的形式實(shí)現(xiàn)對齒輪的模擬功能,由此獲得含有 2 個(gè)自由度的齒輪系統(tǒng)。根據(jù)齒輪系統(tǒng)的受力狀態(tài)建立以下弧齒錐齒輪副扭轉(zhuǎn)振動模型函數(shù):
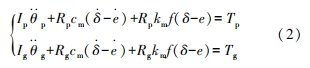
式中:Ip、Ig 分別表示主動輪與從動輪轉(zhuǎn)動慣量;Tp、Tg分別表示主動輪與從動輪驅(qū)動力矩與載荷產(chǎn)生的力矩;e 表示齒輪副靜態(tài)傳動誤差;cm表示齒輪副嚙合阻尼;km表示齒輪副時(shí)變嚙合剛度;f 是齒側(cè)間隙函數(shù)。
將兩弧齒錐齒輪嚙合點(diǎn)在振動與誤差作用下形成的嚙合點(diǎn)法線相對位移表示成以下形式:

上式合并后得到:

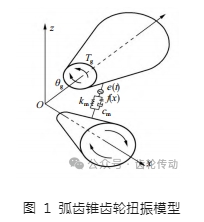
齒面磨損故障激勵機(jī)理
對式(3)進(jìn)行分析可以發(fā)現(xiàn),弧齒錐齒輪扭振微分計(jì)算方程跟常規(guī)動力學(xué)方程接近,可對 2 個(gè)式子進(jìn)行對比分析。以下為典型動力學(xué)方程:

式中:M 表示質(zhì)量矩陣;K 表示剛度矩陣;C 是阻尼矩陣;P 是載荷。
以上式建立的齒輪系統(tǒng)動力模型都涉及慣性力、彈簧力、阻尼力、載荷力的相互關(guān)系。但相對動力學(xué)基本方程存在明顯差異,齒輪在實(shí)際運(yùn)動階段受到靜態(tài)傳動誤差、時(shí)變嚙合剛度、齒側(cè)間隙各類非線性作用條件的綜合影響,這使得齒輪系統(tǒng)形成了明顯的傳動誤差。產(chǎn)生齒面磨損故障時(shí),將會引起齒輪系統(tǒng)的各項(xiàng)力學(xué)特性參數(shù)變化,在齒輪系統(tǒng)中形成了不同內(nèi)部激勵,從而在齒輪系統(tǒng)中形成不同的動態(tài)傳動誤差。
對弧齒錐齒輪進(jìn)行扭振模型計(jì)算過程較為復(fù)雜,需要耗費(fèi)大量時(shí)間解析,因此通常都是選擇數(shù)值的方式完成求解過程。為了進(jìn)化集中參數(shù)模型,優(yōu)化了齒輪的關(guān)鍵參數(shù),這對計(jì)算精度也造成一定的影響,只能利用非線性分析的方式研究齒輪的動力學(xué)特性。根據(jù)有限元實(shí)體模型進(jìn)行處理時(shí)只需設(shè)置合適的幾何精度與邊界參數(shù)便可以獲得精確結(jié)果。
2、弧齒錐齒輪建模
本文利用 Matlab 軟件完成齒面離散點(diǎn)的編程計(jì)算,再利用建模軟件對齒面實(shí)施擬合,由此構(gòu)建得到弧齒錐齒輪模型,各項(xiàng)參數(shù)如表 1 所示。
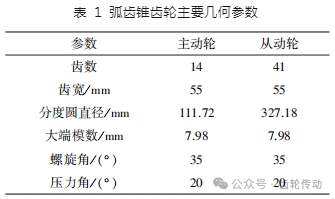
齒面發(fā)生磨損的一個(gè)重要形式是輪齒厚度減小,因此本研究利用控制齒厚參數(shù)的方式來表示齒面的磨損狀態(tài)。齒輪運(yùn)行期間,主動輪相對從動輪會發(fā)生更多的齒面接觸,在同樣的材料下,主動輪齒面會產(chǎn)生更大程度的磨損。因此本文以主動輪作為故障分析對象。通過調(diào)整輪齒齒厚參數(shù)模擬單齒、全齒發(fā)生齒面磨損情況,構(gòu)建了齒面發(fā)生不同磨損程度時(shí)的仿真模型。
對材質(zhì)為 45Cr 的弧齒錐齒輪開展動力學(xué)仿真測試,各參數(shù)如表 2 所示。
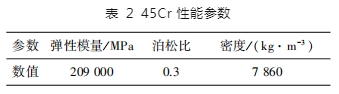
進(jìn)行模型計(jì)算時(shí)加入了阻尼因素的作用,設(shè)置 Ray 阻尼,質(zhì)量矩陣系數(shù)為 α = 0.03,剛度矩陣系數(shù)為 β = 3×10-6 ;齒輪副保持摩擦接觸狀態(tài),對應(yīng)的摩擦因數(shù)為 0.1;主動輪和從動輪都只沿軸心 線發(fā)生旋轉(zhuǎn),保持主動輪轉(zhuǎn)速為 210 r/ min,控制從動輪轉(zhuǎn)矩依次為 500 Nm、1 000 Nm、3 000 Nm,再對齒輪進(jìn)行傳動特性分析。
3、動態(tài)傳動誤差結(jié)果分析
通過仿真計(jì)算獲得主動輪和從動輪產(chǎn)生的轉(zhuǎn)動角大小,根據(jù)測試結(jié)果得到動態(tài)傳動誤差變化曲線。依次計(jì)算單齒與全齒磨損條件下形成的動態(tài)傳動誤差,最后對比了不同磨損程度下動態(tài)傳 遞誤差。
單齒磨損動態(tài)傳動誤差曲線
根據(jù)仿真得到的最初 0.13 s 的動態(tài)傳動誤差并繪制成相應(yīng)的曲線,圖 2 給出了在載荷為 500 Nm 條件下各單齒磨損量形成的傳動誤差。
由圖 2 可以發(fā)現(xiàn),在保持磨損量不變情況下,齒輪經(jīng)過一個(gè)很短時(shí)間的瞬態(tài)狀態(tài)后開始轉(zhuǎn)為穩(wěn)態(tài)階段。當(dāng)磨損輪齒發(fā)生嚙合時(shí),系統(tǒng)中產(chǎn)生了更明顯的激勵,從而形成了更高的動態(tài)傳動誤差 γ;時(shí)間增加至最值 Γ 時(shí),嚙合狀態(tài)逐漸消失,引起動態(tài)傳動誤差 γ 的持續(xù)降低。通過分析圖中各顏色標(biāo)注的曲線可以發(fā)現(xiàn),在初始階段齒面發(fā)生磨損時(shí),提高齒面磨損量 λ 時(shí),動態(tài)傳動誤差 γ 也發(fā)生了上升的趨勢,同時(shí)獲得了更大的 Γ;弧齒錐齒輪具備較大重合度,隨著齒面磨損量 λ 超過臨界值后,磨損輪齒的載荷作用消失,此時(shí)位于磨損輪齒邊緣區(qū)域的輪齒可以對故障齒起到載荷分擔(dān)的效果,動態(tài)傳動誤差 γ 已經(jīng)與此載荷臨界值 γ1一致。
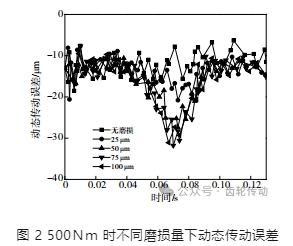
在持續(xù)提高載荷 P 的過程中,輪齒形成了更大程度的彈性形變,保持同樣的磨損量時(shí)形成了更大的動態(tài)傳動誤差 γ,此時(shí)產(chǎn)生了更大的動態(tài)傳動誤差臨界值 γ1。由于在變形過程中可以發(fā)揮補(bǔ)償?shù)男Ч越档土藙討B(tài)傳動誤差的波動性,能夠在更短時(shí)間內(nèi)完成瞬態(tài)轉(zhuǎn)變,使整體變化更加平緩;從而形成了明顯滯后的動態(tài)傳動誤差最值 Γ。
為分析 λ、P 引起的 Γ 變化,選擇 λ 作為自變量,以 Γ 作為因變量擬合得到圖 3 結(jié)果。分析圖 3可以得到以下結(jié)論。
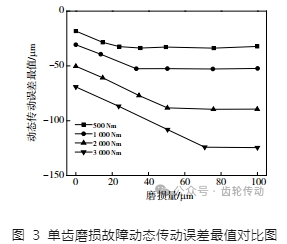
1)恒定載荷下,發(fā)生初始階段的齒面磨損時(shí), Γ 和 λ 表現(xiàn)為單調(diào)遞增的趨勢,提高齒面磨損量 λ 后,發(fā)生了擬合函數(shù)斜率 ε1突變達(dá)到 0,獲得上述載荷的誤差臨界值 γ1 。
2)提高載荷 P 后,擬合函數(shù)斜率 ε1和截距 η1 都形成了更大的絕對值;考慮到弧齒錐齒輪具備較高重合度,此時(shí)臨界值 γ1狀態(tài)發(fā)生持續(xù)提高。
全齒磨損動態(tài)傳動誤差曲線
當(dāng)發(fā)生全齒磨損故障時(shí),對各載荷進(jìn)行動態(tài)傳動誤差測試得到圖 4 結(jié)果。對圖 4 進(jìn)行分析可以發(fā)現(xiàn),逐漸提高齒面磨損量時(shí),形成了更大的動態(tài)傳動誤差。當(dāng)載荷提高后,曲線可以在更短時(shí)間內(nèi)進(jìn)入穩(wěn)態(tài)階段,大幅減小了波動性,形成了更大的動態(tài)傳動誤差 γ 絕對值。
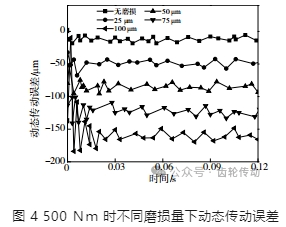
所有齒輪都達(dá)到相同的磨損量,不會出現(xiàn)單齒故障情況下磨損齒不受載荷作用的現(xiàn)象,這使得在全齒磨損故障條件下形成了更穩(wěn)定的動態(tài)傳動誤差。
全齒磨損故障動態(tài)傳動誤差平均值對比結(jié)果如圖 5 所示。分析圖 5 發(fā)現(xiàn),全齒磨損量 λ 和傳動誤差均值 E 形成了線性變化的特征,各載荷下形成了幾乎平行的擬合直線,得到表 3 的各項(xiàng)參數(shù)。
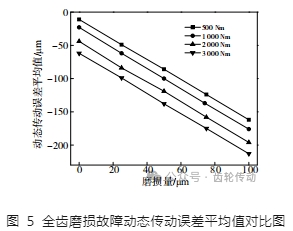
繼續(xù)擬合可得

利用式(6)可估算出存在全齒磨損故障條件下弧齒錐齒輪動態(tài)傳動誤差。
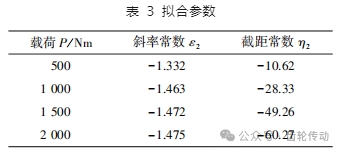
4、結(jié)語
1)提高齒面磨損量 λ 時(shí),動態(tài)傳動誤差 γ 上升,獲得了更大的 Γ;處于恒定載荷下時(shí),初始階段 Γ 和 λ 表現(xiàn)為單調(diào)遞增的趨勢;提高齒面磨損量 λ 后,擬合函數(shù)斜率突變達(dá)到 0。提高載荷 P 后,擬合函數(shù)斜率和截距都形成了更大的絕對值。
2)逐漸提高齒面磨損量時(shí),形成了更大的動態(tài)傳動誤差。當(dāng)載荷提高后,曲線可以在更短時(shí)間內(nèi)進(jìn)入穩(wěn)態(tài)階段,大幅減小了波動性,形成了更大的動態(tài)傳動誤差 γ 絕對值。
參考文獻(xiàn)略.