研究了圓柱線齒輪加工精度檢測方法。首先,根據線齒輪的嚙合特點與齒面構建方法提出線齒輪加工精度檢測方法,并基于此方法研制了加工精度檢測臺。重點介紹了該檢測臺的工作原理、主要系統組成和關鍵結構的設計。進行了加工精度檢測試驗,對銑削加工的塑料線齒輪進行檢測,并簡要分析加工誤差和產生加工誤差的原因。試驗結果表明,該試驗臺能夠實現端面齒廓和接觸線的快速檢測,為圓柱線齒輪的加工精度檢測提供相應的方法和裝置。
線齒輪是一種基于空間共軛曲線的新型齒輪,與傳統齒輪相比具有無根切,設計靈活等特點,經過近幾年的研究,其相關理論與加工技術日趨完善。線齒輪的主要加工方法有靠模法、數控銑削、滾齒加工、激光微燒蝕、3D 打印、冷搓成型和注塑成型等。目前,線齒輪正在應用到行星線齒輪減速器,空間多軸輸出線齒輪減速器等方面,為了保證線齒輪減速器的質量,線齒輪生產過程對加工精度檢測提出了要求。前期研究對激光微燒蝕的錐形線齒輪使用通用超景深設備進行了精度檢測,但該檢測方法對圓柱線齒輪不適用。
齒輪檢測方法主要分為接觸式和非接觸式兩類。目前,主要的非接觸式測量方法是通過三維掃描得到點云數據之后對點云數據進行擬合,再將擬合模型與理論模型進行對比,在對比過程中存在模型位置找正而產生的誤差,找正過程中耗費時間長。現有的齒輪測量中心是針對普通漸開線齒輪開發,造價較高,還不適用于線齒輪的檢測。接觸式測量方法的通用設備是三坐標測量儀,檢測過程中需逐點測量,檢測效率低。為了提高檢測速度與減低成本,本文從線齒輪的嚙合特點與齒面構建方法出發,提出了線齒輪加工精度檢測方法,開發了適用于圓柱線齒輪的加工精度檢測臺,并進行了檢測試驗。
一、圓柱線齒輪加工精度檢測原理
圓柱線齒輪(為表述方便,以下全文簡稱線齒輪)為點接觸嚙合傳動,其接觸線方程為:

式中:m 為接觸線的螺旋半徑;n 為接觸線的螺距;t 為接觸線嚙合點參數,ts 為嚙入點參數 t 的取值,te 為嚙出點參數 t 的取值。
線齒輪的法向齒廓為圓弧齒廓,其方程為:

式中:σ 為線齒法向截圓參數,r 為線齒半徑。如圖 1 所示,線齒輪齒面的構建方法是法向齒廓沿著接觸線進行掃掠得到整個齒面,將線齒輪輪齒進行圓周陣列生成實體得到完整的線齒輪模型,如圖 2 所示。
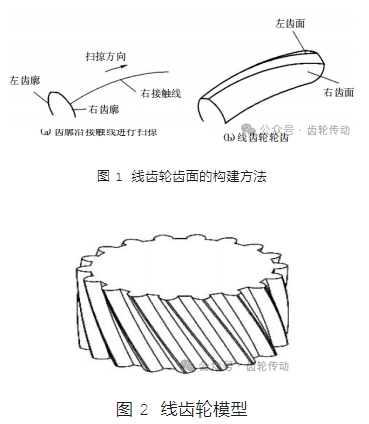
基于以上線齒輪齒面的構建方法,本文提出以接觸線和線齒輪齒廓為檢測項目來評估線齒輪加工精度的方法。線齒輪的齒廓主要分為端面齒廓與法向齒廓,而實際操作中難以實現對法向齒廓的檢測,其齒廓加工誤差可以反映到端面齒廓上,所以本文采用檢測端面齒廓的方式。
線齒輪接觸線檢測原理
線齒輪接觸線的檢測原理如圖 3 所示,齒輪繞齒輪中心旋轉,測頭沿著齒寬方向運動,可獲得線齒輪接觸線的加工誤差。這種檢測方法,測頭頂部圓球的直徑會引起檢測誤差,通過設置測頭與被測線齒輪在測試起點的相對初始位置,可以減小測頭引起的誤差。如圖 4 所示,輪齒的中線繞 O 點旋轉 γ 角度,測頭與被測輪齒齒面在被測點 A 的公法線 n 平行于 x 軸,公法線 n 也是測頭中線,直線 lOA 與輪齒中線夾角為 δ,m 為接觸線螺旋半徑,因此 A 點的坐標為(msin(γ + δ),mcos(γ + δ))。
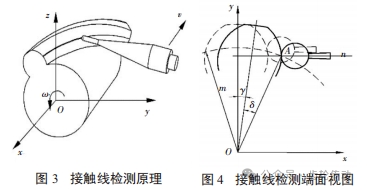
線齒輪端面齒廓檢測原理
圖 5 為端面齒廓檢測原理示意圖,齒輪繞齒輪中心旋轉,檢測傳感器保持靜止,齒輪旋轉一周得到齒輪齒廓。
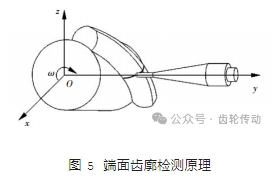
為了進一步說明檢測原理,將檢測過程拆分。如圖 6 所示,被測齒輪以角速度 ω 勻速轉動,被測齒輪與測頭的相對位置由 A 變化到 C,測頭始終指向被測齒輪中心。
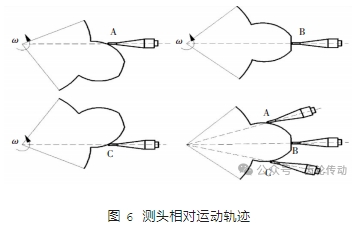
同樣需要對其誤差進行修正,以減小球形測頭所引起的誤差,如圖 7 所示,以齒輪中心為原點,輪齒中線為 x 軸建立坐標系 O-xy,r2 為測頭半徑,r1 為測頭起測半徑。
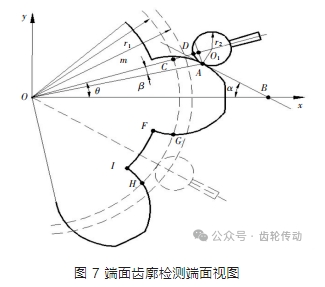
測頭與 x 軸的夾角為 θ,測頭所在位置方向 OO1 與被測點 A 所在位置方向 OA 的夾角為 β,測頭測得的數據 l測為 CD 的長度加上 A 點在 OO1 方向上的加工誤差 ΔAOD,則|OO1|的長度為:

齒廓在 A 點的切線 AB 與 x 軸夾角為 α,因此可得:
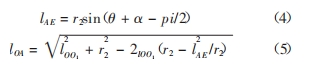
則 A 點可用極坐標(lOA,θ-β)表示。
以內的多邊形區域 FGHI(見圖 7)為未檢測區域,該區域也是非接觸區域,在不發生干涉的情況下該區域不會影響線齒輪傳動,故可以忽略。
從端面齒廓中可獲取齒高,齒厚等信息,齒高會影響兩齒輪之間的嚙合,甚至造成主動輪與從動輪發生干涉,齒厚影響齒輪傳動平穩性,誤差過大會導致齒輪在頻繁變換轉向時產生較大沖擊。
二、線齒輪加工精度檢測臺
檢測臺工作原理
根據以上檢測原理開發了檢測臺,其工作原理如圖 8 所示,被測線齒輪安裝在 A 軸上,檢測臺有 X、Y、Z 軸三個移動自由度,在 X 軸和 Y 軸上分別裝有光柵尺,行程 100 mm,分辨率 1 μm,采集 X 軸和 Y 軸的位移信息;在 Z 軸上安裝有高精度位移式傳感器,分辨率達 1 μm,其輸出差分信號,用于采集齒輪的齒面信息。在 Z 軸上還設置有千分刻度尺,用于 Z 軸的精確定位。轉動軸 A 軸由與之相連的伺服電機驅動,其位置信息通過伺服電機中的內部編碼器進行采集。上位機將采集的數據進行處理,轉換為 A 軸的旋轉角度,該角度即為被測齒輪的旋轉角度。

檢測臺機械系統設計
檢測臺整機結構:檢測臺的整機設計要保證一定的剛度和柔性。電機轉動會產生振動,良好的支撐鋼架和固定裝置可以減小振動產生的影響和抵抗受力變形。檢測臺使用柔性較好的伺服電機,啟停平穩保證較高的運動精度;并且設計了相應的柔性機構,在發生干涉或產生沖擊時能起到自我保護作用,提高檢測精度與整機使用壽命。
線齒輪加工精度檢測臺的結構如圖 9 所示,采用三坐標布置形式,結構簡單,便于操作,主要包括:檢測傳感器、XY 移動臺、伺服電機、Z 軸升降臺、光柵尺、工作平臺、微調裝置、齒輪夾持裝置。光柵尺 1 和 光柵尺 2 分別設置在 XY 方向上,精準獲取檢測傳感器的位置,實時采集位置信息。底座工作平臺采用大理石,具有不易變形,硬度高,耐磨性好等優點。
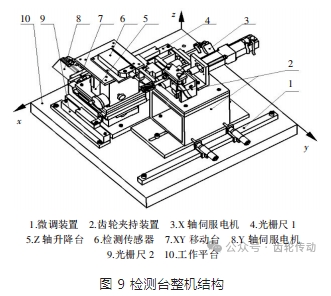
齒輪夾持裝置:夾持裝置是檢測臺重要的組成部分,采用三端夾緊可調節形式,方便線齒輪的快速裝夾,以適應不同參數線齒輪的檢測。圖 10 所示滾子一、滾子二與上頂滾子夾住齒輪夾持棒,被測線齒輪裝夾在齒輪夾持棒上,滾子由伺服電機驅動,滾子與齒輪夾持棒之間的傳動通過摩擦力實現,該夾持的優點是具有自保護功能,在不發生相對滑動的情況下可以進行齒輪檢測,當檢測傳感器與被測齒輪發生意外干涉,齒輪夾持棒與兩滾子之間發生相對滑動,可以保護伺服電機和檢測傳感器不受損壞,提高檢測臺的使用容錯率,符合柔性設計。
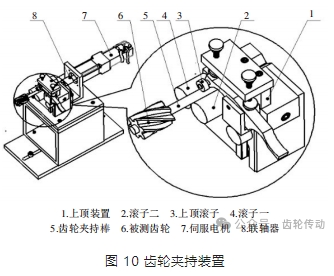
檢測臺控制系統
檢測臺的控制系統主要包括上位機,控制卡和控制器。上位機將檢測命令發送到控制卡,控制卡將信號發送給電機驅動器,由驅動器帶動伺服電機轉動,實現檢測的運動控制。控制卡集成了數據采集模塊,上位機讀取控制卡所采集的點云數據并保存在到本地磁盤。所有數據同步采集,采集信號由上位機發出。控制程序在上位機中運行,使用坐標插補的形式控制檢測傳感器與被測線齒輪的相對位置。控制程序流程圖如圖 11 所示。程序采用 C++編寫。
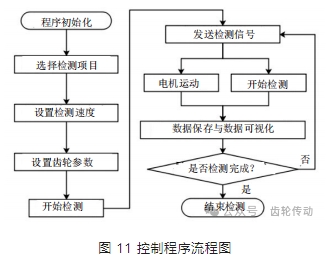
三、檢測試驗與結果分析
檢測試驗
基于以上設計制造的線齒輪加工精度檢測臺如圖 12 所示,使用專用數控銑床加工的線齒輪進行檢測實驗,如圖 13 所示,其材料為聚甲醛,線齒輪參數如表 1 所示。
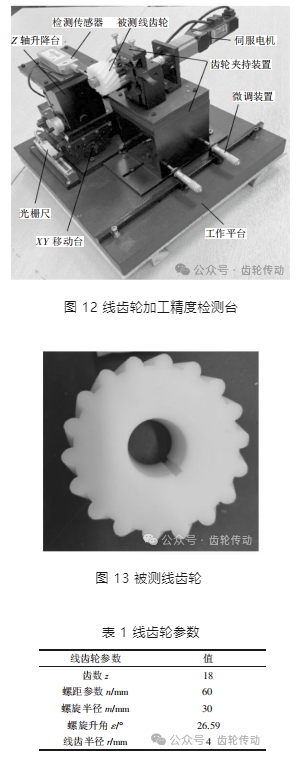
開始檢測前需要對檢測臺進行校準,主要調節齒輪夾持棒與 x 軸導軌的平行度,采用微調裝置進行微調,校準后測量得到齒輪夾持棒與 x 軸導軌的平行度誤差為±1 μm。齒輪夾持棒旋轉時的徑向跳動也會影響檢測精度,通過測量得到齒輪夾持棒的徑向跳動為±1.5 μm。
伺服電機控制模式選用位置與脈沖形式,在采集數據時,既要采集足量的數據點,也要盡量減少檢測時間,這樣才能保證檢測精度和節約時間成本。本文實驗采用的檢測速度為 0.02 mm/s,可根據需求修改檢測速度。伺服電機編碼器的分辨率為 24 bit,所以伺服驅動器中電子齒輪比設置為(16777216/ 5000),選取多個齒與多個端截面分別進行檢測,采集的數據點以(θ,Δm,x)的形式存儲,其中 θ 為齒輪轉過的角度,Δm 為加工誤差,x 為檢測傳感器 x 軸的坐標值。
結果與分析
使用 MATLAB 對測得的數據進行擬合,得出接觸線加工誤差為 7 μm。為了更方便地表示誤差,將(θ,Δm,x)形式存儲的數據點用 xyz 空間坐標系表示,轉換公式如下:
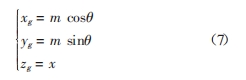
式中:m = Δm + y0,y0 為檢測傳感器軸坐標值。
轉換得到(xg,yg,zg)坐標集合,使用 ScanTo 3D 插件將坐標集合導入 Solidworks,并參照線齒輪的理論模型,采用 Solidworks 內置的測量工具,直接測出加工誤差。導出的 CAD 圖如圖 14 所示。

由于檢測傳感器的局限性,齒根附近區域無法檢測,但由于線齒輪傳動過程中該區域不參與嚙合,可以忽略這部分的檢測。將檢測數據點通過 MAT- LAB 計算或者導入 CAD 軟件后使用 CAD 測量工具進行測量,可得到接觸線所在位置的齒厚誤差為 17 μm。由圖 15 可知,接觸線加工誤差 Δ < 9 μm,齒高加工誤差為 19 μm。
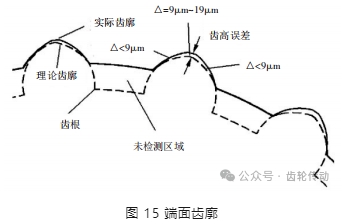
以上結果表明,被測線齒輪接觸線區域的加工精度較好,齒廓的整體加工精度較差。造成以上加工誤差的主要原因有齒胚加工誤差,齒坯裝夾誤差和刀具廓形加工誤差,更重要的原因是數控銑削加工塑料齒輪的切削力對塑料的彈、塑性影響等。
在加工線齒輪的時候,需要保證接觸線加工精度的同時,也需要保證齒根區域與齒頂區域在嚙合過程中不發生干涉,齒廓非接觸線區域的加工精度對線齒輪的傳動精度沒有影響。
總之,線齒輪為兩條空間共軛曲線的嚙合傳動,本文根據線齒輪的嚙合特點與線齒輪齒面構建方法,提出簡化的線齒輪加工精度檢測方法,本文開發的線齒輪加工精度檢測臺操作簡單,主要檢測線齒輪齒廓和接觸線的加工誤差。檢測實驗結果證明了其適用性。
四、結論
本文提出了圓柱線齒輪的加工精度檢測方法,并開發了圓柱線齒輪加工精度檢測臺,得到以下結論:
(1)該檢測臺通過檢測線齒輪的端面齒廓與接觸線的加工誤差即可判斷線齒輪的加工精度,減少了檢測時間,提高了檢測效率。
(2)本文工作為線齒輪的產業化提供了加工精度檢測的相關理論依據與方法,但對于線齒輪加工精度等級的確定方法等,還有待進一步研究。
參考文獻略.