在蝸桿砂輪磨削出的齒輪表面經常會出現明暗條紋狀的周期性規律紋路,此紋路觸摸起來凹凸不平,通常這種紋路被認為是磨削加工過程中振動過大而形成的,所以被稱為振紋。齒面振紋的存在會使齒輪嚙合時載荷無法平穩傳遞而產生振動,因此有振紋的齒輪工作中會經常出現嘯叫等噪聲,此嘯叫噪聲在新能源汽車高速高扭矩狀態下尤為明顯,因為新能源汽車不存在內燃發動機聲音的遮蓋,會使零部件噪聲更加突出。作為汽車傳動系統重要部件,齒輪的質量對提高車輛 NVH 性能和改善乘坐舒適性有重要意義。這種振紋還會嚴重影響齒面的接觸質量,齒輪不正確嚙合會使齒面局部過載,局部齒面嚴重磨損,使用壽命縮短,甚至造成輪齒斷裂。
磨床在加工過程中振動過大會降低各磨床部件的使用壽命,如主軸振動過大會使軸承的受力不均勻,進而導致應力集中且降低其使用壽命,磨床振動的同時還會產生噪聲污染,加工出的工件表面質量也會進一步下降。作為齒輪加工的最后一道工序,磨齒對齒輪的表面形貌具有重大影響。作為評價齒面質量的重要指標之一,齒面粗糙度對齒輪的接觸疲勞、耐磨性和傳動質量均有重要影響。
蝸桿砂輪磨齒因為高效率、低成本、磨削性能與質量穩定等優點,目前被大量應用于中小模數齒輪的磨削加工中,故新能源汽車小模數齒輪多采用此方法加工。但是蝸桿砂輪磨削加工后的齒輪表面微觀質量卻時常出現不合格的情況,特別是不合理的磨齒工藝參數設置容易在齒輪表面產生振紋或者粗糙度不達標??赏ㄟ^工藝參數優化來實現加工目標,關于工藝參數優化模型的建立與求解方法,陳鵬等以自動化加工效率,齒輪單件成本為目標,工件材料、刀具涂層及切削速度、進給量等因素為變量,建立了一種齒輪高速干式滾切工藝參數優化模型,曹衛東等針對少量歷史加工案例支撐下的工藝參數優化問題,提出一種融合支持向量回歸和多目標蜻蜓算法的高速滾齒工藝參數優化方法。李聰波等以不同刀具磨損狀態下的工藝參數為優化變量,建立了考慮刀具磨損的數控車削批量加工工藝參數節能優化模型,并采用多目標模擬退火算法進行優化求解。WU 等建立了效率-成本-精度三目標模型的尋優問題,提出了一種具有自適應進化參數的多目標融合進化算法。KHARKA 等采用神經網絡與實數編碼遺傳算法對齒輪制造工藝進行參數優化,以同時最小化微幾何偏差和表面粗糙度。SHARMA 等采用可取性函數分析方法對刀具側面磨損和表面粗糙度進行并行優化,得到了多響應的最優參數組合。
現有研究缺乏工藝參數對磨齒加工中振動的影響的探索與實驗。本文以蝸桿砂輪磨削某型新能源車用斜齒輪為實驗基礎,采用正交設計實驗方案,探究了磨齒加工中不同工藝參數對磨齒加工中振動大小以及齒輪表面粗糙度的影響。然后基于實驗數據建立了工藝參數與振動、粗糙度的回歸預測模型,分析了各個參數對振動和粗糙度的影響及原因。最后構建以同時減小加工振動、齒面粗糙度為目標的多目標優化模型,采用遺傳算法對加工參數優化,得到了加工振動小、粗糙度小的工藝參數。
一、磨削實驗設計
實驗
本實驗在中國重慶機床有限責任公司生產的 YW7232CNC 型數控蝸桿砂輪磨齒機上進行,磨削砂輪為鄭州宏拓精密工具有限責任公司生產的蝸桿磨 CA 砂輪,砂輪的磨料是 SG 磨料和白剛玉輔料,其中 SG 磨料占 50%,其余是輔料;砂輪其他基本參數見表 1。實驗齒輪為某型新能源車用斜齒輪,材料為 20CrMnTiH,斜齒輪基本參數見表 2,材料力學性能見表 3。
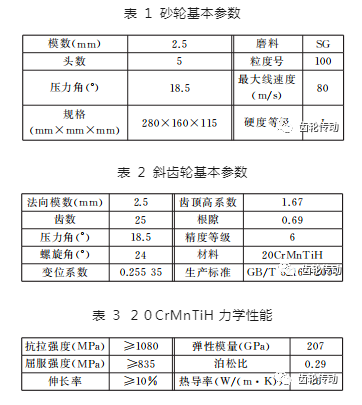
信號采集設備有 PCB 品牌振動加傳感 352C34、PC 信號調理器 480 C02 PCB 低噪聲線纜 2003D20、HIOKI 品牌信號采集記錄儀 8861-50?,F場實驗設備布置安裝與信號采集設備如圖 1 所示。
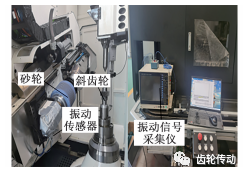
圖 1 實驗設備布置及信號采集儀器
實驗方法設計
對表面質量影響較大的因素有磨削工藝參數 (砂輪線速度、砂輪軸向進速度、砂輪徑向進給量)、磨削加工運動軌跡、砂輪特性與形貌、砂輪是否磨損與修整、磨削液、工件材料、工藝系統的剛度及其動態特性等。磨齒作為本斜齒輪加工的最后一道加工工序,工藝參數設置的重點是要保證斜齒輪的表面加工質量。根據控制變量原則,在機床、冷卻潤滑液、加工工件、砂輪等條件不變的情況下變更工藝參數,采用三因素三水平的正交設計實驗方法探究工藝參數對斜齒輪表面質量和加工中振動的影響。根據此型號斜齒輪實際加工中推薦的磨削參數范圍獲得實驗組表格,見表 4。
表 4 正交設計實驗
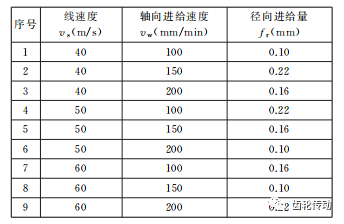
振動信號設備設置振動采樣頻率為 10 kHz,在 YW7232CNC 數控磨齒機上根據表 4 中不同組的工藝參數設置對斜齒輪進行磨削,在每一件斜齒輪開始精加工后按下信號存儲記錄儀 8861-50 上的開始按鈕采集振動信號。采用 KEYENCE 超景深三維立體顯微鏡 VHX 系列測量加工好的齒輪齒面粗糙度。
二、振動粗糙度結果分析與模型的建立
實驗數據處理與分析
采集到的振動加速度信號如圖 2 所示。在振動信號采集過程中發現磨齒精加工過程中的振動遠遠大于滾齒粗加工時的振動。對測得的磨齒振動數據進行分析處理,選取均方根值(root mean square,RMS)作為特征值進行振動分析,振動均方根值的物理意義是振動信號的平均強度大小,RMS 值按照下式計算:

式中,x i 為分析采樣數據;n 為分析采樣數據個數。
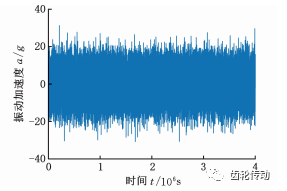
圖 2 振動信號
表面粗糙度是加工去除材料時零件表面產生的不平整度,主要的評定參數有輪廓算數平均偏差 Ra 、輪廓最大高度 Ry 等。因為 Ra 的概念更為直觀,能夠全面地表征零件加工表面微小峰谷的高低以及細密程度,是國內外使用最廣泛的表面粗糙度評定參數,故本文采用 Ra 對磨削表面粗糙度進行評估。
按照表 4 的正交設計方案完成 9 組實驗,并按照上述方法對測得的數據進行處理,得到每組實驗的齒面粗糙度和振動均方根值,詳細數據見表 5。
表 5 齒面粗糙度及振動實驗結果
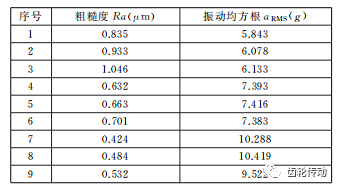
振動模型的建立
振動均方根值回歸方程:用得到的振動均方根值與工藝參數值進行多元二次回歸,得到振動回歸模型方程如下:

式中,f1 為振動均方根值;x1 、x2 、x3分別為砂輪線速度、砂輪沿齒輪軸向進給速度和徑向進給量。
表 6 中,對比振動模型預測的振動均方根值與實際測得的振動均方根值,模型預測的數值十分接近實際測得的值。
表 6 振動實驗數據與模型擬合數據對比
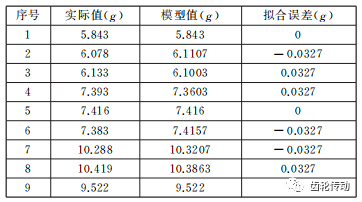
決定系數 R2 (coefficient of determination) 是反映模型擬合優度的重要統計量,常用于評價回歸模型優劣程度。R2的取值范圍為 0~1。R2 的值越大,越接近 1,說明回歸模型對真實值的擬合程度越好;反之,R2 的值越小,說明回歸模型對真實值的擬合程度越差。本振動回歸模型的決定系數 R2 =0.99975,可見此回歸模型擬合效果十分理想。
工藝參數單因素對振動的影響:將3個工藝參數自變量范圍都進行歸一化處理,得到3個工藝參數單因素與因變量振動均方根值之間的關系,如圖 3 所示.

圖 3 工藝參數與振動的關系
由圖 3 知,振動均方根值隨著砂輪線速度的增大而快速增大,成正相關。在砂輪線速度從 40 m/s 變化到 60 m/s 的過程中,振動均方根的值從5.84g 變化為 9.81g ,砂輪線速度在 3 個加工參數因素之中對振動的影響最大、最明顯。原因是砂輪制造過程中磨粒分布的不均勻、氣孔的存在以及磨削加工過程中的磨損造成表面不均勻和切削液的附加等因素,在砂輪旋轉的過程中會產生一個動不平衡量,砂輪在高轉速下的動不平衡會更加明顯,砂輪及其軸系高轉速下的動不平衡是產生磨床振動的最主要來源。滾齒的轉速范圍通常在 5 00 ~ 1000 r/min,振動加速度范圍通常在-10g ~10g。磨齒的轉速范圍通常在 2000~ 6000 r/min,振動加速度范圍通常在-40g~40g,因此,磨齒的振動比滾齒的振動明顯大很多。
砂輪軸向進給速度與振動均方根值關系也成正相關,但是隨著軸向進給速度的增大,振動均方根值的增速變慢,到達最大值后數值平穩波動。在砂輪軸向進給速度從 1 00 mm/min 變化到 200 mm/min 的過程中,振動均方根的值從 5.84g 變化為 6.85g,軸向進給速度在三個加工參數因素中對振動的影響僅次于砂輪線速度。這是由于砂輪軸向進給速度過大會造成加工工件及機床刀具主軸和工件裝夾芯軸等部件剛度和穩定性不足,從而產生振動。
砂輪徑向進給量對振動均方根值的影響最小,在砂輪徑向進給量從 0.01 mm 變化到 0.22 mm 的過程中,振動均方根的值僅僅從 5.84g 增加到 6.04g,對振動大小幾乎不產生影響。
粗糙度模型的建立
粗糙度回歸模型:同理,用齒面粗糙度值與工藝參數進行多元二次回歸,得到粗糙度回歸模型方程如下:

式中,f2 為粗糙度值。
對比粗糙度模型預測的粗糙度值與實際測得的粗糙度值,模型預測的數值十分接近實際測得的值,且決定系數 R2=0.994 82。對比結果如表 7 所示。
表 7 齒面粗糙度實驗數據與模型擬合數據對比
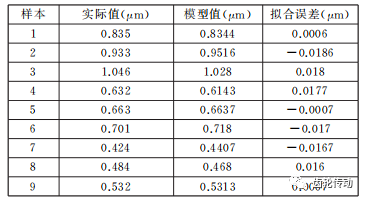
工藝參數單因素對粗糙度的影響:同樣歸一化后,得到 3 個工藝參數單因素與粗糙度之間的關系,如圖 4 所示??梢姶植诙戎惦S著砂輪線速度的增大而減小,在砂輪線速度從40m/s 變化到60 m/s 的過程中,粗糙度值從 0.85 μm減小到 0.43 μm,這是因為砂輪線速度的增加會使單位時間內通過磨削區的磨粒數量變多,單顆磨粒未變形切屑厚度減小且工件表面上切痕深度變淺,有利于切屑的形成,縮短了磨粒切刃的單次磨削時間,降低了磨粒去除材料后在加工表面留下的隆起高度,最終導致齒面粗糙度減小
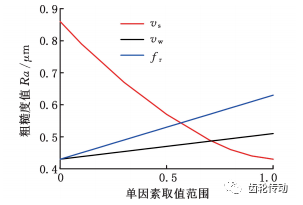
圖 4 工藝參數與粗糙度的關系
粗糙度值隨著軸向進給速度的增大而增大。這是由于軸向進給速度的增加會導致單位時間內磨削齒面的有效磨粒數目減少,使得單位面積齒面上形成的磨削殘留高度增大,由此齒面粗糙度值增大。
粗糙度值隨著砂輪徑向進給量的增大而增大。這是因為徑向進給量的增加會使單顆磨粒的最大磨削厚度增大,磨削力也增大,導致磨削表面變形程度增加,由塑性變形引起的凸起高度增大,齒面粗糙度值也會增加。但徑向進給量的改變對齒面粗糙度的影響與其他兩個工藝參數相比并不是很明顯,這是因為在實際磨削過程中磨削用量是緩慢分次進給的,不是一次以徑向進給量進行磨削。
三、綜合振動與粗糙度優化模型的建立與求解
遺傳算法原理
遺傳算法(genetic algorithm,GA)的是模擬生物進化過程的自然選擇和遺傳學機理計算模型,是以一種群體中的所有個體為對象,并利用隨機化技術指導對一個被編碼的參數空間進行高效搜索最優解的方法。遺傳算法的基本運算過程如下。
(1)初始化。設置進化代數計數器 t ← 0,最大遺傳代數 T,隨機生成 N 個個體作為初始群體 G(0)。
(2)個體評價。計算群體 G(t)中各個個體的適應度,適應度是用來判斷群體中的個體的優劣程度的指標,是根據目標函數來進行評估的。
(3)選擇運算。群體進行選擇運算,目的是將優化的個體遺傳到下一代或通過配對交叉產生新的個體再遺傳到下一代。
(4)交叉運算。群體進行交叉運算,是指將兩個父代個體的部分結構替換重組而生成新個體。交叉使遺傳算法的搜索能力大大提高,在遺傳算法中起核心作用。
(5)變異運算。群體進行變異運算,對個體串的某些基因座上的基因值作變動。變異運算可以使遺傳算法具有局部隨機搜索能力,加速了向最優解收斂的速度,維持了群體的多樣性,防止了未成熟收斂現象的出現。
(6)群體 G(t) 經過選擇、交叉、變異運算之后得到下一代群體 G(t+1)。
(7)終止條件判斷。若 t=T,則以進化過程中所得到的具有最大適應度個體作為最優解輸出,終止計算。遺傳優化算法流程如圖 5 所示。
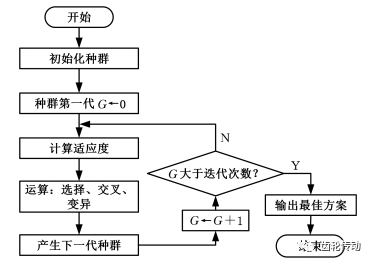
圖 5 遺傳優化算法流程
優化模型的建立
為保證在使用蝸桿砂輪磨齒機加工新能源汽車用斜齒輪時不產生振紋,需要在齒輪表面粗糙度滿足加工要求的前提下盡可能地減小振動。根據此特點要求進行多目標工藝參數優化,為將二維多目標問題降低為一維優化問題,采用線性加權和法的評價函數方法,按各目標的重要程度賦予其相對應的權系數,然后對其進行線性組合并進行最小值尋優:

式中,W1、W2分別為振動與粗糙度對應的權重系數,W1,W2∈ (0,1),且 W1+W2=1。
為了使數據處理更加方便,需要對目標進行歸一化處理,將數據映射到 0 ~ 1 范圍之內,本文采用線性歸一化,線性歸一化表達式為

則本文優化目標表達式變化為
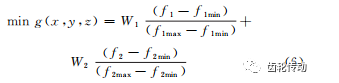
約束條件如下:
(1)砂輪線速度約束。為防止砂輪加工時破裂,保障加工過程中的安全性,砂輪線速度不能超過砂輪上標識的最大安全使用速度;同時為保證齒輪表面的粗糙度符合使用要求,參考本齒輪現場實際生產參數設置經驗,砂輪線速度不能設置過低。因此,砂輪線速度的取值范圍設置為 35m/s ≤ vs ≤ 70m/s。
(2)砂輪軸向進給速度約束。軸向進給速度越小,加工齒輪的時間越長,為保證較高的齒輪磨削效率,軸向進給速度不能設置過低。為防止砂輪磨損速率過快、齒輪表面質量下降,軸向進給速度也不能設置過高。因此,砂輪軸向進給速度的取值范圍設置為 75 mm/min ≤vw ≤ 225 mm/min。
(3)砂輪徑向進給量約束。磨削熱隨著徑向進給的增大而增大,為防止產生的大量磨削熱燒傷齒面表面,同時考慮到加工次數與效率,砂輪徑向進給量取值范圍設置為 0.04mm≤ fr≤0.28mm.
綜上,聯立優化目標函數與約束條件,建立了以減小齒輪加工過程中振動大小、同時提高磨齒表面加工質量為目標的多目標優化模型:
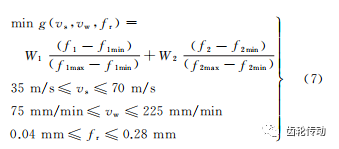
式中,f1max 、f1min 分別為振動均方根值的最大值和最小值;f2max 、f 2min 分別為粗糙度值的最大值和最小值。
優化結果
遺傳優化算法的參數設置:種群大小100,最大遺傳代數120,交叉概率0.7,變異概率0.02;考慮加工振動與齒輪表面粗糙度,選擇振動權重系數W1=0.4、粗糙度權重系數 W2 =0.6 進行優化求解,進化過程如圖 6 所示.
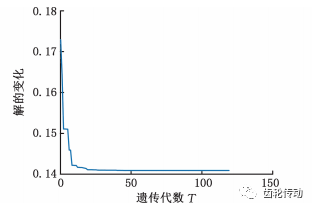
圖 6 遺傳進化過程
現有實際加工參數結果和優化后參數加工結果的對比見表 8??芍褂猛瑫r考慮振動與粗糙度的優化后參數加工時相比實際加工時振動均方根值減小了 3.772g,優化率高達 35.81%;加工后齒輪齒面粗糙度降低了0.017 μm,優化率為3.51%。綜上所述,本文方法可以在保持穩定的粗糙度精度的同時,大大減小了振動,從而有效防止振紋的產生,提高了機床的使用壽命。
表 8 優化結果對比
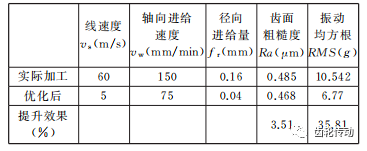
四、結論
(1)針對蝸桿砂輪磨齒機加工新能源汽車斜齒輪時出現振紋的問題,通過正交設計實驗建立了加工振動及齒面粗糙度預測模型,并通過與實驗數據比較,證明兩種模型擬合效果良好。
(2)由兩模型可得,振動的大小隨著砂輪線速度的增大而快速增大,隨著軸向進給速度的增大而增大。徑向進給量對振動大小的影響較小。齒面粗糙度值隨著砂輪線速度的增大而減小,隨著軸向進給速度與徑向進給量的增大而增大。
(3)建立了以最小振動和最小粗糙度值為加工目標的優化數學模型,與優化前相比,用優化后的工藝參數加工可減小35.81%的振動,粗糙度優化率為 3.51%。本文方法可有效防止振紋的產生,提高了機床的使用壽命。
參考文獻略.