直升機減速器中的齒輪對減速器的性能有著至關重要的影響,它起到轉換直升機發動機所輸出功率的功能,并為中樞受力構件直接承受旋翼與機體之間產生的全部作用力和力矩。因此要求減速器中的齒輪承載能力高、壽命長、可靠性好、干運轉能力強,可以在高溫、高壓、高轉速的工況下穩定運行。對齒輪進行倒角處理可以解決齒輪沿齒長方向的尖角、改善齒輪換擋力、降低齒輪傳動產生的噪聲和沖擊力,由此可以避免換擋過程中齒輪間的沖擊打齒,實現平順地嚙合以及減少齒廓面應力集中,從而有效提高齒輪的性能、使用壽命及可靠性。直升機減速器中的弧齒錐齒輪具有硬度高、齒廓形狀復雜的特點,傳統的手工倒角對工人的技術要求很高且工作環境惡劣、勞動強度大、加工效率低、一致性差,使用倒角機倒角又面臨成本高、適應性差的問題。對齒輪采用機器人倒角磨削加工,可以提高成品率、一致性以及加工效率,保證加工的質量,降低成本,提高復雜曲線加工的精度。目前國內外對齒輪、葉片、潔具等形狀復雜的工件均開展了機器人磨削加工的研究。本機器人 磨削系統將對某型弧齒錐齒輪進行倒角加工,最終加工出 C0.5~C0.75 mm 的倒角加工面。
一、機器人倒角磨削系統構成
機器人倒角磨削系統如圖 1 所示,該系統由機器人系統、浮動氣主軸、自動回轉臺、工件等構成。機器人為 ABB 公司生產的 IRB4600 六自由度關節臂機器人,工作范圍為 2.05 m,最大負載為 60 kg。浮動氣主軸為瑞士 Amtru 公司生產的 FB-CUT110,該氣主軸具有徑向浮動功能,可根據齒輪輪廓曲線曲率的變化情況自行進行浮動補償,浮動力最高可達 25 N,最高轉速可達 19 000 r/min。浮動氣主軸安裝在機器人末端,齒輪安裝在回轉臺上,機器人與回轉臺聯動,通過回轉臺的旋轉實現每個齒輪齒廓的倒角加工,從而完成自動化倒角。
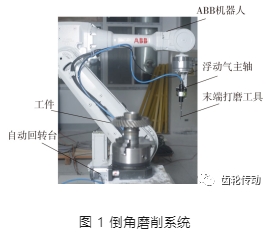
二、機器人磨削倒角工藝流程
倒角工藝流程:圖 2 為弧齒錐齒輪倒角的工藝流程。倒角系統的工具、工件標定和加工路徑離線編程是倒角加工中的重要環節。
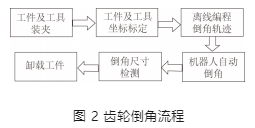
工具坐標系的標定與定義:TCP( tool center point) 即機器人工具中心點,通過機器人內置指令 MToolTCPCalibp1,p2,p3,p4,tool1,max_err, mean_err; 來計算 TCP,其中 p1、p2、p3、p4 為機器人示教時 4 個點的 jointtarget( 6 個軸坐標值) ,計算結果賦值到 tool1 的坐標系。在完成四點示教后,四點構成一個球面,球心即為當前 TCP 所在 wobj0 下的坐標值 xyz,通過獲取球心坐標來計算 TCP。
B= AX (1)
式中:A 為機器人 tool0 表示的當前位置 pose( xyzq1-q4) ; X 為工具 tcp pose( xyz,q1-q4) ; B 為機器人當前工具表示的當前位置 pose( xyz,q1-q4) ,所以得到 X= A-1 B。由此得到在 Robot Studio 中的計算程序(圖 3) 。
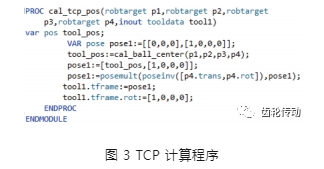
在本次實驗中使用特種刀柄裝夾金剛石磨片為打磨工具。由于打磨工具形狀的特殊無法直接用四點法進行標定,因此使用相同長度的尖針來進行替代,此時 TCP 點為打磨工具端面中心( 圖 4) 。
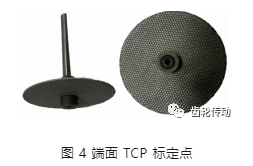
加工軌跡離線編程:倒角加工路徑為機器人在倒角過程中所有姿態以及相應目標點的集合。機器人通過連續不斷地以特定的姿態到達每個目標點來實現倒角加工的過程。倒角系統使用 ABB 公司的離線編程軟件 Robot Studio 生成倒角加工路徑。倒角加工路徑產生方法如下: 1) 在仿真軟件 Robot Studio 中直接導入齒輪的三維模型; 2) 通過四點法標定出工具坐標系,通過三點法標定出工件坐標系,平移齒輪的三維模型使其與實際的齒輪坐標相重合; 3) 在工件坐標系中生成倒角路徑; 4) 優化路徑,進行軌跡規劃和離線仿真避開機器人的奇異點以及倒角機構與工件的干涉區域,刀具為順時針旋轉,在規劃路徑時刀具由齒根向外運行。經過實驗對比效果好于刀具由外向齒根運行,如圖 5 所示。
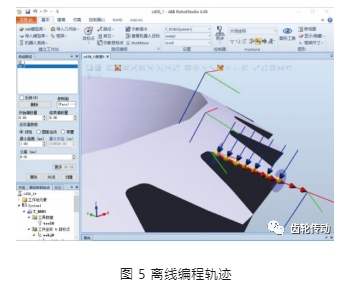
浮動補償接觸力:
1) 浮動補償力優點
采用浮動補償加工的方法,能較好地適應齒輪齒廓邊緣曲線形狀變化,滿足齒輪齒廓邊緣的結構特點,保證齒輪的相關尺寸精度和表面質量,確保倒角過程中精確地控制切削量,能很好地跟蹤齒廓曲線以補償工件的自身變形,還能有效防止倒角過程對齒輪基體造成損傷。當倒角軌跡不規則或者與理論型線有差異時,浮動阻尼可根據被加工齒輪齒廓的實際線型進行自動補償或退讓以達到最佳的倒角效果,其最大補償與退讓量可達到±5 mm。浮動倒角機構設計有精密的切削力控制系統,能通過壓力控制使末端加工磨片緊密貼合被加工齒輪的齒廓曲線,隨加工曲線的形變產生相應的彈性變形,實現倒角齒輪齒廓曲線的自動跟蹤。通過控制浮動阻尼的彈性變形以及相應力矩的大小來調整相應的接觸壓力進而實現磨削力的調節。
2) 補償力與磨削力性能分析
在倒角加工時,為保證倒角加工面的尺寸均勻一致,使用磨片的邊緣點與齒輪齒廓棱邊接觸,此時磨削方式近似于立式平面磨削。
將磨削力分解為 3 個相互垂直的分力: Fn 為法向磨削力、Ft 為切向磨削力、Fa 為軸向磨削力。將單個磨粒與工件之間的磨削力同樣分解為 3 個相互垂直的分力: 法相力 F'n、切向力 F't、軸向力 F'a。由此得到

式中: σ 為比磨削力,垂直于切削方向上的單位切屑面積所受的力; am 為平均切屑面積。
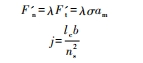
式中: lc 為接觸弧長; b 為接觸寬度; j 為同時進行磨削的磨粒刃數。由以上各式可以推導出:
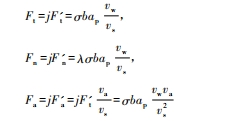
式中: vs 為磨片實際加工點的線速度; va 為 vs 軸向分量; vw 為工件速度; ap 為磨片軸向進給量。
當控制浮動阻尼進行壓緊,此時進給量 ap 增大,單位時間內工件的去除量增加,每個磨粒的切削厚度增加,磨削力增大。當磨片實際加工點的線速度 vs 增大時,單位時間內進行磨削的磨粒個數減少,磨粒的切削厚度減小,磨削力減小。
三、直升機減速器齒輪倒角實驗
試驗目的:使用本機器人倒角系統來對某公司所提供的某型直升機減速器齒輪進行倒角,以驗證本系統的性能。該齒輪的材料為合金鋼,齒廓倒角處硬度為 HRA82。
試驗步驟:按照圖 2 的加工流程圖進行試驗,詳細步驟如下:
對工具(浮動打磨頭) 和工件(齒輪) 坐標系進行標定。在 Robot Studio 中導入工件的三維模型以及 TCP 坐標,對齒輪進行離線編程生成齒輪倒角路徑。進行軌跡規劃和離線仿真,以避開機器人的奇異點以及倒角機構與工件的干涉區域,將離線編程軌跡導入到機器人中。在完成一個齒的加工后,裝夾齒輪的轉臺按照設定好的度數旋轉,按照相同的工藝步驟加工下一個齒。最后檢測倒角的尺寸以及表面質量是否滿足要求。
試驗結果:本試驗使用了接觸式 334006 型輪廓儀來測量倒角尺寸,為了保證數據的準確性以及齒輪中每個齒的加工一致性,在整個齒輪總計 31 個齒中隨機選擇 8 個齒進行檢測,每個齒分別在上、中、下 3 個部位測量尺寸,測量數據見表 1。

四、結語
1) 機器人倒角磨削系統對直升機減速器齒輪的倒角加工具有很強的適用性,本磨削倒角系統包含了機器人與離線編程、自動工裝回轉臺、磨削力補償等前沿方法,自動化程度高,可以使工人擺脫繁瑣的倒角加工,提高工作效率,提升我國制造業的智能化水平。
2) 通過對加工后的齒輪進行測量,測量結果表明齒與齒之間的尺寸一致性較高,齒輪齒廓處精度得到顯著提高,該系統的加工精度完全符合直升機減速器齒輪的加工要求。