諧波減速器依靠柔輪的彈性變形來實現運動與動力傳遞的目的,它具有結構緊湊、傳動比大、輕量化和高精度等優點,被廣泛用于航空航天、機器人、精密光學設備等機械領域。諧波減速器在航天衛星及其他各類航天器的各種驅動機構、高精度指向結構和著陸裝置轉移機構上得到廣泛應用。柔輪作為諧波減速器的核心部件,運轉過程中在交變載荷的作用下容易發生疲勞斷裂,這是減速器重要的失效形式,所以研究柔輪的應力分布及變形規律顯得尤為重要。隨著計算機技術的快速發展,有限元仿真軟件應用于各個領域。利用有限元仿真軟件不僅可以對減速器運行狀態進行準確的分析,還大大節省了試驗成本。
在諧波減速器的有限元仿真研究中,張寧等提出了一種輪齒齒廓線的修正方法,證明優化后的諧波減速器預計壽命提升超過20%。張超等對柔輪進行了疲勞分析,但是計算時把柔輪等效簡化成當量厚度的光滑殼體,準確性不足。楊宇通等使用響應面優化分析和中心復合設計方法發現較大的外圈溝曲率半徑可減小柔輪和軸承外圈的應力,提高柔輪使用壽命。Liu Chunjian 等分析了柔輪的應力分布及變形規律,Dong Huimin等研究了柔輪的變形特性。王亞珍等采用ANSYS Workbench分析了柔性薄壁軸承內外套圈在實際工作載荷及預變形作用下的變形、應力以及載荷分布規律。張林川等使用 ANSYS Workbench 建立了柔性軸承的參數化模型,對不同溝曲率半徑系數的柔性軸承進行靜力學接觸分析,得到了不同參數的柔性軸承的變形規律。相關研究有很多,但目前對諧波減速器柔輪的研究主要集中于杯形柔輪,缺乏對禮帽形柔輪的研究。本文設計了一種合理簡化的禮帽形諧波減速器模型,分析了不同載荷下柔輪與剛輪的嚙合特性,對柔輪進行了應力分布和變形規律分析,通過對柔性軸承的應力變形研究驗證了柔輪非線性變形的原因。本文分析結果為柔輪壽命研究提供了一定的理論依據。
一、諧波減速器有限元分析模型的建立
本文以某禮帽形諧波減速器為主要分析對象。禮帽形柔輪在負載增加的情況下所受應力的增幅遠遠低于杯形柔輪的增幅,因此比較適合大負載傳動,柔輪與剛輪的齒廓采用雙圓弧形式,凸輪為標準橢圓且近似為剛體。根據減速器負載和安裝要求,給出柔輪的結構簡圖如圖1所示,柔輪與鋼輪的基本參數取值見表1。
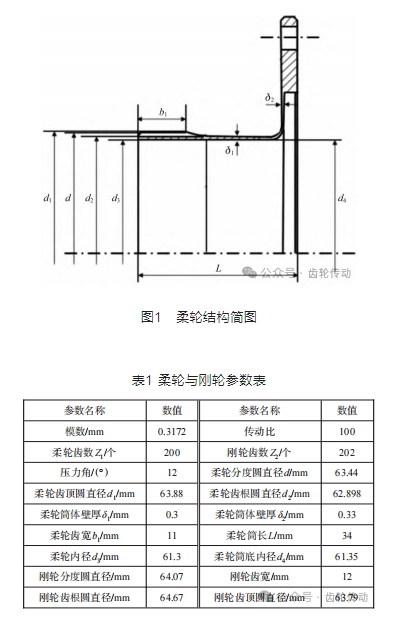
柔性軸承作為波發生器中最主要的組成部分,它與普通軸承有顯著的區別,柔性軸承的內外圈壁厚很小且具有柔性,因此在與凸輪裝配后可以隨著凸輪輪廓曲線產生強制彈性變形。根據靜力學分析,滾子在周向的位移主要受保持架約束,各個滾子之間周向間距基本不變,所以在進行有限元分析時將波發生器簡化為不含保持架的柔性軸承和凸輪兩部分。軸承外圈外徑應和柔輪變形前的內徑相等,柔性軸承的參數見表 2。在三維建模軟件 SOLIDWORKS 中,以凸輪軸向為Z軸、短軸為X軸、長軸為Y軸完成減速器三維模型的裝配,如圖2所示。
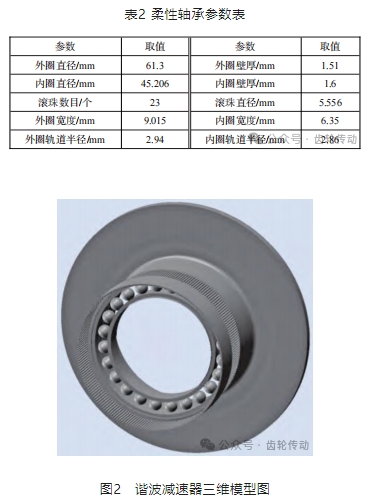
利用CAE前處理軟件ANSA對三維模型進行網格劃分,凸輪采用剛性單元,其他可變性單元采用6面體8節點縮減積分單元C3D8R,網格模型圖如圖3所示。將劃分好的網格模型導入Abaqus中,設置減速器各部件的材料屬性,選用具有高強度、足夠韌性和淬透性的合金鋼30CrMnSiA作為柔輪材料,剛輪采用強度適中且具有一定抗變形能力的碳素結構鋼(45 鋼),柔性軸承選用軸承鋼,凸輪等效為剛性體。在傳動過程中,主要有4對接觸副,分別為柔輪外齒與剛輪內齒的接觸、柔輪內壁和柔性軸承外圈之間的接觸、凸輪與柔性軸承內圈之間的接觸以及柔性軸承內部滾子與內外圈溝槽之間的接觸。摩擦系數設置為0.1,法相剛度系數為0.1,同時采用增廣拉格朗日算法。打開大變形非線性開關,柔輪帽檐兩側都采用固定約束,剛輪只釋放Z軸的旋轉自由度,剛性凸輪參考點只被允許沿著Y軸產生位移。
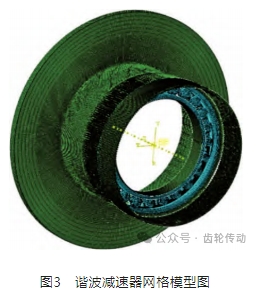
二、柔輪的嚙合特性和應力變形分析
柔輪嚙合特性分析
諧波減速器工作過程中,柔輪(FS)和剛輪(CS)的嚙合齒對和齒面承載情況會對柔輪的變形產生嚴重的影響,所以柔輪與剛輪的嚙合特性是正確獲取柔輪不同位置應變分布規律必須考慮的因素,圖4給出了不同負載扭矩下柔輪上接觸齒對數量和接觸條紋沿著軸線和周向的變化情況。從圖4中可知,在裝配完成沒有負載的情況下,嚙合齒對存在干涉情況,干涉位置主要在長軸靠近端面處,主要原因是柔輪發生橢圓變形后其外端面的徑向位移量最大。當負載逐漸增大時,柔輪變形重新進行載荷分配,柔輪上參與嚙合的齒對數也隨之增加,長軸處具有最長嚙合長度,單齒嚙合長度逐漸向杯底靠近。
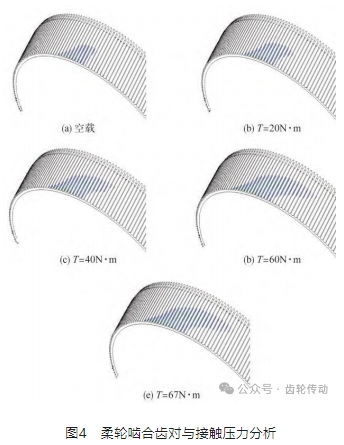
為進一步分析剛輪與柔輪嚙合過程的不同載荷對其嚙合特性的影響規律,圖5給出了嚙合齒對數和最大嚙合壓力隨著負載扭矩的變化情況。從圖5中可知,隨著剛輪上負載的增加,最大嚙合壓力增大,剛輪和柔輪嚙合齒對數逐漸上升,兩者變化規律基本一致;當負載達到額定負載時,嚙合齒對數增至27個齒,由于柔輪的長軸兩端嚙合特性基本一致,可認為總嚙合齒對數達到54個;負載為20N·m時,其最大接觸壓力約為197MPa;當負載上升到67N·m時,最大接觸嚙合壓力也上升到了224MPa左右;當負載增大三倍時,其最大接觸壓力只增加了約14%,嚙合齒對數增加了約 68%,柔輪可以在負載變化下通過有效的周向的彈性變形實現載荷在齒對間的重新分配,所以負載的變化并不會顯著引起嚙合齒對接觸壓力的變化,所以更應該關注負載波動給柔輪杯體變形和支撐軸承帶來的影響。

柔輪應力與變形分析
圖 6 給出了整個柔輪上的等效 Mises 應力分布情況。從圖6中可知,不同載荷下柔輪的Mises應力(米塞斯應力)分布規律幾乎一致,即柔輪的最大等效Mises應力位于筒體與帽底上的過渡圓弧的長軸和短軸對應位置,由于柔輪發生橢圓變形后,長軸位置是往筒壁外擴張的,所以在長軸上形成了壓應力,而短軸是往筒內拉升的,在短軸位置形成了拉應力。由于柔輪齒圈的周向變形導致載荷在齒上重新分配,所以柔輪最大Mises應力的位置幾乎都是位于過渡圓角上,且負載對其影響似乎并不顯著。
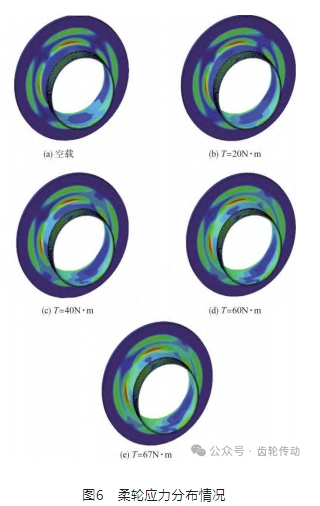
但是柔輪失效往往是過渡圓弧的疲勞斷裂導致的,所以有必要考慮負載作用下引起的應力分量變化。圖7給出了空載與負載為67N·m時柔輪過渡圓弧上剪應力的變化情況,從圖7中可知,在空載時過渡圓弧位置剪應力在圓弧上的分布主要是由橢圓變形引起的,而在加載后,剪應力在圓弧位置顯著增至70MPa,上升幅度約為75%,所以考慮負載波動影響下柔輪過渡圓弧材料的剪切失效是研究柔輪杯底斷裂的主要因素。
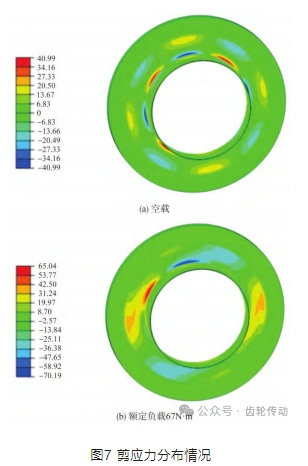
由于嚙合的核心位置為柔輪長軸處,柔輪的實際徑向變形量對嚙合深度也有重要影響,研究柔輪徑向變形量對正確選擇設計齒形時的理論徑向變形量、凸輪的修型參數等有重要意義。圖8給出了柔輪長軸位置的徑向變形量和杯體上三個截面位置的周向變形,空載下的周向變形和長軸的徑向變形最大。空載狀態下,柔輪的周向變形曲線在柔輪長軸兩側對稱,加載后周向變形曲線均沿著負載方向發生了偏移。
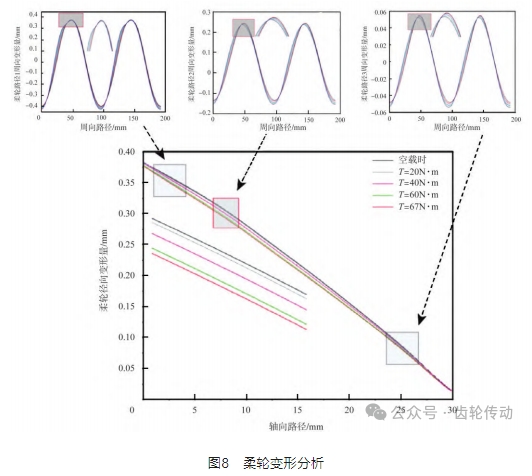
柔輪沿著軸向的徑向變形量與距離并不是線性關系,而是具有非常明顯的非線性特征,在越靠近杯口的位置其非線性特征越明顯,隨著負載的增加,柔輪的最大徑向變形量逐漸減小,而不同載荷下變形量差別最大的位置并不是柔輪端面,而在靠近端面距離約7mm的位置,即柔輪齒軸向最大嚙合深度位置,該位置嚙合齒數寬度最長而且嚙合齒數最多,嚙合齒對分擔了絕大部分負載,所以加載后該位置受沿著齒面法向載荷作用產生壓縮變形最大,導致其徑向變形量減小最明顯。
三、柔性軸承應力與變形分析
為了進一步探究造成柔輪應力分布及變形規律的原因,對同樣具有柔性的薄壁軸承進行分析顯得十分必要。圖9為柔性軸承在空載和受載時的徑向變形云圖,從圖9中可知,柔性軸承被剛性凸輪撐開后,其長軸和短軸的最大徑向變形為0.38mm,已知理論的徑向變形量為0.3805mm,與有限元分析結果基本一致;在鋼輪上施加額定負載67N·m 后,柔性軸承的長、短軸變形略有變化。
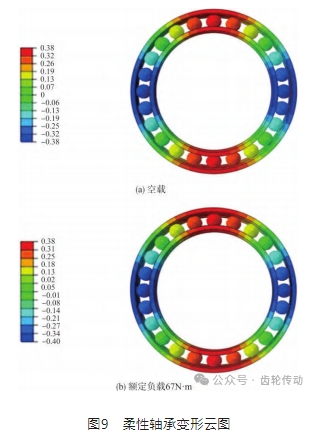
加載后柔性軸承外圈的徑向變形量變化較內圈變化明顯,圖10詳細給出了空載和加載狀態下沿著軸承圓周方向其外圈外端面的徑向變形情況,加載后外圈長軸的徑向變形減小,而短軸增大,這是因為加載后長軸端受到了柔輪上嚙合齒的載荷作用而壓縮長軸,軸承沿著扭矩方向轉動,導致短軸的徑向變形增大。
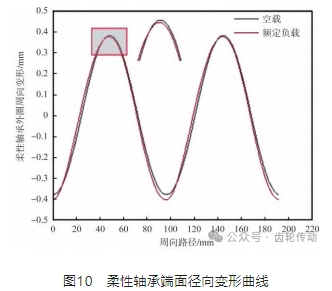
分析了外端面周向的徑向變形后,進一步分析軸承外圈長軸位置處沿著軸線方向的徑向變形量,如圖11所示,其中橫坐標表示分析位置到軸承外端面的距離,與圖10對應處的受載荷軸承長軸位置的徑向變形沿著軸線都變小,且在內端面位置達到最小徑向變形。
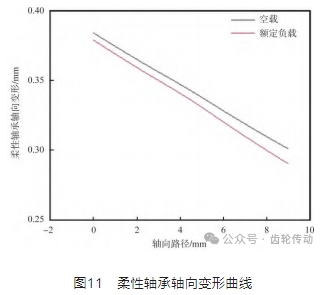
為了進一步分析軸承在軸向的徑向變形特征,圖12給出了軸承在長軸上的剖面變形云圖。從圖12中可知,實際情況下的柔性軸承變形遠比等效凸輪復雜。實際上,由于柔性軸承內圈表面與凸輪表面屬于過盈配合,其徑向位移受到凸輪限制,軸向徑向變形基本一致;而軸承外圈沿著軸向卻有非常明顯的傾斜,導致軸承外圈呈現出喇叭口的變形,主要是因為軸承外圈在安裝過程中是由柔性軸承和滾子約束其徑向位移的,所以在柔性軸承裝入柔輪并發生橢圓變形后,外圈與柔輪內壁的接觸是從軸承內端面至外端面,導致軸向并不是都與柔輪內壁發生了接觸,這也是柔輪徑向變形量沿著軸向呈現出非線性的主要原因。
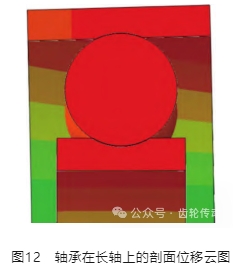
柔性軸承的復雜徑向變形除影響柔輪齒廓設計外,軸承內部的接觸壓力分布也會對軸承的壽命產生重要影響。圖 13 為軸承外圈在空載和負載情況下的應力分布云圖。從圖13中可知,在空載狀態下軸承外圈長軸端接觸滾子總數為5個,且滾子在長軸兩側對稱分布,滾子與滾道沿著長軸方向呈細長橢圓形接觸;空載下外圈滾道上最大接觸壓力為 318.3MPa,而加載后外圈滾道最大壓力上升到了 419.45MPa,滾道上的接觸壓力分布規律顯著發生變形,其壓力分布不再對稱,而是向長軸的一側偏移。

圖 14 給出了軸承空載和加載下滾子與外圈接觸時滾子的接觸壓力分布情況。從圖中可知,滾子上接觸壓力呈現細長橢圓形,加載前與外圈接觸的滾子位置具有最大接觸應力為529.1MPa,而加載后該位置的接觸壓力上升到679.9MPa,且滾子壓力分布也與滾道類似,沿著長軸一側偏移。
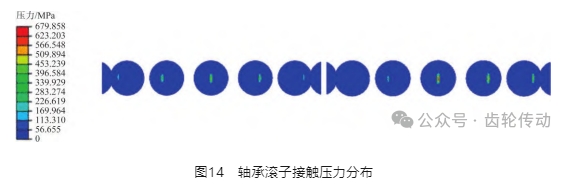
為了進一步分析軸承上的壓力變化情況,圖15給出了軸承外圈滾道上壓力在加載前和加載后沿著周向的分布情況。滾子和內圈滾道上加載前后壓力分布與之相似,此處不贅述。加載后滾道壓力峰值顯著升高,且壓力分布不再沿著長軸對稱,而是出現明顯的位置偏載,除了位置偏載外,其壓力沿著扭矩的周向作用方向從長軸位置沿著一側逐漸減小。通過上述分析結果可知,柔性軸承滾道上的壓力分布與目前理論計算時假設的軸承壓力分布顯著不同。
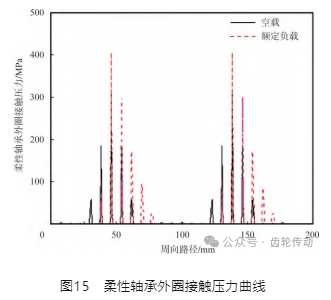
四、結論
通過研究,可以得出以下結論:
(1)當負載從 20N·m 增至 67N·m 時,柔輪與剛輪的最大接觸壓力只增加了約14%,嚙合齒對數增加了約68%,表明柔輪可以在負載變化下通過有效的周向的彈性變形實現載荷在齒對間的重新分配,負載的變化并不會顯著引起嚙合齒對的接觸壓力的變化。
(2)不同載荷下柔輪的Mises應力分布規律幾乎一致,柔輪的最大等效Mises應力位于筒體與帽底過渡圓弧處的長軸與短軸對應位置。隨著負載的增加,切應力上升幅度大,剪切失效是柔輪杯底斷裂的主要原因。隨著負載的增加,柔輪的最大徑向變形量逐漸減小,變化最大的位置并不是柔輪端面,而在柔輪軸向最大嚙合深度位置,該位置嚙合齒數寬度最長而且嚙合齒數最多,分擔了絕大部分負載。
(3)軸承外圈呈現出喇叭口的變形是柔輪徑向變形量沿著軸向呈現出非線性的主要原因。加載前,軸承滾道和滾珠的壓力沿長軸兩側對稱分布,加載后其壓力分布會發生明顯的位置偏移。這些分析結果可以為柔輪齒廓設計和實際減速器壽命研究提供理論支撐和幫助。
參考文獻略.