齒輪傳動是應用最廣泛的機械傳動之一,可傳遞空間任意兩軸之間的運動與動力,并變換運動方式。齒輪傳動還具有傳動平穩、精確、效率高,且結構緊湊、工作可靠等特點。
在“以塑代鋼”趨勢的帶動下,中國的工程塑料工業發展勢頭迅猛,生產力不斷提高,品種和用量也在不斷增加。隨著高性能工程塑料的不斷開發,塑料齒輪已作為動力型傳動件在汽車、家用電器等領域得到了廣泛應用。目前,我國塑料齒輪的設計、校核等標準大多還是參考現行的金屬齒輪標準。由于塑料齒輪與金屬齒輪材料不同,因此對塑料齒輪的設計方法、材料選用、加工工藝及檢測方法都與金屬齒輪存在很大的差異。塑料齒輪按材料分類主要有熱固性塑料齒輪和熱塑性塑料齒輪,熱塑性塑料齒輪主要應用于功率相對較小的傳動機構,筆者針對熱塑性塑料齒輪提出了設計與制作的方法。
一、塑料齒輪的特性
塑料齒輪相比金屬齒輪,具有質量輕、慣性小、耐腐蝕、耐磨損和低噪聲等特點,并具有良好的絕緣性,被廣泛應用于汽車、低壓電器等領域。基于塑料的注塑工藝,塑料齒輪還可以實現復雜的幾何形狀和著色處理。但是由于工程塑料的固有特性,使塑料齒輪具有較大的熱膨脹系數、較小的彈性模量和彎曲強度。
因此,在設計塑料齒輪時應盡量彌補塑料特性的缺點,利用塑料特性的優點來設計塑料齒輪。
二、塑料齒輪設計
齒形設計
漸開線齒輪中心距發生變動時不影響傳動比,因此能夠承受齒輪傳動裝置所固有的中心矩誤差,并且保證在傳動過程中瞬時傳動比不變。非漸開線齒形制對齒輪中心距的誤差敏感性較大,因此非漸開線齒形制不太適用于塑料齒輪輪系。美國為塑料漸開線齒輪推出了一種新的 AGMA PT 基本齒條,其最大特點是齒根采用了全圓弧,適用作動力型傳動用的塑料齒輪。
AGMA PT 基本齒條與 ANSI、ISO 標準的齒形 ( 即 ANSI/AGMA 細齒距基本齒條、ISO 粗齒距基本齒條) 參數對比見表 1,其中齒形參數可參考圖 1。
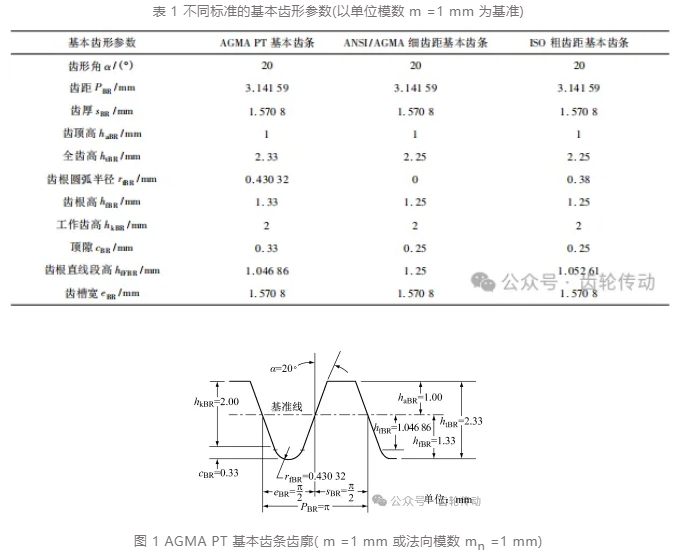
齒形修正
為了改善齒輪的嚙合狀態,提高載荷變化的均勻性,一般都需要對齒形進行適當修正,塑料齒輪受外界環境和制造加工等對尺寸的影響較大,更需要重視齒形的修正。
齒根圓弧修正:齒根圓弧不僅可以增強齒根的彎曲強度,還可以提高注塑的流動性,避免應力集中。圖 2 為 2 種不同齒根圓弧對齒根處所產生應力水平的 3 種應力分布圖。
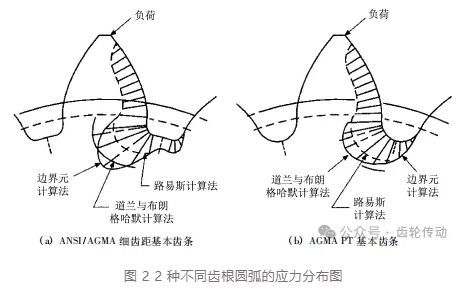
從圖 2 可以看出: AGMA PT 基本齒條的應力水平比 ANSI/AGMA 細齒距基本齒條低。因此,塑料齒輪應盡量都采用全齒根圓角半徑,在不引起配對齒輪齒頂干涉的情況下調整齒根圓弧,以增加 輪齒的載荷能力。
齒頂修緣:當 2 個齒輪在嚙合傳輸載荷時,由于載荷過大往往會使輪齒彎曲變形,從而會產生嚙合噪聲。為了補償這種彎曲變形,輪齒的兩側從中部到頂部需要逐漸變薄( 見圖 3) 。
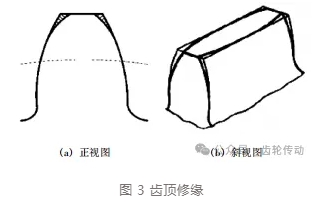
AGMA PT 基本齒條的齒頂修緣一般可由一小段圓弧齒廓來代替(見圖 4) ,其中齒頂修緣代用圓弧半徑 RTBR = 4 m,代用圓弧半徑的起始高度hαTBR = 0. 5 m。
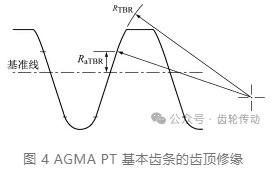
齒形角修正:ISO、AGMA 和 GB 等齒輪標準推薦使用的齒形角為 20°,增加齒形角可以降低齒輪彎曲應力和接觸應力,從而提高齒輪強度并減少磨損,但是增加齒形角會使齒頂寬度和齒根圓角半徑減小,而減小齒形角可以提高齒輪的重合度。
當齒輪傳動載荷方向是變化的或是不一致時,為了滿足 2 個方向的不同工作要求,可以設計不同的齒形角(見圖 5) 。例如,用于承載負荷的齒輪齒側,增大其齒形角,可有助于降低接觸應力; 而將用于非承載負荷的齒輪齒側設計為小齒形角,可以增加齒頂厚度和齒頂高。反之,用于承載負荷的齒側為小齒形角,可以提高重合度或減小工作嚙合角; 而將用于非承載負荷的齒輪齒側設計為大齒形角,可以起到增強輪齒彎曲強度的作用。
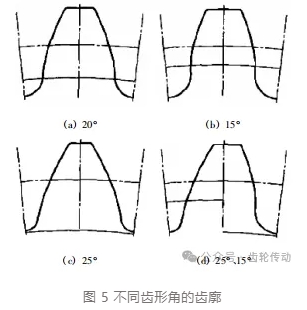
這種非對稱金屬齒輪往往受加工工藝的影響而無法實現,對于塑料齒輪則可以通過采用線切割成型的加工工藝實現,因此塑料齒輪可以根據工作要求來適當調整齒形角。
平衡齒厚:在齒輪設計中,一般嚙合的 2 個齒輪齒數設計不同,而模數和壓力角相等,這會導致設計出來的2 個齒輪的齒根部分寬度相差很大。齒數較少的齒輪齒根寬度相對較小,在承載運動時,小齒輪會成為該齒輪副強度的最弱處。為了優化齒輪的承載能力和嚙合側隙,應增加小齒輪的齒根厚度,同時減少相嚙合的大齒輪的齒根厚度,使小齒輪的齒根厚度等于或略大于大齒輪的齒根厚度(見圖 6) 。如果采用變位系數來平衡齒厚,則可以使小齒輪正變位,而大齒輪負變位。
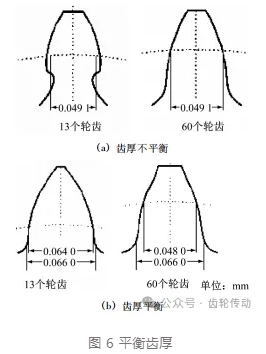
齒輪結構設計
塑料齒輪的結構設計應與材料物性和注塑成型工藝相適應,在設計齒輪的輪緣和輪轂時,需要注意壁厚、尖角、加強筋等要求。
在保證齒輪整體強度的前提下,應盡量滿足整體結構的壁厚均勻,這不僅利于注塑生產、降低材料成本,而且還能在一定程度上增加結構強度。常見的齒輪結構見圖 7。
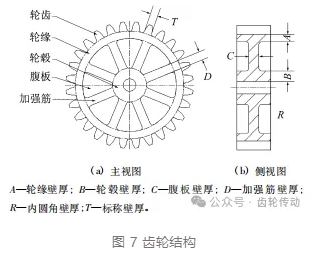
為便于結構設計,筆者選取齒輪齒壁厚作為標稱壁厚,輔助結構的壁厚可以參考表 2 以標準壁厚為基準進行選擇。考慮塑料件在注塑冷凝過程中存在收縮現象,一般壁厚不應超過 4 mm。為了減少收縮給齒輪帶來的精度問題,應該避免在腹板上設計通孔,且在腹板上設計加強筋時,也需要注意加強筋的布局,盡量在齒輪兩側交錯設計加強筋,防止塑料件出現高、低收縮區的影響。
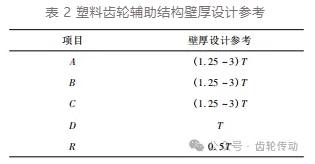
三、塑料齒輪常用材料
熱塑性塑料齒輪常用的材料主要有聚甲醛 (POM) 、尼龍(PA) 、聚碳酸酯(PC) 、聚酯(PBT) 、聚苯硫醚(PPS) 、聚醚醚酮(PEEK) 等。
POM 是常用也是最重要的塑料齒輪材料,一般為塑料齒輪的首選材料。POM 具有優越的物理性能,耐磨性、耐疲勞、高剛度,且具有較好的化學穩定性、電絕緣性和尺寸穩定性。但由于 POM 收縮率大、熱變形溫度低,因此 POM 齒輪不太適合應用于環境問題較高的場合。
尼龍 66( PA66) 和尼龍 46( PA46) 具有良好的堅韌性和耐用度,特別是改性 PA 材料的力學性能更優。但是由于 PA 具有較強的吸濕性,會引起塑料齒輪性能和尺寸的變化,因此 PA 齒輪不太適合在環境濕度較大的場合下使用。
PC 具有優良的抗沖擊性能,硬度高、收縮率低和吸水率低,且具有較好的尺寸穩定性。但由于 PC 不具自潤性,易磨損,因此 PC 齒輪主要應用于使用壽命低、載荷小的玩具產品。
PBT 具有較高的機械強度、耐熱性和耐腐蝕性,且塑料表面光滑,具有良好的機械傳動性能,但是缺口沖擊強度相對較低。
PPS 具有較高的硬度,尺寸穩定性好,且具有耐疲勞和耐化學性能等特點,可以長期在 200 ℃ 以 上的溫度條件下使用。
PEEK 是一種半晶態的高分子聚合物,是塑料齒輪中的頂級材料,PEEK 不僅具有耐高溫、綜合力學性能高、耐磨損和耐化學腐蝕等特性,還具有低吸水性、高韌性和耐沖擊性。由于 PEEK 價格昂貴,因此 PEEK 齒輪主要應用于飛機及軍用場合。
四、塑料齒輪強度校核
塑料齒輪具有噪聲低、抗腐蝕、慣性小,且制作成本低,可在無潤滑條件下傳動等優點。但是由于塑料齒輪的彈性模量低、機械強度低、熱傳導性差、熱膨脹系數大等缺點,限制了塑料齒輪在一定高載荷、高轉速和高溫度場合下的使用。
塑料齒輪常見的失效形式主要有斷裂和磨損 2 種類型(見圖 8) 。齒根附近斷裂大多是由于過載或疲勞超過了材料疲勞極限造成的; 節點附近斷裂或磨損大多是由于材料的抗熱能力差,在齒輪嚙合過程中輪齒齒面摩擦引起的溫升以及機械負荷的共同作用下,齒面出現嚴重磨損,如果中心距安裝過大也會導致齒輪節點附近斷裂或磨損; 而過度磨損導致齒面變薄主要是由于沒有潤滑導致的,或接觸面之間發生了粘著磨損,如接觸面之間有顆粒或磨損碎屑等。
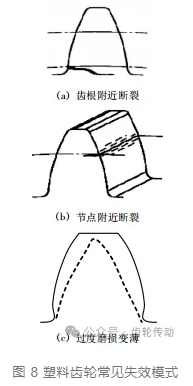
目前有關塑料齒輪強度計算的理論及標準比較少,大多技術人員以金屬齒輪的強度計算方法為參考,通過修改某些系數來計算或評估塑料齒輪的強度,然后再通過實驗的方法驗證該強度是否滿足使用要求。目前主要采用路易斯方程校核輪齒的彎曲強度,采用赫茲應力公式計算齒輪的齒面接觸強度,筆者以直齒輪強度校核計算為例。
塑料齒輪一般會進行齒形修正,因此齒頂受全負荷的假設不成立。由于塑料齒輪的注塑加工誤差及工藝要求,計算分析時一般不考慮齒根圓角的應力集中,但是需要考慮齒寬方向的實際接觸寬度。齒輪的強度涉及的因素較多,計算分析時必須嚴格考慮各種因素對強度的影響。
齒根彎曲強度校核
齒根的許用轉矩 TFp按以下公式計算:

式中: σb 為齒根最大彎曲應力,MPa; b 為有效齒寬,mm; d 為齒輪的分度圓直徑,mm; Y 為節點附近的齒形系數,見表 3 ; Z 為齒數。
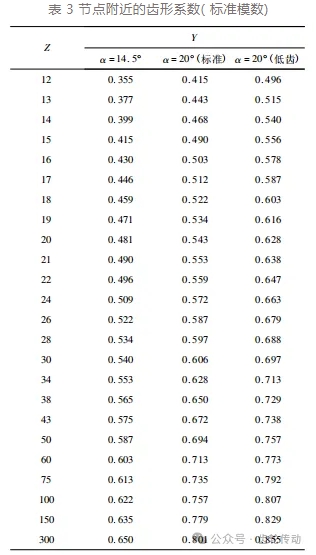
齒根的最大許用彎曲應力 σb 為:

式中: σ'b 為標準條件下的齒根許用最大彎曲應力,MPa,見圖 9; KV 為速度修正系數,見圖 10; KT 為溫度系數,見圖 11; KL 為潤滑系數; KM 為材質系數; KG 為材料強度修正系數; Cs 為使用系數。
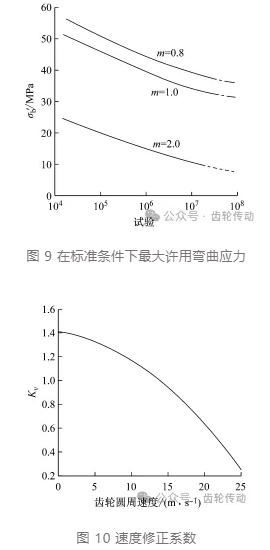
塑料齒輪的模數相對較小,一般取 0. 8 ~ 2,當齒輪模數小于 0.8 時可參考模數 0.8 的最大許用彎曲應力,而模數大于 2 時,需要取低于模數 2 的最大許用彎曲應力。
在環境溫度較高的情況下需要對溫度補償,一般可以通過齒輪的彎曲強度和溫度關系來修正(見圖 11) 。
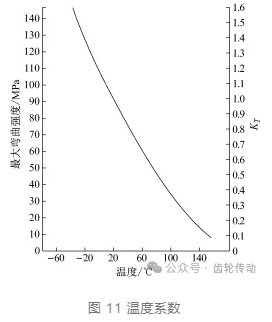
雖然塑料齒輪相比金屬齒輪具有自潤滑效果,但是在大多數情況下還是會增加潤滑脂以提高潤滑效果。齒輪在無潤滑情況下,一般 KL 取 0.75; 用油脂初期潤滑時 KL 可取 1.0。
塑料齒輪應盡量與塑料齒輪進行嚙合,如與金屬齒輪嚙合時,對金屬齒輪應相適應地降低粗糙度要求,否則容易磨損塑料齒輪齒面。塑料齒輪與塑料齒輪嚙合時,KM 可取 1.0; 塑料齒輪與金屬齒輪嚙合時,KM 可取 0.75。
常見的 POM 齒輪材料強度修正系數見表 4,使用系數參考表 5(其中 1 ~ 4 號表示 POM 齒輪一天的運轉時間分別為 24 h、8 ~ 10 h、3 h 和 0.5 h) 。
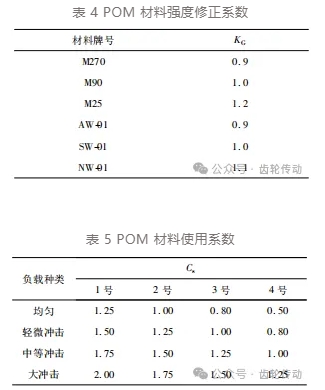
齒面接觸強度校核
一般塑料尺寸在有潤滑的條件下磨損量比較小,但在沒有潤滑的條件或一定壽命后潤滑效果下降后,塑料齒輪很容易磨損并出現斷裂現象。根據赫茲應力公式對塑料齒輪的齒面接觸強度 σH 進行校核。
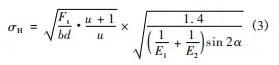
式中: Ft 為齒面所受的圓周力,N; u 為齒數比; E1、E2 為材料的彈性模量,MPa。
該塑料齒輪的強度校核計算方法主要是基于某幾種常用的工程塑料的基本性能數據,而隨著目前改性的工程塑料的發展與應用,還需要進一步加強對塑料齒輪的強度理論研究及實驗分析。
五、塑料齒輪的制作與加工
塑料注塑成型的收縮特性是影響塑料齒輪精度的主要因素,因此塑料齒輪模腔的設計是一項關鍵技術。一般塑料件注塑收縮大多為各向等比例收縮,而塑料齒輪在其漸開線齒形上的收縮量是非線性的,增加了漸開線塑料齒輪模具型腔的設計難度。
如果將塑料齒輪的模腔設想為一個假想的齒輪,而該齒輪的齒數不變,根據齒輪分度圓直徑 d = mZ 可知,在加工齒輪模腔過程中,考慮收縮率而使齒輪分度圓直徑的變化,就相當于齒輪模數的變化。
塑料齒輪模腔的齒輪模數 m'為:

式中: δ 為塑料收縮率。
齒輪模腔的其余參數可由 m'代入計算求得。這種計算方法也被稱為變模數法。
塑料齒輪在注塑成型的過程中,塑膠熔體會以注塑澆口為中心收縮,因此澆口的位置對齒輪圓度影響較大,澆口的分布形式對塑料齒輪的力學性能也有較大影響。為了提高塑料齒輪的精度,盡量 采用多點分布式澆口,且澆口在同一圓周上均勻分布,這種澆口布局會大大縮短熔接痕形成時間,且形成的低收縮區傾向也會減小(見圖 12) 。
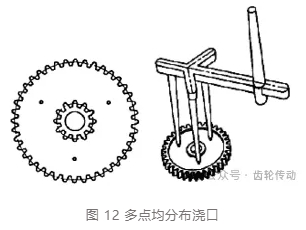
模具的制造還需要關注排氣系統、冷卻系統和等位結構等常用的模具設計要求。塑料齒輪的注塑工藝皆與塑料的收縮相關,因此控制合理的收縮率才能制造出高精度的塑料齒輪,其中模具溫度、注塑壓力和保壓時間對塑料齒輪成型的收縮率具有重要影響。
六、結語
塑料齒輪已經在很多領域中確立了傳統金屬齒輪的替代品地位,隨著熱塑性塑料的發展,熱塑性塑料齒輪也逐步擴大了應用范圍。塑料齒輪具有很多金屬齒輪不具備的優點,但是也存在一定的缺陷,因此在設計階段不僅需要進行精確計算和校核,還必須制造出合理、精確的齒輪模具,同時配以合理的注塑工藝才能實現。
筆者提出的關于塑料齒輪的齒形設計、齒形修正和強度校核方法,以及模具制造與加工的基本要求,有助于提高熱塑性齒輪的可靠性。
參考文獻略.