風力發(fā)電是新能源的重要發(fā)展方向之一,而風電機組長期、全天候在惡劣復雜的工作環(huán)境下運行,其安全性、穩(wěn)定性尤為重要。齒輪的主要作用是動力傳輸,同時也是非直驅式風力發(fā)電機的關鍵部件,一旦發(fā)生故障,會直接影響風電機組的穩(wěn)定工作和使用壽命,因此保證其正常運作對整個風電機組系統(tǒng)具有重要的意義。
齒輪的典型缺陷類型主要包括疲勞裂紋、齒面點蝕、齒面膠合、齒面磨損、斷齒以及在加工過程中易出現(xiàn)的磨削燒傷等,這些類型的缺陷一般出現(xiàn)在輪齒齒面上,在風電機組齒輪箱故障中占有較大比例。國外研究機構FZG(慕尼黑工業(yè)大學齒輪研究中心)等在早期對齒輪內(nèi)部疲勞斷裂進行了試驗研究和數(shù)值模擬。英國克蘭菲爾德大學的 TOUTOUNTZAKIS等采用聲發(fā)射技術(AE)進行了齒輪缺陷檢測,同時探討了從軸承箱監(jiān)測齒輪缺陷的可能性。劉柄顯等提出一種基于巴克豪森噪聲的檢測方法,該方法具有檢測和表征微觀金相組織中馬氏體深度的能力,同時可以避免激勵頻率對巴克豪森噪聲信號輸出的影響。在對于造價相對便宜或工作環(huán)境不苛刻的齒輪檢測研究中,我國有許多學者用基于機器視覺判別的自動化系統(tǒng)取代了人工缺陷檢測;基于振動分析的監(jiān)測技術是目前運用較廣泛且成熟的一種監(jiān)測方法,該技術通過對信號進行處理并提取特征信息來進行定位、定性,能有效評估齒輪的運行狀態(tài);此外可采用的無損檢測技術還有超聲檢測、油液分析、紅外線成像、溫度傳感器等。以上研究在風電機組齒輪檢測和監(jiān)測方面已經(jīng)取得一定成果,但均存在一定弊端,如:① 機器視覺技術目前無法滿足工業(yè)無損檢測的靈敏度要求,且對工作環(huán)境要求較高;② 監(jiān)測方法多數(shù)需要連貫、系統(tǒng)地使用整套設備,而國內(nèi)的系統(tǒng)化研究起步較晚,很少有風場配備整套的監(jiān)測系統(tǒng);③ 振動分析對齒輪早期故障的預測有一定的局限性,往往需要協(xié)同使用其他檢測手段;④ 巴克豪森噪聲技術只能檢測出齒輪表面及近表面缺陷,對于內(nèi)部缺陷的檢測靈敏度不高且檢測時間較長,操作復雜。
針對目前風電機組齒輪檢測的難點,提出一種基于地磁場的被動式弱磁檢測技術。該技術方法操作簡易便捷,掃查速度快且靈敏度高,在檢測過程中不需要耦合或外加激勵,所采用的弱磁探頭能滿足對表面缺陷和內(nèi)部缺陷的檢測需求。
一、弱磁檢測原理
磁化是指使原來不具有磁性的物質(zhì)獲得磁性的過程,磁化強度是描述物體磁性強弱程度的物理量。外磁場強度相同的情況下,磁化率是影響磁化強度與磁感應強度的唯一條件。當磁場中的磁介質(zhì)發(fā)生磁化時會產(chǎn)生附加磁場,而附加磁場和原磁場疊加后的總磁感應強度與原磁場強度之間的關系可表示為

式中:B為磁感應強度;H為磁場強度;X1為物質(zhì)的磁化率;μ0為真空中磁導率,取4π×10-7H · m-1;μ1 為相對磁導率,μ1=1+X1。
在地磁場的作用下,任何處于其中的物質(zhì)都會發(fā)生或多或少的磁化。由式(1)可知,如果物質(zhì)是連續(xù)且均勻的,其磁導率也應是相同且無變化的。因此,當齒輪不存在缺陷時各位置的磁導率相同,在地磁場磁化下表面的磁感應強度也是均勻穩(wěn)定的;反之,若存在缺陷,那么在缺陷處的磁導率會發(fā)生突變,磁感應強度也會在缺陷附近發(fā)生變化。表面缺陷和內(nèi)部缺陷的弱磁檢測信號對比如圖1所示,當缺陷位于齒輪表面時,因為空氣的相對磁導率比工件的相對磁導率小,則通過弱磁探頭采集到的缺陷處的磁感應強度會變小,所以曲線呈現(xiàn)下凹的狀態(tài);當缺陷位于齒輪內(nèi)部時,因為缺陷處的磁感應線被排斥,所以缺陷上方的磁感應強度增大,采集到的磁感應曲線呈現(xiàn)上凸的磁異常現(xiàn)象。
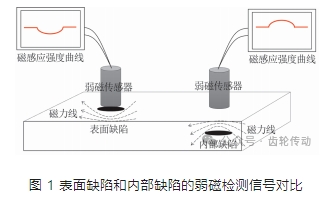
二、檢測試驗
檢測試驗中所使用的1#,2#試樣材料為低合金高強度鋼,牌號為17Cr2Ni2Mo,其優(yōu)異的耐腐蝕性和抗疲勞性能使其常被作為齒輪、軸承等重要機械部件的制造材料,1#,2#試樣結構如圖2,3所示。其中1#試樣的厚度為4 mm,有4處人工預制的表面裂紋缺陷;2#試樣含有一處位置未知的磨削燒傷。齒輪在疲勞磨損或應力集中處易萌生自然細小裂紋,一般裂紋寬度并不大,因此1#試樣的預制裂紋缺陷尺寸從左至右分別10 mm×0. 35 mm(長× 寬,下同),10 mm×0. 45 mm,10 mm×0. 4 mm,10 mm×0. 3 mm,對1#試樣進行正面掃查以模擬檢測齒輪的表面裂紋缺陷,試樣背面材料均勻且無表面缺陷,對其背面進行掃查以模擬檢測內(nèi)部缺陷;將2#試樣的輪齒齒面作為檢測面以模擬檢測磨 削燒傷缺陷。采用實驗室自主研發(fā)的弱磁檢測探傷儀檢測上述試樣,并多次反復試驗以驗證其重復性。弱磁探頭采用高精度磁通門傳感器,其量程為 ±250 000 nT,靈敏度可達1 nT,采樣頻率為25 Hz,最多可組成12通道的陣列探頭,根據(jù)試樣尺寸此次試驗選用單探頭。檢測時,需要將試樣放置于穩(wěn)定的磁場環(huán)境內(nèi),將弱磁探頭放置于待測試樣表面,接著采用人工手動掃查的方式,沿著掃查方向勻速穩(wěn)定、不間斷地采集試樣的磁感應信號,且掃查速度不 超過5 m · min-1 ,信號處理后采用其他無損檢測方法對2#試樣進行檢測,以進行對比驗證。
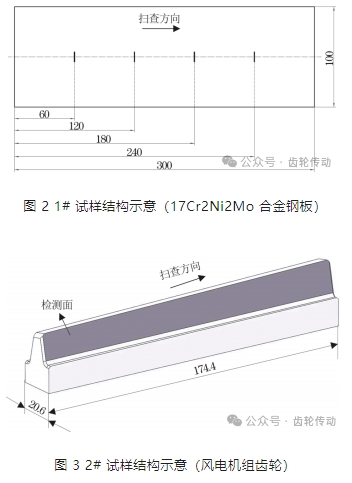
三、試驗結果分析
原始信號分析
分別檢測了1#試樣的正面和背面以及2#試樣,兩個試樣的磁感應強度相差數(shù)十倍,且1#試樣的磁感應強度極差相對較小,其原因是2#試樣在復雜的加工流程和周期性外力載荷的作用下,產(chǎn)生了力磁效應而導致整體的磁感應強度變高。1#,2#試樣的弱磁檢測原始信號曲線如圖4所示。由圖4(a), (b)可以看出,兩次檢測分別在距離為60,120,180,240 mm附近都出現(xiàn)了不同程度的磁異常現(xiàn)象,正面檢測的原始信號中呈下凹狀是因為檢測的是1#試樣正面的表面缺陷,背面同理,此時弱磁檢測信號呈現(xiàn)的變化趨勢和缺陷位置都與實際缺陷情況相符。在圖4(c)中,可觀察到原始信號曲線在距離為30 mm 處存在輕微連續(xù)的變化,在距離為130~140 mm處有下凹的變化趨勢,此時無法通過肉眼區(qū)分其為干擾信號還是突變的異常信號,故需要進一步利用信號處理方法進行分析,更準確地提取缺陷信號并判別缺陷。
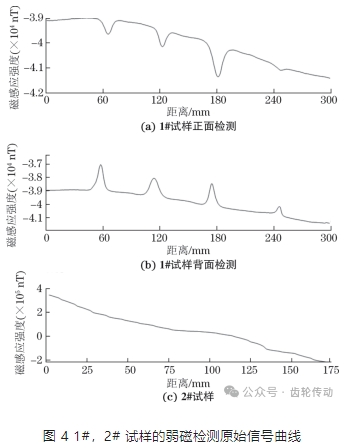
1#,2#試樣弱磁檢測信號處理后的信號曲線如圖5所示,對比磁感應強度可以看到1#試樣的磁感應強度遠小于2#試樣的,這是因為兩試樣的磁導率變化情況有較大的區(qū)別。根據(jù)磁致伸縮效應,受到更復雜機械加工的2#試樣的磁導率變化更大,因此其磁感應強度變化范圍會遠大于1#試樣的,不同試樣間的磁感應強度差異并不影響檢測結果與分析。
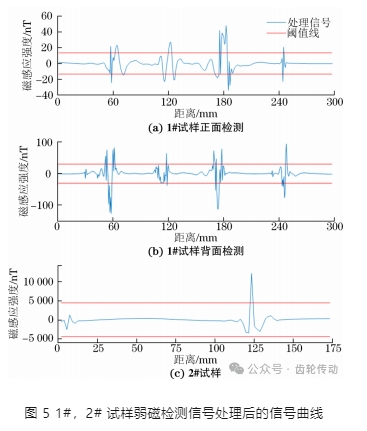
缺陷信號提取
在檢測過程中,弱磁探頭容易受到掃查抖動或者環(huán)境中磁場疊加等因素影響,其所采集的磁感應強度信號曲線也會發(fā)生變化。為了避免雜波對突變?nèi)毕菪盘柕挠绊懀岣呷毕菖袆e的準確性,使用二階差分、小波變換和基于拉依達準則的信號處理方法對原始信號分別進行處理分析。
采用二階差分對原始數(shù)據(jù)進行預處理,可以突出檢測信號的突變點和強調(diào)高頻信號。小波變換適合應用于實際工程領域,同時也適用于處理檢測中采集信號夾帶的瞬態(tài)反常現(xiàn)象,選擇合適的小波基 更利于對特征信號的提取,由于Symlets小波既可以用于連續(xù)小波變換也可以用于離散小波變換,且與弱磁檢測信號有一定的相似度,表現(xiàn)形式為symN(通常2 ≤N≤ 8),與其他小波基函數(shù)相比有較高的對稱性、正則性和相似性。結合弱磁信號特質(zhì),為了取得更高的信噪比和更好的缺陷信號提取效果,筆者選取了sym5小波對原始信號進行處理。
拉依達準則是指在數(shù)據(jù)量n>50的前提下,假設數(shù)據(jù)只含隨機誤差,并根據(jù)貝塞爾公式計算出的試驗標準偏差s作取舍依據(jù),若樣本均值為 x,按一定概率得到一個區(qū)間,認為凡超過該區(qū)間的誤差屬于粗大誤差,含有粗大誤差的數(shù)據(jù)即為異常數(shù)據(jù)。若存在可疑值xj使得殘值數(shù)值ej滿足

則認為該數(shù)據(jù)xj不屬于隨機誤差而是粗大誤差,即為應該剔除的異常值。
將一組檢測數(shù)據(jù)看作數(shù)據(jù)樣本,弱磁探頭所采集的磁感應強度值為xj,若殘值數(shù)值ej >3s,則認為該處的磁感應強度值為異常值,即為需要提取的磁異常信號。因此可將3s作為判別缺陷的依據(jù)。
在圖5中紅線是基于拉依達準則生成的閾值線,其中上閾值線為+3s ,下閾值線為
-3s 。若磁感應強度大于上閾值線或小于下閾值線,認為該位置的采樣點為異常點,則判別該處所采集的弱磁信號為缺陷信號。圖5(a),(b)中兩次檢測信號超過閾值線的部分都很好地對應了實際缺陷,其中正面和背面檢測中距離為240 mm處的突變信號在原始信號中變化很小,經(jīng)過數(shù)據(jù)處理之后明顯突出。通過信號處理,干擾、雜波等影響因素被較好地消除了,如2#試樣原始信號曲線30 mm位置處的雜波被過濾,使得缺陷引起的突變信號更加明顯,說明小波變換和基于拉依達準則生成的閾值線對干擾信號和缺陷信號具有較好的區(qū)分度,能應用于弱磁檢測技術的信號處理中。在圖5(c)中,2#試樣的125 mm處附近信號超過了上閾值線,結合原始曲線判定該位置處附近存在缺陷而引起了突變信號。而原始曲線中該位置的變化起伏較小,據(jù)此可以判斷該缺陷位于表面,同時原始曲線的下凹趨勢持續(xù)較久,一般區(qū)域型損傷或應力集中處才會呈現(xiàn)這種趨勢,故判斷該位置即磨削燒傷處。
CT和巴克豪森噪聲檢測對比試驗
采用工業(yè)CT對2#試樣進行掃描和三維成像,其檢測結果如圖6所示,結合4張圖片可以直觀地了解被檢物體內(nèi)部的結構和損傷情況:被檢試樣中未發(fā)現(xiàn)裂紋、點蝕、磨損等工業(yè)CT能檢測出的缺陷類型。
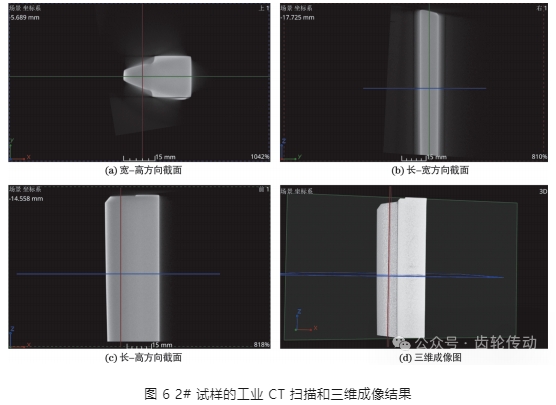
由于工業(yè)CT無法檢測出磨削燒傷,筆者在不損傷試樣的前提下,采用巴克豪森噪聲技術驗證2#試樣是否存在磨削燒傷。
巴克豪森噪聲檢測法(MBN)在檢測鐵磁性材料過程中,遇到硬度或殘余壓應力減小時MBN信號均方根值會增大,故當出現(xiàn)信號在某一區(qū)域曲線突然增大時可以確定其為磨削燒傷。經(jīng)過反復試驗,筆者設置激勵電壓為3 V,頻率為45 Hz以取得最好的檢測效果。根據(jù)拉依達準則畫出上閾值線+3s,作為信號曲線突增程度的判斷依據(jù),若超過閾值線則認為存在磨削燒傷缺陷。2#試樣的MBN均方根值曲線如圖7所示,可見距離為125~130 mm處的 MBN均方根值高于該組數(shù)據(jù)的閾值線,由此可以判斷該位置處出現(xiàn)了異常信號,為磨削燒傷,與弱磁檢測試驗結果一致,驗證了弱磁檢測技術檢測風電機組齒輪的可行性。
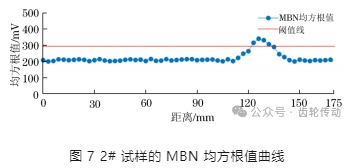
四、結語
通過設計風電機組齒輪缺陷檢測試驗,利用弱磁檢測技術對兩個試樣的不同類型缺陷進行檢測,分析磁感應強度數(shù)據(jù),并利用CT檢測和巴克豪森噪聲檢測進行驗證,得出如下結論。
(1)在地磁場的環(huán)境下,弱磁檢測技術作為風電機組齒輪缺陷檢測的新方法,可有效、快速地對齒輪表面和內(nèi)部裂紋以及磨削燒傷進行檢測,且定位準確。
(2)運用Symlets小波分析并基于拉依達準則取閾值線對弱磁檢測信號進行處理和缺陷判別,在提升信噪比、提取缺陷信號方面有很好的效果,進而能得到更準確可靠的弱磁檢測信號曲線。
參考文獻略.