隨著汽車行業的不斷發展,汽車已經成為人們日常生活中常用的交通工具,隨著人們對汽車乘坐舒適度及環保要求的不斷提高,汽車往更加智能化和環保的方向發展。變速箱的振動問題對汽車的整體性能有較大影響,隨著汽車變速箱的不斷集成化、功能多樣化及傳動功率不斷增大,汽車變速箱的噪音問題受到了越來越多的關注。變速箱的振動噪聲主要來自于齒輪、齒輪箱、齒輪軸及軸承之間的配合誤差及加工精度,控制變速箱的振動的有效方法是控制齒輪傳動系統的振動噪聲,也有利于提高齒輪的使用壽命及汽車的市場競爭力。
2 齒輪傳動系統振動噪聲問題及分析
2.1 齒輪傳動系統振動原因
汽車變速箱的主要功能是根據駕駛環境及路況需要調整齒輪系統傳動比,使汽車能順利通過特定路面或在各種環境中行駛,汽車齒輪變速箱主要包括變速傳動機構(傳遞速度和扭距)及變速操縱機構。在汽車行駛的過程中,變速箱齒輪嚙合狀態隨時間在不停的發生變化,屬于多軸多層次的動態振動的系統。
齒輪傳動系統零部件并非剛體,各種材料在屈服極限范圍內都具有一定的彈性,受到動態激勵時齒輪傳動系統會產生動態響應引起振動。主要包括齒輪嚙合外部激勵和齒輪副內部激勵。外部激勵形成的主要因素有發動機輸出扭矩及轉速波動、齒輪偏心、齒輪不符合動平衡要求、離合器的非線性及滾動軸承的時變剛度等。內部激勵是由于輪齒動態嚙合力引起,主要因素有齒輪誤差、輪齒的受載變形、輪齒嚙合對數的變化等。
3 變速箱齒輪修形
汽車行駛過程中,由于加工誤差和彈性變形等因素,汽車變速器齒輪嚙入和嚙出的時候偏離標準嚙合線引起沖撞和干擾,引發變速箱抖振,如果與外部結構之間發生共振,將產生較大的噪聲,針對這種類型的振動,單純的依靠加工工藝或安裝技術,并不能達到較好的成效,還會造成齒輪加工成本及變速箱制造成本提高。因此,齒輪修形技術在解決嚙合沖擊引起的汽車噪聲問題中具有重要的作用,利用齒輪修形技術可有效消除幾何干涉發生時的載荷變化,使嚙合過程載荷平均分布,降低嚙合沖擊,提高齒輪強度及齒輪運行的穩定性能。利用傳動系統仿真分析軟件可方便地得到變速箱振動噪音的數據,得到最佳修形方法,便于對傳統系統進行優化設計。
3.1 齒輪修形原理
圓柱齒輪嚙合過程中單齒嚙合與雙齒嚙合交替進行,輪齒受到的接觸載荷是周期性變化的。單齒嚙合與雙齒嚙合交替時,會引起齒輪的載荷明顯的突變。傳動系統零部件制造過程中必然存在誤差,標準的漸開線齒輪在進入嚙合及嚙出時會發生幾何干涉,另外,材料性質決定齒輪在受力時存在彈性變形,這會導致主動輪齒輪相對從動齒輪發生相對轉動,引起附加的彈性變形,產生嚙合沖擊。
3.2 齒形修形方法
齒輪形修形量與輪齒嚙合時產生的變形量和加工誤差有關,齒輪生產企業都有對應的計算方法及標準,在選擇修形曲線時應結合經驗及修行工藝等因素,遵循以下原則:
①修形后的齒輪副在嚙合時,輪齒載荷應該平滑變化 ;
②修形后的齒輪嚙合過程中有抵抗非額定載荷引起的沖擊及噪聲的能力 ;
③修形曲線要符合現有的加工工藝,滿足實際工況要求。
齒形修形主要包括齒頂修緣(去除齒輪頂部的材料)和齒根修形(去除齒根相近部位的材料)。齒形修形時可同時對主動輪及從動輪齒輪采用修形,也可選其中便于修形的齒輪進行修形處理。由于齒輪根部修形會降低齒輪的強度,所以一般同時對兩個齒輪分別進行修形處理。在齒頂圓直徑處修整的過程中,嚴格控制頂部倒角,以免降低齒輪嚙合重合度。
3.2.1 修形量
齒輪修形的關鍵位置是齒頂或齒根,這些區域的修行量需要精確計算,

其中:δi - 齒輪在嚙入、嚙出位置產生的最大干涉量(由誤差引起),mm;
xmax- 齒輪嚙入產生的最大綜合變形量(標準漸開線齒輪),mm
式(1)中 xmax 的計算公式為:
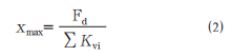
其中:Fd- 齒輪的法向嚙合力,N;
Kvi- 嚙合齒對總嚙合綜合剛度,N/m;
由公式(2)可知,最大綜合變形量與嚙合力成正比,與綜合剛度反比,當嚙合力一定時,在輪齒嚙入或嚙出位置時∑Kvi最小,xmax 有最大值,當齒輪重合度小于 2 時,

式中:Kv1- 齒對在嚙合位置 1 時的綜合剛度,N/m;
Kv2- 齒對在嚙合位置 2 時的綜合剛度, N/m;
當齒輪重合度小于 2 時 Kv1、Kv2 可按下式求得:

其中:Kz- 主動輪在嚙合位 i(i=1,2)處的剛度,N/m;
Kc- 從動輪在嚙合位置 i(i=1,2)處的剛度,N/m;
Kpv- 由接觸變形引起的剛度,N/m;n
式⑷中 Kz、Kc 及 Kpv 可按下式計算:

其中:Fi - 輪齒在 i 處嚙合點的法向嚙合力,N;
δ∑i - 嚙合點處沿嚙合線方向的綜合變形量,mm。
3.2.2 修形長度與修形曲線
修形長度 L 的公式為:

其中:Z- 嚙合線長度,mm;
Pb- 基節長度,mm。
修形曲線 Δ 計算公式為:

其中:Δk- 最大修形量,mm;
L- 測量的嚙合線上界點到嚙合終點或始點的長度,mm;
x- 嚙合位置的相對坐標 ;
b- 冪指數,b=1 時修形曲線為直線, b=2 的修形曲線為拋物線
3.2.3 鼓形齒的修整
汽車變速箱運行過程中,內部傳動系統齒輪和軸會發生微小的彈性變形,變速箱體也因受力變形,在加工過程中,齒輪、軸、軸承、箱體等零部件會出現加工誤差和測量誤差,這些因素有可能造成齒端突然接觸,引起傳動系統沖擊,因此,可通過鼓形齒的方法進行齒向修整,提高齒輪傳動精度。鼓形齒的修整需要選取合適的鼓形量(0.01~ 0.15mm),鼓形量的選取要結合變速箱實際工況及傳動系統零部件的材料,可通過多次試驗進行選取。
4 結論
汽車變速箱傳動系統穩定性與齒輪的使用壽命及傳動效率有直接關系,隨著汽車行業的不斷發展,變速箱齒輪嚴重磨損或輪齒折斷這些破壞現象已經很少發生,齒輪強度優化的方向是齒輪的修形處理,齒輪優化設計的過程中可利用仿真軟件得到有效的數據。參考這些數據,優化齒輪結構形式,提高齒輪精度,降低變速箱噪音, 提高傳動效率。