一、問題背景
根據反饋,某汽車用執行器機構出現異響情況,對故障件進行拆解發現執行器內部齒輪(2#/3#,如圖1所示深色零件)出現斷裂故障,進而導致異響。
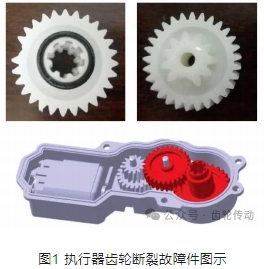
二、問題原因分析
總體分析思路
如圖2所示,按照人、機、料、法、環等因素,從齒輪制造、結構設計、使用工況、電器控制邏輯設計等方面進行全面分析和排查。
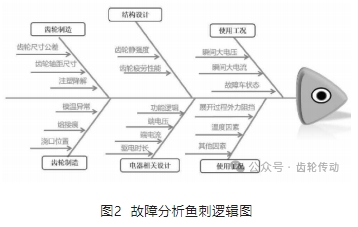
故障件斷面排查
(1)故障件齒輪斷口排查 如圖3及圖4所示,經過顯微鏡對斷口進行掃描分析,確認斷裂形式為脆性斷裂,材料結晶度狀態良好。齒面及斷口無明顯缺料等工藝缺陷。
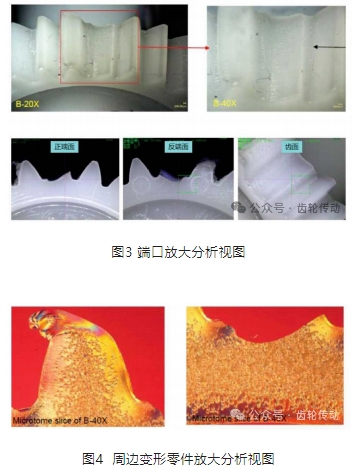
(2)故障件材料孔隙排查 如圖5所示,塑料產品在注塑時因工藝原因會存在氣孔等缺陷,嚴重的會影響產品整體強度。經過對故障件進行工業 CT掃描,分析故障件各斷面孔隙率及孔隙大小,發現其符合注塑要求,未現明顯缺陷。
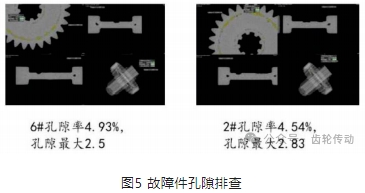
齒輪制造
(1)故障件模具排查
對故障件模具進行排查,以確認模具是否存在影響齒輪強度的風險點,經過對故障對應模腔齒輪模具放大及掃描觀察,未發現明顯影響齒輪強度的缺陷點,如圖6所示。
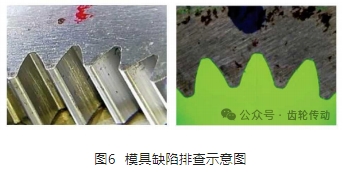
(2)齒輪注塑工藝排查
注塑件注塑過程中的缺陷對產品強度存在很大影響。主要影響因素如料溫、注射壓力、注射時間、注射速度、保壓時間、冷卻時間、模具溫度等,邀請材料專家對以上因素進行實地驗證及評估,未發現明顯異常因素。
對生產記錄進行排查未發現異常生產中斷等影響產品質量的事項發生。
對材料重量進行分析計算,排除了材料降解的可能性,在此不做詳述。
(3)故障件齒輪尺寸排查
1)執行器齒輪組中心距尺寸排查。執行器齒輪組中心距對齒輪產品耐久性存在較大影響,中心距偏小容易導致齒輪組嚙合出現根切現象進而導致執行器動作卡滯甚至齒輪斷裂問題,中心距偏大容易導致齒輪運行中出現撞擊進而影響齒輪組耐久性。
對故障件同批次零件中心距進行排查,滿足設計要求,在此不再詳述。
2)執行器齒輪齒形排查。如圖7所示,對故障件齒輪齒形進行排查,發現其滿足設計要求。
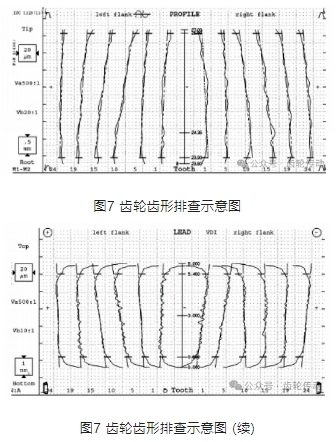
材料符合性排查
在材料符合性排查中,結合了兩種方法進行材料成分分析和材料特性分析,分別為傅立葉變換紅外吸收光譜分析 (FTIR, 如圖8所示)以及差示掃描熱法 (DSC, 如圖9所示)。經過分析排查,發現故障件材料與設計材料相符。
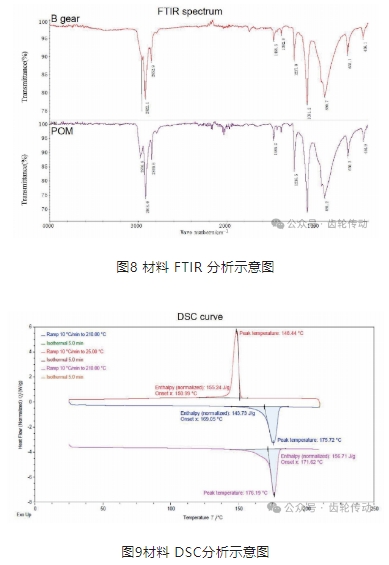
執行器在車輛上的運行工況排查
車輛在點火、熄火工況下其電壓存在差異,本節主要排查車輛在不同工況下是否存在高電壓導致執行器扭矩超差進而導致齒輪組超載導致的耐久性能降低問題。
經過對至少30臺車輛的排查,通過示波器測量執行器插接器處的輸入電壓和電流,發現其工作電壓均滿足執行器允許工作電壓區間,如圖10~圖13所示。
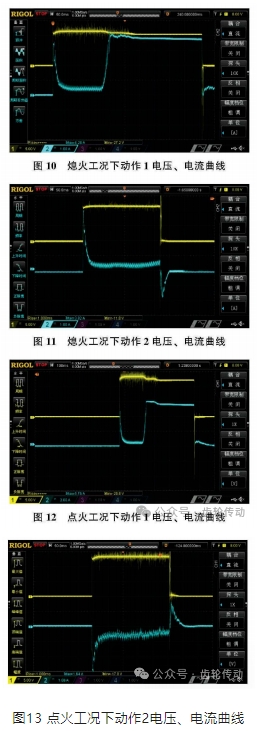
從以上電壓、電流曲線圖可以看出,車輛在點火工況下其工作電壓較熄火工況下高。另外,不論在熄火還是點火工況下,動作1均存在明顯堵轉現象,可能會影響產品性能。
執行器電機扭矩排查
經過對同批次電機進行抽檢,測量20件電機產品,發現其輸出扭矩、轉速均在設計范圍內,在此不再詳述。
執行器控制邏輯排查
對該執行器控制邏輯進行排查,發現動作1過程中存在明顯堵轉(供電時間500ms, 實際動作所需時間320ms), 而動作2無堵轉(位置開關信號檢測到即斷電),以上與實車測量結果相吻合,如圖14所示。
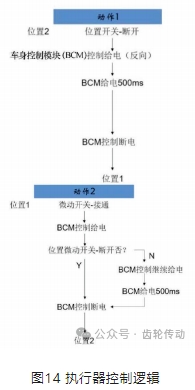
執行器齒輪組強度校核
該節通過靜態強度以及疲勞強度方面進行分析,判斷齒輪組強度是否滿足耐久性要求。
(1)齒輪組靜態強度校核 通過CAE 手段分析齒輪組靜態強度,發現其靜態應力小于材料許用應力,安全系數約為1.3,如圖15所示。
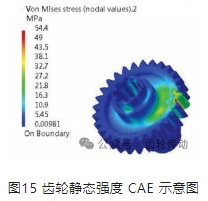
(2)齒輪組疲勞強度校核 如圖16所示,通過CAE手段分析齒輪疲勞強度,發現其在2.7節所述存在堵轉工況的控制邏輯下,材料實際應力超出材料許用應力3倍以上,導致其耐疲勞性能不滿足要求。
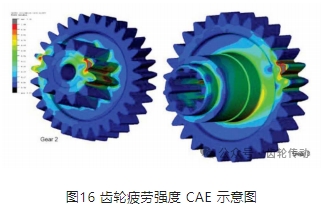
分析總結
從上述分析可以看出,出現該故障的原因是其控制邏輯中存在堵轉工況,而執行器齒輪組疲勞強度無法滿足堵轉工況下的耐久性要求。
三、執行器整改方案
根據原因分析情況看,解決執行器耐久性能存在兩種方法,第一種方法為增強執行器齒輪組強度,第二種方法為通過改善控制策略,消除堵轉工況。兩種方法進行對比,第一種需要重新設計齒輪組,會導致執行器尺寸增大,另外開發成本也大幅增加,經濟性差,而第二種方法相對僅需要修正軟件控制邏輯,經濟性和操作性也更好。
而對于第二種方法,我們制定了三種子方案進行嘗試驗證。
方案一 :降低堵轉時間
該方案僅修改動作2的 BCM 給電時間,從而降低堵轉時間(執行器動作所需時間約為320ms, 堵轉時間約為 30ms, 如圖17所示),經過臺架耐久及實車耐久驗證,故障已消除,效果明顯。
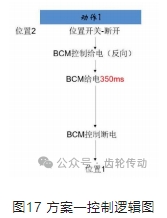
方案二:消除堵轉工況
執行器所需電器件增加位置開關,使其在位置1及位置 2均可通過感應位置開關及時斷電,消除堵轉工況,經過臺架耐久及實車耐久驗證,故障已消除,效果明顯。
方案三:通過脈沖寬度調制 (PWM) 調速控制降低輸出扭矩
更換執行器控制模塊,采用具備PWM 調速控制的模塊進行控制(供電波形如圖18所示),降低正常使用有效電壓,進而降低執行器輸出扭矩,提升耐久性能。經過臺架耐久及實車耐久驗證,故障已消除,效果明顯。另外通過調速控制,除了解決耐久性問題,還大幅降低了執行器動作聲(對比如圖19所示)。
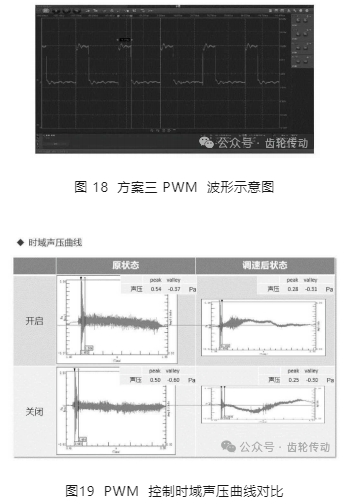
四、總結
本文結合某汽車用執行器齒輪斷裂問題分析及整改過程,簡要說明了執行器類零件的耐久性能排查思路及其解決措施。希望能對行業內執行器類零件開發工作提供必要的支持和借鑒。
參考文獻略.