蔡司的免相關性驗證測量被視為是行業創新,因為它從根本上永久改變了在線測量技術,并最終改變了制造業。全球創新不僅使汽車制造商能更高效地測量和生產,并使他們向未來的“智能工廠”大幅邁進。
“免相關性驗證的測量將為在線測量技術提供全新的平臺并提高生產效率,”蔡司自動化檢測部門主管Kai-Udo Modrich博士說。為了讓您更好地理解汽車制造商如何從使用這種技術中獲益,我們決定快速瀏覽一下所有的在線測量解決方案。
尺寸準確性-全世界汽車制造商的全部及最終目標
汽車制造商使用在線測量系統監控生產,滿足其高質量標準。這些系統能檢測與設定特性的形狀偏差,并在生產周期中提供100%的檢測,使制造商能夠大幅地減少前提調整時間,尤其是在產品提速生產階段。而檢查形狀特點的速度和精度主要取決于使用的光學測頭。去年,ZEISS AIMax Cloud測頭在Automatica展覽會上給車身專家留下了深刻的印象。該3D探頭使用邊緣投影在幾分之一秒時間內產生一個點云。除了常見的形狀特點,新的測頭設計使其可以快速、精確地獲得過去難以測量或無法測量的特性(如鉚釘)。通過獲得厚點云,ZEISS AIMax Cloud只用一次拍攝就能立即測量多個特性。
此外,即使極小的特性和差異極大的表面也能精確測量。
Modrich解釋說:“ZEISS AIMax Cloud設定了基于機器人的3D在線測量技術用于車身制造的新標準。”柔性機器人在所有在線系統中非常普遍,機械臂將這個優異的測頭移動到各個車身部件上的對應特點。這種方法能確保整個測量系統提供準確的結果,無需后續測量。
傳統的在線測量系統,其測量基準的重復精度是由溫度補償來保證的。由于自熱和環境溫度的變化,需要對機器人臂的延伸進行有效補償。機器人測量一般具有極小的絕對精度,通常通過在三坐標測量機(CMM)上進行對比測量來補償測定的測量值,然后使用多次測量來檢查相關性。Modrich將測量實驗室中的額外CMM工作負載視為問題。
可靠性從第一個部件開始
蔡司開發的免相關性驗證測量確??煽康販y量組件尺寸。該系統使用標準照相機來檢測機器人與其規定位置的偏差,該偏差可能是由之前說過的溫度影響而導致的。這些照相機安裝在在線單元上方,輕松跟蹤ZEISS AIMax Cloud測頭的每個動作。機械臂和在線檢測單元上有標志,因此系統能確定測頭在空間中的絕對位置。通過這些信息以及智能算法,蔡司開發的這款軟件就能檢測到與標準狀態的偏差,并立即濾出。有了該系統,公司不再需要定期在高精度CMM上對車身部件進行后續測量,然后將發現的在線和CMM測量結果之間的差異傳輸到在線測量系統作為校準值。“現在制造商可以放心,從第一個部件開始測量的數值都是正確的,”Modrich說。“我和很多客戶交談過,我知道汽車制造商都在迫切地等待這款產品,因為好處很明顯:公司大幅加快了制造新車型的提速生產時間,并更快達到所需的生產節拍。這些都意味著切實的節約成本。“對于這個智能生產專家來說,這只是最明顯的好處。由于該系統已經從第一個部件開始提供可靠的數據,它在在線測量站和焊接機器人之間形成生產閉環的基礎。軟件開發人員仍在致力于整合技術員工的多年經驗。但對Modrich來說只是時間問題。“在線測量數據直接控制制造機器的那天將要到來。”
“免相關性驗證的測量將為在線測量技術提供全新的平臺并提高生產效率,”蔡司自動化檢測部門主管Kai-Udo Modrich博士說。為了讓您更好地理解汽車制造商如何從使用這種技術中獲益,我們決定快速瀏覽一下所有的在線測量解決方案。
尺寸準確性-全世界汽車制造商的全部及最終目標
汽車制造商使用在線測量系統監控生產,滿足其高質量標準。這些系統能檢測與設定特性的形狀偏差,并在生產周期中提供100%的檢測,使制造商能夠大幅地減少前提調整時間,尤其是在產品提速生產階段。而檢查形狀特點的速度和精度主要取決于使用的光學測頭。去年,ZEISS AIMax Cloud測頭在Automatica展覽會上給車身專家留下了深刻的印象。該3D探頭使用邊緣投影在幾分之一秒時間內產生一個點云。除了常見的形狀特點,新的測頭設計使其可以快速、精確地獲得過去難以測量或無法測量的特性(如鉚釘)。通過獲得厚點云,ZEISS AIMax Cloud只用一次拍攝就能立即測量多個特性。
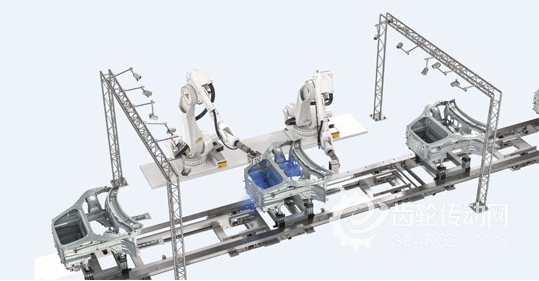
此外,即使極小的特性和差異極大的表面也能精確測量。
Modrich解釋說:“ZEISS AIMax Cloud設定了基于機器人的3D在線測量技術用于車身制造的新標準。”柔性機器人在所有在線系統中非常普遍,機械臂將這個優異的測頭移動到各個車身部件上的對應特點。這種方法能確保整個測量系統提供準確的結果,無需后續測量。
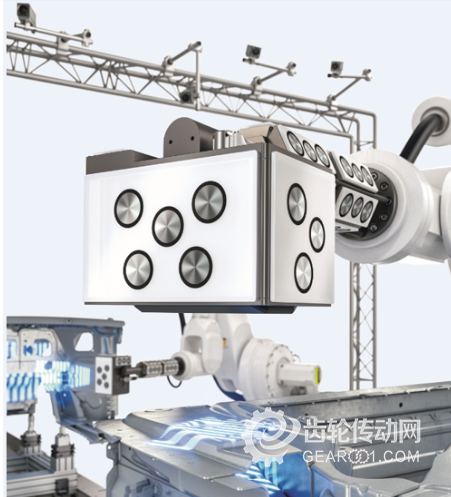
傳統的在線測量系統,其測量基準的重復精度是由溫度補償來保證的。由于自熱和環境溫度的變化,需要對機器人臂的延伸進行有效補償。機器人測量一般具有極小的絕對精度,通常通過在三坐標測量機(CMM)上進行對比測量來補償測定的測量值,然后使用多次測量來檢查相關性。Modrich將測量實驗室中的額外CMM工作負載視為問題。
可靠性從第一個部件開始
蔡司開發的免相關性驗證測量確??煽康販y量組件尺寸。該系統使用標準照相機來檢測機器人與其規定位置的偏差,該偏差可能是由之前說過的溫度影響而導致的。這些照相機安裝在在線單元上方,輕松跟蹤ZEISS AIMax Cloud測頭的每個動作。機械臂和在線檢測單元上有標志,因此系統能確定測頭在空間中的絕對位置。通過這些信息以及智能算法,蔡司開發的這款軟件就能檢測到與標準狀態的偏差,并立即濾出。有了該系統,公司不再需要定期在高精度CMM上對車身部件進行后續測量,然后將發現的在線和CMM測量結果之間的差異傳輸到在線測量系統作為校準值。“現在制造商可以放心,從第一個部件開始測量的數值都是正確的,”Modrich說。“我和很多客戶交談過,我知道汽車制造商都在迫切地等待這款產品,因為好處很明顯:公司大幅加快了制造新車型的提速生產時間,并更快達到所需的生產節拍。這些都意味著切實的節約成本。“對于這個智能生產專家來說,這只是最明顯的好處。由于該系統已經從第一個部件開始提供可靠的數據,它在在線測量站和焊接機器人之間形成生產閉環的基礎。軟件開發人員仍在致力于整合技術員工的多年經驗。但對Modrich來說只是時間問題。“在線測量數據直接控制制造機器的那天將要到來。”
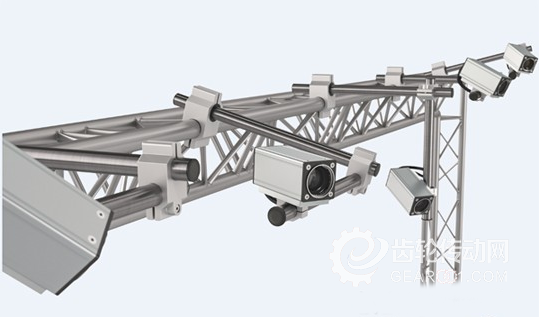