誤差對諧波減速器的性能、壽命、嚙合狀態等方面的影響很大,因此需要對此進行深入研究。影響柔輪應力與嚙合特性的誤差因素很多,總體可以分為制造誤差與裝配誤差。在諧波減速器已經制造加工完成的情況下,制造誤差對諧波傳動嚙合性能與柔輪應力的影響已不可控,而在三大部件的裝配過程中,必然產生裝配誤差,進而使諧波減速器的應力分布、嚙合狀態、運行穩定性、傳動精度及使用壽命受到影響,因此,研究裝配誤差對諧波減速器的影響規律,得到滿足良好應力水平與合理側隙的裝配誤差范圍,對工程實際問題具有一定的指導意義。
基于此,本文以無公切線式雙圓弧齒廓諧波減速器為研究對象,分析了影響諧波傳動嚙合性能與引起柔輪應力分布變化的主要裝配誤差,包括剛輪與柔輪的中心距誤差、凸輪安裝位置誤差。在建立諧波減速器有限元非線性多齒嚙合模型的基礎上,探究各個裝配誤差對諧波傳動嚙合特性與柔輪應力分布的影響,在柔輪的長短軸正負向設置多個觀測點,分別提取各個觀測點的應力值及最大徑向變形量,得到各裝配誤差對應力分布及最大徑向變形的影響關系,結合MATLAB參數化手段探究各裝配誤差與齒間嚙合側隙的關系,為諧波減速器的誤差控制提供參考方法。
一、雙圓弧柔輪齒廓設計與主要裝配誤差
無公切線雙圓弧共軛齒廓設計
雙圓弧齒廓有更大的嚙合弧長,目前諧波傳動齒廓研究熱點為公切線雙圓弧齒廓。本次研究采取的無公切線雙圓弧齒廓與公切線雙圓弧齒廓相比,其共軛區間更大且設計流程更簡單,更便于生產加工。
圖1所示為局部坐標系下的雙圓弧基本齒形。
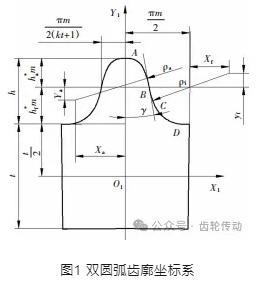
該柔輪局部坐標系S1是以柔輪輪齒的對稱軸為Y1軸,以Y1軸和柔輪中性層曲線的交點O1為坐標原點,以過O1 點垂直于Y1軸的直線為X1軸。該無公切線雙圓弧齒廓包括3段相切圓弧,分別為柔輪齒凸齒廓AB、凹齒廓BC、齒根圓過渡齒廓 CD。雙圓弧齒廓的基本參數含義如表 1 所示。
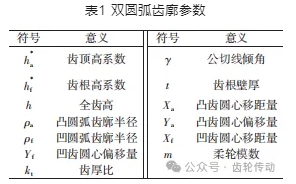
根據圖1,以從齒頂A處起的齒廓弧長u為參數,r為右側齒廓的矢徑,n為其對應法向量。
在AB段上:
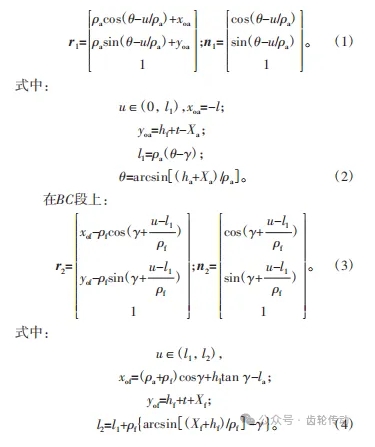
首先建立嚙合基本方程并采用改進運動學法設計剛輪的理論共軛齒廓。采用數值離散思想,將各段的弧長參數 u離散成s個點,再將對應齒廓段點的 r、n 代入嚙合基本方程,即可求得該點剛柔輪共軛轉角集,最后通過坐標變換求得與柔輪齒廓共軛的剛輪理論齒廓。
諧波齒輪主要裝配誤差
諧波減速器的裝配誤差主要來源于各部件之間的相互配合過程,主要分為波發生器與柔輪之間的裝配誤差以及剛輪與柔輪之間的裝配誤差。而波發生器與柔輪的裝配誤差主要有波發生器中凸輪與柔性軸承的配合間隙、柔性軸承的徑向跳動、柔性軸承的徑向游隙、波發生器軸的徑向跳動等,剛輪與柔輪的裝配誤差主要有剛輪與安裝孔間的徑向跳動與配合間隙、柔輪與輸出軸的配合間隙等。本文采用固定剛輪的安裝方式,即將剛輪作為機架,波發生器作為輸入端,柔輪杯底作為輸出端的形式。為簡化分析提高效率,僅分析容易量化且可通過實驗平臺測量的因素。主要為剛輪與柔輪的中心距誤差、凸輪安裝位置軸向誤差與徑向誤差。
1)剛輪與柔輪的中心距誤差。
安裝柔輪與剛輪時,一般應保證兩者的中心軸線重合,在實際工程中,兩者存在一定的誤差,將兩軸線之間的距離稱為中心距,用eCF表示。eCF的偏差稱為剛輪與柔輪的中心距誤差,用δCF表示。
2)凸輪軸向安裝誤差。
凸輪在裝配過程中,在柔輪上的安裝位置截面離柔輪杯底的距離用dWF表示,dWF的偏差稱為凸輪軸向安裝誤差,用δWFZ表示。
3)凸輪徑向安裝誤差。
凸輪在裝配過程中,在柔輪上的安裝位置截面離柔輪杯底的距離用eWF表示, eWF的偏差稱為凸輪徑向安裝誤差,用δWFJ表示。
如圖2為上述裝配位置參數的示意圖。
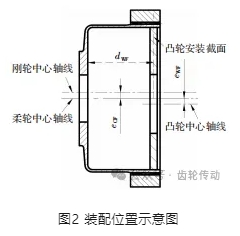
采用控制變量法結合MATLAB參數化與有限元實驗法分析各種裝配誤差對諧波傳動側隙與柔輪齒面應力的影響。以諧波減速器型號CSF-25-120為實例,可知理論的剛輪與柔輪的中心距eCF=0,理論凸輪安裝位置軸向距離dWF=24 mm,理論凸輪安裝位置徑向距離eWF=0。
需要研究的因素有:剛輪與柔輪的中心距誤差δCF,凸輪軸向安裝誤差δWFZ,凸輪徑向安裝誤差δWFJ。剛柔輪的中心距誤差與凸輪徑向安裝誤差所包括的范圍為一圓柱體區域,為降低實驗復雜程度,僅考慮長短軸方向誤差取值。短軸與長軸方向上的δCF分別設為δCFX和δCFY,凸輪短軸與長軸方向上δWFJ分別設為δWFX和δWFY。對各因素進行實驗安排,實驗安排如表2所示,共計25組實驗。
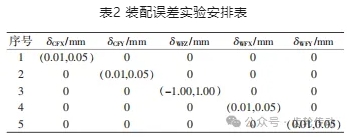
二、諧波齒輪有限元分析
共軛空間齒廓計算實例
采取HD公司的諧波齒輪型號CSF-25-120,模數m= 0.263 mm,柔輪齒數z1=240,剛輪齒數z2=242,傳動比i=120,理論徑向變形量 w*0=0.261,根據齒廓方程式(1)~式(4),可得柔輪齒廓參數如表3 所示。采用基于改進運動學法的諧波嚙合理論,得到剛輪的理論共軛齒廓。
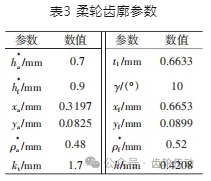
諧波減速器有限元建模
建立剛輪、柔輪及波發生器的有限元模型通過 ABAQUS軟件分析柔輪表面應力。
1)建立剛輪、柔輪與波發生器的三維實體模型,去除倒角,對模型進行簡化。
2)利用ANSA 劃分網格,如圖3 所示,采用八結點六面體單元 C3D8R,并測試柔輪應力對網格數量的依賴性。
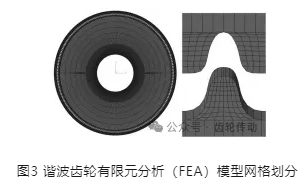
3)定義約束條件。網格模型導入ABAQUS,建立參考點,與柔輪杯底固結,設置為完全約束狀態,波發生器分為上下兩半同時裝入柔輪,保證兩者初始裝配狀態無干涉。
4)設置接觸對??紤]柔輪彈性變形特點,由于波發生器與柔輪內壁接觸狀態和區域未知,因此設置“面-面”接觸對,摩擦因數取0.15,滑移為有限滑移,主表面平滑度取為0.2。
5)賦予材料屬性。材料性能參數如表4所示,柔輪材料為30CrMnSiA,剛輪和波發生器材料為45鋼。
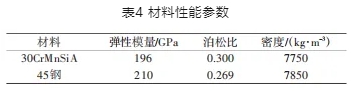
6)根據表2所列數據對諧波齒輪模型進行裝配調整,共計25組實驗。并對各組實驗進行仿真計算,提取實驗結果數據。
三、裝配誤差對雙圓弧齒輪嚙合特性與柔輪應力分布的影響
剛柔輪中心距誤差對柔輪應力影響
提取不同δCFY值下的計算結果,繪制應力云圖,為區分齒根處應力與齒面應力的變化,在柔輪齒長軸正向附近設置齒面應力觀測結點1、齒根應力觀測點2、短軸正向附近設置齒面應力觀測點3、齒根應力觀測點4、長軸負向附近設置齒面應力觀測點5、齒根應力觀測點6。提取柔輪齒面最大應力、杯底最大應力及各觀測點應力繪制曲線如圖 4、圖5所示。
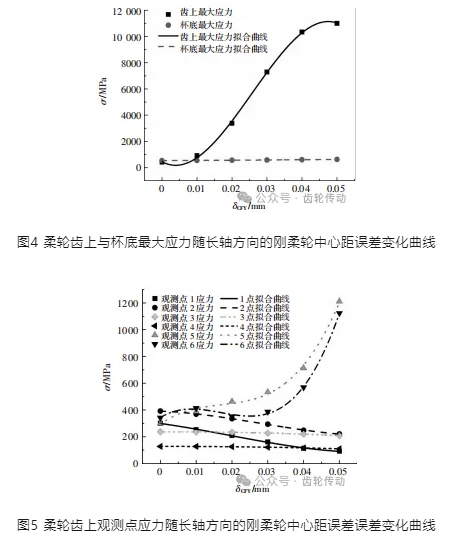
結果表明,δCFY 從0增大到 0.05 mm,柔輪杯底最大應力基本保持不變,柔輪齒上最大應力由410 MPa增大到了 11 000 MPa,擴大約27.5倍,同時,長軸正向的齒面與齒根觀測點應力隨著δCFY增加而減小,短軸附近的齒面與齒根觀測點應力幾乎不變,而長軸負向的齒面與齒根觀測點應力急劇增大,呈指數增長。結果表明,長軸方向的剛柔輪中心距誤差對柔輪齒上最大應力影響極大。對杯底最大應力影響很小。
對δCFY下的模型進行計算,繪制應力云圖,增加短軸負向齒面應力觀測點7、齒根應力觀測點8。提取柔輪齒上與杯底最大應力及觀測點 1、 2、3、4、7、8 的應力繪制曲線如圖6所示。
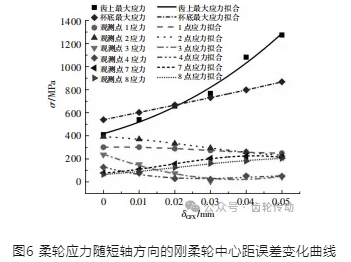
結果表明,隨著δCFY的增加,柔輪上齒面最大應力和杯底最大應力均隨之呈線性增長,齒面最大應力增幅較大,約為200%,杯底最大應力增幅約為61%。柔輪長軸附近的齒面與齒根應力略有減小,短軸正向附近的各應力也緩慢減小至50 MPa左右,而短軸負方向附近的各應力略有增加。這是由于剛輪安裝偏差往短軸正向偏移,使得短軸負向附近輪齒齒側間隙變小,加大了嚙合深度,因此齒上應力變大。而短軸正向附近的輪齒反之。對于杯底應力來說,嚙合深度增加同時使嚙合接觸面增加,嚙合受到的阻力增加,力矩隨之增大,使得杯底最大應力增加。
凸輪安裝位置誤差對柔輪應力影響
提取δCFY∈(-1.00,1.00)mm時柔輪應力云圖,觀察齒上的最大應力、杯底最大應力、長軸齒面與杯底位置觀測點 1、2應力的變化情況,進行多項式擬合繪制曲線如圖7所示。
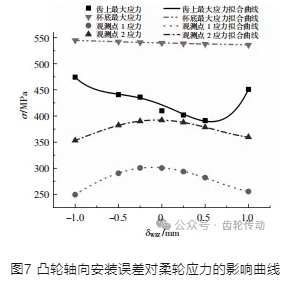
從圖7 可以看出,隨著凸輪軸向安裝誤差從-1 mm到1 mm變化,柔輪杯底最大應力幾乎不變。長軸附近觀測點1、2上的應力有先增后減的趨勢,在δWFZ取0 mm左右,長軸觀測點1、2均達到最大。當δWFZ∈(-0.25,0.25)mm范圍時,柔輪齒面與齒根處觀測點的應力變化非常小。柔輪齒上的最大應力變化較復雜,其隨著凸輪安裝位置從柔輪齒后端到前端先減小、后增大,在δWFZ取0.5 mm左右存在最小值。觀察不同δWFZ的應力云圖還可以發現最大應力位置從齒前端開始往齒后端移動。總體來看,應力大小變化不大,變化率為12.5%。
圖8為柔輪齒上最大應力隨長軸方向凸輪徑向安裝誤差變化曲線,圖9 為柔輪齒上觀測點應力和杯底最大應力隨長軸方向凸輪徑向安裝誤差變化曲線。
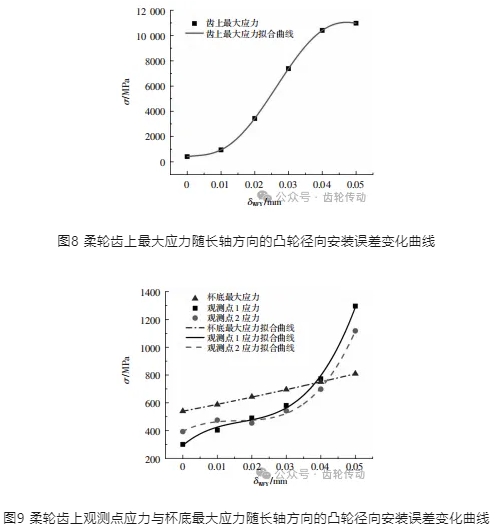
結果表明,長軸方向的凸輪徑向安裝誤差對柔輪齒上應力影響極大。這是由于凸輪長軸方向上的徑向安裝誤差會對柔輪上實際徑向變形量產生影響,而徑向變形量對柔輪的應力影響顯著。
圖 10 為柔輪應力隨短軸方向的凸輪安裝徑向誤差變化曲線。隨著短軸方向凸輪徑向誤差的逐漸增大,長軸附近的齒面與齒根觀測點1、2應力呈下降趨勢,短軸附近的點3、4 應力呈上升趨勢。這表明較大應力區域將從長軸附近往短軸方向發生偏移,應力云圖中應力分布的位置也隨之改變,總體應力水平較低。
四、結語
1)長軸方向的剛柔輪中心距誤差與凸輪徑向安裝誤差對柔輪齒面與齒根應力影響最大,短軸方向的剛柔輪中心距誤差與凸輪徑向安裝誤差次之,凸輪的軸向位置誤差影響最小。
2)短軸方向的剛柔輪中心距誤差及長軸方向的凸輪徑向安裝誤差對柔輪杯底應力略有影響,其余因素影響很小。
3)在諧波齒輪的裝配過程中,應優先保證δCFY與δWFY的精度,再考慮δCFX與δWFX,最后確定凸輪軸向位置。
參考文獻略.