為了滿足直升機傳動系統輕量化的需求,作為直升機關鍵零部件的傳動齒輪具有薄壁的顯著特征,在切削加工中容易出現變形嚴重和尺寸精度難以保證的問題。本文以高強度中合金滲碳鋼齒輪薄輻板為研究對象,基于 ABAQUS 有限元分析軟件,開展了切削加工仿真研究,通過建立三維動態切削仿真模型,分析了加工過程中工件所受的切削力與切削參數之間的關系; 并運用靜態仿真分析了切削力和夾緊力疊加對薄輻板加工變形的影響,對仿真結果進行了極差分析。最后,通過開展試驗對仿真結果進行了驗證。結果表明: 齒輪薄輻板加工變形量靜力學分析顯示齒輪輻板軸向變形量最大,徑向變形在輪轂處最大; 極差分析發現,切削速度為 150 m /min、進給量為 0.06 mm /r、切削深度為 1.8 mm 為最優切削參數,最大變形量的預測誤差小于 10%。
在航空航天領域,保證飛行器足夠推重比的條件下,盡可能地減輕其零部件的重量,是重點發展的方向之一。齒輪薄輻板在航空發動機零部件中應用廣泛,具有重量輕、轉速高、載荷重的特點。航空高性能齒輪由于壁厚薄,在生產過程中存在剛性弱等問題,材料多使用高硬度、難加工的碳素鋼和合金鋼,其切削加工過程中極易產生變形、平行度和圓周度偏差過大等問題,這會導致齒輪輪轂區域出現偏心引起齒輪不平衡的振動,特別是輻板車削軸向變形較大,加工精度控制困難。為確保航空齒輪的加工精度,必須對加工變形進行控制。
近年來,國內外諸多學者從各方面對薄壁件加工性能和工藝優化進行了深入研究。加工性能方面,在對薄壁件變形研究加工結束后工件變形產生的影響,相比于初始殘余應力,切削殘余應力對于變形的影響較大。Masoudi 等通過測量工件上的殘余應力,研究殘余應力與變形之間的相關性,結果表明力和溫度對薄壁零件的殘余應力和變形有直接影響。在考慮薄壁齒輪和空心軸的齒輪動力學模型中,采用殼單元代替梁單元和集中質量單元建立齒輪-軸有限元模型,防止簡化薄壁結構,導致過大的臨界速度。王大勇建立了薄輻板結構的齒輪模型,根據動力學方程及載荷分配求解單個輪齒上的載荷歷程,并依據嚙合時間進行加載,模擬了齒輪正常工作條件下的受力狀態。工藝優化方面,廖凱等對航空鋁合金薄壁構件的幾 何形狀和加工表面應力進行研究,運用變形解析函數對薄壁構件加工變形程度進行預測性計算和分析,結果顯示,薄壁構件變形撓度與理論計算值偏差為 312 μm,偏差處于變形不確定度范圍內,解析函數準確性得到驗證。Li 等通過實驗測量薄壁件加工后一定時間內的變形規律,提出一種基于提高等效彎曲剛度的薄壁件加工變形控制方法。
Chen 等建立了一個動力學模型來預測薄壁零件加工變形,使用迭代計算考慮了切削力與加工變形之間的耦合關系。李承然等基于溫度場-滲碳場-組織場-應力應變場多場耦合模型,運用有限元仿真分析對 AISI9310 鋼薄輻板齒輪的熱處理過程進行了數值模擬,分析淬火過程輪齒組織與應力演變規律及冷處理和回火過程對輪齒組織含量和應力大小的影響,得到了齒輪熱處理后最終的殘余應力和變形。叢靖梅等提出了基于工況映射與薄殼應力貼合的殘余應力變形的仿真預測方法,實驗結果表明該方法能夠有效預測薄壁件的加工殘余應力變形。研究人員對齒輪各個部位的結構優化開展了較多的研究,但有關齒輪薄輻板的加工變形控制方面的文獻較少。現有的文獻多數采用實驗法在工藝上做工藝方案改善,缺乏針對薄壁輻板加工變形開展的研究。高性能齒輪生產過程中關于輻板較薄、切削時易變形、尺寸精度難以控制等問題的研究還有所欠缺,對于切削參數優化多數基于仿真實驗設計,缺少進行相關試驗驗證。
本研究基于 ABAQUS 仿真平臺,對航空齒輪鋼 18Cr2Ni4WA的切削過程進行有限元模擬,開展切削仿真研究,通過建立三維動態切削仿真模型,采用正交實驗設計,研究不同切削參數下的切削力以及加工變形量; 根據切削力與切削參數的對應關系,獲得切削參數與工件變形量之間的對應關系,進行了加工工藝參數的優化研究; 并運用靜態仿真分析,研究了切削力和夾緊力的疊加對薄輻板加工變形的影響; 最后對仿真結果進行了極差分析,通過試驗的方式對仿真結果進行了驗證。
一、齒輪薄輻板模型
齒輪模型
鑒于目前多數航空齒輪都會采用薄輻板的形式,本文基于某發動機附件傳動齒輪作為研究對象,對其車削加工工序引起的加工變形規律進行研究。薄壁齒輪的關鍵尺寸如圖 1 所示,整體直徑為 120 mm,齒厚為 20 mm,輪轂直徑為 29 mm。輻板加工區域直徑為 100 mm,齒胚輻板加工前厚度為 10 mm,使用三爪卡盤夾持,加工后厚度為 3 mm。
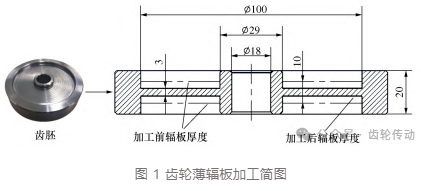
材料物理特性和本構模型
本文所研究的薄壁輻板齒輪材料為強度高、韌性好和淬透性好的中碳鋼 18Cr2Ni4WA,該材料經過復雜的化學熱處理后,坯料心部硬度達到 HRC31 ~ HRC41,表面硬度不低于 HRC60,以確保齒輪表面有較高硬度且心部呈現一定的韌性。然而,這也會給材料的切削加工帶來一定的困難,切削時表現出切削力大、切削溫度高,表面容易產生硬化現象,消耗功率大、摩擦劇烈、刀具磨損快等特點。
本構模型是金屬材料切削仿真模擬材料大塑形變形的關鍵,具有代表性的是 Johnson-Cook ( J-C) 本構模型和 Zerilli-Armstrong 模型,兩個本構模型都引入材料的應變硬化、應變率硬化和熱軟化參數。Zerilli-Armstrong 模型主要運用在體心立方及面心立方金屬,同時針對不同的晶體結構有著不同的表達形式; J-C 本構模型是使用經驗作為主要參考來源的本構模型,主要針對的是大應變、高應變率、高溫變形的材料,同時也能運用在各種晶體結構。J-C 本構模型的溫度適用范圍很廣,從室溫到材料熔點溫度范圍內都是有效的。三項乘積分別對應了應變硬化、應變率硬化和溫度軟化對材料流動應力的影響,適合用來模擬高應變率下的金屬材料。因此,綜合以上因素的比較,本文選用 J-C 本構模型來表達材料的本構關系,用連乘的方法關聯,綜合反映變形熱力參數之間的數量關系,其表達式為
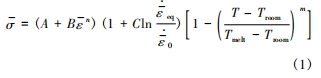
式中: 為等效流動應力;
為等效塑性應變;
為等效塑性應變率; Troom、Tmelt 和 T 分別為室溫、熔化溫度和當前溫度;
為材料的參考應變率 ( 10-3 s-1 ) ; 模型常數 A、B、C、n 和 m 分別為材料的屈服強度、應變硬化參數、應變率敏感系數、硬化參數和熱軟化系數。
18Cr2Ni4WA 材料的 J-C 本構參數如下: A = 1 010 MPa,B = 1 409 MPa,C = 0. 04,n = 0. 67,m = 1. 2。物理、力學、熱學參數見表 1。
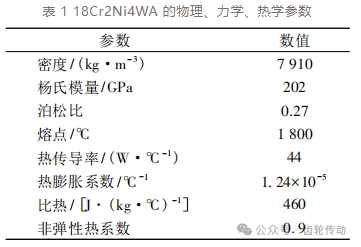
二、研究條件與方案
刀具選擇與切削方式
齒輪輻板具有深槽結構,使用普通外圓車刀加工會出現可達性差的問題,故選用端面切槽刀配合專用的端面切槽刀桿(見圖 2) 作為加工刀具組合,其中刀具選取金屬陶瓷刀具( C 型金屬陶瓷刀片 Al2O3+ZrO2 ) 。端面切槽在粗加工階段采用軸向進給的車削方式,首刀從最大直徑處開始向內加工,這一步需要產生連續切屑避免在窄槽中堵屑,特殊情況可以采用啄進式加工或人為設置暫停的方法。首刀后的每一刀設置為背吃刀量 ap 的 0. 6 ~ 0. 8 倍,vc 為切削速度; f 為進給量,具體原理如圖 3 所示。
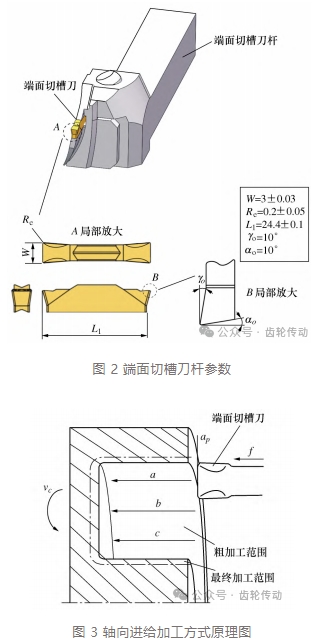
仿真參數
從切削的工藝參數角度考慮,使用單因素實驗設計方案來研究 3 個工藝參數對實際切削力的主要影響,這些參數涉及切削速度 vc,進給量 f 和切削深度 w。vc 值選取端面切槽推薦范圍 90 ~ 150 m /min,f 值選取端面切槽推薦值 0. 1 mm /r 附近的參數,w 的推薦值為背吃刀量 ap 的 0. 6~0. 8 倍。
為了充分考察切削三要素對切削力的影響,故每個因素取 4 個水平,設計三因素四水平正交實驗 L16( 43 ) ,試驗方案見表 2。
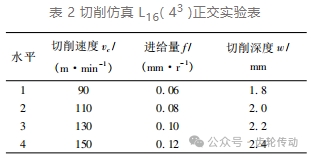
三、切削有限元仿真與試驗
三維切削有限元模型建立
建立工件三維有限元模型,分別建立切屑層和基體,通過綁定的方式連接在一起。由于齒輪的實際尺寸比較大,在動態切削仿真中將模型材料參數單位設置為 m,其中被加工工件厚度 0. 02 m,切屑層寬為 0. 015 m,其余位置為基體部分,仿真模型和網格劃分模型如圖 4 所示。三維有限元模型網格采用六面體單元,圓周方向網格布種尺寸為 0. 000 5 m,徑向方向網格布種尺寸為 0. 000 25 m,網格單元類型選擇為八結點熱耦合六面體單元 C3D8RT。仿真采用熱力耦合分析步,刀具剛切削工件時,切削力呈現上升趨勢,當刀具完全切入工件時,切削力才呈現出平穩狀態。為保證刀具能夠完全的切入工件,設置三維切削仿真時間及分析步時間為 0. 004 s。其中,刀具網格劃分模型設置為八結點熱耦合六面體為主的自由進階算法,采用單元 C3D8RT 進行劃分,仿真過程不考慮刀具磨損對加工的影響,所以設置刀具為剛體。約束材料基體底部、左側和右側邊線的自由度; 初始溫度設置為 20 ℃ ; 切屑層與刀具之間的摩擦符合庫倫摩擦定律,摩擦因數為 0. 2,建立三維正交仿真模型。
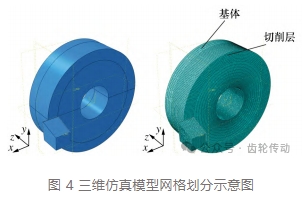
仿真結果
切屑形貌:以切削速度 vc = 90 m/min,進給量 f = 0. 06 mm/r,切削深度 w = 1. 8 mm 為例,得到的工件切削過程中等效應力分布云圖,如圖 5 所示。
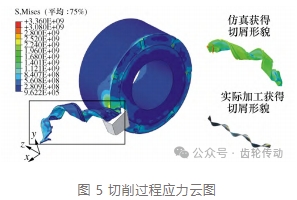
通過圖中特征可以發現,切屑類型為帶狀切屑形貌,切削層經塑性變形后被刀具分離,并隨前刀面流出。有限元仿真過程獲得的切屑形貌與實驗結果對比,如圖 5 所示。由圖 5 可以知: 仿真切屑形貌整體光滑,切屑較長時切屑呈螺旋狀卷曲,同時切屑邊緣并無明顯鋸齒狀毛刺,這些特征與切屑的實際形貌相吻合,說明仿真結果符合實際加工結果。
切削力:三維切削仿真提取的切削力結果如圖 6 所示。切削力方向以仿真模型方向為主。仿真過程中,隨著刀具開始切削,切削力快速增大,隨著切削過程逐漸平穩,切削力變化也逐漸趨于平穩,這和實際加工情況相符。當切削過程達到穩定狀態之后,切削力連續波動,由于切削過程中第一剪切區的高溫引起材料的熱軟化導致切削力下降。切削熱隨切削力的降低而降低,迫使熱軟化效應降低導致切削力增大,因此造成切削力的波動這種影響也反映在有限元模型中。在實際端面切槽加工中,切削深度相對于進給量大的多,吃刀抗力大,所以 y 方向的主切削力最大。
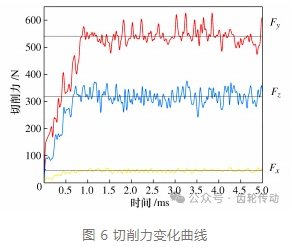
變形位移:在每一分析步中提取三維動態切削仿真中輸出的切削力,依次將切削力載荷分布到走刀路徑上的各個結點上,基于有限元求解計算,獲取輻板加工變形預測結果。仿真后得到車削加工的變形位移,如圖 7 所示。由圖 7 可知: 靠近齒輪輪轂位置變形量最大,輻板切削時切削力過大對輪轂的同軸度有很大的影響。
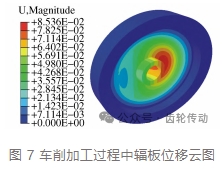
試驗設計
加工試驗開始之前,需要對所有待加工材料進行去應力退火處理,盡量消除工件內部初始殘余應力,減小對加工變形試驗結果的影響。加工完成后使用三坐標測量儀測量加工零件的尺寸精度,測量設備為 ZEISS 型號 SPECTRUM 測量機,使用 GOOD FIXTURE 定位臺進行定位,測量位置為基準面輻板。具體加工測量流程如圖 8 所示。
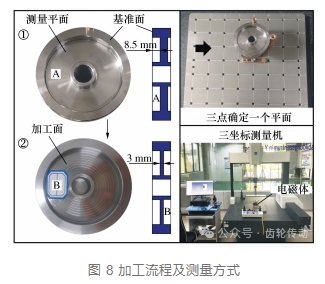
四、切削參數優化與試驗驗證
正交實驗結果
切削力與刀具參考點的作用力的關系為等大反向,故通過刀具參考點輸出切削運動方向切削分力 Fc、垂直切削運動方向切削分力 Ff,經計算得到切削分力在波動穩定區域的平均值。輻板變形量提取預測仿真模型中的最大變形量 U,實驗結果見表 3。
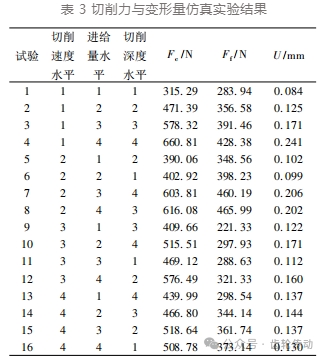
極差分析
極差分析法是一種直觀分析法,可以將復雜的多因素數據轉變成簡單的單因素數據解決問題,轉變計算公式為:
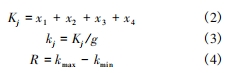
式中: Kj 為所研究因素同等水平條件下對應的試驗數據之和( j 為水平代號) ; x1、x2、x3、x4 為對應試驗數據; kj 為對應水平數據平均值; g 為水平重復數; R 為極差。
經過計算,得到輻板變形量 U 的極差值,見表 4。
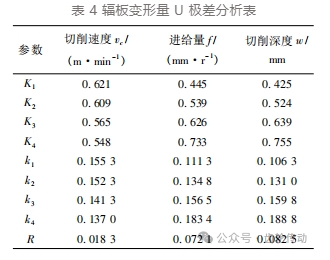
輻板變形量 U 與切削參數的響應關系如圖 9 所示。由圖 9 可知: 切削深度是影響輻板變形的主要因素,進給量為次要因素。選取因素的水平與要求的指標有關,研究要求齒輪薄輻板加工變形量 U 越小越好,則應取最小的那個水平,即取切削速度 150 m /min、進給量 0. 06 mm /r、切削深度 1. 8 mm 為最優切削參數。
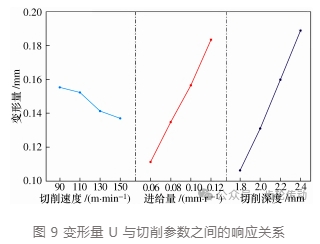
變形量試驗驗證
采用仿真與試驗變形量做對比驗證,從三坐標測量儀測量圖10 可以看出: 試驗變形量U 為0. 13 mm,將仿真獲得的變形數據與試驗獲得的變形數據進行對比,最大變形量 U 的預測誤差在 10%以下。分析結果表明,預測模型仿真結果與試驗加工情況規律一致。
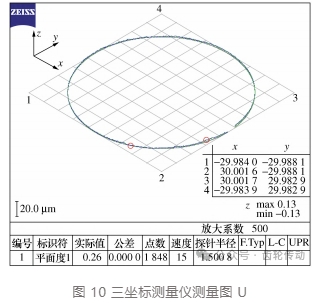
五、結論
本文基于 ABAQUS 軟件對高強度中合金滲碳鋼 18Cr2Ni4WA 進行三維切削仿真研究,提出了薄壁齒輪薄輻板加工變形預測有限元模型,并通過極差分析獲得了最佳切削參數,同時開展試驗進行了驗證。得出的結論如下:
1) 通過靜力學分析實現了齒輪薄輻板加工變形量的預測,基于三維切削仿真獲得了切削力參數和切屑形貌,將切削力施加在齒輪模型上以獲得齒輪的最大變形量。研究發現,齒輪輻板軸向變形量最大,徑向變形在輪轂處最大。
2) 通過設計 L16( 43 ) 型正交實驗仿真,分析了切削三要素對加工過程中切削力的影響,揭示了切削力獲得對齒輪輻板變形的影響。并基于極差分析發現,切削深度的選擇對輻板變形影響最大,切削深度對切削力影響最大,適當增大進給量、減小切削深度可以減少變形同時提高加工效率。
3) 加工參數優化研究結果表明,切削速度為 150 m/min、進給量為 0. 06 mm/r、切削深度為 1. 8 mm 為最優切削參數,此時齒輪薄輻板加工變形量 U 最小; 并將仿真獲得的變形數據與試驗獲得的變形數據進行對比,最大變形量 U 的預測誤差在 10%以下。
參考文獻略.