隨著科技的發展,人們對汽車的駕駛體驗提出了更高的要求,汽車噪聲也逐漸成為影響整車駕駛舒適性的重要因素之一。除了汽車行駛過程中的風噪和輪胎與地面的摩擦噪聲,變速箱齒輪嘯叫也是汽車噪聲的主要來源之一。
在動力傳輸過程中,變速箱齒輪嚙合過程中的高頻振動和齒輪傳遞誤差造成的沖擊,是變速箱噪聲的來源。除了改善齒輪的宏觀參數,以及對齒輪進行微觀修形以減小傳遞誤差,改善齒輪(軸)的裝配方法,提高齒軸系統的整體剛度也有益于變速箱NVH性能的改善。
本文從某型號CVT變速箱的噪聲問題入手,首先,通過瀑布圖鎖定了噪聲產生的位置為小齒輪軸。其次,通過測量小齒輪軸端面與軸承支架的表面的平行度,發現小齒輪軸的偏移現象。再次,根據“螺栓 541 原則”分析了變速箱殼體與小齒輪軸支架接合面粗糙度對螺栓預緊力的影響。最后,結合有限元仿真與實驗,驗證了通過改變殼體與小齒輪軸支架接合面粗糙度,以增大螺栓預緊力,并降低小齒輪軸偏移的可行性。
一、變速器嘯叫問題分析
汽車變速箱噪聲是在變速箱內部多重激勵的同時作用下產生的,其內部激勵包括內部剛度激勵,齒輪高頻嚙合接觸激勵與齒輪軸錯位導致的傳遞誤差激勵。
某型號的CVT變速箱出現了零公里噪聲問題,變速箱運行過程中的嘯叫明顯,噪聲評價不合格。從實測的噪聲瀑布圖中可以觀察到,在23階、41階和82階 的噪聲曲線明顯;根據NVH階次跟蹤,在23階、41階、82階存在多項噪聲超差;EOL復測結果也證明,這3個 階次的噪聲均大于標準值,如表1所示。
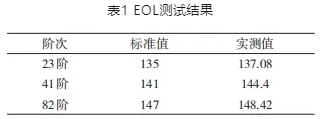
通過對NVH階次數據的分析,并結合瀑布圖可以判斷變速箱噪聲的來源是小齒輪軸,其中噪聲的階次對應著小齒輪的倍頻。為了驗證這一判斷的正確性,并找出小齒輪軸噪聲問題根源,對故障件進行拆箱檢查,并分配一臺正常件作為對照組。
該型號變速箱的小齒輪軸結構剖視圖,如圖1所示,圖中綠色部分為小齒輪軸,軸的左端面通過圓錐滾子軸承與變速箱殼體連接,右端與支架連接;小齒輪軸支架通過5個螺栓固定在殼體上。
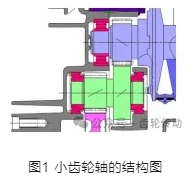
在小齒輪軸的齒面上涂藍油并進行嚙合測試,運轉后差速器齒輪與小齒輪有一半不能完全嚙合,該現象說明小齒輪軸發生了偏移,導致較大的傳遞誤差,并成為齒輪嚙合過程中,噪聲的激勵源。
表2為小齒輪端面與殼體的平行度對比。其中,噪聲故障件的平行度偏差為0.059,遠大于正常件;對故障件進行重新安裝后平行度恢復到0.02。經過重新裝配后,故障件的嘯叫消除。由此可以得出,軸承座偏移導致軸系傾斜最終發生齒輪噪聲問題。

由于軸承座通過5個螺栓固定在殼體上,偏移主要原因可以歸結于螺栓的預緊力不足。如圖2所示,根據541原則,螺栓在添加擰緊力矩的過程中,實際轉化為螺栓夾緊力的扭矩僅占10%,另有50%用于克服螺栓法蘭面與被夾緊物體表面的摩擦力,另外40%用于克服螺紋副中的摩擦力,如果采用一定的改善措施(如涂抹潤滑油)或螺紋副中存有缺陷(如雜質、磕碰等),該比例關系會受到不同影響而改變。

為了提高螺栓的夾緊力,預防軸承座偏移的發生,除了增大預緊扭矩外,還可以采取以下措施。本案例中使用帶法蘭面的金屬螺栓,其中螺栓的法蘭面與小齒輪軸承座的上表面接觸,依據上述的541法則,減小螺栓法蘭面與軸承座上表面的粗糙度,可以有效降低 這兩個結合面之間的摩擦系數,從而降低用于克服螺栓法蘭面與被夾緊物體表面的摩擦力的占比,提高夾緊力。此外,還可以增加軸承座下端面與殼體接合面的表面粗糙度,增大軸承座與殼體間的最大靜摩擦力,來預防偏移。
二、仿真分析
軸承支座與殼體結構具體見圖3。由上述測量分析可知,軸承支座的滑動變形可能是螺栓的軸向預緊力不夠,根據541螺栓法則,其根本原因可歸結為螺栓頭法蘭面與軸承支座面的摩擦過大;軸承支座的滑動變形也可能是軸承支座與殼體的摩擦力不足。軸承支座的滑動變形量大小直接影響著齒輪軸的傾斜程度,對噪聲的產生起著至關重要的作用。為此,使用ANSYS 軟件對不同摩擦系數的軸承支座和殼體進行有限元分析,探究它們的滑動變形情況。
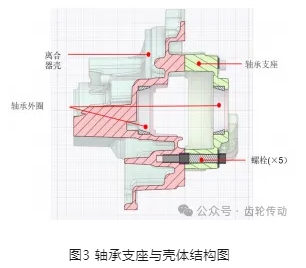
考慮螺栓預緊力不足,在ANSYS中設置了18 kN、23 kN和28 kN這3種螺栓預緊力,結果如圖4所示。
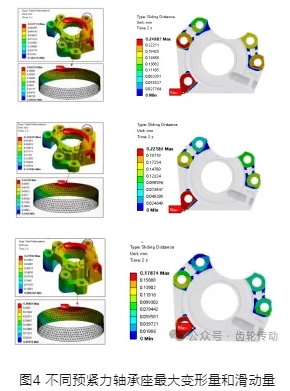
通過對上述云圖的整理匯總,得到了不同預緊力軸承座最大變形量和滑動量的表格,如表3所示。
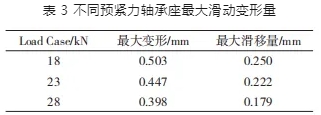
從表3數據可以看出,預緊力越大,軸承座的最大變形量、與離殼的最大滑移量越小,小的變動量可以抑制軸系的傾斜,減小噪聲產生,這充分表明了螺栓預緊力不足是噪聲產生的重要原因。根據541螺栓法則,螺栓預緊力的不足是由于需要克服的阻力太大,其中螺栓頭法蘭與殼體的摩擦阻力占到了40%,這是導致預緊力缺乏的根本原因。為此,使用ANSYS對不同摩擦系數的螺栓與軸承支座接觸面、軸承支座與殼體接觸面進行數值分析,探究其對軸承支座滑動變形的影響。
螺栓與軸承支座接觸面的摩擦系數 μ1分別設置為 0.1 和 0.25,軸承支座與殼體接觸面 μ2分別設置成 0.1和0.3,邊界條件設置相同,將μ1和μ2排列成不同的組合,為了排除預緊力帶來的影響,同時也設置了兩組預緊力做對比分析,經過ANSYS軟件分析后得到如圖 5所示的變形云圖。
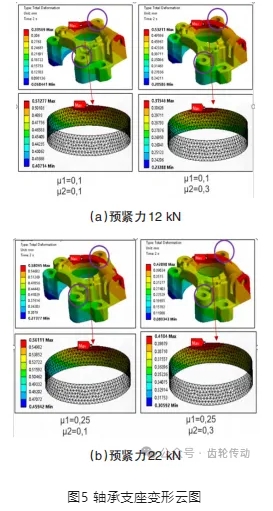
在相同的摩擦系數下,通過ANSYS對軸承支座的滑動情況也進行了分析,分析結果見圖6。
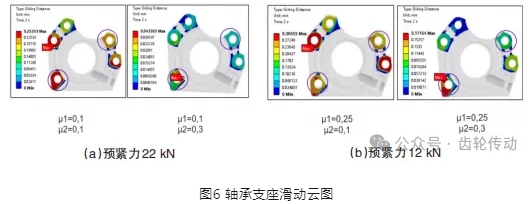
從圖6可以看出,不同的摩擦系數對軸承支座的變形量與滑動量會產生很大的影響,如表4所示。
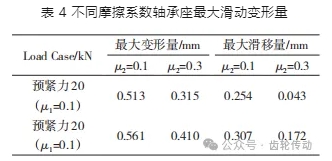
從表4中可以看出,在μ1相同為0.1的情況下,隨著軸承支座和殼體摩擦系數的增大,兩者之間的滑動量由 0.254 降低到了 0.043,軸承支座的最大變形量由 0.513降低到了0.315,對于不同的預緊力12.08 kN和摩擦系數μ1=0.25,趨勢依然相同,這表明較大的μ2摩擦系數可以抑制軸系傾斜,對減弱噪聲起到非常重要的作用,這也體現出軸承支座與殼體的摩擦系數是本案例噪聲產生的重要原因。
三、實驗驗證
根據測量結果和仿真結果,可以判斷螺栓擰緊力、軸承座端面與殼體之間的摩擦系數即兩者結合面的粗糙度會影響變速箱噪聲,為進一步驗證結果,筆者進行了以下實驗:實驗使用砂紙對軸承座和殼體接合面進行打磨,增大殼體間摩擦力,其次在螺栓法蘭端面抹油,減小螺栓與軸承座間的摩擦力,增加螺栓擰緊力矩,由 38 N·m 增加到 42 N·m;完成以上措施后,將變速箱裝配完成,到產線進行EOL測試。軸承座打磨前粗糙度是 0.297,打磨后的粗糙度是 0.85,進行測試后與之前數據進行對比,如表5所示。
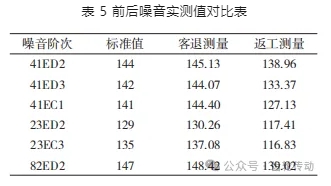
返工后的變速箱在進行 EOL 測試的數據均出現了下降,驗證了之前測量結果和仿真結果的正確性。
四、結論
本文從裝配角度考慮噪聲產生的原因,通過仿真和實驗進行驗證,主要結論如下。
(1)實驗與仿真結果具有一致性,驗證了有限元模型的正確性。
(2)變速箱裝配過程中的螺栓預緊力和結合面粗糙度對噪聲的產生有很大的影響。
(3)增大軸承支座螺栓預緊力和結合面粗糙度可以有效抑制軸系傾斜,減少傳遞誤差,降低噪聲。
參考文獻略.