齒輪作為重要的工業基礎部件,被廣泛應用在各種傳動系統中,其生產質量直接影響機械設備運行的平穩性及使用壽命,因此齒輪的出廠檢測具有重要的意義。齒輪雙面嚙合儀能夠對齒輪各個單項誤差進行綜合,得到齒輪的徑向綜合總偏差,反映出齒輪實際應用場合的傳動狀況,其結構簡單、操作方便、檢測效率高、測量結果可以很好地反映齒輪工作的真實狀態,是齒輪質量的主要檢測方法之一,廣泛應用于齒輪的快速測量與分選工業現場中。
傳統的機械式齒輪雙面嚙合儀對齒輪進行檢測時,需要依靠操作者手動驅動或手輪驅動使產品齒輪旋轉一周,對檢測過程中千分表的數據進行分析并記錄,存在檢測速度慢,無法保持恒速恒載狀態等問題,對檢測精度有一定的影響。為了提高檢測效率,實現齒輪的標準化測量,國內外研制出多種型號的智能齒輪嚙合儀,如哈量智能齒輪雙面嚙合綜合測量儀 3100A 型、德國 FRENCO ZWP 06 齒輪雙面嚙合儀、大阪精密機械 GTR-4LS 小模數齒輪雙面嚙合 儀等均在市場中得到應用,提高了齒輪的檢測效率,但受其成本限制,與傳統的機械式齒輪雙面嚙合儀相比,使用率相對較低。因此在現有的基礎上,針對實際生產情況,研制出全自動齒輪雙面嚙合儀,對于齒輪標準化測量和提高檢測效率具有重要的意義。
本文通過對傳統的機械式齒輪雙面嚙合儀進行智能化改造并設計相應的測控系統,并對整個系統進行了試驗,實現齒輪的自動化測量與結果分析,有效提高齒輪的檢測效率。
一、系統檢測原理
齒輪雙面嚙合儀測量原理
齒輪雙面嚙合測量技術是基于齒輪精度的誤差運動學理論,利用齒輪雙面嚙合綜合測量快速獲取齒輪的誤差信息。齒輪雙面嚙合測量儀結構如圖 1 所示,產品齒輪和測量齒輪分別安裝到左右平臺的固定軸上,在拉簧的作用力下,兩齒輪無側隙嚙合,通過固定在底座上的千分表測量滑動平臺沿導軌的位移信息間接測量齒輪中心距的變化。將千分表的測量數據和齒輪旋轉角度記錄下來繪制曲線,得到齒輪雙面嚙合徑向誤差曲線(見圖 2)。
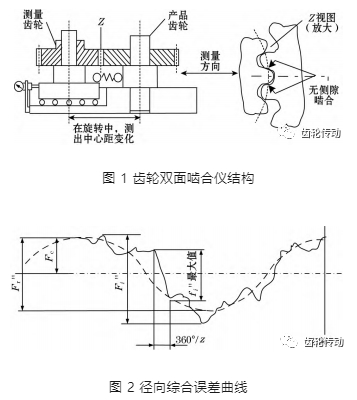
齒輪雙面嚙合儀檢測參數
齒輪雙面嚙合測量項目主要包括徑向綜合總偏差 Fi″ 和一齒徑向綜合偏差 fi″。
(1) 徑向綜合總偏差 Fi″ 指的是在齒輪雙面嚙合檢測時,測量齒輪與產品齒輪兩齒輪之間無側隙嚙合,產品齒輪旋轉一周的過程中,兩齒輪中心距的最大值與最小值之差,是影響齒輪傳遞運動準確性的主要誤差項目之一。其計算如式(1) 所示。

式中: i = 1,2,3…,n; Y[i]為中心距數組。
(2) 一齒徑向綜合偏差 fi″ 指的是在產品齒輪與測量齒輪嚙合接觸旋轉一周后,在單個齒距角內,兩齒輪中心距的最大值。fi″ 主要影響單個齒距角內瞬時傳動比的變化,是影響齒輪傳動平穩性的主要誤差項目之一,其計算如式(2) 所示。

式中 z2 為被測齒輪齒數。
二、測控系統方案設計
為了保證系統的可靠性和滿足系統的智能化測量需求,采用 PLC 為下位機、計算機為上位機的相結合的方案實現齒輪雙面嚙合儀測控系統人機交互功能,測控系統方案設計方案如圖 3 所示。
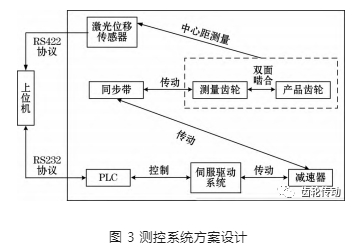
硬件部分主要由上位機、伺服驅動系統、同步帶、產品齒輪、測量齒輪、激光位移傳感器及 PLC 組成。上位機通過 RS422 通信協議實時獲取和處理激光位移傳感器的數據信息,得到測量齒輪和產品齒輪中心距變化信息。PLC 通過 RS232 通信協議接受來自上位機的報文指令,作用于伺服控制系統,控制電機精確運動。
在進行齒輪測量試驗時,上位機發送指令給 PLC,控制產品齒輪旋轉一圈,同時處理和記錄測量過程中激光位移傳感器的數據,繪制出測量曲線。產品齒輪停止旋轉后,上位機對記錄的數據再次處理,評價齒輪是否滿足加工要求。
三、測控系統硬件設計
齒輪嚙合儀驅動改造
對某型齒輪雙面嚙合儀器進行驅動改造如圖 4 所示,在測量齒輪側新增一個底座用于安裝減速器,減速比為 1∶10,伺服電機連接減速器,使得齒輪旋轉時單位脈沖對應的相位角精度提升 10 倍,從而提高定位精度。減速器的輸出端和標準齒輪固定軸各安裝一個同步輪,用同步帶連接,標準齒輪軸上的同步輪打孔固定傳動銷,標準齒輪底端銑削出凹槽,當同步輪轉動,傳動銷在周向上與標準齒輪凹槽產生轉矩,從而帶動標準齒輪穩定旋轉。激光位移傳感器通過支架固定到底座的左側,激光直射到滑動平臺的左側端面上,測量滑動平臺沿導軌的位移變化。改造后的齒輪雙面嚙合儀由手動驅動模式升級為伺服系統驅動模式,增加齒輪測量過程的平穩性,提高了檢測精度。
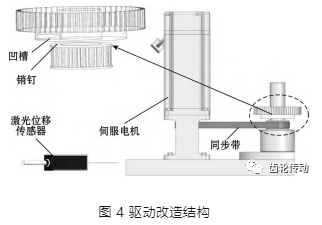
位移測量模塊
位移測量模塊測量齒輪的中心距變化,將測量數據實時傳輸到上位機處理。系統采用 HL-G103-S-J 型號的激光位移傳感器測量齒輪嚙合中心距的變化,原理是發射出一束激光射向物體表面,測量出往返時間,根據光速計算出往返距離。該傳感器有效測量范圍為 26.3 mm,分辨率為 0.5 μm,滿足測量任務的精度要求,并以 RS422 通訊協議將測量數據發送到上位機。
控制模塊和驅動模塊
控制模塊以 FX3U-64 PLC 為主控制器,FX3U 系列控制器具有價格低、響應速度快,功能強大,使用靈活等特點。伺服控制器產生高速脈沖信號,作用于伺服驅動器,精確控制測量過程中齒輪的旋轉位置。PLC 系統的 I/O 分配表如表 1 所示。
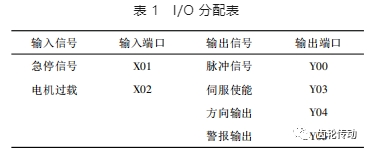
為保持測量過程中精確的位置控制,本文選用伺服 A5 系列 MHMF012LU2M 伺服電機及與之匹配的伺服控制驅動器 MADLT05SF 作為測控系統的驅動單元。
四、測控系統軟件設計
系統的軟件設計包括上位機的人機交互界面軟件設計和具有隨動功能的 PLC 控制程序設計。上位機人機交互界面用 LabVIEW 設計,主要負責測量過程數據記錄和綜合誤差曲線的顯示以及測量結果的分析,是操作者與設備測量信息交互的平臺; PLC 則主要負責齒輪的旋轉定位和隨動過程中的位置控制。
具有隨動功能的 PLC 程序設計
PLC 執行的主要功能分為測量功能和隨動功能,如圖 5 所示。測控系統上電后,PLC 初始化運行參數,定義默認的電機旋轉速度和產品齒輪旋轉一周的脈沖數,并根據實際測量要求調節測量速度,實時記錄伺服電機的絕對位置。本文通過產品齒輪齒數和測量齒輪齒數計算出產品齒輪旋轉一周的脈沖數,計算公式為

式中:Pul 為產品齒輪旋轉一圈脈沖數; n 為電機旋轉一圈脈沖數; Z1 為產品齒輪齒數; Z2 為測量齒輪齒數。
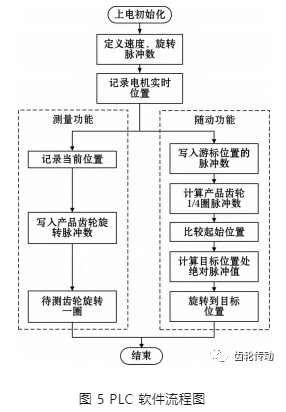
PLC 收到上位機的測量指令后,控制伺服電機以設定的速度驅動產品齒輪精確旋轉一周。
針對產品齒輪表面可能存在毛刺或附有異物的問題,設計隨動功能。從誤差曲線可以觀察到異常位置,移動游標至該位置后,上位機向 PLC 寫入異常位置信息,PLC 比較該位置與測量時的初始位置,計算出異常位置相對于操作者的位置,隨后控制電機將產品齒輪的異常位置正對操作者。
上位機程序設計
選用 LabVIEW 開發測控系統的上位機程序,主要分為設置模塊、數據交互模塊、測量分析模塊、歷史數據模塊。
設置模塊建立起上位機與 PLC 和激光位移傳感器通信連接,是數據交互的基礎條件; 數據交互模塊分為 2 個部分,一是根據 PLC 數據傳輸規則發送指令和讀取 PLC 寄存器信息,二是根據激光位移傳感器數據格式獲取測量的數據信息; 測量分析模塊對測量數據進行處理,繪制綜合誤差曲線,得到齒的誤差信息;歷史數據模塊用于讀取測量過的齒輪信息。
設置模塊:設置模塊是建立上位機和 PLC 通信以及獲取測量數據的基礎,該模塊利用 VISA 工具包設置上位機與 PLC、上位機與激光位移傳感器的通信參數,建立起通信連接。在此模塊可以控制電機正轉、反轉動作以及觀察查激光位移傳感器的當前數據信息,用于判斷上位機與 PLC 和激光位移傳感器是否通信正常以及調節測量硬件,使測控系統達到良好的工作狀態。
數據交互模塊:數據的交互是測控系統的關鍵部分。上位機采用 FX 編程口通信協議協議直接發送報文指令給 PLC,進行數據交互。創建一個報文生成模塊子 vi,輸入要寫入的值和 PLC 相應的寄存器地址,通過公式節點計算出報文,以字符串的形式發送到 PLC,報文生成程序如圖 6 所示。

對來自激光位移傳感器的數據以截取字符串的形式得到十進制數字符串,轉化為整數,處理得到實際數值; 針對字符串數據突變的現象,設定一個閾值,剔除超出閾值的數據,保證數據的準確性; 激光位移傳感器數據采集處理程序如圖 7 所示。
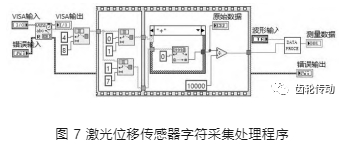
測量分析模塊:測量分析模塊是智能化齒輪雙面嚙合儀測控系統的核心,主要功能是實時繪制誤差曲線,分析測量結果。
在此模塊中需要輸入測量齒輪齒數 Z1、產品齒輪齒數 Z2、公差范圍和設置測量速度,從而建立一個測量方案。啟動檢測流程后,上位機給 PLC 發送測量指令,同時采集傳感器位移數據,顯示測量齒輪和產品齒輪的實時嚙合曲線,并將原始數據以 txt 文件的形式保存到系統中。
采用集合經驗模態分解的方法( EMD) 處理產品齒輪旋轉一圈后激光位移傳感器采集的原始數據( 如圖 8 所示) ,分離出測量齒輪與產品齒輪的中心距數據,確定嚙合誤差曲線中所有的極大值和極小值,獲得 fi″; 確定數據的最大值與最小值,計算 Fi″,從而判斷 齒輪是否滿足加工要求。若產品齒輪某個位置存在異常,操作者可移動嚙合曲線的游標,可將該位置正對操作者,方便觀察異常情況。
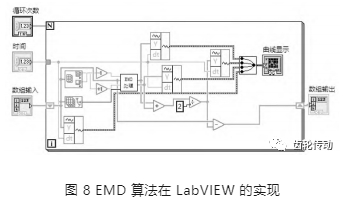
歷史數據模塊:歷史數據模塊可以還原出所有產品齒輪的測量結果信息,界面如圖 9 所示。操作者可以選擇數據所在的文件夾,選擇要讀取的數據,獲取測量時間。單擊“讀取”按鈕,可以獲得 Z1、Z2、設定的最大誤差范圍以及實際誤差,同時繪制出歷史嚙合誤差曲線圖; 若需要出具檢測報告,可通過“報表生成”按鈕一鍵生成。
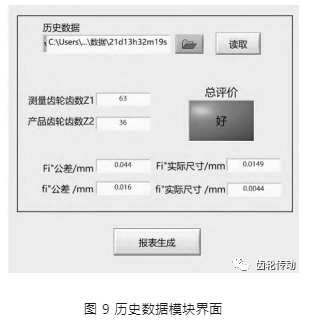
五、系統試驗驗證
齒輪雙面嚙合儀智能化改造后的機械結構部分和電氣控制部分如圖 10 所示。為了驗證測控系統在實際測量過程中的穩定性和重復測量精度,對各個功能進行測試,選取產品齒輪齒數為 36,測量齒輪齒數為 63 作為試驗對象。
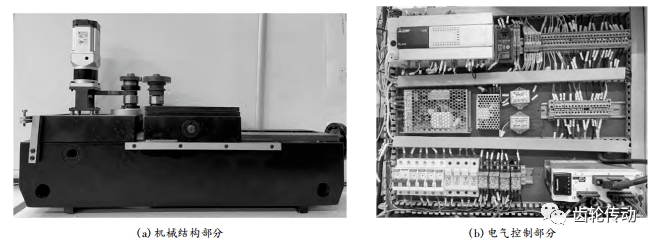
圖 10 齒輪雙面嚙合儀智能化改造機械結構部分和電氣控制部分
智能化改造機械結構部分和電氣控制部分
新建一個測量方案,在參數輸入部分輸入基本的測量參數,設定 Fi″ 和 fi″ 的最大誤差范圍。單擊“開始測量”,上位機向 PLC 發送測量指令,精確控制產品齒輪旋轉一周,同時解析激光位移傳感器的數據,繪制綜合誤差曲線。測量結束后,得到 fi″ 和 Fi″。兩組數據都在設定的最大誤差范圍之內,說明產品齒輪符合加工要求。并在綜合誤差曲線中顯示最大值與最小值的位置,同時對反映一齒徑向綜合偏差的誤差曲線加粗顯示。測量結果如圖 11 所示。
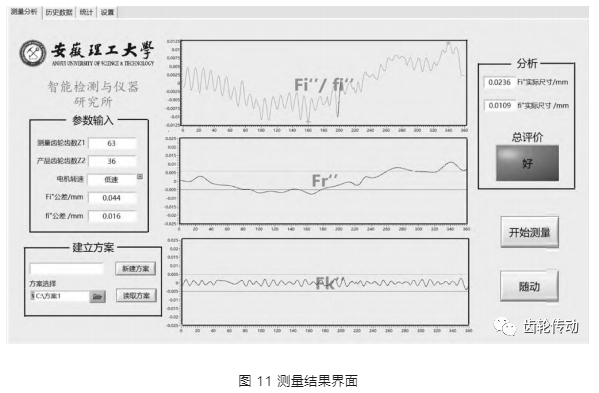
移動 x 軸上綜合誤差曲線中的游標到異常位置,單擊“隨動”按鈕,控制伺服電機將產品齒輪該位置正對操作者,方便觀察該位置的情況,驗證隨動功能的完整性。
根據以上的試驗方法,對產品齒輪齒數為 36,測量齒輪齒數為 63 的試驗對象進行多次試驗。試驗結果如表 2 所示。
使用德國 FRENCO ZWP 14 齒輪雙面嚙合儀測量的產品齒輪的結果為: Fi″ 為0.023 6 mm,fi″ 為0.010 7 mm。由表 2 可得,通過 7 組試驗可以發現,經過智能化改造后的齒輪雙面嚙合儀可以準確的得到齒輪主要測量參數,測量數據重復性誤差較小,滿足檢測要求。
六、結論
本文對機械式齒輪雙面嚙合儀進行改造,設計了基于 FX3U-64 PLC 與 LabVIEW 的智能齒輪雙面嚙合儀測控系統,提出了總體方案、硬件和軟件的設計。經過實際測試,結果表明該測控系統實現了齒輪的自動化測量、對數據的采集和處理分析,能夠自動判別 齒輪的加工質量,操作者可根據波形圖定位到齒輪異常位置,滿足了工業的生產需求,有效提高了齒輪的檢測效率。
參考文獻略.