齒輪是一種傳遞運動和動力的機械零部件,是機械產品中重要的基礎元件,其廣泛應用于汽車車輛、電動工具、航天航空、各類機械設備等眾多主機行業。
齒輪是機器中質量最大、最復雜、最關鍵的零件之一,在很大程度上決定了所使用的機器和機構的性能。作為傳動系統的核心部件,傳動系統的質量往往由齒輪的精度決定。國家標準GB/T10095.1-2008和GB/T10095.2- 2008對漸開線圓柱齒輪的精度參數進行了明確的規定。對齒輪精度參數的精密測量是保證其互換性、連接強度、工作精度等性能的基本前提,因此實現齒輪精度參數的自動檢測對提高齒輪的傳動精度和可靠性具有非常重要的意義。
小模數齒輪是指模數小于等于1mm的齒輪,一般來說其外形尺寸也比較小,廣泛應用于精密機械、儀器儀表等精密傳動領域。傳統的綜合性齒輪測量儀器如CNC齒輪測量中心、三坐標測量機存在操作復雜、價格昂貴、維修難度大、適應性較差、動態性能不足、效率低下等問題,無法進行在線的應用。而專用的齒輪測量器具,例如公法線千分尺、游標測齒卡尺等都只能實現某一項精度參數的手工測量,測量效率和精度都受到很大限制。這兩類方法都屬于接觸式的離線測量方法,受到探頭尺寸的限制,它們無法伸入小模數齒輪的齒槽內,進而無法實現其精度參數的檢測。
進入新世紀以來,在制造業中信息化、智能化的發展趨勢越來越要求質量檢測技術具備較低的時延,能夠實現產品在位檢測。機器視覺影像測量技術正是這樣一種高效的檢測方法,它是一種融合了計算機圖形學、信息處理、光電子學和模式識別等科學為一體的現代檢測技術,具有非接觸、高速度、動態范圍大、信息量豐富、成本相對低廉等諸多優點,廣泛用于各種實時、在線、自動化的精密測量中。
機器視覺檢測技術作為一種高效的幾何量測量新技術,也非常適用于小模數圓柱直齒輪精度參數的測量。特別是智能制造大背景下,如何實現齒輪精度參數的自動化、非接觸、高精度檢測成為齒輪制造智能化的基礎性問題。本文將影像測量技術應用在小模數齒輪精度參數的自動化檢測上,搭建了一套小模數圓柱直齒輪精度參數測量實驗系統,對本文所述方法進行了實驗驗證。
一、齒輪精度參數檢測原理
機器視覺齒輪精度參數檢測系統的原理如圖1所示,它通過成像系統將被測物面成像至光電檢測單元(相機感光面),光電檢測單元將光信號轉換為電信號(電子圖片),并將其傳送至上位機。上位機獲得檢測圖像后,利用圖像處理軟件從檢測圖像中提取出所需的幾何特征,在根據成像系統的數學模型,計算出所關心的幾何量,從而實現被測產品幾何參數的測量。
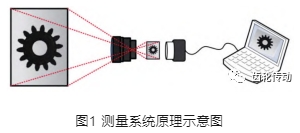
坐標轉換原理
為了建立測量模型,引入了4個坐標系:
1)世界坐標系Ow-XwYwZw,也稱為測量坐標系用于描述被測物體的空間位置;
2)相機坐標系Oc-XcYcZc,也是一個三維直角坐標系,原點位于鏡頭光心處,X、Y軸分別與相面的兩邊平行,Z 軸為鏡頭光軸,與像平面垂直;
3)像素坐標系O0-UV,一個二維直角坐標系,反映了相機CCD/CMOS芯片中像素的排列情況。原點位于圖像的左上角,U軸、V軸分別與像面的兩邊平行,其坐標值為整數,單位為像素;
4)像平面坐標系O-XY,又被成為圖像坐標系,是一個二維直角坐標系,其坐標軸的單位通常為毫米(mm),原點是相機光軸與相面的交點(稱為主點),即圖像的中心點,X軸、Y軸分別與U軸、V軸平行。可由像素坐標系經過平移和單位變換得到圖像坐標系。
機器視覺一般測量過程就是從獲得的檢測圖像中提取出特征點(或點族),經過一系列坐標變換得到世界坐標系下被測物體的特征點坐標,進而得到被測物體各項幾何參數。因此,機器視覺測量過程的關鍵是坐標系的轉換。對于單目視覺測量來說,為了方便計算,選定世界坐標系的X軸、Y軸分別與相機坐標系的X軸、Y軸平行,坐標原點則設計為成像系統光軸與被攝物平面的交點。因此,本文所述方法所涉及到4個坐標系的關系如圖2所示。
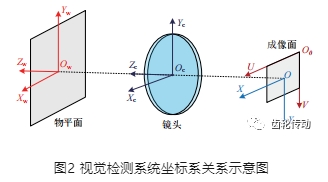
圖像坐標系與像素坐標系的關系為單位轉換和坐標平移的關系,設像素坐標系原點在像平面坐標系下的坐標為(u0,v0),每個像素點在圖像坐標系x軸、y軸方向的尺寸為dx和dy,且像點在像平面坐標系下的坐標為(x,y),于是可得到像點在像素坐標系下的坐標(u,v)的齊次坐標形式如式(1)所示:
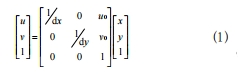
本文所設定的世界坐標系與相機坐標系的關系特殊,僅存在坐標的平移,設被測物面上某點的坐標為(xw,yw,0),其對應在相機坐標系下在坐標為(xc,yc,U)因此可得兩個坐標系的轉換關系為:
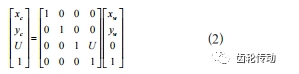
式(2)中,U為被測物面到鏡頭光心的距離,也即物距。
從相機坐標系到圖像坐標系的轉換就是3D坐標點到2D平面的透視映射。根據小孔成像模型和三角形相似定理可以得到兩個坐標系的轉換關系為:
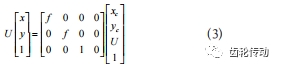
式(3)中,f為鏡頭的有效焦距,單位:mm。
聯合式(1)~式(3),最終整理可得像素坐標與世界坐標系的轉換關系:
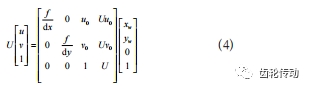
也即:
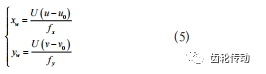
式(5)中,fx為U軸方向歸一化焦距,fx=f/dx;fy為V 軸方向歸一化焦距,fy=f/dy。
這樣就能將像素坐標系中所有的點轉化到被測物面坐標系,也即世界坐標系。單目視覺測量中,提取出來的特征點將其轉換到世界坐標系下,即可得到實際被測物體的幾何尺寸信息。
相機標定及圖像矯正
由相機獲取的圖像上每一點的亮度將反映空間物體表面某點反射光的強度,而該點在圖像上的位置則與空間物體相應點的幾何位置有關。這些位置的相互關系由相機成像幾何模型所決定。該模型的參數稱為相機參數,這些參數必須由實驗與計算來確定,實驗與計算的過程稱為相機標定。式(5)中的fx,fy,u0,v0均為本文相機標定過程中需要確定的內參數,物距U為外參數。
在理想情況下從相機坐標系轉換到圖像坐標系時,放大倍率是常數,但是在實際的光學系統中,透鏡的放大率會隨光束和主軸間所成角度改變而改變。由于透鏡制作和安裝存在不確定性,導致遠光軸區域的放大率與光軸附近的放大率差異較大時會導致平面內圖形的各部分與原物不成比例,這種現象就是圖像畸變,常見的圖像畸變又分為徑向畸變和切向畸變兩種。本文引用張正友標定法,利用標準棋盤格實現內參矩陣和徑向畸變、切向畸變參數的標定及矯正。
式(5)中U/fx 和U/fy被稱為系統的像素當量,單位為:mm/pixels。由于標定用標準棋盤格的方格邊長為已知標準量,根據標定圖片可知一個方格邊長所占據的像素數,兩數相除即可得到像素當量,進而可得物距U。
圖像預處理
利用成像系統和相機采集的被測物數字圖像往往包含一些噪聲,而且被測物的特征也很不明顯。因此,完成被測齒輪圖像采集后,必須對圖像進行預處理,完成齒輪輪廓邊緣的提取。
數字圖像的預處理主要包括高斯濾波、二值化、腐蝕膨脹以及Canny邊緣提取四大部分。高斯濾波可以有效地消除實際相機拍攝圖像中出現的高頻噪聲干擾。圖像二值化使處理后圖像的灰度值只有0和255兩種數值,從而保留和突出重要的形態信息。通過腐蝕和膨脹對二值圖中的高亮區域進行處理,則可以使得目標輪廓邊界更為平滑,便于后續處理。Canny算法通過梯度算子計算突出灰度值,并對得到的圖像進行強度梯度篩選、非極大值抑制、雙閾值算法等運算,保證邊緣提取準確率。
測量算法流程
完成齒輪圖像的預處理后,基本上得到了齒輪的內外輪廓,如何從外輪廓像素中提取出有用特征,是最終實現齒輪幾何參數自動化測量的關鍵。本文以小模數圓柱直齒輪的齒距、齒厚和公法線長度3個重要的齒輪制造精度控制參數的自動測量為例,設計了機器視覺測量算法,具體流程圖如圖3所示。
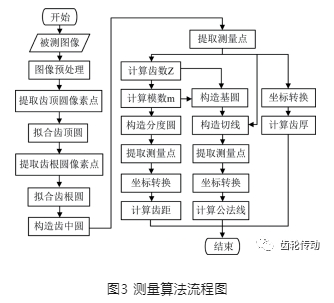
完成圖像預處理后,需要對外部齒廓像素進行進一步處理,從中提取出齒廓中齒頂圓像素點,再利用最小二乘法擬合齒頂圓。其中,提取齒頂圓像素點這一關鍵步驟尤為重要,直接影響著測量系統的整體精度,其算法流程圖如圖4所示。首先應用OpenCV中的Findcontours()函數從預處理后的圖像中提取出齒輪的內外輪廓像素,并摳除齒輪的安裝孔輪廓;然后利用最小凸包算法勾勒出齒輪最外層輪廓,并以5×5的大小建立齒頂圓掩膜;最后將預處理后的圖像與掩膜相乘,便得到齒頂圓輪廓。
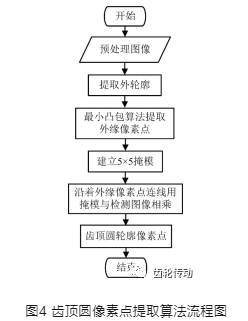
齒根圓像素點的提取過程如圖5所示,先計算齒頂圓的像素圓度,也即先評估齒頂圓上點相對于理想圓的徑向波動范圍,記為ΔR;齒根圓和齒頂圓同心,再計算齒廓上離圓心最近的點(該點必為齒根圓上點),記錄該點到圓心的距離為Rmin;齒根圓與齒頂圓應具有相當的圓度誤差,判斷每一個齒廓上的像素點到圓心的距離是否小于 (Rmin+ΔR),若小于該值則該像素點記為齒根圓上點。

除了齒頂圓和齒根圓像素點的提取以外,本文所述齒輪參數自動測量算法的3個關鍵子程序分別為:圓的最小二乘擬合算法、測量點提取算法以及精度參數計算算法,下面將簡述這3個關鍵子算法的原理。
圓的最小二乘擬合:本文使用最小二乘法原理擬合齒頂圓、齒根圓。最小二乘法是從誤差擬合角度對回歸模型進行參數估計的方法,它通過最小化誤差的平方和尋找數據的最佳函數匹配。
設擬合圓的面積為S,圓心為(a,b),半徑為r。通過Canny算子邊緣檢測得到的第i個邊界為D(xi,yi), i∈(1,…,n),該點距離圓心的距離為ri ,以ri 為半徑的圓面積為Si ,那么兩個圓的面積誤差εi 為:

根據最小二乘原理,當誤差εi 的平方和最小時,解得:
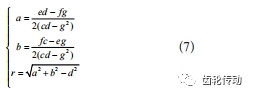
式(7)中:
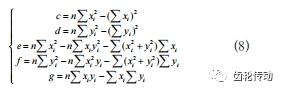
測量點提取:對于測量點的確定,根據齒輪幾何參數的定義本文先在齒輪外輪廓圖片上構造與齒輪基準軸線同心參考圓,參考圓與齒輪外輪廓的交點即為測量點。不同的被測參數具有不一樣的參考圓(詳見1.4.3節),測量點定義如圖6所示。利用圖3所示算法已經擬合得到的齒頂圓和齒根圓,參考圓與它們同心,直徑則是根據它們各自的定義得到,這樣很容易在軟件算法上實現各個參考圓的構建。
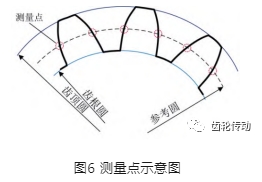
齒輪精度參數計算:小模數齒輪主要用于精密傳動結構中,它對傳動的準確性有較高的要求。齒輪精度參數中,齒距偏差、齒厚、 公法線長度等參數是影響傳動準確性的主要因素,因此本文主要針對小模數齒輪的齒距,弦齒厚及公法線長度(如圖7所示)進行檢測。這些參數的定義均為兩測量點間的弦長或者弧長,因此只需要明確兩測量點的位置坐標與齒輪中心坐標即可。算法實現過程中,需先構造參考圓或者切線,然后提取測量點,將測量點像素坐標轉換到物平面坐標系下,然后計算兩個測量點的距離或者弧長即可實現齒輪幾何參數的計算。
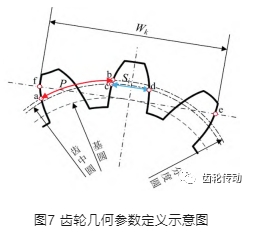
1)弦齒厚的測量算法
弦齒厚定義為齒高中部圓圓周上一個輪齒兩側齒廓間弧線的弦長就是齒厚,如圖7中Si 所示,也即圖中測量點c 和d之間齒中圓圓弧的弦長。構造齒中圓之前,需擬合齒頂圓和齒根圓,得到齒頂圓和齒根圓的直徑和圓心,齒中圓的直徑即為齒頂圓和齒根圓直徑的平均值,其圓心與齒頂圓和齒根圓同心。通過計算每齒與齒中圓的一對交點間的距離即可得到弦齒厚,其計算公式簡單在此不予贅述。
2)齒距的測量算法
根據定義,齒距定義為分度圓上任意兩個同側齒面間的弧長,如圖7中P所示,也即圖中測量點a和b之間的分度圓圓弧。通過計算相鄰兩齒與齒中圓的兩對測量點中兩個同側測量點間的弧長獲得。要構造分度圓,需要先計算得到該齒輪齒數Z,分度圓與齒頂圓同心,其直徑則為模數m(模數采用其規格值)和齒數Z的乘積。在齒厚參數的計算前,先構造了齒中圓提取了齒中圓上的各個測點。根據測量點的個數能夠計算出該齒輪的齒數Z。
構造分度圓后,提取測量點a和b,再結合分度圓的圓心坐標,可根據式(9)來計算齒距P:

式(9)中,(x1,y1)和(x2,y2)為物平面坐標系下兩個測量點的坐標,(xc,yc)為物平面坐標系下分度圓圓心的坐標,rc表示分度圓的半徑。
3)公法線長度的測量算法
公法線長度是指齒輪上幾個輪齒的兩端異向齒廓間所包含的一段基圓圓弧的弦長,即該兩端異向齒廓間基圓切線線段的長度如圖7中Wk所示,也即測量點e和f之間的線段長度,以圖7所示跨齒數k=3為例,公法線長度的計算過程如下:
(1)根據定義基圓與分度圓同心,基圓直徑等于cosα 與分度圓直徑的乘積,α為壓力角,由此構建基圓,記圓心為O;
(2)構建測量c和測量點d的中心點,記為點O’;
(3)連接圓心點O和中心點O’,構建中心線OO’;
(4)計算中心線OO’與基圓的切點坐標;
(5)根據切點構建基圓的切線,切線的方向與中心線OO’正交;
(6)提取切線與齒輪齒廓的交點,即為圖7中測量點e和f;
(7)計算測量點e和f之間的距離,即為所求公法線長度W3。
二、小模數齒輪精度參數測量實驗
實驗系統
為驗證本文所述機器視覺方法測量小模數圓柱直齒輪精度參數的有效性,搭建了一套影像測量系統。為模擬實際自動化生產線,實驗系統通過傳送帶傳送齒輪到指定位置。將影像測量系統安裝到工業機器人的末端,利用上位機控制機器人調整相機拍攝位置與拍攝角度。該系統實物如圖8所示,它主要由傳送帶、機械臂、LED光源、定焦鏡頭、工業相機以及上位機所構成。該系統里有COMS高分辨率工業相機進行攝像,將獲取的圖像上傳至上位機,進行圖像處理和參數測量計算。測量系統主要部件的型號及性能參數如表1所示,系統尺寸測量分辨率為0.006mm。
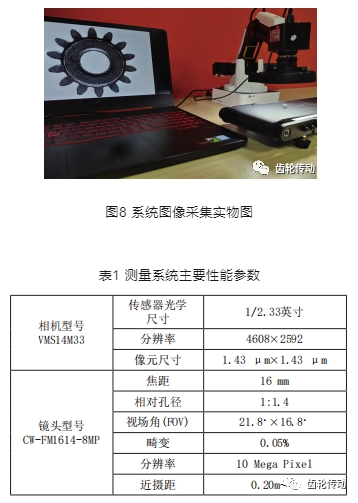
齒輪參數測量
本文對精密傳動領域常用的14齒小模數直齒輪進行一系列齒輪參數測量實驗。為了驗證本文所述方法和系統的準確性,使用標準14齒小模數齒輪作為被測件,其主要幾何參數如表2所示。
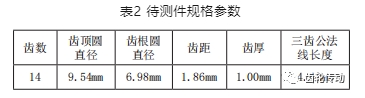
測量結果分析
對齒輪圖像進行處理后,可以得到如圖9所示的外部齒廓圖像。再由外向內分別構建分度圓、中圓以及基圓,從它們與齒輪輪廓構成的相交圖像中提取測量點,并畫出如圖10所示的公法線圖像,最終通過測量算法算出齒輪的齒厚、齒距和公法線長度。
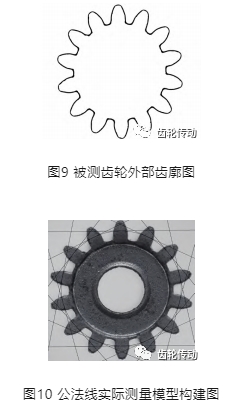
測量重復性分析:
使用本系統對待測件上同一齒進行8次測量,再對數據進行比較,可得到測量重復性的分析結果,待測件測量參數如表3所示。
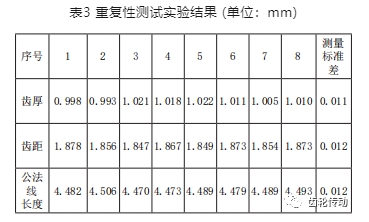
由表3測量結果,運用貝塞爾公式進行重復性標準差的計算,可以得出三項齒輪參數測量結果的重復性標準差均小于等于0.013mm,以齒距的重復性測試為例,作出圖 11所示折線圖,可以清晰的判斷出該測試齒序的齒距在 1.847mm~1.878mm之間,可見本系統的測量重復性較高。
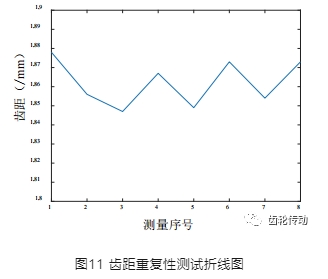
測量正確性分析:同樣本文還對待測件進行多次測量后求和取平均值。由于被測齒輪精度參數的真值未知,故這里將測量結果與被測齒輪規格參數進行對比,以檢驗本系統測量結果的正確性,被測件測量平均值與偏差如表4所示。
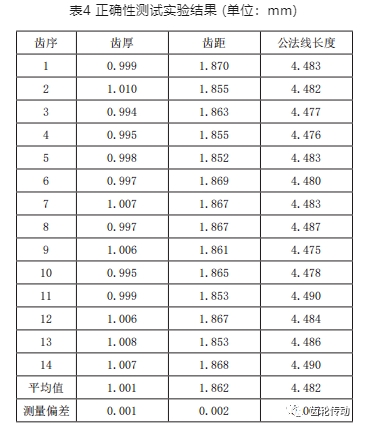
從表4中反映的是對齒輪14個齒序的齒厚、齒距以及分別14個齒序為基準的三齒公法線長度,以齒輪齒厚為例,作出如圖12所示的折線圖,比較直觀的展示出齒輪的齒厚情況,可以看出,齒輪齒厚、齒距、公法線長度與齒輪規格參數偏差最大僅有0.002mm,可見本系統的測量重復性精度極高,測量所得結果具有很高的正確性。
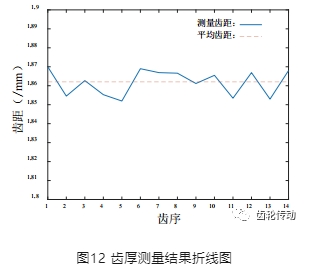
三、結語
針對的小模數圓柱直齒輪的精度參數測量問題,本文提出了一種基于機器視覺的自動化檢測方案。該方法利用高分辨率工業相機和成像系統對被測小模數齒輪進行攝像,經圖像預處理、齒輪特征擬合、測量點提取、坐標轉換等處理后,根據齒輪精度參數定義計算出被測齒輪的精度參數值。從測量結果及分析看,該自動化測量系統的測量重復性良好,測量標準差達0.013mm,重復性精度較傳統方法更優。本文所述方法和系統實現了對小模數齒輪各精度參數的非接觸、高精度的快速檢測。解決了當前接觸式測量法因探頭尺寸限制無法實現小模數齒輪精度參數測量的問題,為齒輪的自動化在線檢測提供了可行的技術方案。
參考文獻略.