在設計開發六檔轎車變速器時,最大輸入扭矩增加到180Nm以上,為了減少變速器重量,結構更加輕便,僅采用滲碳淬火工藝已無法滿足齒輪疲勞壽命的設計要求。為此,我司從材料、工藝上進行新的嘗試來提升齒輪根部的彎曲疲勞強度和齒輪表面的接觸疲勞強度。而影響疲勞強度的因素有受力狀態、工作溫度、材料的化學成分及顯微組織、表面質量和殘余應力等。現主要考慮合金元素、表面狀態對疲勞強度的影響,通過工藝開發,充分發掘材料的性能來提高疲勞強度,滿足疲勞壽命的設計要求。
1.增加低碳合金鋼中Ni元素含量
變速器齒輪可采用SAE8620H材料代替20CrMoH來提高齒輪根部的彎曲疲勞強度,表1為SAE8620H與20CrMoH材料主要化學成分的區別。SAE8620H材料Ni元素含量增加了約0.50%,Cr元素含量減少約0.50%,即用0.50%的Ni元素代替0.50%的Cr元素。Ni元素能中等強化鐵素體,增加Ni元素能很好地提高心部鐵素體組織的強度。分別抽取不同爐號的10個試樣,進行力學性能試驗,見表2,SAE8620H試樣屈服強度明顯高于20CrMoH試樣10%以上,有利于齒輪根部彎曲疲勞強度的提升。
表1 20CrMoH與SAE8620H主要化學成分(質量分數)要求(%)
表2 20CrMoH和SAE8620H屈服強度對比
2.控制齒輪淬火后的心部硬度
而Ni元素對淬透性的影響弱于Cr元素,在其他主要成分相差不大時,SAE8620H的淬透性明顯低于20CrMoH,J9端淬值通常低3HRC左右,即使轎車變速器齒輪模數≤3mm,但對心部硬度造成的影響很明顯。為了充分發揮SAE8620H材料的韌性,提高齒輪根部彎曲疲勞強度,通過臺架試驗發現轎車變速器齒輪的心部硬度最佳控制在35~40HRC。SAE8620H材料可以采取如下措施來提高齒根心部硬度:選取合適的端淬值;適當冷速的淬火油;提高淬火溫度;提高淬火時冷卻烈度及均勻性等。
3.選取合適的噴丸強化工藝
對扭矩要求更高的齒輪副,在齒部精加工后增加強力噴丸工藝,在齒輪表層形成一塑性變形層即強化層,當前我司噴丸強化工藝強化層深度約為0.15mm。利用該表面塑性變形層分別從殘余壓應力場、變形顯微組織、殘留奧氏體向馬氏體轉變、機加工刀痕的有效消除等方面來改善齒輪的疲勞強度。
但噴丸強化是具有動能的高速鋼丸噴打到齒面,使齒部產生塑性變形,對齒面存在較大的損傷。對于研磨齒面,粗糙度變差約0.2μm、齒部精度下降一級以上。通過選取較低的噴丸強度(弧高值0.2~0.3mmA),配合圓度G2級以上的切絲鋼丸,能有效減少齒面塑性變形量,而表層殘余壓應力又能達到600MPa以上的設計要求。 在正常噴丸強化后,采用直徑0.2mm的切絲鋼丸再進行一次更低強度的噴打,能進一步優化齒面粗糙度,減少表層疲勞微裂紋源。
4.噴丸強化后磷化處理
針對噴丸強化后齒面損傷問題,可在噴丸強化后再增加錳系抗磨磷化工藝。齒面在噴丸強化過程中產生了大量的凹坑,磷化膜能很好地覆蓋凹坑,提升齒面粗糙度,同時磷化膜具有多孔結構可吸附大量潤滑油,改善齒面潤滑狀況。為了獲得的較好的存油效果,采用90~98℃的高溫磷化工藝,磷化膜厚度10~25μm,磷化膜晶粒度3~16μm,表面腐蝕深度控制在0~4級。經實驗測量,磷化后齒面摩擦因數約為0.151,優于普通磨齒齒面摩擦因數,改善了齒面嚙合時潤滑狀態,從而延長了齒輪副疲勞壽命。
5.噴丸強化后高能等離子噴涂處理
(1)表層顯微組織相變強化
高能等離子噴涂工藝致使表層約20μm深度區域化學成分及顯微組織發生改變,從20μm~0.15mm處依然是噴丸強化層。高能等離子噴涂,采用Mo等合金元素組成的復合材料,鉬能使鋼的晶粒細化,提高力學性能。在高溫高壓的條件下撞擊并滲透進母材的20μm以內深度表面,使金屬表面20μm以內深度的晶相組織發生改變(見圖1、圖2),圖2表面波紋度很小,幾乎沒有晶界氧化,疲勞微裂紋就不易從表面發生,有利于齒面疲勞強度的提高。
圖1 滲碳淬火后金相組織(500×)
圖2 噴涂后金相組織(500×)
經過高能等離子噴涂后,表面顯微硬度有所提升(見表3),雖影響很淺,但能適當提升齒面接觸疲勞強度。
表3 輸入軸噴涂前后表面硬度值
(2)殘余壓應力增加
從殘余應力檢測值表4可看出,次表層殘余壓應力增加量達到10%以上,進一步強化了壓應力場,而提升疲勞強度。
表4 輸入軸齒部噴涂前后殘余應力值
(3)齒面摩擦因數的改善
在加工過程中加入固體潤滑劑,固體潤滑劑滲入金屬表面后,使表面具有自潤滑的效果,摩擦阻力減少。經過摩擦試驗測試(見圖3),干摩擦因數下降12.1%,濕摩擦因數下降7.8%,齒輪副在嚙合過程中,齒面運轉狀況得到進一步改善。
經過高能等離子噴涂后,齒形輪廓偏差、螺旋線輪廓偏差值下降4~6μm;對于0.8~1.6μm的磨、剃齒面,齒面粗糙度改善約50%(見表5)。高能等離子噴涂能很好地彌補噴丸強化給齒面帶來的損傷,優化齒輪表面質量,從而提升疲勞強度。
表5 輸入軸噴涂前后粗糙度變化
6.結語
綜上所述,提高低碳合金鋼齒輪的疲勞強度,可以采取以下措施:
(1)選取韌性較好的SAE8620H等含Ni低碳合金鋼。
(2)采用合適的滲碳淬火工藝,控制齒輪心部硬度。
(3)采取適當的噴丸強化工藝,提升表層殘余壓應力值。
(4)強噴后增加高溫等離子噴涂等復合工藝。
1.增加低碳合金鋼中Ni元素含量
變速器齒輪可采用SAE8620H材料代替20CrMoH來提高齒輪根部的彎曲疲勞強度,表1為SAE8620H與20CrMoH材料主要化學成分的區別。SAE8620H材料Ni元素含量增加了約0.50%,Cr元素含量減少約0.50%,即用0.50%的Ni元素代替0.50%的Cr元素。Ni元素能中等強化鐵素體,增加Ni元素能很好地提高心部鐵素體組織的強度。分別抽取不同爐號的10個試樣,進行力學性能試驗,見表2,SAE8620H試樣屈服強度明顯高于20CrMoH試樣10%以上,有利于齒輪根部彎曲疲勞強度的提升。
表1 20CrMoH與SAE8620H主要化學成分(質量分數)要求(%)
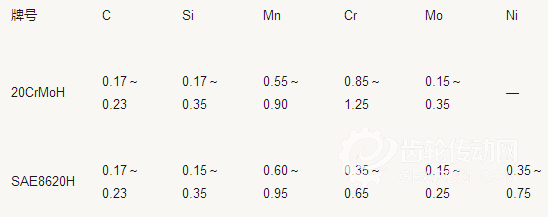
表2 20CrMoH和SAE8620H屈服強度對比
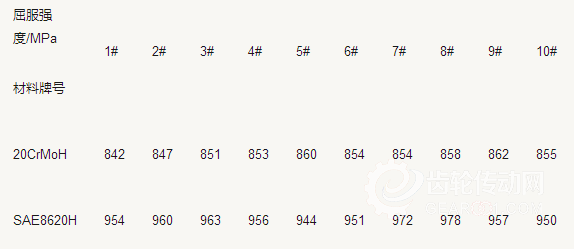
2.控制齒輪淬火后的心部硬度
而Ni元素對淬透性的影響弱于Cr元素,在其他主要成分相差不大時,SAE8620H的淬透性明顯低于20CrMoH,J9端淬值通常低3HRC左右,即使轎車變速器齒輪模數≤3mm,但對心部硬度造成的影響很明顯。為了充分發揮SAE8620H材料的韌性,提高齒輪根部彎曲疲勞強度,通過臺架試驗發現轎車變速器齒輪的心部硬度最佳控制在35~40HRC。SAE8620H材料可以采取如下措施來提高齒根心部硬度:選取合適的端淬值;適當冷速的淬火油;提高淬火溫度;提高淬火時冷卻烈度及均勻性等。
3.選取合適的噴丸強化工藝
對扭矩要求更高的齒輪副,在齒部精加工后增加強力噴丸工藝,在齒輪表層形成一塑性變形層即強化層,當前我司噴丸強化工藝強化層深度約為0.15mm。利用該表面塑性變形層分別從殘余壓應力場、變形顯微組織、殘留奧氏體向馬氏體轉變、機加工刀痕的有效消除等方面來改善齒輪的疲勞強度。
但噴丸強化是具有動能的高速鋼丸噴打到齒面,使齒部產生塑性變形,對齒面存在較大的損傷。對于研磨齒面,粗糙度變差約0.2μm、齒部精度下降一級以上。通過選取較低的噴丸強度(弧高值0.2~0.3mmA),配合圓度G2級以上的切絲鋼丸,能有效減少齒面塑性變形量,而表層殘余壓應力又能達到600MPa以上的設計要求。 在正常噴丸強化后,采用直徑0.2mm的切絲鋼丸再進行一次更低強度的噴打,能進一步優化齒面粗糙度,減少表層疲勞微裂紋源。
4.噴丸強化后磷化處理
針對噴丸強化后齒面損傷問題,可在噴丸強化后再增加錳系抗磨磷化工藝。齒面在噴丸強化過程中產生了大量的凹坑,磷化膜能很好地覆蓋凹坑,提升齒面粗糙度,同時磷化膜具有多孔結構可吸附大量潤滑油,改善齒面潤滑狀況。為了獲得的較好的存油效果,采用90~98℃的高溫磷化工藝,磷化膜厚度10~25μm,磷化膜晶粒度3~16μm,表面腐蝕深度控制在0~4級。經實驗測量,磷化后齒面摩擦因數約為0.151,優于普通磨齒齒面摩擦因數,改善了齒面嚙合時潤滑狀態,從而延長了齒輪副疲勞壽命。
5.噴丸強化后高能等離子噴涂處理
(1)表層顯微組織相變強化
高能等離子噴涂工藝致使表層約20μm深度區域化學成分及顯微組織發生改變,從20μm~0.15mm處依然是噴丸強化層。高能等離子噴涂,采用Mo等合金元素組成的復合材料,鉬能使鋼的晶粒細化,提高力學性能。在高溫高壓的條件下撞擊并滲透進母材的20μm以內深度表面,使金屬表面20μm以內深度的晶相組織發生改變(見圖1、圖2),圖2表面波紋度很小,幾乎沒有晶界氧化,疲勞微裂紋就不易從表面發生,有利于齒面疲勞強度的提高。
圖1 滲碳淬火后金相組織(500×)
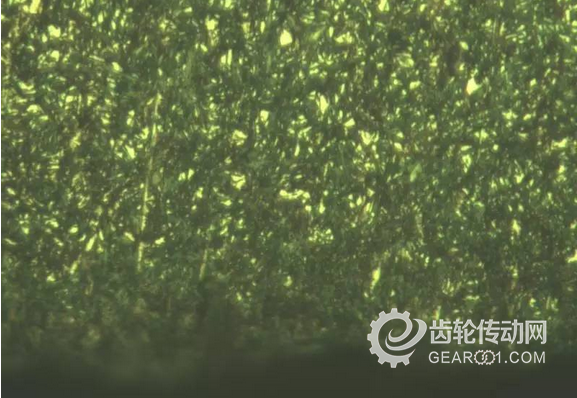
圖2 噴涂后金相組織(500×)
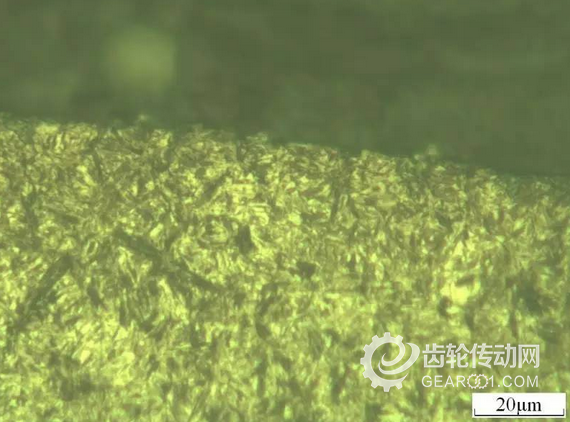
經過高能等離子噴涂后,表面顯微硬度有所提升(見表3),雖影響很淺,但能適當提升齒面接觸疲勞強度。
表3 輸入軸噴涂前后表面硬度值
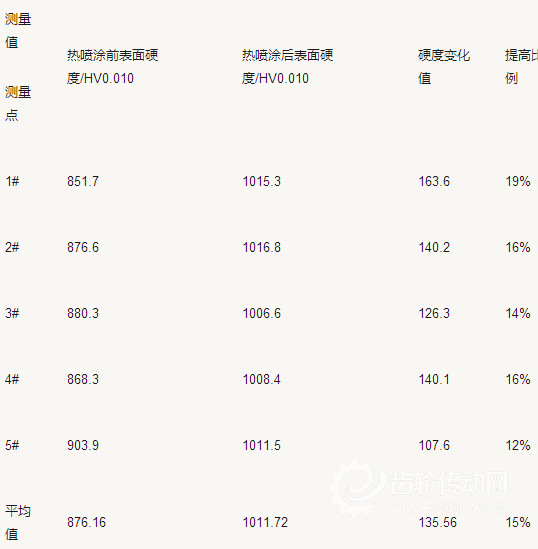
(2)殘余壓應力增加
從殘余應力檢測值表4可看出,次表層殘余壓應力增加量達到10%以上,進一步強化了壓應力場,而提升疲勞強度。
表4 輸入軸齒部噴涂前后殘余應力值
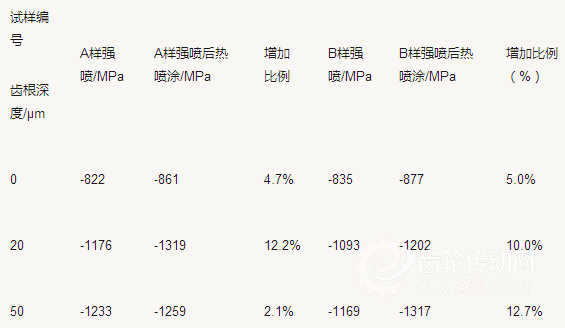
(3)齒面摩擦因數的改善
在加工過程中加入固體潤滑劑,固體潤滑劑滲入金屬表面后,使表面具有自潤滑的效果,摩擦阻力減少。經過摩擦試驗測試(見圖3),干摩擦因數下降12.1%,濕摩擦因數下降7.8%,齒輪副在嚙合過程中,齒面運轉狀況得到進一步改善。
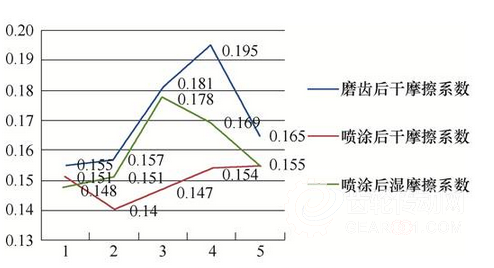
經過高能等離子噴涂后,齒形輪廓偏差、螺旋線輪廓偏差值下降4~6μm;對于0.8~1.6μm的磨、剃齒面,齒面粗糙度改善約50%(見表5)。高能等離子噴涂能很好地彌補噴丸強化給齒面帶來的損傷,優化齒輪表面質量,從而提升疲勞強度。
表5 輸入軸噴涂前后粗糙度變化
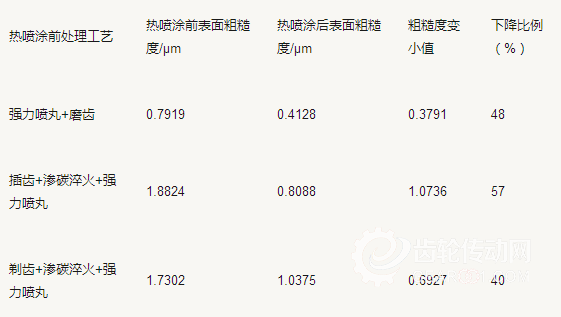
綜上所述,提高低碳合金鋼齒輪的疲勞強度,可以采取以下措施:
(1)選取韌性較好的SAE8620H等含Ni低碳合金鋼。
(2)采用合適的滲碳淬火工藝,控制齒輪心部硬度。
(3)采取適當的噴丸強化工藝,提升表層殘余壓應力值。
(4)強噴后增加高溫等離子噴涂等復合工藝。