20 世紀 60 年代末,德累斯登工業大學提出漸開面包絡環面蝸桿傳動( TI 蝸桿傳動) 。該傳動具有多齒接觸、承載能力大、傳動效率高的優良特性,因而廣泛應用于制造裝備、船舶艦艇等國民經濟和國防裝備重要領域。
國內外學者長期致力于 TI 蝸桿傳動的嚙合性能、參數優化、三維建模、加工方法等方面的研究。日本 Maki 等對其嚙合性能、接觸線分布進行了詳細分析;朱炎、段路茜等分析了喉徑系數、螺旋角、法向模數、蝸輪齒寬等參數對 TI 蝸桿載荷分布的影響,并分別用改進粒子群算法和自適應算法對參數進行了優化;梁邦龍等利用數值計算數據點,借助三維造型軟件,探討了 TI 蝸桿的三維精確造型方法; Sun 等對 TI 蝸桿的包絡理論、邊界條件、嚙合性能、齒面的精確磨削方法和砂輪廓形等進行了全面深入的研究,研制了鋼-鋼配對的硬齒面 TI 蝸桿減速器樣機,并用試驗驗證該樣機在低載荷下具有優良的傳動性能;陳燕等建立了包括 TI 蝸桿傳動在內的各類包絡環面蝸桿的統一數學模型,探討了包絡環面蝸桿齒面以車代磨的實現原理,并以尼龍 TI 蝸桿為例進行了原理性驗證。
從上述研究現狀來看,國內外專家對 TI 蝸桿傳動的理論和試驗都有較為全面的研究,但對材料配對研究相對較少。文中針對 TI 蝸桿傳動,建立數學模型和精確三維實體模型,選用兩組不同材料配對,基于有限元法分析兩組材料配對形式下的接觸應力,并用疲勞破壞試驗進行驗證。
一、漸開線齒輪包絡環面蝸桿副數學模型
建立傳動副包絡展成過程的標架,如圖 1 所示, σm(om :xm ,ym ,zm ) 和 σn(on :xn ,yn ,zn ) 為空間固定標架,其底矢分別為 (im ,jm ,km ) 和(i n ,j n ,kn ) ;σ1(o1 :x1 , y1 ,z1 ) 和 σ2(o2 :x2 ,y2 ,z2 ) 為運動標架,其底矢分別為 (i 1 , j 1 ,k1 ) 和(i 2 , j 2 ,k2 ) ;漸開線齒輪與標架 σ1 固連, 角速度為 ω1 ,角位移為 φ1 ,環面蝸桿與標架 σ2 固連, 角速度為 ω2 ,角位移為 φ2 ,且 φ2 / φ1 = ω2 / ω1 =z1 / z2 =i 21 ,z1 為漸開線齒輪齒數,z2 為蝸桿頭數,i 21 為傳動比, a 為中心距。
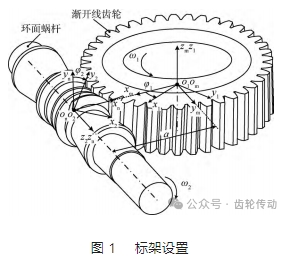
漸開線齒輪齒面方程為:
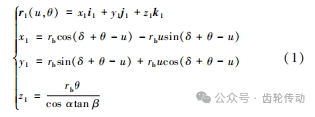
式中:u,θ ———漸開線齒輪的齒面參數;
δ ———位置關系角;
rb , β ———漸開線齒輪的基圓半徑和分度圓螺旋角;
α———分度圓壓力角。
根據齒輪嚙合原理,可得嚙合函數為:
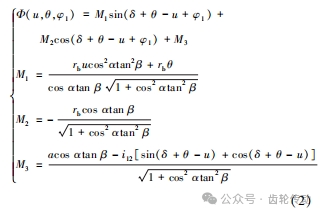
聯立式(1) 、式( 2) ,可得漸開線齒輪齒面接觸線方程為:

根據圖 1 所示的坐標變換關系,將漸開線齒輪齒面接觸線方程式(3)變換到蝸桿固連標架 σ2 中,可得環面蝸桿齒面方程式為:
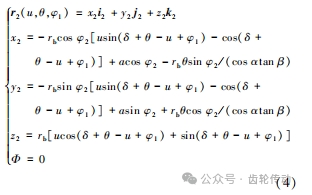
二、傳動副接觸特性分析
傳動副有限元模型
根據環面蝸桿齒面方程,求解系列螺旋離散點,按照點—線—面—體的方式建立傳動副精確三維模型,依據接觸齒對進行簡化,對簡化模型進行六面體網格劃分;齒面按 0. 5 mm×0. 5 mm×0. 5 mm 進行劃分,其他區域按 0. 8 ~ 1 mm 的邊長進行劃分,共 132. 9 萬個節點, 36. 0 萬個單元,簡化模型和有限元模型如圖 2 所示。
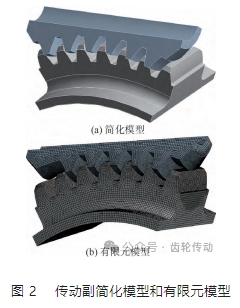
材料對傳動副齒面應力的影響
選用兩組材料配對來對比分析不同材料對傳動副接觸情況的影響,第 1 組齒輪和蝸桿均采用 42CrMo,氮化熱處理,第 2 組齒輪采用 QT600 - 3 , 蝸桿采用 42CrMo,氮化熱處理,各材料屬性如表 1 所示。
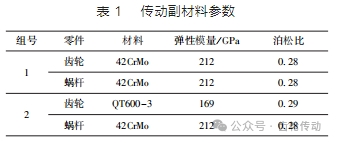
限制蝸桿內孔所有自由度,限制齒輪的軸向移動, 僅保留其周向的旋轉自由度, 并在齒輪周向施加 28 000 N·m 的轉矩,可得兩組材料情況下齒面的應力情況,如圖 3 所示。由圖可知,在相同的網格尺寸、相同的加載條件下,第 1 組材料的齒輪齒面和蝸桿齒面最大等效應力分別為 2 182 MPa 和 3 114 MPa,第 2 組 2 材料的齒輪齒面和蝸桿齒面最大等效應力分別為 175 MPa 和 2 931 MPa,應力最大值均勻分布在齒頂和齒根的邊沿,這是由于傳動副輪齒的邊沿接觸產生的; 采用第 2 組材料時,齒輪和蝸桿的最大應力均有所下降,蝸桿應力下降程度較為明顯,齒輪應力雖然也有所下降,但是變化不大。整體來說,傳動副在采用第 2 組材料配對形式時,齒面等效應力較小,受力狀況也較好。
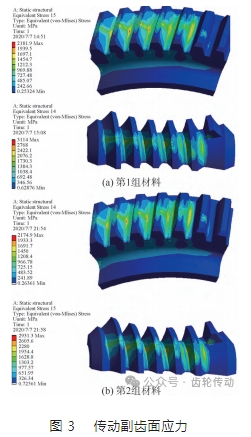
材料對傳動副齒面應變的影響
基于表 1 的材料配對,并添加相同的約束條件和載荷,求解得到兩組材料配對下的齒面等效應變云圖如圖 4 所示??梢钥闯?第 1 組材料齒面最大應變為 0. 014 9 mm,第 2 組材料齒面最大應變為 0.014 2 mm, 均產生于根部。

三傳動副疲勞破壞試驗
在齒輪嚙合儀上對傳動副進行對檢,其接觸斑點如圖 5 所示,接觸斑點分布與圖 3 有限元分析結果吻合。在浙江恒豐泰減速機制造有限公司搭建傳動副的疲勞測試試驗臺,按照要求評估超過 25 年設計壽命, 用來測試樣機的磨損情況和耐用性,如圖 6 所示。試驗分兩步,首先進行耐用性測試,按照超過 25 年的設計壽命要求,在齒輪試驗機上進行傳動副的負荷運轉試驗,考察齒面的磨損情況;然后進行疲勞破壞試驗, 在樣機自鎖情況下持續靜態加載直至斷齒,試驗機停止運行,考察輪齒折斷情況。
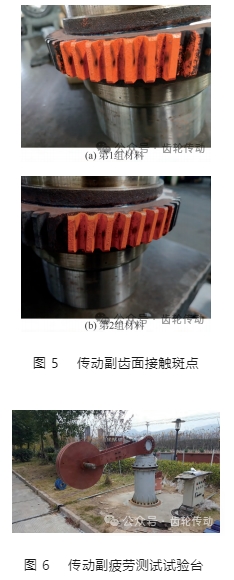
兩組不同材料的傳動副負荷加載量級和加載方法完全相同,轉矩從 1 000 N·m 開始加載,步長為 1 000, 加載到 5 000 N·m,蝸桿軸轉數與轉矩加載的對應關系如表 2 所示。按照 25 年設計壽命的負荷運載,兩組材料齒面的磨損情況如圖 7 所示,兩組傳動副斷齒出現的負荷量級相同,均為 28 000 N·m,其折斷情況如圖 8 所示。由圖 7 和圖 8 可知:第 1 組材料傳動副漸開線齒輪輪齒斷齒數量較多,齒輪齒面磨損更為嚴重;第 2 組材料傳動副漸開線齒輪有 2 顆齒斷齒,相對第 1 組材料而言,蝸桿和齒輪齒面磨損較輕,兩組材料斷齒均從齒根折斷;從磨損情況、折斷數目與折斷位置來看, 與前述有限元應力應變分析結果吻合。
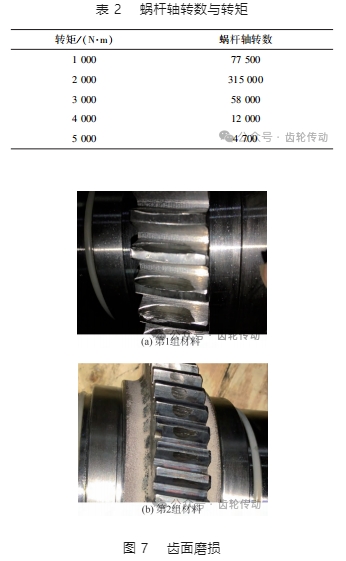
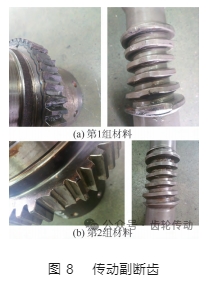
四、結論
針對 TI 蝸桿傳動,建立其數學模型,根據數學模型創建精確三維模型,分析兩組不同材料情況下傳動副的齒面應力情況,并進行傳動副的疲勞破壞試驗,主要結論如下:
(1)齒輪和蝸桿均采用 42CrMo 的材料配對,與齒輪采用 QT600-3,蝸桿采用 42CrMo,氮化熱處理的材料配對相比較,后者齒面應力應變均較小。
(2)兩組材料傳動副輪齒折斷出現的載荷級相同,均從根部折斷,且第 1 組材料漸開線齒輪折斷齒數較多,蝸桿和齒輪齒面磨損較為嚴重,與應力應變分析結果相吻合。
參考文獻略.