鼓形齒接軸是傳動類關鍵產品,具有徑向、軸向和角向等軸線偏差補償能力,結構緊湊、回轉半徑小、承載能力大、傳動效率高、噪聲低等優點,廣泛應用于冶金、礦山、起重運輸等行業。滲碳淬火硬齒面內齒圈是其核心零件,滲碳淬火后硬度達到 57 ~ 62HRC,其窄空刀槽齒圈齒部無法磨齒,采用插齒刮削存在加工難度大、刀具磨損快、齒形精度難以保證的共性問題。近年來,雖針對內齒圈加工方式進行了部分改進,但一直缺乏系統的工藝性研究,內齒圈產品質量穩定性較差,某鋼廠使用的鼓形齒接軸在使用過程中出現鼓形齒齒面接觸異常,齒面壓潰,鼓形齒接軸使用壽命不滿足設計要求的情況。此次依托現有插齒設備,通過改進插齒刀刃磨方式、優化插齒刀設計、優化刮削工藝參數等手段,提升硬齒面內齒圈刮齒齒形精度,提高鼓形齒接軸整體質量。
一、內齒圈結構及技術要求
某型號鼓形齒接軸直齒內齒圈外徑∅380 mm,內徑∅280H8,空刀槽寬 25 mm,模數 8 mm,齒數 36,如圖 1 所示。
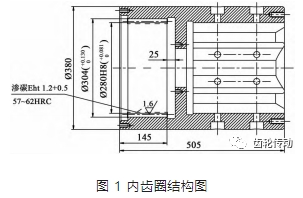
內齒圈的主要技術要求如下:
( 1) 內齒圈材料為 17Cr2Ni2Mo,抗拉強度≥ 1080 MPa,屈服強度≥785 MPa,具有較高的強度和韌性。
( 2) 內齒圈齒面需滲碳淬火處理,滲碳層硬度 57 ~ 62HRC,精加工后有效硬化層深 1.2 ~ 1.7 mm。
( 3) 齒面精加工精度為國標 7 級,齒面粗糙度為 Ra1.6 μm。內齒圈齒根圓為∅304H9,需與齒面同時刮削加工。
二、制造難點分析
綜合分析該內齒圈的結構和技術要求,其主要制造難點如下:
( 1) 內齒圈齒面滲碳淬火處理,滲碳層硬度 57 ~ 62HRC,滲碳淬火后齒面變形導致余量不均勻,插齒刮削異常困難,加工效率低,精度難以保證。
( 2) 常規硬質合金插齒刀刮削時前刀面刃口磨損很快,刀具容易崩刃,刮削齒形誤差較大。
( 3) 內齒圈左右齒面和齒根都有嚴格公差要求,需要三個面同時刮削,即插齒刀頂刃也要參與切削,故合理的切削參數設定是保證齒形精度的重點和難點。
三、影響齒形精度的主要因素
插齒刀前刀面刃磨精度
硬齒面插齒刀是采用抗沖擊性能良好的負前角結構并用硬質合金刀片制造而成的插齒刀,對于滲碳淬火硬齒面內齒圈 (齒部硬度 57 ~ 62HRC) 刮削性能良好。為了發揮硬齒面刮削過程高效輕快和斜角切削的優勢,硬質合金插齒刀前刀面頂刃結構采用負前角形式,以確保兩側面漸開線主切削刃有良好的負刃傾角。隨著插齒刀頂刃負前角的增大,刀齒后面的磨損也不斷減小。但是,只有插齒刀前刀面角度為零(也即平面) 時,兩側面漸開線切削刃投影形成的曲線才是理論正確的齒面漸開線。前刀面負前角越大,其抗崩刃能力越強,但齒面漸開線曲線精度誤差越大,所以要兼顧插齒刀的齒廓構形精度和刮削抗崩刃能力,前刀面角度一般設計為-5°。
硬齒面內齒圈刮削過程中,刀具刃口逐漸磨損不再鋒利,須對插齒刀 - 5°前刀面進行刃磨(見圖 2),刀具刃磨后能否保證刀具固有的參數和精度,尤其是前刀面斜向跳動誤差是否合格,對加工零件的齒形精度有至關重要的影響。
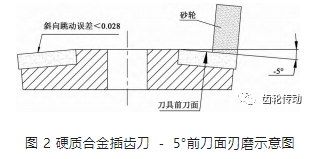
插齒刀可在萬能工具磨床上沿前刀面刃磨,也可在外圓磨床上刃磨。直齒插齒刀是用砂輪的外圓柱面刃磨。刃磨時,萬能夾頭應調整一個角度,其值為插齒刀的頂刃前角,使前刀面母線與砂輪外圓柱面母線平行。
插齒刀精度和耐磨性
插齒過程是插齒刀與零件按照展成原理進行的無間隙嚙合(切削) 運動,插齒刀的精度直接影響零件齒面漸開線齒廓構形精度,至關重要。內齒圈滲碳淬火后齒部硬度為 57 ~ 62HRC,硬度很高,常規硬質合金插齒刀切削過程中,刀具刃口極易磨損、翻邊和脫落(見圖 3) ,磨損后刀具刃口齒形誤差變大,導致切削加工的內齒齒形精度超差。
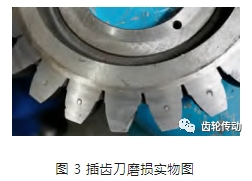
通過插齒刀磨損情況分析(如圖 4) ,硬質合金插齒刀的刀具耐磨損度與工件的齒面精度具有直接聯系,且刀具耐磨度越高,刀具齒廓保持度越好,加工后零件的齒面齒形精度越高。反之,刀具耐磨度越低,刀具刃口越容易磨損、翻邊,加工后零件的齒面齒形精度越差。
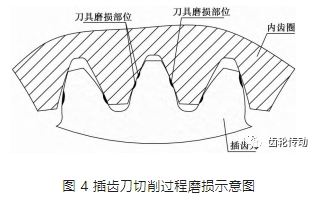
機床精度和刮削工藝參數
插齒機的性能和精度對硬齒面內齒圈刮齒的效果影響很大。實際生產中我們應盡量選擇剛性好高精度的插齒機,并適當減小傳動鏈間的反向間隙,目前國內插齒機生產廠家中沒有專門生產用于硬齒面內齒加工的刮齒專機。由于硬齒面內齒圈滲碳淬火后的精刮齒過程負荷不大、沖程次數不高,故我公司在現有的數控插齒機上進行硬齒面刮削加工。為提升機床精度,由公司設備部門對數控插齒機進行了維修保養,減小各運動部件之間的反向間隙,對機床主軸錐孔進行專業研磨提高錐孔精度,制作高精度的插齒刀接刀桿,確保刀具裝夾后整體跳動誤差小于 0.01 mm。
與常規的硬齒面內齒圈不同,鼓形齒接軸內齒圈兩齒面和齒根都有嚴格公差要求,需要三個面同時刮削,即插齒刀頂刃也要參與切削。故無法像硬齒面外齒輪那樣在滲碳前用帶凸角的留量滾刀提前將齒根挖根處理: 即精加工時只需加工兩齒面,齒根不用加工,減少刀具負荷。所以對于三面同時刮削的硬齒面內齒圈,刮削時要選擇好粗、半精和精插齒時的余量分配、刀具刃磨頻次、圓周進給量、主軸沖程次數、徑向進給量等切削參數,確保零件高效高精度加工,刀具磨損小齒廓保持度好,從而保證內齒齒形精度。
四、加工方案優化
改進插齒刀刃磨方式
公司之前采用一臺老式萬能工具磨床,工人憑經驗手動調整 - 5°修磨角度,前刀面斜向跳動誤差 0.2 mm,遠大于要求值 0.028 mm,插齒刀修磨精度很低。且該機床未配備冷卻水箱,采用干磨磨刀時熱量無法消除,硬質合金刀片極易產生磨削裂紋,進而產生剝落,導致刀具精度喪失,已嚴重影響到插齒加工質量和效率。
為提高插齒刀刃磨精度,對插齒刀刃磨方式進行改進。根據插齒刀磨削原理,制作一套組合工裝用于立式 MX2000 數控外圓磨床進行濕磨插齒刀。針對插齒特點,設計插齒刀裝夾刀桿孔為基準的裝夾工裝,工裝由底座、壓板、鎖緊螺母三部分組成(見圖 5) ,采用插齒刀內孔及端面定位、螺栓把合壓緊裝夾方式,插齒刀裝夾定位底面與底座裝夾基準面貼合。
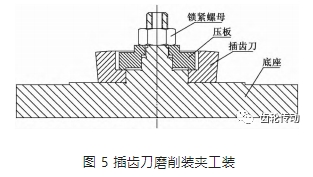
對 MX2000 數控立式磨床的右砂輪磨頭進行改造,將右磨頭角度調整為 5°,滿足插齒刀前刀面5°錐面的修磨要求(見圖6) 。然后利用組合工裝對插齒刀前刀面進行磨削試驗,編制數控磨削程序確保前刀面刃磨角度正確,砂輪吃刀量為 0.01 mm,走刀速度 20 mm/min。磨削后插齒刀前刀面斜向跳動誤差≤0.012 mm,粗糙度 Ra≤0.6 μm,同時將磨削完成的插齒刀送刀具廠家進行齒 輪檢測儀計量,檢測結果顯示采用該磨削方法磨削的插齒刀,齒部精度均合格,表觀質量良好無燒傷(見圖 7) 。
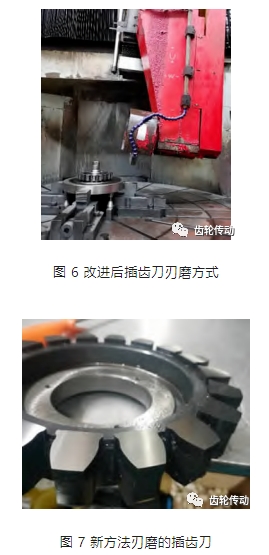
插齒刀改進優化
利用硬質合金插齒刀進行硬齒面刮齒,是滲碳淬火高硬度內齒圈齒部加工的高效加工方法,對于沒有加長小磨頭內磨齒專機的廠家更是不錯的加工方案。尤其是對于結構特殊如空刀槽很窄的內齒圈,無法對其進行齒面磨削加工,硬質合金插齒刀可發揮其獨到作用,解決這一加工瓶頸。目前常規使用的硬質合金插齒刀結構為前刀面是 -5°的圓錐面,刀具磨損鈍化后可以對 -5°前刀面進行重新刃磨。插齒刀齒頂后刀面也是圓錐面,其圓錐半角,即插齒刀頂刃后角通常取為 6°,而刀齒兩側面,即刀齒側后刀面均為漸開螺旋面,左側為右旋,右側為左旋。
隨著插齒刀前刀面徑向負前角的增大,隨之其切削刃抗崩刃能力增強,但漸開線齒廓構形精度卻急劇降低,因此,現有的硬質合金插齒刀前刀面通常采用不大于 -5°的負前角,這使其抗崩刃能力受到了限制。盡管如此,目前這種前刀面-5°負前角的設計結構,已經對其刀具側刃漸開線齒形精度造成一定限制,齒形精度無法進一步提高,故加工的硬齒面內齒圈也無法滿足 6 ~ 7 級精度要求。而且它在刮削大于或等于 60HRC 的滲碳淬火內齒圈時,其耐磨性與抗崩刃性能也有待進一步提高。
為解決目前常規硬質合金插齒刀的齒廓漸開線構形精度與采用合理切削角度之間的矛盾,以發揮刀具的最佳刮削性能,滿足加工高精度硬齒面內齒圈的要求,項目組與刀具廠家一起研究討論,提出一種抗崩刃能力更強、耐磨性和齒廓構形精度更高的硬質合金插齒刀優化方案。
方案中為減小刀具齒形誤差,通過對插齒刀分度圓壓力角進行修正,使刀具切削刃投影在分度圓處的切線和理論漸開線的切線重合,修正后的插齒刀刀刃水平投影與理論漸開線在分度圓處相切,將前刀面﹣5°負前角帶來的刀具齒廓漸開線構形誤差降低到最小。通過反復試驗研究,對硬質合金插齒刀刀片材質進行改進升級,采用耐磨性和抗沖擊性能更好的材料和熱處理方案,研制出新型 AA 級硬質合金插齒刀(見圖 8) 。
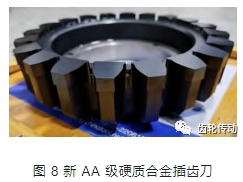
優化刮削工藝參數
滲碳淬火硬齒面內齒圈由于齒面硬度極高,熱處理后齒圈存在整體變形,導致各齒面余量不一致,且滲碳淬火噴砂后附著在齒面的噴砂層對刀具磨損影響較大,所以硬齒面內齒圈刮齒加工與軟齒面內齒圈插齒存在很大差異,需要對插齒刀具、滲碳前齒面余量、精加工齒面余量分配、磨刀頻次和刮齒參數進行優化設計,才能保證精刮齒后三坐標計量合格。
滲碳淬火前半精插齒時,考慮到滲碳淬火變形和漲大量,對內齒圈齒厚( 或量棒距 M 值) 進行相應的留量,以保證精刮齒時齒面有足夠的加工余量。由于圖紙要求精加工后有效硬化層深 1.2 ~ 1.7 mm,故熱處理前齒面留量要合適,不能偏大也不能偏小,偏小則無法消除熱處理變形,齒面將殘留黑皮; 偏大則齒面滲碳層刮削過多導致滲碳層深度減小,且導致加工量增加使插齒刀磨損加劇。根據公司相關技術標準和現場記錄的歷史數據,該內齒圈熱處理前的齒面精加工留量控制為單邊 0.6 mm,由于精加工齒根圓有嚴格公差要求,所以滲碳淬火前齒根按比例相應留量 1.2 mm。
限制插削速度的主要因素是被插齒輪的材料硬度,在保持切削參數相同的條件下,切削相同件數的同種齒輪,當被加工齒坯的硬度增加 10% ,刀具的磨損將增加 40% 。插削速度是以沖程次數和插削的行程長度來體現的。故在插削行程長度確定后,將切削速度換算成沖程次數,以用于插齒機的調整。切削速度按下面公式計算:
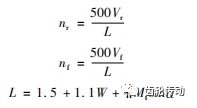
式中,nr 為粗插的沖程次數; nf 為精插的沖程次數; Vr 為粗切的切削速度(m/min) ; Vf 為精切的切削速度(m/min) ; L 為插削的行程長度(mm) ; W 為齒輪的齒面寬度(mm) ; Mt 為齒輪的端面模數; α 為齒輪分度圓螺旋角(°) 。
通過系列刮齒實驗,滲碳淬火硬齒面內齒圈插齒采用粗插齒—半精插齒—精插齒加工方案,優化后加工參數為:
(1) 粗插齒時先修正熱處理變形量,先不加工齒根。額定圓周進給量 0.35 mm/沖程,粗插齒時,適當增加圓周進給量可提高插齒效率。主軸沖程次數 25 ~ 30 次/min,徑向進給量 0.5 ~ 0.3 mm,隨加工沖程減少。
(2) 半精插齒時,兩齒面和齒根都要刮削,切削抗力加大,額定圓周進給量適當減小,控制為 0.30 mm/沖程,主軸沖程次數 20 ~ 25 次/min,徑向進給量 0.25 ~ 0.15 mm,隨加工沖程減少。
( 3) 精插齒時,額定圓周進給量 0.25 mm/沖程,主軸沖程次數 20 ~ 25 次/min,徑向進給量 0.1 ~ 0.15 mm,隨加工沖程減少,按余量設置。精插齒過程中,要密切觀察刀具磨損情況,增加插齒刀前刀面刃磨頻次,確保插齒刀刃口鋒利且齒廓正確。
五、方案實施及效果
滲碳淬火內齒圈安排在Y58數控插齒機進行刮齒加工(如圖 9) 。依據圖紙參數、刀具工裝號,選擇優化后的硬質合金插齒刀。刮削插齒刀需準備 3 把刀,1 號粗刀用于粗加工,因加工時刀具損傷較快,且齒面還有加工余量,可以選擇合金刀片有損傷的舊插齒刀加工; 2 號半精刀、3 號精刀都必需選擇完整的合金插齒刀。
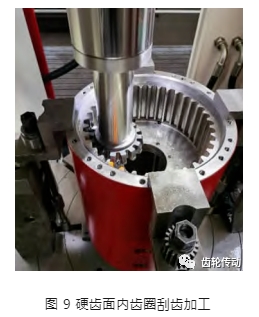
依據插齒參數和工藝留量,用內徑千分尺檢查齒部余量及變形量,找到余量最大的齒作為對刀基準齒。需要在圓周方向上均布選取不少于 6 處位置進行測量,并且需測量同一齒齒槽的上下兩處。設置粗插齒切削參數為: 沖程 25 次/min,進刀速度 0.05 mm/沖程,圓周進給率 0.35 mm/沖程,每刀吃刀量 0.3 mm,粗加工齒厚留量 0.4 mm。設置精插齒切削參數為: 沖程 20 次/min,進刀速度 0.03 mm/沖程,圓周進給率 0.25 mm/沖程,每刀吃刀量 0.1 ~ 0.15 mm。根據加工過程中測量齒根上下數據差值,差值較大就需要刃磨插齒刀,刃磨刀具在新改進的數控立磨上進行,保證插齒刀的刃磨精度和刃口鋒利。
加工完成的內齒圈通過三坐標計量齒形、齒向、齒距和徑向跳動誤差,精度完全達到圖紙要求的 7 級精度,三坐標齒形檢測數據見表 1。
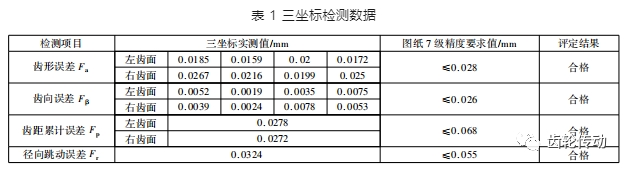
通過齒面涂抹紅丹粉,檢查內外齒嚙合接觸情況,齒面接觸印跡達到設計要求(如圖 10) 。
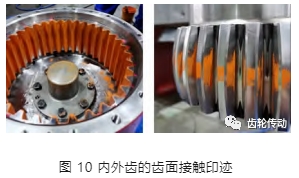
通過改進前后的三坐標數據對比,并利用箱線圖分析得出(如圖 11) : 刀具精度和耐磨性對齒形精度影響最大。改進前采用普通硬質合金插齒刀加工,齒形誤差在 0.05 ~ 0.08 mm 范圍波動,不滿足圖紙 7 級精度要求( Fa≤0.028) ; 改進后采用更加耐磨的 AA 級涂層插齒刀,齒形誤差達到圖紙 7 級精度要求。
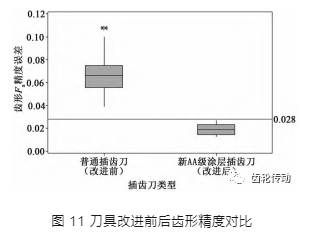
六、結論
通過滲碳淬火硬齒面內齒圈刮齒工藝研究,優化滲碳淬火硬齒面內齒圈刮齒工藝規范,固化加工方案,優化切屑參數,改進刀具刃磨方式,提升了硬齒面內齒圈的齒面加工精度,該項目研究獲得以下結論:
(1) 數控插齒機能實現 7 級及以上精度硬齒面內齒圈的高精度制造。該項目研究前,公司插齒機加工的內齒圈最高只能達到 8 級精度。該項目研究后其硬齒面內齒圈已達到國標 7 級,部分參數達到 6 級精度,該項目的成功研制為 7 級及以上精度硬齒面內齒圈插齒加工找到了解決途徑。
(2) 采用新開發的數控專用程序和濕磨工藝刃磨的插齒刀,前刀面斜向跳動誤差 ≤0.012 mm,粗糙度 Ra≤0.6 μm,使插齒刀刃磨后重新達到了原始出廠精度。
(3) 改進后的新型耐磨材料硬質合金插齒刀,加工時刀具磨損很小,切削 4 個圓周后仍然能保持較好的齒部輪廓度,切削輕快,節約了頻繁換刀刃磨時間,效率提升約 30% 。
(4) 精加工刮削時,最佳切削參數為: 沖程 20 次/min,圓周進給率 0.25 mm/沖程,每刀吃刀量 0.1 ~ 0.15 mm,最后一刀光刀前重新刃磨插齒刀,該方案能滿足公司其他項目模數 8,齒副長 200 mm 以內的各種硬齒面內齒圈的加工要求。
(5) 通過本項目研究發現,插齒刀的精度和耐磨性對硬齒面內齒圈齒形精度影響最大,硬質合金插齒刀的優化改進對硬齒面內齒圈齒形精度提升起決定性作用。