近年來,隨著我國“雙碳”戰略的實施,風電作為清潔能源在我國電力能源布局中的重要性不斷提升,以大兆瓦風電增速傳動技術為代表的研究和應用最為引入注目。風電增速箱是風電動力傳輸的關鍵設備,負責將風輪在風力作用下產生的動力傳遞給發電機,相對于其他工業齒輪箱,具有可靠性高、增速比大、高功率密度等特點。內齒圈作為增速箱的核心組成零件,其設計水平和承載能力顯著影響了風電增速箱的輕量化水平。因此,其制造質量得到了人們的廣泛關注。
通常,風電內齒圈主要的生產流程為連鑄圓坯→自由鍛+環鍛→正火→粗車→粗銑齒→調質→半粗車→精銑齒→感應淬火→噴丸→磨齒→探傷等。與滲碳淬火和滲氮相比,感應淬火具有生產效率高、節能環保和制造成本低等優點。然而,在實際生產過程中,內齒圈在感應淬火工序中淬火開裂問題尤為普遍。王榮認為,感應淬火工藝不當是造成感應淬火開裂的主要原因。鄭長進等針對內齒圈感應淬火工藝的過程控制進行了分析,從原材料質量控制、感應器制造、感應淬火工藝等方面提出了控制要點。黃星等認為,調整感應淬火的工藝頻率能有效減少淬火裂紋,但以上均未定量評估偏析和脫碳對感應淬火開裂的影響。本文旨在探索鍛造過程中偏析和脫碳對風電感應淬火開裂的影響,分析得到材料和鍛造關鍵技術指標對感應淬火開裂的影響規律,從而為內齒圈的生產制造提供優化依據。
一、開裂原因分析
宏觀形貌及磁粉探傷
內齒圈材料為 42CrMo4 鋼,模數 21 mm,齒輪外徑 Φ2166 mm,內徑 Φ1832 mm,齒寬 550 mm,單齒感應淬火工藝,節圓層深要求 4.4 ~ 5.4 mm。內齒圈感應淬火后,在磁粉探傷時,發現齒頂處存在感應淬火裂紋。內齒圈感應淬火裂紋齒部的分布圖如圖 1 所示。由圖 1 可見,內齒圈表面呈藍色回火色,圖 1 中箭頭所指的齒部均存在感應淬火裂紋。由圖 1 所見,裂紋分布處較多,幾乎達到了整個齒輪 3 /4 的齒數。
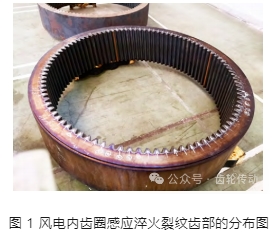
圖 2 為風電內齒圈磁粉探傷狀態下的宏觀形貌。可見,磁粉聚集線位于齒頂附近,沿徑向分布。
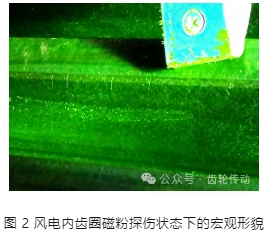
顯微組織觀察
為進一步分析聚集線形成原因,對內齒圈進行了金相分析。使用線切割在裂紋附近選取齒塊截面試樣進行低倍形貌觀察。共取 10 根開裂齒條進行解剖分析,分析了感應淬火裂紋齒塊的低倍組織特征,得到了感應淬火裂紋齒塊的兩種典型的宏觀低倍形貌(見圖 3) 。由圖 3 可知,在感應淬火開裂的齒部呈現較為嚴重的組織偏析,如箭頭位置所示,偏析組織呈現塊狀和條帶狀。
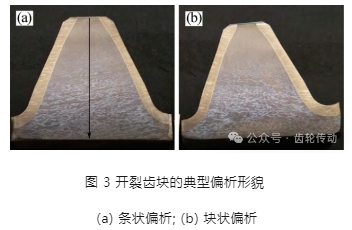
在裂紋附近選取齒塊截面試樣進行金相檢查。圖 4 是裂紋截面顯微組織,裂紋呈沿晶擴展,尾端尖細,未見分叉,具有淬火裂紋特征。
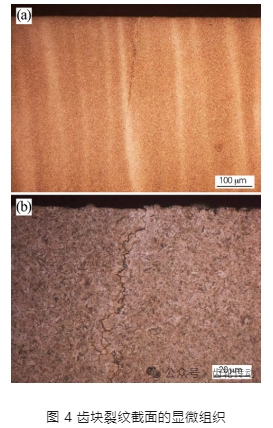
由于裂紋位置均發生在齒頂處,因此對齒頂附近進行金相檢查,圖 5 是齒頂附近截面顯微組織,發現齒頂附近存在深約 60 μm 的脫碳層,脫碳層組織為塊狀鐵素體 + 馬氏體,次表面層組織為馬氏體,根據 JB /T 9204—2008《鋼件感應淬火金相檢驗》可以評定其馬氏體級別為 4 級,未見組織粗大特征。
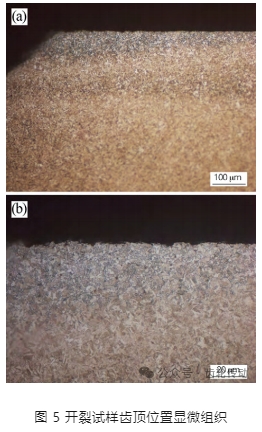
為了進一步確認脫碳,分別對齒部開裂位置的表面脫碳層、基體暗區、基體亮區進行硬度測試。采用 FEM -7000 型顯微硬度計進行硬度測試,載荷砝碼 300 g,加載時間 10 s。圖 6 為開裂齒塊齒頂附近各區域顯微硬度測試數據。由圖 6 可以看出,齒頂附近基體暗區和亮區硬度偏差較大,且表面脫碳層硬度僅為 312 HV0.3。
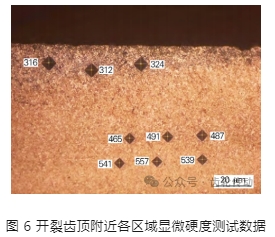
脫碳層對開裂的影響
通過淬火硬度也可以反推出表面含碳量,從圖 6 可以看出,未脫碳的淬火硬度為 557 HV0.3,表面脫碳層硬度僅為 312 HV0.3。根據表 1 可知,557 HV0.3 對應的含碳量為 0.41% 。根據碳含量和硬度的關系可知,312 HV0.3 對應的含碳量為 0.06%。結合含碳量對相變轉變溫度 Ms 的影響可知,脫碳層會極大加劇感應淬火開裂。需要指出的是,感應淬火過程中并不會形成脫碳,因此該脫碳層應在感應淬火之前已經存在。通常,齒頂的半脫碳層會通過機加工去除,但當調質畸變過大,調質后局部齒頂加工量不夠,就會在齒頂處殘存半脫碳層。
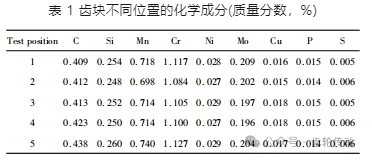
偏析開裂的影響
為了進一步檢測內齒圈的成分偏析情況,對感應淬火開裂齒塊進行不同區域的直讀光譜測試( 距離表面 5 mm 開始測量,間隔 10 ~ 15 mm 交替測量) ,測試位置的示意圖如圖 3(a) 所示。表 1 為齒塊不同位置的化學成分情況。由表 1 可知,齒塊的化學成分偏析主要是碳元素,齒頂位置碳含量偏低,隨著往齒心部移動,碳含量不斷增加。
在齒圈均布取 6 個感應淬火開裂齒塊,進行化學成分測試,以對整個齒圈進行碳偏析分析。內齒圈碳含量偏析程度如圖 7 所示。由圖 7 可知,整個齒圈鍛件的碳偏析程度已經達到了 0.06% 的偏差。即使在 1 號位置(齒頂處) 碳偏析程度也達到了0.04%左右。
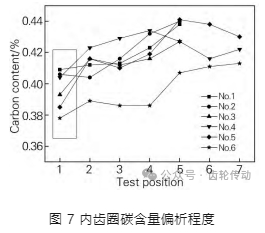
碳偏析的存在必然會影響鋼的相轉變溫度 Ms。以 Wang 等給出的方法計算 0.38%碳含量和 0.44%碳含量的相轉變溫度 Ms,分別為 337 ℃和 321 ℃。不同碳含量的 Ms 溫度差達到了 20 ℃ 左右,這會導致在感應淬火過程中產生較大的組織應力差,從而導致淬火開裂。另外,碳偏析也會疊加鍛造的影響,形成如圖4(a) 所示的帶狀組織。帶狀組織會破壞鋼的連續性,增加淬火冷卻時的應力集中程度,從而也促進了感應淬火裂紋的擴展。另外,風電內齒圈在感應加熱后采用噴 PAG 水溶劑淬火液進行冷卻。由于噴淬要比浸入淬火的冷卻速率快,其大幅度提升了內齒圈感應淬火過程的淬火應力,當疊加碳偏析時更加容易造成感應淬火開裂。由此可見,碳偏析程度達到 0.04% 及以上時,淬火風險必然會增加。
綜上所述,內齒圈齒頂裂紋具有淬火裂紋特征,齒頂處馬氏體組織細小,未見粗大現象,可以排除由過熱現象導致開裂的原因。而齒頂表面存在半脫碳層,一般感應淬火過程中無法形成脫碳,因此該脫碳層應在感應淬火之前已經存在。半脫碳層含碳量低,Ms 點高,所以先淬成馬氏體,然后次表層再淬成馬氏體,對表面層產生推擠,而表層組織已轉變成硬度高塑性低的馬氏體,超過一定強度時就會發生開裂。此外,內齒圈基體帶狀組織偏析也會增加淬火冷卻時的應力集中程度,淬火裂紋會沿著偏析條帶處徑向擴展。
二、工藝改進措施
齒頂脫碳層形成原因及解決措施
感應淬火是一個快速加熱淬火過程,加熱過程不超過 10 s,感應淬火工藝不會出現齒頂脫碳,其脫碳環節應為鍛造工藝或調質處理殘留。目前,隨著大兆瓦風電技術快速發展,42CrMo4 鋼內齒圈的規格不斷變大。為了保證內齒圈熱處理性能,大部分都開始采用水劑淬火液進行熱處理,導致熱處理畸變有增大傾向。尤其在生產過程中出現多次熱處理返工時,會對后續精車和銑齒工序的加工量產生較大的影響,就有可能導致表面脫碳層未去除。
由此可見,由于調質畸變導致的齒頂橢圓或加工尺寸不足,使得局部齒頂脫碳層未能有效去除。通常可采用增加調質處理后的機加工尺寸或者提高水劑淬火液濃度來進行預防。
偏析定量表征及解決措施
風電內齒圈的鋼牌號為 42CrMo4,且采用連鑄工藝制造成圓坯進行齒坯成形。由于 42CrMo4 鋼的碳含量在 0.38% ~ 0.45% ,在大截面連鑄過程中容易形成嚴重的偏析。在直徑 Φ600 mm 的 42CrMo4 鋼大圓坯,沿著直徑方向進行成分檢驗。圖 8 為 Φ600 mm 連鑄坯沿著直徑方向的碳濃度分布。由圖 8 可知,大連鑄坯的碳偏差值達到了 0.06% 。
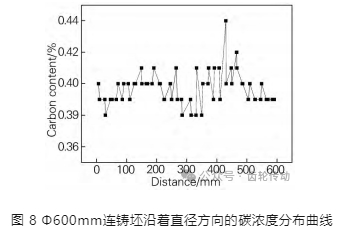
自由鍛是風電內齒圈的常用成形方法,合理的鍛造比可以保證坯料的均勻性和致密程度。表 2 為鍛造比對內齒圈碳偏析差的影響。由表 2 可知,連鑄坯鍛造比達到 7 以上時,內齒圈碳偏析差可降低至 0.02%。
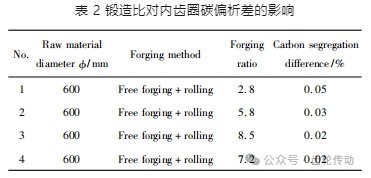
另外,在保證鍛造比的同時,還需要考慮內齒圈的工作表面應用的是連鑄坯的中心部位,為此需要進行控制沖孔的要求。通常,在沖孔工藝設計時,可以通過控制沖孔質量來實現連鑄坯中心部位偏析的去除。控制沖孔質量通過 A × H 來計算,其中,H 為連鑄坯下料長度,單位為 mm; A 為下料系數,單位為 kg /mm。表 3 為不同的下料系數對內齒圈齒部顯微缺陷和淬火開裂的影響。由表 3 可見,當下料系數≥0.019 時,可以避免齒部顯微缺陷和淬火開裂的產生。
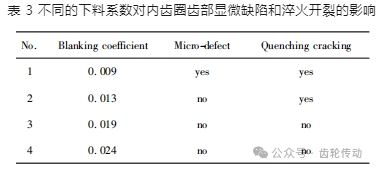
三、結論
1) 碳偏析和脫碳層是導致內齒圈感應淬火開裂的重要原因。脫碳極大地加劇感應淬火開裂的風險,內齒圈的碳偏析程度達 0.04% 以上時,增加了感應淬火開裂的風險。
2) 通過三向鍛造的方式獲得鍛造比大于 7 的坯料,可以有效改善碳偏析,從而預防偏析形成的感應淬火開裂問題。
3) 在沖孔工藝設計時,可以通過控制沖孔質量來實現連鑄坯中心部位偏析的去除。當下料系數 ≥0.019 時,可以避免齒部顯微缺陷和淬火開裂的產生。
參考文獻略.