無論是傳統乘用車還是新能源乘用車,差速器都是汽車零部件的一個重要組成部分,它提供動力傳動,保障汽車轉彎安全差速。傳統差速器和主減速齒輪是通過物理方式連接,即采用螺栓連接,差速器特性對螺栓、轉矩要求比較高。在商用車領域,EMAG LaserTec 提供了激光焊接整體生產系統,將主減齒輪和差速器采用化學融合方式連接,焊接成為一個整體。針對貨車差速器的生產,EMAG 生產系統將 3 個獨立部件焊接在一起,由此可省去大約 40 處昂貴的螺栓連接成本,同時重量也大幅減輕。
一、技術研發
株洲齒輪有限責任公司(以下簡稱“株洲齒輪”)與某高校合作在乘用車上對差速器和主減齒輪焊接技術進行研究。
焊接技術難點:差速器殼體材料主要為球墨鑄鐵,主減速齒輪材料主要為滲碳鋼,兩種材料的含碳量、金相組織和化學性能差異很大,無法通過自融方式焊接為一個整體。我們采用添加焊絲的方式進行焊接,采用以鎳為基體的焊絲。焊接技術方案為部件激光清洗、部件壓裝、部件激光焊接、焊縫超聲波探傷、總成烘干、清潔焊縫和焊渣等,兩臺工業機器人完成整個系統的上下料和作業。
部件激光清洗
通過機器人獨立上料,對差速器殼體和主減齒輪的焊接部位的表面進行激光灼燒(圖 1),除去所有殘留物,例如冷卻劑或防腐劑,減少雜質對焊接質量的影響,激光清洗中激光器功率較低,既即達到清洗目的,又能保護產品。激光清洗過程非常快捷,同時設備又采用雙工位清洗,設備工作效率高。
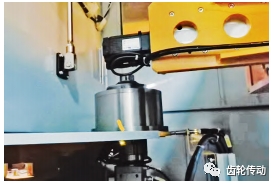
圖 1 激光清洗機
部件壓裝
機器人從激光清洗機中取出部件并將其送入壓裝工位,壓裝設備有力和位移監控功能,確保壓裝到位(圖 2)。
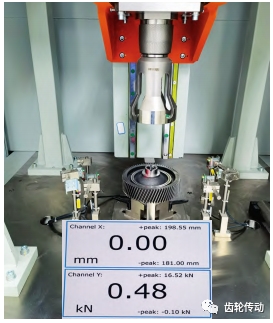
圖 2 主減齒輪壓裝機
激光焊接
機器人將壓裝好的部件取出并傳遞到焊接設備(圖 3),通過專用的工裝軸向定位夾緊后,采用高能量填絲焊技術將差速器殼體和主減齒輪焊接成為整體。整個焊接過程非常快捷,激光器發射激光,先將鎳基焊絲融化,然后焊絲作為焊接中介將差速器和主減齒輪融合成一個整體。
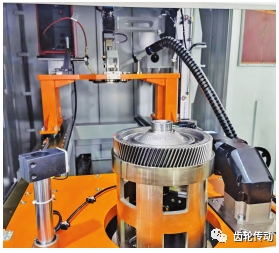
圖 3 激光焊接機
合理的焊接工藝參數焊接出的差速器和主減齒輪的熱變形都比較小。株洲齒輪已經完成 4 mm、5 mm 和 5.5 mm 焊縫的焊接工藝開發,實現了焊接變形小、焊接飛濺小、焊接質量高及無虛焊等。
超聲波探傷
焊接完成后采用超聲波檢測技術(圖 4),系統會 100% 自動檢查焊接區域質量,做到零缺陷。完成探傷后進行總成烘干,將探傷的媒介探傷液烘干,防止產品生銹。烘干后機器人轉運到刷焊縫工位,對焊縫表面的焊渣、氧化層等進行清理。
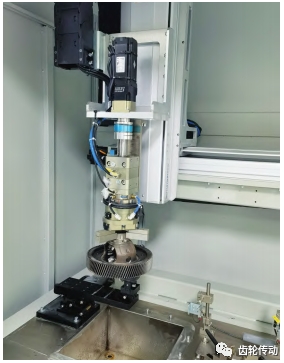
圖 4 超聲波探傷機
二、焊接技術優勢
采用焊接方式連接的差速器具備輕量化、低成本、高精度、低噪聲和結構緊湊等幾方面優勢。
輕量化
差速器和主減齒輪通過焊接方式連接取代了傳統的螺栓連接方式,不僅節省了大量的螺栓,而且差速器殼體和主減齒輪結構設計更加簡約,質量明顯改善。根據株洲齒輪開發 3000 N · m 的 B 型減速器和 5000 N · m 的 C 型減速器的焊接差速器和螺栓差速器對比,發現 3000 N · m 的 B 型減速器焊接差速器總質量較螺栓差速器總質量減少了 0.95 kg,減重約 15.5%;5000 N · m 的 C 型減速器焊接差速器總質量較螺栓差速器總質量減少了 1.24 kg,減重約 13.1%。由此可見焊接差速器在輕量化方面具有明顯優勢,見表 1。
表 1 差速器輕量化 (單位 :kg)
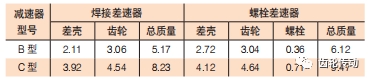
低成本
差速器和主減齒輪采用焊接方式連接后首先節省了大量的螺栓的昂貴費用;與此同時也取消了差速器和主減齒輪上的螺栓孔、螺紋孔等工藝,節約了鉆孔和攻絲等加工費用、取消了總成裝配工序,節約了裝配等人工費和螺栓擰緊設備費用。而相對增加的僅有焊接成本,在批量自動化條件下,焊接成本要低很多,激光焊接的成本比螺栓差速器成本低約 20%。
高精度
傳統螺栓連接差速器的主減齒輪單獨進行磨齒,然后再與差速器裝配,螺栓打緊。主減齒輪磨齒使用高精密磨齒機,磨齒過程中采用心軸定位,由于定位面較小,磨齒過程中齒輪有輕微抖動,齒輪的螺旋線精度略差,同時與差速器裝配后累積裝配誤差后,以實際使用的軸承位置為基準檢測,齒輪的螺旋線精度變化很大。通過多組齒輪數據得出表 2 中的齒輪精度平均值。
表 2 螺栓差速器齒輪精度 (單位 :μm)

焊接差速器的主減齒輪和差速器焊接之后作為一個整體部件進行磨齒,磨齒過程中采用頂尖和差速器的軸承處外圓軸向定位,定位精度高,裝夾力大,磨齒后穩定性好,磨齒后的精度即為實際使用精度,沒有裝配誤差。通過多組齒輪數據得出表 3 中的齒輪精度平均值,對比兩種磨齒方式,發現焊接差速器的齒輪累積偏差 Fp 接近 1 級齒輪精度;而螺栓差速器的齒輪累積偏差 Fp 達到 3 級齒輪精度,焊接差速器的齒輪累積偏差提高了 1 級。焊接差速器的齒輪徑向跳動公差 Fr 達到 2 級齒輪精度;而螺栓差速器的齒輪的徑向跳動公差Fr 達到 3 級齒輪精度,螺栓擰緊后累積裝配誤差后齒輪的徑向圓跳動公差達到了 6 級,明顯焊接差速器的齒輪的徑向圓跳動公差提高了 3 級。焊接差速器齒輪的螺旋線傾斜偏差一致性 fhβ V 值和螺旋線三截面扭變偏差達到了 1 級齒輪精度;而螺栓差速器齒輪的螺旋線傾斜偏差一致性 fhβ V 值和螺旋線三截面扭變偏差達到了 2 級齒輪精度,齒輪精度提高了 1 級。可見焊接差速器齒輪可以達到 2 級齒輪,比螺栓差速器齒輪高了 4 級精度。量產時螺栓差速器主減速齒輪磨齒可以穩定達到 5 級齒輪精度,裝配和螺栓擰緊后,齒輪可以達到 6 ~ 7 級精度。而量產的焊接差速器的主減齒輪可以穩定達到 4 ~ 5 級精度,沒有裝配誤差。焊接差速器在齒輪精度方面有明顯優勢。
表 3 焊接差速器齒輪精度 (單位 :μm)

低噪聲
焊接差速器齒輪磨齒后可以達到 2 級齒輪精度,裝配到減速器中進行 NVH 測試,二級齒輪噪聲有明顯降低,噪聲較螺栓差速器齒輪箱降低 2 dB, 如圖 5 所示。
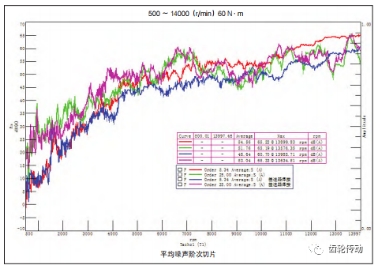
圖 5 焊接差速器與螺栓連接差速器 NVH 對比
結構緊湊
螺栓差速器結構設計時要考慮差速器承載能力,預留差速器空間、螺栓裝配空間等,從而限制了主減齒輪尺寸,主減齒輪不能過小。而采用焊接結構時差速器可以完美避開這些限制,焊縫位置可以設置在差速器外側,焊縫探傷空間僅為螺栓空間的 50%,由此累積二級傳動的中心距可以減小 10 ~ 20 mm。因此減速器的整體尺寸可以更小,而承載能力也很大,同時減速器質量也會更輕,也實現了乘用車輕量化。
三、結論
株洲齒輪正在逐步優化焊接工藝流程,加載機器人產線,控制生產節拍,保證穩定的工藝和高效率。同時株洲齒輪也與各大高校聯合開發焊接結構設計、工藝路線,潛心研究,打破國外對焊接差速器技術的壟斷,引領乘用車的焊接差速器技術發展。