滾齒是利用展成原理加工齒輪的一種方法,相比較于插齒、剃齒等方法具有生產效率高、成本低的特點,但是滾齒中的滾刀屬于生產成本環節中的消耗品,普通高速鋼滾刀加工一段時間后由于前刀面磨損,需進行重磨,對于新型的涂層雙切滾刀則需要進行退涂、重磨、涂層的復雜流程,每次使用后的修復成本能夠達到滾刀成本的20%左右,如何控制滾刀磨損不僅是企業生產成本的控制環節,也是企業生產效率提升的重要環節。Maiuri分析了影響滾刀壽命的因素,包括材料、涂層、切削參數等;張榮闖等對滾齒切 削力進行了預測,并計算了切削力模型;張應等建立了滾刀壽命預估模型并優化,但是該模型計算復雜。
本文針對以上研究的不足,提出了通過六西格瑪實驗設計研究影響滾刀壽命的顯著性因子,并根據實驗數據擬合出提高滾刀壽命的最佳工藝參數,并通過實際加工進行驗證。
一、高速雙切滾刀特點及現狀
滾齒加工是按照展成原理來實現切削加工的,滾刀與工件的嚙合相當于一對交錯軸的螺旋齒輪嚙合,滾刀可以看作是一個齒數很少、螺旋角很大的齒輪,在這個齒輪垂直于螺旋線方向開出容屑槽,并磨削出前刀面、后刀面。高速雙切滾刀又稱為重切滾刀,是一種具有較多切削槽的涂層整體滾刀,與傳統滾刀相比,其具有更長加工壽命和更短切削時間的特點。雙切滾刀材質為粉末冶金高速鋼,并在其表面增加 PVD 氮鉻化鋁涂層,該滾刀在設計時采用主齒和副齒結構,在相同的外徑時,切削刃能夠增加一倍。雖然雙切滾刀優勢明顯,但是刀具的磨損還是無法避免,不管是前刀面還是后刀面,當受到加工溫度、加工振動、工件材質和機床剛性等的影響時都會造成刀具磨損,特別是加工溫度越高,刀具材料就會變得越軟,耐磨性就會越差,雖然加工過程中75%~80%的熱量會通過切削液或者鐵屑帶走,但是隨著加工溫度的升高,刀具使用壽命會急劇降低,因此必須選擇合理的加工工藝以提升雙切滾刀的實際使用壽命。
二、滾齒加工工藝參數
在滾齒加工過程中,企業為了利潤最大化,要求在保證產品質量的前提下提高加工效率,而這一切都與滾齒加工工藝參數有關。滾齒加工工藝是依據零件圖紙、機床設備、刀具參數和夾具結構等確定的,工藝制定后,如何選取合適的滾齒工藝參數是各企業研究的 重要內容,參數選擇不合理容易造成零件加工不合格、滾刀快速磨損和節拍降低等問題,滾齒工藝參數包括滾刀轉速、滾刀軸向進給速度、切削次數和切削深度等,滾齒工藝參數直接影響滾刀使用壽命。
三、滾刀磨損現象
滾刀在使用時隨著時間和加工次數的增加,在滾刀后刀面或者前刀面會出現月牙灣狀磨損,當磨損的寬度達到0.2mm 時就需要對滾刀進行退涂、重磨、涂層工序,0.2mm 的磨損寬度可以通過電子顯微鏡來進行測量,如果磨損達到0.2mm 仍然繼續使用,在加工過程中會出現加工工件及刀具溫度急劇上升,造成滾刀磨損急劇加大,嚴重時可能造成滾刀報廢。
四、六西格瑪滾刀壽命實驗研究
實驗目的:
為了提高企業加工效率,降低高速雙切滾刀重磨、涂層次數特提出此實驗要求,通過實驗,確定影響滾刀壽命的顯著因子,并通過數據分析這些因子對滾刀壽命的影響,以刀具磨損達到0.2mm為滾刀壽命界限、刀具壽命最大化為優化目標,擬合最優滾齒加工工藝參數。
實驗條件及特征因子確定:
實驗零件參數:齒輪類零件,模數 18 mm,齒數 31,壓力角20°,全齒高42.3mm,齒寬500mm,材料為18CrNiMo7,調質硬度 HB217~HB255。
實驗滾刀參數:高速雙切滾刀,模數18mm,每圈齒數18,壓力角20°,材料為粉末冶金高速鋼,硬度為 HRC65~HRC68。
從雙切滾刀加工工藝及現場情況來看,影響雙切滾刀壽命的特征因子有滾刀轉速、滾刀軸向進給、切削次數和冷卻方式。
實驗方法:
實驗設計是一種安排實驗和分析實驗數據的數理統計方法,通過前期的策劃和研究,能夠以較小的實驗規模、較少的實驗次數和較低的實驗成本得到理想的實驗結果和科學的結論。
本文采用全因子實驗,共選取4個因子 X,試驗指標為雙切滾刀壽命 Y,共計16次實驗,實驗中對各因子分別取高、低兩種水平,通過實際加工和檢測來統計滾刀壽命。
實驗因子選擇和水平設定:
依據滾刀廠家推薦參數及實際加工過程中使用經驗,設置4個因子 X的高、低水平,如表1所示。

實驗結果分析:
通過16 次實驗,將雙切滾刀壽命統計后經過 MINITAB分析所得標準化效應 Pareto圖如圖 1 所示,圖中橫坐標為六西格瑪檢驗統計量t值,分界線為依據選定的顯著性水平α=0.05給出臨界值2.57,超出該值的因子為顯著因子。因子 A 為滾刀轉速,B為滾刀軸向進給,C為切削次數,D 為冷卻方式,BC為滾刀軸向進給和切削次數交互效應,BD 為滾刀軸向進給和冷卻方式交互效應,AD 為滾刀轉速和冷卻方式交互效應,AB為滾刀轉速和滾刀軸向進給交互效應, AC為滾刀轉速和切削次數交互效應,CD 為切削次數 和冷卻方式交互效應。從圖1中可以直觀地分析出影 響滾刀壽命的最主要因子為滾刀軸向進給,其次為滾 刀轉速,而切削次數和冷卻方式交互效應對滾刀壽命影響最小。
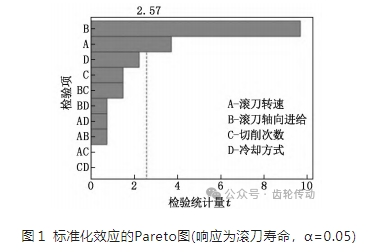
分析完主要因子和次要因子后,還需對殘差狀況進行診斷,以此來判斷分析模型是否合適,圖2為滾刀壽命殘差圖。圖2(a)顯示各點近似在一條直線;圖2(c)中矩形左右對稱,可認為該實驗設計的殘差近似服從正態分布;圖2(b)和圖2(d)顯示該實驗設計的殘差基本符合隨機波動。從殘差圖的分析來看,本次實驗模型基本滿足要求。
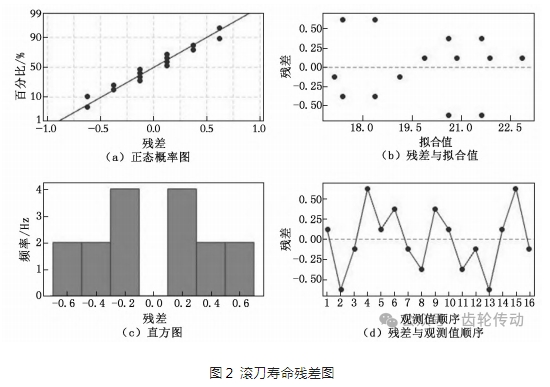
方差分析能夠直觀地根據結果來推斷哪些因子對結果有明顯的影響以及影響有多大,表2為方差分析結果。通過表2結果中的檢驗水平P 值大小來判斷因子是否顯著,P 值小于0.05為顯著因子,而滾刀軸向進給和滾刀轉速的P 值小于0.05,因此為顯著影響因子。
通過 DOE(DesignOfExperiments)實驗設計及分析,可得出以下結論:
(1)影響雙切滾刀壽命的顯著因子為滾刀軸向進給,軸向進給的大小直接影響雙切滾刀壽命。
(2)次顯著因子為滾刀轉速,滾刀轉速較高時滾刀壽命會有所下降,但不如軸向進給影響顯著。
(3)冷卻方式對雙切滾刀壽命影響較低,所以在實際加工中采用油冷和風冷對滾刀壽命影響較小。
(4)切削次數對雙切滾刀壽命影響較低,在加 工時為保證加工效率可采用較少的切削次數。
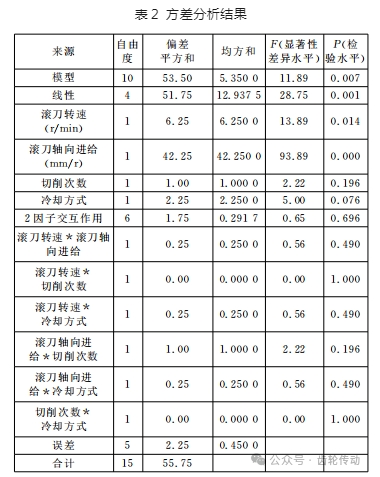
優化工藝參數:
通過去除不顯著因子,修正回歸方程,對響應參數優化設計后,擬合出最佳的工藝參數如表3所示。通過對該參數分析,在主要因子滾刀軸向進給取低水平、滾刀轉速取低水平時擬合的滾刀壽命取值最大,并且復合合意性比較接近1,總體看來此設置能夠為所有 響應獲得一個較好的結果。
根據擬合后的參數進行現場實驗驗證,通過對油冷機床多批次零件加工時的參數調整,高速雙切滾刀壽命符合預期效果,說明該參數具有一定指導作用。
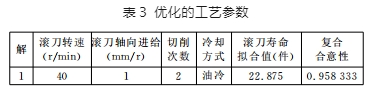
五、結論
高速雙切滾刀在實際應用中能夠極大地提升企業加工效率,但是滾刀磨損、退涂、修磨、涂層占用了滾刀很多的使用時間,并且滾齒加工是一個復雜的工藝過程,如何延長高速雙切滾刀使用壽命是急需解決的企業生產瓶頸。本文通過六西格瑪實驗設計,通過較少的實驗次數、經濟的實驗方法獲得了最佳的結果,并且分析了影響滾刀壽命的因子,優化了加工工藝參數,通過實際使用,達到了預期目的,并且將 DOE 實驗設計應用于滾齒工藝參數優化,為其他機械加工工藝參數優化提供了新的思路。
參考文獻略.