滾剃工藝方案
二軸一擋齒輪在變速器中主要在起步和爬坡時發揮其功能,其運轉齒的齒形齒向精度對變速器的噪聲影響不是決定性的因素。根據這種情況,考慮對客車用變速器中的該零件進行磨齒改剃齒的工藝改進,能提高生產效率,降低生產成本。
滾剃工藝方案為:鍛坯→等溫正火→粗、精車→插齒→滾齒→剃齒→滲碳降溫/直接淬火/回火、應力噴丸→磨削孔及端面加工→嚙合噪聲檢驗→清洗→終檢→入庫。
滾剃工藝中的剃齒加工
剃齒是精加工齒輪的一種方法。由于剃削生產率高、齒輪質量好、剃齒刀具使用壽命長以及所用機床結構簡單、調整方便,所以在成批生產的汽車、拖拉機和機床等齒輪加工中,剃齒工藝得到了廣泛應用。
1.剃齒的加工方式
按剃削的進給方向,剃齒加工方式有軸向剃齒、對角剃齒、切向剃齒、徑向進給剃齒四種方式。根據我公司產品特點、生產批量和剃齒機的狀況,在產品加工中均采用軸向剃齒和徑向剃齒兩種方式。本文中,二軸一擋齒輪的剃齒加工采用軸向剃齒法進行加工。
2.機床與工裝
(1)剃齒機 采用前西德ZSA320剃齒機,可加工直齒和斜齒圓柱齒輪,并能加工鼓形齒和小錐度齒輪,可進行軸向、對角和切向三種剃齒,精度等級5級,表面粗糙度值Ra=0.63μm。
(2)剃齒刀 選擇盤形剃齒刀,精度A級,采用W6Mo5Cr4V2鋼自制的標準型剃齒刀經修形加工后使用,基本參數為直徑244mm、寬度25mm、齒數46、螺旋角2.5°、軸交角10°。
(3)剃齒夾具 采用浮動式夾具,該夾具以產品內圓面為基準,以減小工件的裝夾誤差。
(4)刀具與工件裝夾 剃齒刀裝夾后其軸向圓跳動和徑向圓跳動都≤0.01mm。在產品裝夾時要求機床前后頂尖的徑向圓跳動≤0.005mm,兩頂尖中心連線(頂尖間距在150mm內)對工作臺移動方向的偏移≤0.01mm,機床主軸的端面和徑向跳動≤0.005mm,墊圈兩端面的平行度≤0.005mm。同時保證剃齒心軸與齒輪內孔有良好的配合,有最小的配合間隙。
3.剃齒剃削參數控制
(1)齒輪要求的技術參數 剃齒要求控制的參數值通過分析熱前、熱后各參數的變化規律確定。該齒輪剃齒參數的控制值見附表。因剃齒為熱前工序,考慮熱前修正問題,所以齒形、齒向根據冷熱變形情況具體確定,附表中齒形、齒向公差值僅供參考。
(2)切削速度 盤形剃齒刀工作時,齒高上各點的切削速度是變化的。一般所說的切削速度是指嚙合節點處的滑動速度。合金鋼材料的剃齒刀切削速度為105m/min,最后計算工件轉速nw為141r/min。
(3)進給量 縱向進給量與齒面粗糙度、刀具使用壽命及生產率有關,對于表面粗糙度要求細、材料硬度高的齒輪應取較小值。縱向進給量分為工件每轉縱向進給量f(mm/r)和工作臺每分鐘縱向進給量vf(mm/min),二者之間關系為:vf = fnw
對二軸齒輪來說,f值可取0.1~0.2mm/r。根據多次試剃結果,確定粗、精加工工作臺vf分別為35mm/min和20mm/min。
徑向進給量與機床、夾具的剛度及剃齒時修正剃前誤差的能力有關。根據我公司長期生產情況,按經驗留剃削余量0.09~0.12mm。根據相關資料,每單行程0.02~0.06mm。對中間軸齒輪最后確定的徑向進給量,按0.10mm剃削余量分配每單行程分別為0.02mm、0.03mm、0.03mm和0.02mm。
(4)行程次數 行程次數分為切削行程次數和光整行程次數,切削行程次數根據剃齒余量和徑向進給量而定。當徑向進給量較小時,過多的行程次數會使切削條件變壞,同時使刀具使用壽命降低。而光整行程次數同齒面粗糙度有關,光整行程次數增加,齒面粗糙度參數值降低。同時,切削及光整行程總次數均應采用雙數。二軸一擋齒輪剃齒加工中,切削行程的單行程次數為四次,光整行程的單行程數次數為兩次。
(5)軸交角和切削液?剃齒刀與工件的軸交角是影響剃削性能的一項重要因素,它直接影響刀刃的切削性能、加工表面質量、剃削工件齒形精度和刀具使用壽命。軸交角范圍一般為10°~20°,根據齒輪參數和剃齒刀參數可知本文所提齒輪的剃齒軸交角為10°。剃齒加工中應使用充足的、潤滑性和流動性較好的切削液,以獲得良好的剃齒效果。
4.剃齒精度的保證
剃齒加工過程中,刀具與工件間沒有傳動鏈,而是一種自由傳動。剃齒對校正被剃齒輪的各項誤差能力是不相同的,有些誤差能夠校正,有些誤差基本上不能校正,或校正后又轉換為別的誤差形式出現。由于剃齒機理上的先天缺陷,剃齒后齒形一般要出現凹變,破壞正確的漸開線齒廓,因而,常對剃齒刀齒形要進行修正。根據剃齒工藝特點,合理確定剃前齒輪的精度十分重要。
(1)剃前齒坯要求 控制工件材料的質量,如硬度要均勻,不應有硬的雜質與氣孔等局部缺陷,以防止剃齒刀過早磨鈍;要保持剃齒基準面和剃前切齒加工的基準面一致;剃前切齒齒面不應有加工硬痕;剃齒刀齒頂和工件齒根不發生干涉;提高剃前加工精度,減小剃齒余量;保證剃前齒輪精度達到:第一公差組(主要是影響傳遞運動準確的誤差項目Fw、Fr)不低于剃后要求,其他誤差項目可以比剃后精度低一級;視熱處理變形情況進行預修整,可采用剃前切齒刀具齒形預修整或齒向(螺旋角)預修整。
(2)剃齒要求?結合剃前預修整,剃齒刀還可根據熱處理變形進行部分預修整;為保持剃齒刀修正工件誤差的能力,剃齒時的重合度應≤1.5mm;剃齒刀應及時刃磨,保持刀刃鋒利。剃齒刀磨鈍時,工件齒面出現擠痕,齒形誤差增大,接觸精度下降,剃齒時噪聲增大;選用合理的切削用量。剃齒速度對工件齒形和齒距精度影響顯著,光整行程次數對加工齒面質量有較大影響;根據工件材質選用合適切削液并需過濾。
5.剃齒過程注意事項
在剃齒加工中,必須注意以下幾點:
1)不合理的切削用量將導致控制參數不穩定,產生在齒輪上的剃齒應力變化異常,最終使齒輪熱變形無規律。
2)機床調整后必須先進行試剃齒輪,經檢驗合格后,才進行批量生產。
3)在剃齒過程中若發現齒面失去了剃刀花紋,出現了擠壓痕跡,齒面無光澤,齒形端面出現較大飛邊,有啃刀現象,齒形誤差增大,剃齒過程發生異常聲音等情況時必須及時換刀。
剃齒刀的修形
1.剃齒刀刃磨依據
對齒輪滾剃或滾剃修磨工藝來說,剃齒刀的刃磨修形極為重要。由于產品不同、要求不同,其齒形修正程度也就有所不同。剃齒刀齒形修磨的主要依據有三點:
1)由齒輪嚙合的原理可知,剃齒刀與被加工齒輪嚙合時,由于瞬時傳動比的變化,引起了瞬時切削力的差異,從而使被加工齒輪在節圓附近產生0.01~0.02mm不等的中凹現象,偏離理論漸開線,因而剃齒刀必須在其相應區域將齒形修凹0.01~0.02mm,以補償齒輪齒形中凹量。
2)實際上對具有理論漸開線的齒輪在載荷下嚙合傳動時,也不能保證傳動中平穩運轉和不發生噪聲,所以必須要有合理的齒形以減少載荷嚙合下的干涉。
3)由于在熱處理過程中齒輪都會產生齒形、齒向的變形,必須對熱前剃齒刀修形提出要求。當然,要準確地確定剃齒刀齒形十分困難,因為它不僅關系到齒輪的最終齒形和齒向,而且還將直接關系到剃齒質量的好壞,所以往往需要經過多次反復試剃齒輪后才能獲得最佳的剃齒刀修形曲線。
2.剃齒刀齒形修形的基本方法
1)首先用符合設計精度要求的標準漸開線剃齒刀先對被加工齒輪進行試剃,剃削過程必須正確,調整機床和裝夾等各項操作因素必須嚴格執行切削規范,并將剃好的齒輪在漸開線檢查儀上測繪出齒廓的齒形曲線。
2)根據被剃齒輪所測得的齒廓形狀和曲線中凹量,算出齒輪凹量ρf 的樣板角度值、剃齒刀ρf 附加傾斜角的角度值,選定剃齒刀修正對應點的角度樣板及改變磨削安裝角的角度值。
3)經上述方法修磨齒形后的剃齒刀剃出的齒輪基本上能滿足齒廓形狀的要求,但還需根據實際情況多次摸清產品熱處理后的變形情況,再次對剃齒刀進行相應的修磨,然后用經再次修形后的剃齒刀加工齒輪,直到剃出合格的接觸斑痕和漸開線形狀為止。
在剃削齒輪時,開始采用標準齒形的剃齒刀剃削出來的產品壓力角偏小,齒形修正0.015~0.018mm,根據這一齒形我們對剃齒刀齒形修正-0.015mm,再次對產品進行試剃,最終使產品的齒形符合產品設計要求,經總成裝配前的配對噪聲檢測,90%以上產品合格。
剃齒熱前后數據的統計分析
在二軸一擋齒輪滾剃工藝改進的剃齒控制中,進行了公法線數據的測量,一共測量了12件齒輪的熱前后公法線長度值。結果表明,齒輪剃齒加工后的公法線值,在現有熱處理條件下其熱前后值有上漲的趨勢,其絕對變形量基本上集中在0.02mm,符合齒輪公法線長度公差0.06mm的要求;且熱后公法線值滿足成品尺寸及公司的相關質量偏離的技術要求(成品公法線值W8=110.82~110.759,Fw≤0.045mm)。這也說明了齒輪公法線值的控制重點在剃齒工序。為了較準確地表明剃齒的效果好壞,在加工中還測量了齒輪的熱前后齒形齒向對比曲線。
結果顯示,剃齒后的齒形齒向曲線熱前后走向一致,變化較小,變化相對穩定,說明保證齒輪熱后的齒形齒向要求,剃齒控制是關鍵。
結語
通過二軸一擋齒輪的滾剃工藝實例分析,證明了滾剃工藝具有可行性,并且剃齒控制是關鍵。只有將兩者緊密地結合起來,滾剃工藝推廣才能得以實施,“滾剃磨”工藝改為“滾剃”工藝可以大大降低產品的磨齒加工時間,縮短產品的制造周期,經濟效益顯著。
二軸一擋齒輪在變速器中主要在起步和爬坡時發揮其功能,其運轉齒的齒形齒向精度對變速器的噪聲影響不是決定性的因素。根據這種情況,考慮對客車用變速器中的該零件進行磨齒改剃齒的工藝改進,能提高生產效率,降低生產成本。
滾剃工藝方案為:鍛坯→等溫正火→粗、精車→插齒→滾齒→剃齒→滲碳降溫/直接淬火/回火、應力噴丸→磨削孔及端面加工→嚙合噪聲檢驗→清洗→終檢→入庫。
滾剃工藝中的剃齒加工
剃齒是精加工齒輪的一種方法。由于剃削生產率高、齒輪質量好、剃齒刀具使用壽命長以及所用機床結構簡單、調整方便,所以在成批生產的汽車、拖拉機和機床等齒輪加工中,剃齒工藝得到了廣泛應用。
1.剃齒的加工方式
按剃削的進給方向,剃齒加工方式有軸向剃齒、對角剃齒、切向剃齒、徑向進給剃齒四種方式。根據我公司產品特點、生產批量和剃齒機的狀況,在產品加工中均采用軸向剃齒和徑向剃齒兩種方式。本文中,二軸一擋齒輪的剃齒加工采用軸向剃齒法進行加工。
2.機床與工裝
(1)剃齒機 采用前西德ZSA320剃齒機,可加工直齒和斜齒圓柱齒輪,并能加工鼓形齒和小錐度齒輪,可進行軸向、對角和切向三種剃齒,精度等級5級,表面粗糙度值Ra=0.63μm。
(2)剃齒刀 選擇盤形剃齒刀,精度A級,采用W6Mo5Cr4V2鋼自制的標準型剃齒刀經修形加工后使用,基本參數為直徑244mm、寬度25mm、齒數46、螺旋角2.5°、軸交角10°。
(3)剃齒夾具 采用浮動式夾具,該夾具以產品內圓面為基準,以減小工件的裝夾誤差。
(4)刀具與工件裝夾 剃齒刀裝夾后其軸向圓跳動和徑向圓跳動都≤0.01mm。在產品裝夾時要求機床前后頂尖的徑向圓跳動≤0.005mm,兩頂尖中心連線(頂尖間距在150mm內)對工作臺移動方向的偏移≤0.01mm,機床主軸的端面和徑向跳動≤0.005mm,墊圈兩端面的平行度≤0.005mm。同時保證剃齒心軸與齒輪內孔有良好的配合,有最小的配合間隙。
3.剃齒剃削參數控制
(1)齒輪要求的技術參數 剃齒要求控制的參數值通過分析熱前、熱后各參數的變化規律確定。該齒輪剃齒參數的控制值見附表。因剃齒為熱前工序,考慮熱前修正問題,所以齒形、齒向根據冷熱變形情況具體確定,附表中齒形、齒向公差值僅供參考。
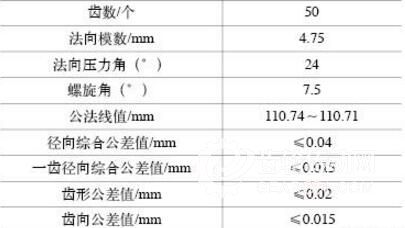
剃齒控制的參數表
(2)切削速度 盤形剃齒刀工作時,齒高上各點的切削速度是變化的。一般所說的切削速度是指嚙合節點處的滑動速度。合金鋼材料的剃齒刀切削速度為105m/min,最后計算工件轉速nw為141r/min。
(3)進給量 縱向進給量與齒面粗糙度、刀具使用壽命及生產率有關,對于表面粗糙度要求細、材料硬度高的齒輪應取較小值。縱向進給量分為工件每轉縱向進給量f(mm/r)和工作臺每分鐘縱向進給量vf(mm/min),二者之間關系為:vf = fnw
對二軸齒輪來說,f值可取0.1~0.2mm/r。根據多次試剃結果,確定粗、精加工工作臺vf分別為35mm/min和20mm/min。
徑向進給量與機床、夾具的剛度及剃齒時修正剃前誤差的能力有關。根據我公司長期生產情況,按經驗留剃削余量0.09~0.12mm。根據相關資料,每單行程0.02~0.06mm。對中間軸齒輪最后確定的徑向進給量,按0.10mm剃削余量分配每單行程分別為0.02mm、0.03mm、0.03mm和0.02mm。
(4)行程次數 行程次數分為切削行程次數和光整行程次數,切削行程次數根據剃齒余量和徑向進給量而定。當徑向進給量較小時,過多的行程次數會使切削條件變壞,同時使刀具使用壽命降低。而光整行程次數同齒面粗糙度有關,光整行程次數增加,齒面粗糙度參數值降低。同時,切削及光整行程總次數均應采用雙數。二軸一擋齒輪剃齒加工中,切削行程的單行程次數為四次,光整行程的單行程數次數為兩次。
(5)軸交角和切削液?剃齒刀與工件的軸交角是影響剃削性能的一項重要因素,它直接影響刀刃的切削性能、加工表面質量、剃削工件齒形精度和刀具使用壽命。軸交角范圍一般為10°~20°,根據齒輪參數和剃齒刀參數可知本文所提齒輪的剃齒軸交角為10°。剃齒加工中應使用充足的、潤滑性和流動性較好的切削液,以獲得良好的剃齒效果。
4.剃齒精度的保證
剃齒加工過程中,刀具與工件間沒有傳動鏈,而是一種自由傳動。剃齒對校正被剃齒輪的各項誤差能力是不相同的,有些誤差能夠校正,有些誤差基本上不能校正,或校正后又轉換為別的誤差形式出現。由于剃齒機理上的先天缺陷,剃齒后齒形一般要出現凹變,破壞正確的漸開線齒廓,因而,常對剃齒刀齒形要進行修正。根據剃齒工藝特點,合理確定剃前齒輪的精度十分重要。
(1)剃前齒坯要求 控制工件材料的質量,如硬度要均勻,不應有硬的雜質與氣孔等局部缺陷,以防止剃齒刀過早磨鈍;要保持剃齒基準面和剃前切齒加工的基準面一致;剃前切齒齒面不應有加工硬痕;剃齒刀齒頂和工件齒根不發生干涉;提高剃前加工精度,減小剃齒余量;保證剃前齒輪精度達到:第一公差組(主要是影響傳遞運動準確的誤差項目Fw、Fr)不低于剃后要求,其他誤差項目可以比剃后精度低一級;視熱處理變形情況進行預修整,可采用剃前切齒刀具齒形預修整或齒向(螺旋角)預修整。
(2)剃齒要求?結合剃前預修整,剃齒刀還可根據熱處理變形進行部分預修整;為保持剃齒刀修正工件誤差的能力,剃齒時的重合度應≤1.5mm;剃齒刀應及時刃磨,保持刀刃鋒利。剃齒刀磨鈍時,工件齒面出現擠痕,齒形誤差增大,接觸精度下降,剃齒時噪聲增大;選用合理的切削用量。剃齒速度對工件齒形和齒距精度影響顯著,光整行程次數對加工齒面質量有較大影響;根據工件材質選用合適切削液并需過濾。
5.剃齒過程注意事項
在剃齒加工中,必須注意以下幾點:
1)不合理的切削用量將導致控制參數不穩定,產生在齒輪上的剃齒應力變化異常,最終使齒輪熱變形無規律。
2)機床調整后必須先進行試剃齒輪,經檢驗合格后,才進行批量生產。
3)在剃齒過程中若發現齒面失去了剃刀花紋,出現了擠壓痕跡,齒面無光澤,齒形端面出現較大飛邊,有啃刀現象,齒形誤差增大,剃齒過程發生異常聲音等情況時必須及時換刀。
剃齒刀的修形
1.剃齒刀刃磨依據
對齒輪滾剃或滾剃修磨工藝來說,剃齒刀的刃磨修形極為重要。由于產品不同、要求不同,其齒形修正程度也就有所不同。剃齒刀齒形修磨的主要依據有三點:
1)由齒輪嚙合的原理可知,剃齒刀與被加工齒輪嚙合時,由于瞬時傳動比的變化,引起了瞬時切削力的差異,從而使被加工齒輪在節圓附近產生0.01~0.02mm不等的中凹現象,偏離理論漸開線,因而剃齒刀必須在其相應區域將齒形修凹0.01~0.02mm,以補償齒輪齒形中凹量。
2)實際上對具有理論漸開線的齒輪在載荷下嚙合傳動時,也不能保證傳動中平穩運轉和不發生噪聲,所以必須要有合理的齒形以減少載荷嚙合下的干涉。
3)由于在熱處理過程中齒輪都會產生齒形、齒向的變形,必須對熱前剃齒刀修形提出要求。當然,要準確地確定剃齒刀齒形十分困難,因為它不僅關系到齒輪的最終齒形和齒向,而且還將直接關系到剃齒質量的好壞,所以往往需要經過多次反復試剃齒輪后才能獲得最佳的剃齒刀修形曲線。
2.剃齒刀齒形修形的基本方法
1)首先用符合設計精度要求的標準漸開線剃齒刀先對被加工齒輪進行試剃,剃削過程必須正確,調整機床和裝夾等各項操作因素必須嚴格執行切削規范,并將剃好的齒輪在漸開線檢查儀上測繪出齒廓的齒形曲線。
2)根據被剃齒輪所測得的齒廓形狀和曲線中凹量,算出齒輪凹量ρf 的樣板角度值、剃齒刀ρf 附加傾斜角的角度值,選定剃齒刀修正對應點的角度樣板及改變磨削安裝角的角度值。
3)經上述方法修磨齒形后的剃齒刀剃出的齒輪基本上能滿足齒廓形狀的要求,但還需根據實際情況多次摸清產品熱處理后的變形情況,再次對剃齒刀進行相應的修磨,然后用經再次修形后的剃齒刀加工齒輪,直到剃出合格的接觸斑痕和漸開線形狀為止。
在剃削齒輪時,開始采用標準齒形的剃齒刀剃削出來的產品壓力角偏小,齒形修正0.015~0.018mm,根據這一齒形我們對剃齒刀齒形修正-0.015mm,再次對產品進行試剃,最終使產品的齒形符合產品設計要求,經總成裝配前的配對噪聲檢測,90%以上產品合格。
剃齒熱前后數據的統計分析
在二軸一擋齒輪滾剃工藝改進的剃齒控制中,進行了公法線數據的測量,一共測量了12件齒輪的熱前后公法線長度值。結果表明,齒輪剃齒加工后的公法線值,在現有熱處理條件下其熱前后值有上漲的趨勢,其絕對變形量基本上集中在0.02mm,符合齒輪公法線長度公差0.06mm的要求;且熱后公法線值滿足成品尺寸及公司的相關質量偏離的技術要求(成品公法線值W8=110.82~110.759,Fw≤0.045mm)。這也說明了齒輪公法線值的控制重點在剃齒工序。為了較準確地表明剃齒的效果好壞,在加工中還測量了齒輪的熱前后齒形齒向對比曲線。
結果顯示,剃齒后的齒形齒向曲線熱前后走向一致,變化較小,變化相對穩定,說明保證齒輪熱后的齒形齒向要求,剃齒控制是關鍵。
結語
通過二軸一擋齒輪的滾剃工藝實例分析,證明了滾剃工藝具有可行性,并且剃齒控制是關鍵。只有將兩者緊密地結合起來,滾剃工藝推廣才能得以實施,“滾剃磨”工藝改為“滾剃”工藝可以大大降低產品的磨齒加工時間,縮短產品的制造周期,經濟效益顯著。