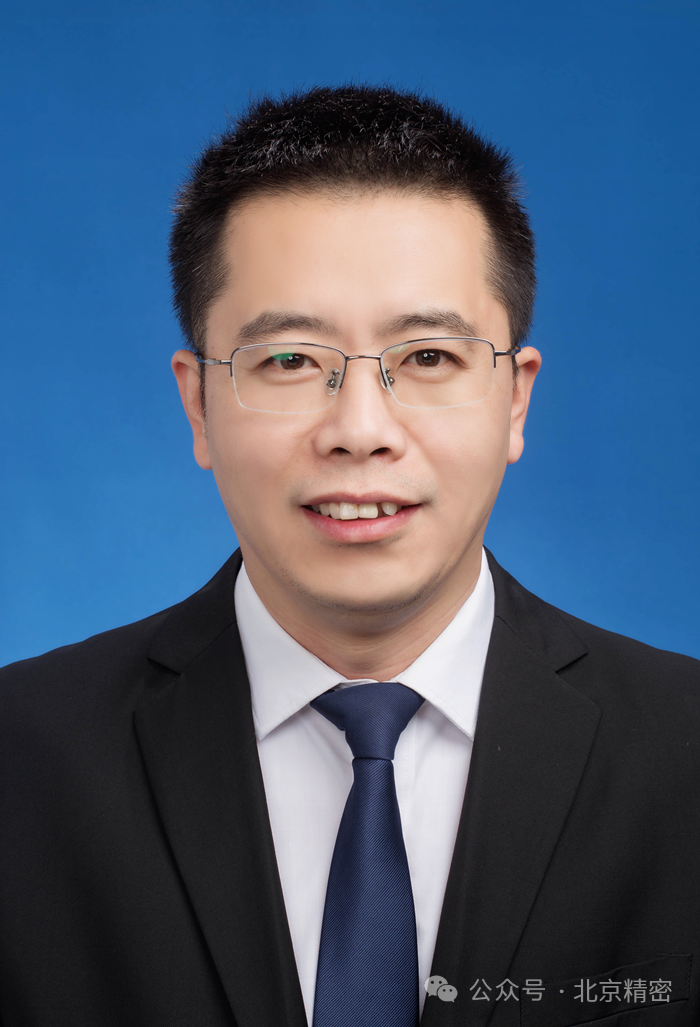
和法洋簡介:1984年生,2018年博士畢業于北京工業大學,師從石照耀教授,高級工程師。中國通用機械工業協會減變速機分會標準化工作委員會委員,《機械傳動》編委會青年委員。主要從事蝸桿傳動研究,涉及嚙合理論、數控裝備、精度檢測、軟件開發等。已獲得發明專利10項,實用新型專利10項,軟件著作權7項,發表論文17篇。主持上海市科創基金2項。
平面二次包絡環面蝸桿傳動研究進展
和法洋 石照耀
平面二次包絡環面蝸桿傳動具有多齒嚙合、雙線接觸和潤滑角大的特點. 與同型號的圓柱蝸桿傳動相比,其承載能力強、傳動效率高、使用壽命長。根據嚙合原理,由母面包絡出蝸桿的過程稱為第一次包絡。若母面為平面、蝸桿外形為環面,則通過第一次包絡得到的蝸桿稱為平面包絡環面蝸桿。以平面包絡環面蝸桿為母面包絡出蝸輪的過程稱為第二次包絡,得到的蝸輪稱為平面二次包絡蝸輪。由平面包絡環面蝸桿和平面二次包絡蝸輪組成的傳動形式就稱為平面二次包絡環面蝸桿傳動。本文從設計技術、制造技術和檢測技術三個方面綜述了平面二次包絡環面蝸桿傳動50多年來的研究和發展現狀,并給出需要進一步研究的問題。
1. 設計技術方面
1.1. 三維造型技術
平面包絡環面蝸桿和平面二次包絡蝸輪的齒面均為空間復雜曲面,其三維實體建模可用于數控加工和有限元仿真分析等。早在1977年平面包絡環面蝸桿和平面二次包絡蝸輪的數學模型就已經建立起來了,但是由于成型的特殊性至今沒有嚴格的三維精確建模方法。現行的建模方法主要分為兩種,一種是根據嚙合原理建立齒面方程,借助Matlab等軟件求出平面包絡環面蝸桿和平面二次包絡蝸輪齒面上瞬時接觸線或其他交線上的點,然后再導入三維造型軟件,通過曲面擬合生成齒面。這種方法復雜而費時,對參數的變化不能快速響應。而且模型齒面與理論齒面不可避免存在偏差,需要判斷兩者之間的誤差能否滿足精度要求. 另一種是直接數字化建模。該方法基于展成原理,模擬實際加工過程,進行布爾運算生成實體. 避免了復雜的嚙合方程的計算。但是在考慮承載變形和修形時,三維建模過程更加復雜。直接數字化建模中蝸輪和蝸桿每轉動1次進行切削稱為一步,轉動的角度稱為步長。步長越小,所得模型精度越高,但是數據量就越大。需要根據計算機性能和精度需求來確定合適的步長。
1.2. 嚙合特性分析
在20世紀90年代以前,評價平面二次包絡環面蝸桿傳動宏觀接觸狀態的瞬時接觸線、齒面接觸區域、各類界限曲線和評價微觀嚙合性能的誘導法曲率半徑系數、相對卷吸速度、潤滑角的計算都已經非常成熟。以中心距為125mm,傳動比為40的未修形平面二次包絡環面蝸桿傳動為例,平面二次包絡蝸輪齒面上瞬時接觸線的分布如圖1所示。齒面存在接觸線交叉區,該區域接觸頻率較高,容易發生疲勞點蝕,是蝸輪齒面最薄弱的地方。
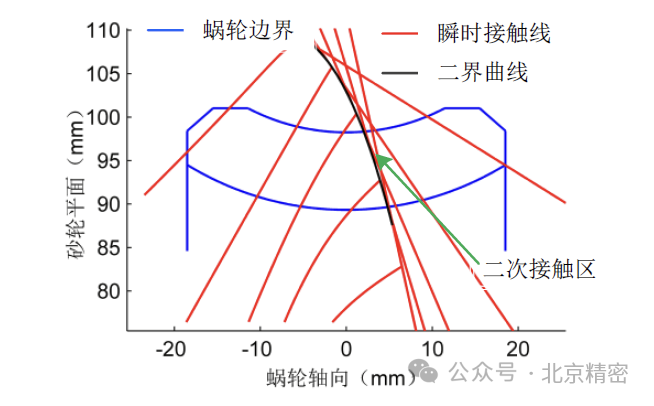
圖1 未修形傳動蝸輪
在載荷分布方面,未修形傳動的接觸載荷從嚙入端到嚙出端是逐漸減小的。接觸線兩端的接觸載荷較大,其他部位分布比較均勻。最大載荷出現在二次接觸區靠近二界曲線附近。而隨著總載荷的加大和運轉時間的增長,載荷分布偏向嚙出端。接觸應力沿接觸線呈“L”或“U”形分布。
1.3. 參數優化設計
平面二次包絡環面傳動性能分析方面的研究表明,選擇合理的參數可以提高傳動性能。通過分析文獻發現在平面二次包絡環面蝸桿傳動中心距和傳動比固定的情況下,先后出現了多種不同的參數優化方法,在設計變量、約束條件、優化目標和優化算法等方面均有所不同。每種方式都可以取得比優化前更好的效果,但是并不一定取得最佳的嚙合性能。考慮的因素不同得出的結論也不同,可比性較差。
1.4. 修形設計
除了對參數進行優化外,實踐表明合理的修形也可以提高平面二次包絡環面蝸桿傳動的性能。對于平面二次包絡環面蝸桿傳動,修形分為兩種:一種是基于嚙合原理的修形,通過第一次包絡的部分相對運動參數不等于第二次包絡的相對運動參數來實現。這些參數可以是中心距、傳動比、蝸桿與蝸輪的相對軸向位置等。這種修形方式需要對蝸桿和滾刀進行同樣的修形,修形后的平面二次包絡環面蝸桿傳動仍是線接觸. 另一種是失配修形,主要采取第一次包絡過程中包絡蝸桿和包絡滾刀的參數不一致或采用其他類型的環面蝸桿來代替平面包絡環面蝸桿等方式。修形后的齒面不再是線接觸。對于這兩種修形方式,很多文獻并沒有區分開來,并且對于修形和未修形的平面二次包絡環面蝸桿傳動存在多種稱謂,如表1所示。
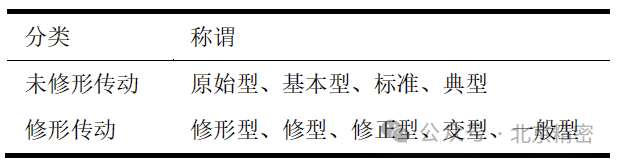
表1 不同稱謂
基于嚙合原理的修形的研究主要集中在修形類型的選取和修形量的選擇兩個方面。根據修形后平面二次包絡蝸輪齒面是否存在二界曲線,修形傳動可分為I型傳動和II型傳動。未修形、I型和II型平面二次包絡環面蝸桿傳動的性能對比如表2所示。
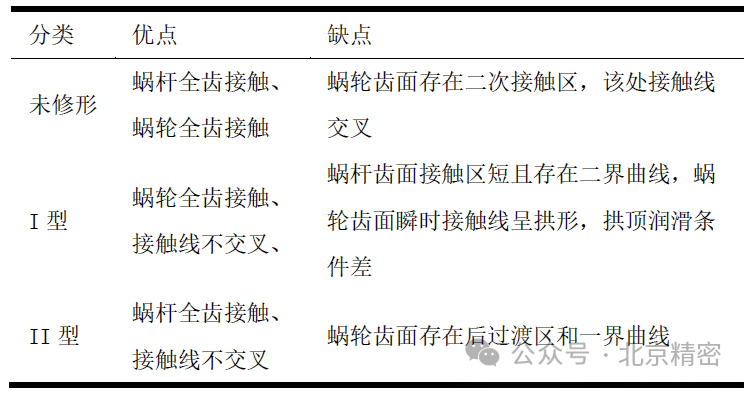
表2 性能對比
仍以圖1所示蝸輪副參數為例,當中心距修形量為-0.3mm時的I型傳動和中心距修形量為0.3mm時的II型傳動蝸輪齒面瞬時接觸線的分布,分別如圖2、3所示。
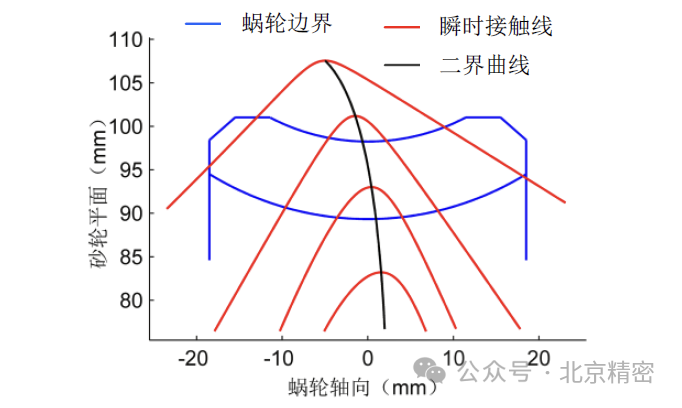
圖2 I型傳動蝸輪
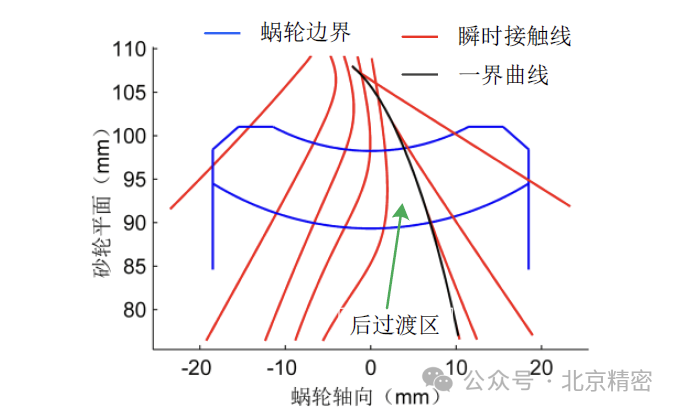
圖3 Ⅱ型傳動蝸輪
對于采用中心距修形的平面二次包絡環面蝸桿修形傳動,修形量越大,其蝸輪相對于未修形傳動蝸輪齒面的變化越大。其中I型傳動的蝸輪齒面切深比未修形傳動蝸輪淺;II型傳動蝸輪齒面的切深比未修形傳動蝸輪深。對于II型傳動,蝸輪齒面上微觀嚙合性能較差的一界曲線總能被滾刀切除。
跑合試驗表明I型傳動的傳動效率高于II型傳動,溫升低于II型傳動,但仍處于混合潤滑狀態。在保證了幾何尺寸精度和安裝精度的前提下,降低環面蝸桿副的齒面粗糙度比修形更能顯著提高膜厚比,從而實現完全彈性流體動力潤滑。
2. 制造技術方面
2.1. 數控加工技術
平面包絡環面蝸桿和平面二次包絡蝸輪是實現平面二次包絡環面傳動的基礎原件,它們的制造精度、質量直接影響傳動的效率、噪聲、運動精度和使用壽命。平面包絡環面蝸桿齒面的加工方式可以分為三種:車削、磨削和銑削。傳統的加工方式是在具有回轉臺的專用機床上進行的。在回轉臺上安裝切刀盤即可進行車削,安裝銑刀盤即可進行銑削,安裝磨頭即可進行磨削。這種機床在結構樣式上通常為外圓磨床樣式、車床樣式或滾齒機樣式。加工時通過沿蝸桿徑向移動回轉臺來調節中心距,通過配掛輪來調整傳動比。三種樣式都存在著機床調整煩瑣、加工周期長、成本高,而且加工范圍受回轉臺直徑限制的缺點。
平面二次包絡蝸輪通常采用滾刀滾切的方式加工。滾刀在齒面磨削成型后需要進行后角鏟磨,并保留一定的刃帶寬度。由于每個刀齒兩側的刃口曲線及其上面每點在滾刀螺旋面上的螺旋角都不一樣,使得滾刀后角的鏟磨特別復雜和困難,目前主要還是靠手工鏟磨。滾切后的蝸輪齒面存在殘留的切削棱,如圖4所示。通過增加容屑槽數可以降低殘留切削棱的高度,如圖5所示,但是滾刀的制造難度會增加。由于采用徑向進刀的加工方式,每顆齒所切下的銅屑也不一致,如圖6所示。刀齒的受力和磨損程度也不一致。
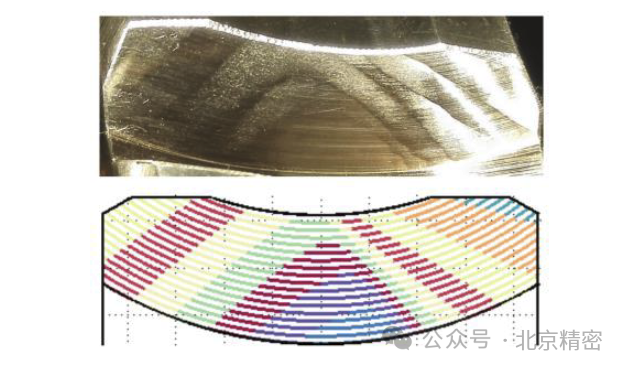
圖4 滾切蝸輪齒面
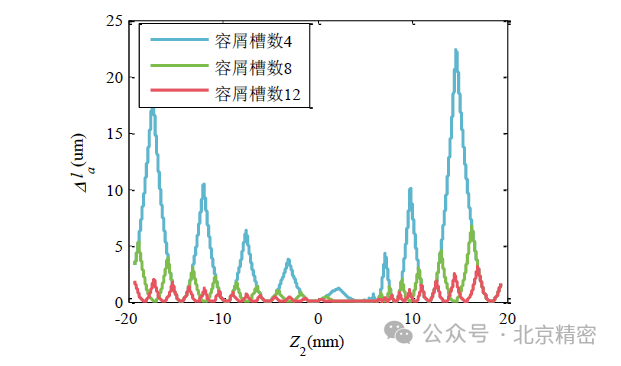
圖5 殘留切削棱高度
隨著數控技術的發展,出現了平面包絡環面蝸桿數控車削技術、虛擬回轉中心技術、五軸聯動加工技術、平面二次包絡蝸輪銑削技術和平面二次包絡蝸輪滾刀后角鏟磨技術五種新型的數控加工技術。2.1.1 數控車削技術
蝸桿毛坯裝夾在數控車床上,首先根據嚙合原理計算出蝸桿齒面上各點的坐標,然后通過三軸聯動,控制車刀頂刃的運動軌跡沿蝸桿齒面來進行車削。這種加工方式下車床數控系統必須具備三軸聯動功能,車削效率低,精度低。近幾年又出現了基于普通數控車床的新型車削技術。該技術采用普通切斷刀,利用宏程序和螺紋切削功能實現了變導程環面蝸桿的快速開齒。采用該技術可以顯著提高加工效率、降低制造成本,但是加工出來的是直廓環面蝸桿,需要進一步磨削才能成型。在其磨削過程中仍存在著加工余量不均勻的現象。如圖7所示,蝸桿嚙入端磨削余量大于嚙出端磨削余量,齒頂磨削余量大于齒根磨削余量。

圖7 磨削余量
2.1.2 虛擬回轉中心技術
虛擬回轉中心技術主要用于平面包絡環面蝸桿齒面的磨削。采用該技術的機床床身結構為車床樣式或外圓磨床樣式。以車床樣式為例,開齒后的環面蝸桿安裝在主軸上,雙層工作臺上安裝了回轉臺,回轉臺上又安裝有磨頭。雙層工作臺沿X向和Z向進行圓插補運動,帶動回轉臺做平移,與此同時回轉臺沿B軸做旋轉運動,蝸桿繞C軸也轉動相應的角度進行四軸聯動。四聯動軸的運動關系為圓插補運動轉動的角度等于回轉臺轉動的角度,蝸桿轉動的角度與回轉臺轉動角度的比值為傳動比。此外磨削過程中通過控制插補運動的半徑,來保證砂輪磨削平面始終與虛擬的主基圓相切,砂輪回轉邊緣始終與蝸桿齒根相切。這樣就實現了平面包絡環面蝸桿齒面的磨削。采用虛擬回轉中心技術的機床取消了中心距調整機構和主基圓半徑調整機構,而且與傳統的加工方式相比其回轉臺尺寸縮小了很多,增大了機床的加工范圍,機床操作也簡單。但是聯動軸數多,對機床的精度要求高。
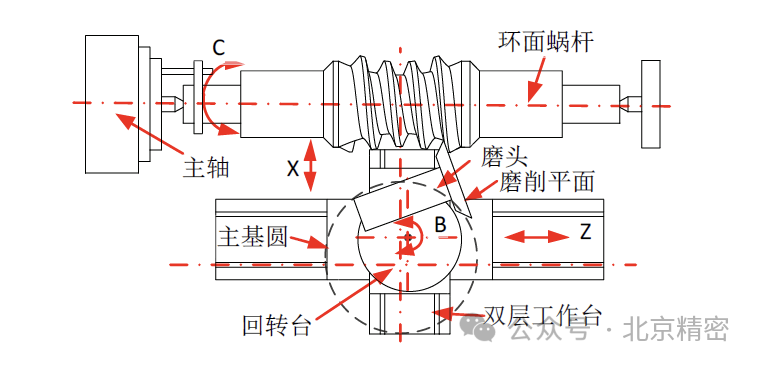
圖8 虛擬回轉中心磨削示意圖
虛擬回轉中心技術的出現也推動了平面包絡環面蝸桿車削和銑削技術的發展。將磨頭更換為車刀就可以進行平面包絡環面蝸桿的粗車,更換為銑刀盤就可以進行快速銑削。
2.1.3 五軸聯動加工技術
平面包絡環面蝸桿齒面為可展直紋面,因此就可以在五軸聯動加工中心上進行側銑加工。首先通過計算得到蝸桿齒面上瞬時接觸線的方程,然后控制側銑刀刀具路徑就可以進行銑削加工。粗加工的側銑刀具路徑通過瞬時接觸線沿齒面法向偏置粗加工余量的距離產生,精加工的路徑是由刀具側刃完全與瞬時接觸線重合而產生。該技術解決了精加工時加工余量不均勻的問題,提高了精加工效率和精度。
2.1.4 平面二次包絡蝸輪銑削技術
加工大型、單件或小批量的平面二次包絡蝸輪時滾刀的制造成本比較高,故適合對蝸輪進行數控銑削加工。數控銑削技術的基本思路是建立平面二次包絡蝸輪的模型之后,依據模型對加工路徑進行規劃,然后在數控機床上使用普通刀具對毛坯進行數控切削。作者在配備第四軸的立式加工中心上對II型傳動蝸輪進行了銑削加工。滾切和銑削后的蝸輪對比如圖9所示,左側為滾切得到的蝸輪。通過比可以發現,銑削的蝸輪齒面不再存在切削棱,而且可以定量切除一界曲線及其附近區域。銑削的蝸輪跑合半小時內傳動性能即可達到設計要求。
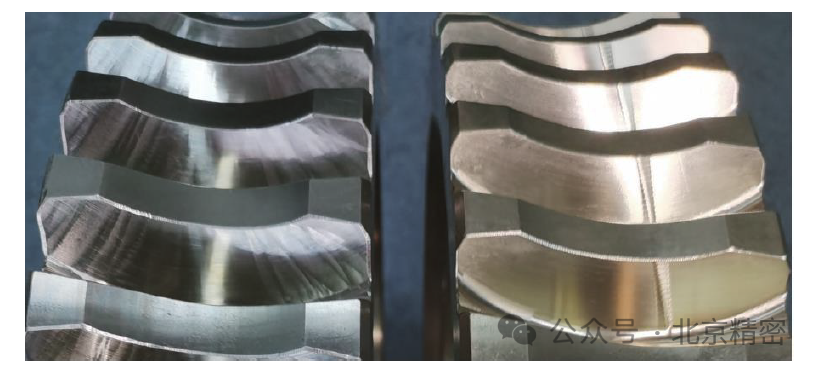
圖9 滾切與銑削蝸輪對比
2.1.5 平面二次包絡蝸輪滾刀后角數控鏟磨技術
平面二次包絡蝸輪滾刀后角的鏟磨一直是制約平面二次包絡環面蝸桿傳動推廣應用的難點之一。 采用虛擬回轉中心技術可以實現平面二次包絡蝸輪滾刀后角數控磨削。在采用虛擬回轉中心技術的環面蝸桿磨床上,通過控制4個軸的相對位置,使砂輪磨削平面的法矢量始終與刀齒后刀面在刃帶線處的法矢量平行以保證后角角度,砂輪磨削平面始終與刃帶線上的點相接觸以保證磨削滿足刃帶寬度的要求,且使砂輪回轉邊緣始終與滾刀齒根相切,以限定砂輪的位置,防止漏切或干涉。數控鏟磨試驗得到的滾刀如圖10所示。由于平面包絡環面蝸桿齒面磨削設備的砂輪半徑比較大,當滾刀容屑槽數大于4或螺旋角比較大時,后角鏟磨就會存在干涉現象。此時就需要對加工設備進行適當的改造或采用新的技術手段。
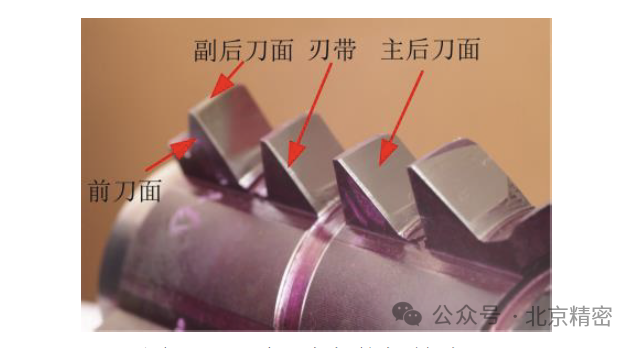
圖10 平面二次包絡蝸輪滾刀
螺旋槽前刀面可以改善刀齒分度環面上各點處的前角,但是齒頂和齒根處的前角依然無法均衡。采用變速比的加工方法則可以使得每排刀齒左右兩側的前角都近似為0°,從而改善切削條件。對于裝配式平面二次包絡蝸輪滾刀還可以通過對刀片進行前期的加工成型來避免后期的后角鏟磨。
2.2. 制造技術對比分析
對平面包絡環面蝸桿的五種制造技術進行對比,如表3所示。 通過分析可以發現,先采用數控車削技術進行粗車粗車,然后采用虛擬回轉中心技術進行精磨是較經濟的一種加工方式。
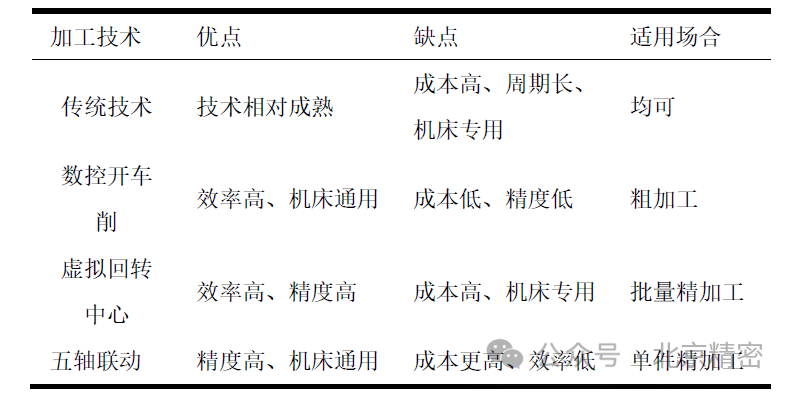
表3 蝸桿加工方式對比
平面二次包絡蝸輪的加工可以分為如表4所示的飛刀、滾刀、剃齒刀、銑刀和研輪共五種方式,不同方式的優缺點和適用場合如表4所示。

表4 蝸輪加工方式對比
通過對比可以發現滾刀滾切仍然是批量制造下平面二次包絡蝸輪最經濟的加工方式,這也是目前制造企業普遍使用的一種方式。當小批量時更適合采用數控銑削加工。
2.3. 蝸輪副裝配技術
受制造誤差和安裝誤差的影響,平面包絡環面蝸桿和平面二次包絡蝸輪裝配后需要根據齒面接觸情況來進行適當調整。研究發現中心距、蝸輪喉平面、蝸桿喉平面和軸交角誤差共4項安裝誤差導致的接觸區和傳動誤差曲線的變化規律是不一致的。結合接觸分布規律,當蝸桿副安裝階段接觸斑點不符合設計要求時調整蝸桿副的相對位置可以改善接觸斑點分布。在蝸桿的制造階段,應控制誤差曲線的走向,在滿足精度要求的情況下使蝸桿入口齒頂偏低。在設計階段則需要控制蝸桿加工中心距的公差使其為正值,主基圓直徑的公差也為正值,從而降低安裝誤差造成的潛在影響。
2.4. 潤滑油
平面二次包絡環面蝸桿傳動比同型號的圓柱蝸桿傳動對潤滑油的性能要求高. 試驗發現相對于聚α-烯烴合成油,采用聚乙二醇合成油時其傳動效率會提高4.5%左右,溫升降低150C。采用礦物油時其傳動效率則會降低10%左右,溫升提高580C以上。長期連續工作的平面二次包絡環面蝸桿減速器采用聚乙二醇合成油性能更佳,礦物油僅適用于非連續工作且負載較低的場合,當采取散熱措施后可以使用聚α-烯烴合成油。
3. 測量技術方面
平面包絡環面蝸桿沿蝸桿軸向不同位置的齒形、齒距、齒厚各不相等,制造誤差的檢測比較復雜,這一問題始終限制著行業的發展。近年來在平面包絡環面蝸桿及平面二次包絡蝸輪滾刀的誤差測量以及平面二次包絡環面蝸輪副的誤差測量方面也取得了一系列的進展。
3.1. 蝸桿及滾刀誤差測量
坐標測量法具有通用性強、主機結構簡單、測量精度高的特點,適合于平面包絡環面蝸桿齒面精度的測量。這種測量方式可以在三坐標測量機、齒輪測量中心或專用的測量儀上進行。相對于三坐標測量機,齒輪測量中心和專用測量儀的測量效率高,更適合于平面包絡環面蝸桿的測量。北京工業大學團隊針對平面包絡環面蝸桿和平面二次包絡蝸輪滾刀誤差的測量問題,研制了如圖11所示的環面蝸桿和滾刀檢測儀。該檢測儀為臥式結構,機械系統主要包括徑向(X軸)、軸向(Z軸)、豎直方向(Y軸)3個方向的移動軸和一個回轉軸軸。該儀器以電子展成法為基礎。測量時首先沿豎直方向(Y軸)移動測頭,使其在過蝸桿軸線的水平面內。然后控制測頭沿X、Z軸移動,同時蝸桿沿軸轉動。利用測量軟件再對光柵尺和測頭采集的數據分析處理就實現了對齒面誤差的測量。該儀器可以檢測平面包絡環面蝸桿的螺旋線誤差、對稱軸截面喉部齒形誤差、分度誤差和拓撲誤差,平面二次包絡蝸輪滾刀的螺旋線誤差、刃口齒形誤差和容屑槽周節誤差。通過開發相應的軟件還可以實現對平面二次包絡蝸輪齒面誤差的測量。該儀器投入生產應用8年多來有效解決了齒面精度的測量問題。
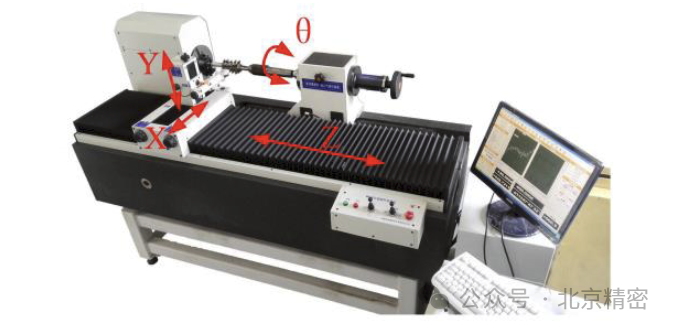
圖11 環面蝸桿和滾刀測量儀
進一步的研究發現中心距、傳動比、母平面傾角、主基圓直徑和喉平面位置五項工藝系統參數誤差導致的環面蝸桿齒面拓撲誤差的變化規律是不一致的,而且五項工藝系統參數誤差導致的蝸桿分度螺旋線和軸對稱截面喉部齒廓誤差的變化規律可以來表征整個齒面的變化。基于環面蝸桿和滾刀檢測儀的測量數據,通過誤差溯源,得出了需要調整的工藝系統參數的數值。將其輸入到采用虛擬回轉中心技術的數控磨床中進行誤差反調,使平面包絡環面蝸桿的螺旋形誤差和軸向齒形誤差達到了6級精度,并實現了批量化生產。最終試驗用平面二次包絡環面蝸桿減速器的傳動效率比國家標準高了近7個百分點。
3.2. 蝸輪副誤差測量
20世紀90年代研制的二次包絡環面蝸桿副測量儀采用平面測頭測量平面包絡環面蝸桿的切向綜合誤差。近年國內個別廠家也研制了一種環面蝸輪副檢測設備。通過分析蝸輪和蝸桿的轉角的位置關系來測量環面蝸輪副的切向綜合誤差和一齒切向綜合誤差。此外利用沿蝸桿徑向移動的滑臺上的光柵尺來測量蝸輪副的中心距誤差,給蝸輪副涂色后查看其接觸斑點的分布。
4. 需要進一步研究的問題
20世紀90年代研制的二次包絡環面蝸桿副測量儀采用平面測頭測量平面包絡環面蝸桿的切向綜合誤差。近年國內個別廠家也研制了一種環面蝸輪副檢測設備。通過分析蝸輪和蝸桿的轉角的位置關系來測量環面蝸輪副的切向綜合誤差和一齒切向綜合誤差。此外利用沿蝸桿徑向移動的滑臺上的光柵尺來測量蝸輪副的中心距誤差,給蝸輪副涂色后查看其接觸斑點的分布。
4.1. 技術標準體系完善
技術標準是產業健康、規范發展的有力保障。平面二次包絡環面蝸桿傳動精度檢測標準于1996年頒布,至今已有20多年。隨著技術的發展,當年制定的精度標準已經偏低,需要結合新型檢測設備和技術進行完善。目前平面二次包絡環面蝸桿傳動的設計參數仍不統一,不同廠家生產的的平面包絡環面蝸桿和平面二次包絡蝸輪不具備互換性,而且尚未形成系列化、標準化產品。通過制定參數標準可以提高全行業產品的互換性。此外也需制定平面二次包絡蝸輪以及滾刀和新型加工設備的檢驗標準。
4.2. 工業軟件開發
經過多年實踐,作者先后開發了數控開齒宏程序、虛擬回轉中心磨削程序,以及設計參數分析、蝸桿誤差仿真與反調修正、蝸桿副安裝誤差影響分析、蝸輪數控銑削、滾刀刀片設計等軟件,并投入生產應用。雖然解決了制造過程中的難點問題,但是尚未實現整個領域相關軟件的整合,也尚未真正完全實現閉環制造。開發成熟的設計和制造工藝軟件,進行知識固化,有利于技術的推廣應用。
5. 結束語
1)近年來針對平面包絡環面蝸桿、平面二次包絡蝸輪以及滾刀的加工制造出現了多種新型數控加工方式和裝備,檢測技術和儀器也有了突破, 但是技術仍不夠成熟和完善。
2)隨著技術的發展,平面二次包絡環面蝸桿傳動在完善技術標準體系、開發工業軟件后,其傳動性能將進一步提高,制造成本將進一步降低。
3)輕量化、高效和使用壽命長是國內外齒輪行業的發展方向。平面二次包絡環面蝸桿傳動作為一種高性能傳動方式,其自身的特點正符合這種發展趨勢。通過技術的不斷創新,構建集設計、制造和檢測于一體的閉環系統,實現其高效、高精制造,將極大推動環面蝸桿傳動事業的發展。