差速器是汽車底盤動力傳遞的重要部件之一,其組成主要有行星齒輪、半軸齒輪、差速器殼、十字軸等零件,其作用就是滿足汽車轉彎時兩側車輪轉速不同的要求,使汽車能夠順利過彎。在整個動力傳遞過程中,差速器殼起著支撐、連接、傳遞扭矩的作用。本文通過對差速器殼軸承安裝外圓采用磨床加工和數控車床加工工藝的對比,分析影響加工質量的因素,從而制定出合理的加工工藝,制造出高精度、低成本的產品。
一、現狀描述
我公司生產的某系列差速器殼工藝流程:OP10 車大端(數車)—OP20 車小端(數車)—OP30 滾花鍵(滾齒機)—OP40 磨削(磨床)—OP50 鉆孔(組合機)—OP60 倒角(立鉆)—OP70 攻絲(搖臂鉆)—OP80 銑鍵槽(銑床)。
由上述工藝流程可以看出,該產品過程工藝鏈比較長,且大多采用普通設備加工。其中磨削工序主要加工差速器殼軸承安裝外圓,采用 MB1632 普通外圓磨床加工,設備如圖 1 所示,磨削過程中存在以下問題:
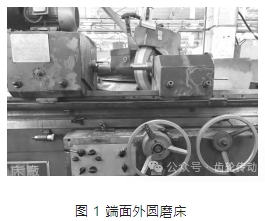
(1)與其他切削過程相比,磨削的比切削能量大、速度高,能量消耗也更高。這些能量絕大部分轉化為熱能,其中約有 80%傳入工件。當局部溫度很高時,加工表面就會出現種種熱損傷及熱變形,影響加工表面質量與加工精度。如我公司生產的某差速器殼,其端面在磨削后放置 5~ 8 s 時出現裂紋,經分析為砂輪磨粒鈍化后,磨削高溫不能很快導出,致使產生磨削裂紋。故在后續生產中,砂輪修磨頻次由原來 1/10 更改為 1/6,砂輪修整頻次提高,不但導致生產效率較之前降低,同時因砂輪頻繁修整,消耗加快,導致生產成本增加。
(2)普通磨床加工極易受人為因素(如情緒波動、體力強弱、技術水平高低等)干擾,操作者的技能直接影響加工效率和產品的加工精度。如圖 2 所示,為保證差速器殼軸承安裝外圓根部圓弧 R3.5,操作者需手動修整砂輪圓角,過程不但危險且修整的圓弧形狀不規則,其次磨床 Z 向無刻度盤,軸向尺寸的控制主要依靠操作者對磨削火花的經驗判定,導致尺寸穩定性差。經統計, 2020 年磨床崗位因人為原因造成的不良品共計 18 件,廢品損失金額 2 041 元。
(3)磨削過程中產生的粉塵、有害氣體及廢棄物會對職業健康及環境造成危害。隨著經濟和制造技術的高速發展,制造業呈現出一些新的特征:產品綠色化,所提供的產品必須在全生命周期內資源消耗低,無污染或少污染,而磨削加工是微量切削,產生的金屬磨屑、脫落的磨料及黏合劑等形成的微細粒粉塵極易被人吸收而影響身體健康。為了減少環境污染,公司對磨削產生的砂輪灰、廢舊砂輪、油泥需進行危廢處理,費用每噸約 2 400 元(價格隨國家環保調控),致使生產成本增加。
綜合以上原因,并結合公司目前生產模式由傳統人工操作向自動化、柔性化、集成化的轉型趨勢,我公司對差速器殼軸承安裝外圓加工方案進行改進,由磨削加工更改為車削加工,通過數控機床自動控制,裝夾的高精度,保證產品加工的一致性及穩定性,同時提高生產效率,降低操作者勞動強度。
二、產品工藝性分析
1.材料分析
該產品設計材料為 40Cr-GB/T 3077,調質硬度洛氏硬度(23~28);具有良好的綜合力學性能、良好的低溫沖擊韌性和低的缺口敏感性,切削加工性能較好,車削加工亦可得到良好的表面加工質量。但因 40Cr 材質具有優良的韌性,切削余量過小時不易斷屑,需考慮車削時鐵屑是否纏刀或劃傷產品外圓。
2.尺寸公差分析
如圖 2 所示,差速器殼軸承安裝外圓尺寸 Φ80+ 0.039+0.020 mm,公差 0.019 mm,表面粗糙度要求 Ra1.6 μm,尺寸精度和表面質量要求較高,故工藝方案需確定合理的加工余量、切削參數等,從而保證連續加工過程中的產品尺寸及表面質量穩定。
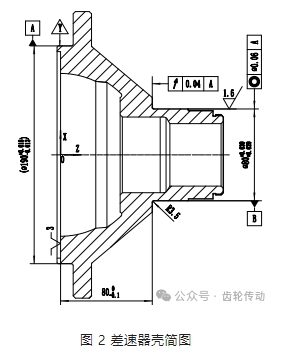
3.形位公差分析
差速器殼屬于回轉體,根據圖樣要求,軸承安裝外圓及端面相對基準 A 同軸度要求 Ф0.06 mm,端面跳動 0.04 mm,如何保證產品形位誤差要求,需綜合考慮設備及裝夾精度,從而制定合理的工藝方案。
三、解決方案
1.設備選型
數控機床具有高的定位精度和重復定位精度,而普通精度的數控機床其定位精度可達 0.01 mm,重復定位精度可達 0.006 mm。為提高資源利用率,綜合考慮已有設備,選擇 OP20 車小端工序數控車床 CK7525 加工,如圖 3 所示設備,將差速器殼磨削工序加工內容合并至 OP20 車小端工序。通過對設備精度進行檢測,其中 X 向反向間隙 0.005 mm,重復定位精度 0.005 mm,定位精度0.01 mm;Z 向反向間隙 0.008 mm,重復定位精度 0.006 mm,定位精度 0.01 mm;滿足加工要求。
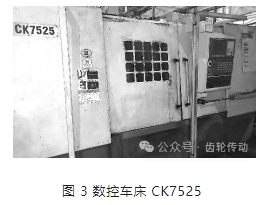
2.夾具選型
為保證加工過程的一致性和穩定性,如圖 4 所示,選用 SMW 公司的后拉式液壓三爪卡盤,重復定位精度可達到 0.005 mm 以內,三爪經過熱處理保證一定的硬度后可減少過程中因磨損造成的精度失準。同時三爪夾持部位設計為鋸齒形,增加設備高速運轉過程中工件與三爪之間的摩擦力,防止工件移動或甩出。
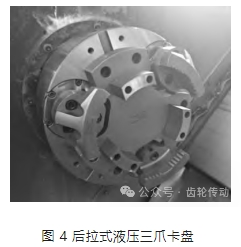
3.刀具選型
刀具選擇不僅影響機床的加工效率,而且直接影響零件的加工質量,根據產品尺寸精度及表面質量要求,要求所選擇刀具必須具備精度高、壽命長且尺寸穩定的特點。通過對不同供方、材質及槽型的刀片進行加工驗證,我公司選擇肯納帶修光刃的金屬陶瓷刀片 CNMG120408FW KT315 加工,如圖 5 所示,該類型具備低速到高速的切削加工,耐磨性好,加工表面質量較高。經現場驗證,切削過程中產品尺寸精度變差±0.002 mm,產品加工表面質量符合工藝要求。該刀片共 4 個刀尖,每刀尖加工產品 270 件,刀片加工壽命 1 080 件/片,單件成本消耗 0.06 元。通過與磨削加工成本對比,磨削砂輪單件成本消耗 0.11 元,采用車削加工后,加工成本較磨削下降 45.5%。
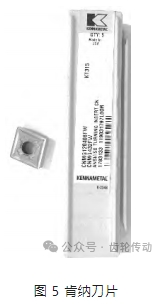
4.切削參數
因所選刀片為修光刃的金屬陶瓷刀片,抗沖擊性能較差,適合小切削余量的加工。故精車外圓單邊余量選擇 0.2~0.3 mm 之間,端面精加工余量 0.1~0.2 mm 之間;為獲得較高的表面粗糙度,采用高轉速低進給的方法來滿足工藝要求。通過對刀具強度和設備性能綜合驗證,如表 1 所示,當主軸轉速為 900 r/min,單邊切深為 0.2 mm、進給量為 F0.1 mm/r 時,產品表面粗糙度可達到 Ra0.388 μm,滿足產品表面質量要求。
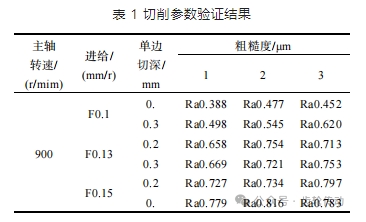
四、效果驗證
(1)同軸度 Ф0.06 mm 及端面跳動 0.04 mm:使用同軸度檢測量具連續抽取 30 件,對差速器殼軸承安裝外圓同軸度端面跳動進行檢測,檢測結果如表 2 所示,同軸度范圍在 Ф0.020~Ф0.040 mm 之間,其中 83%的產品同軸度可達到 Ф0.030 mm 以內;端面跳動檢測值在 0.010~0.020 mm 之間,檢測結果 100%均符合工藝要求。
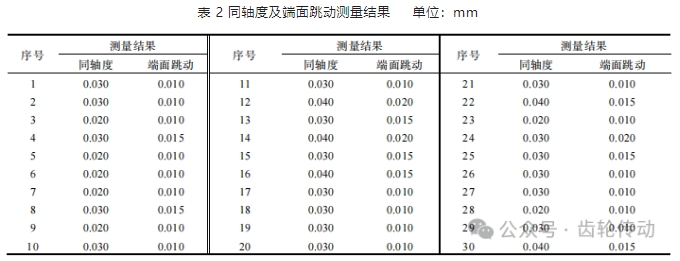
(2)粗糙度 Ra1.6 μm:采用粗糙度測量儀對外圓表面粗糙度進行檢測,檢測結果如表 3 所示,車削后的差速器殼軸承安裝外圓表面粗糙度滿足質量要求。為驗證刀具磨損對表面粗糙度的影響,現場連續對 210 件產品進行數據檢測統計,其中 65%的產品表面粗糙度可達到 Ra0.8 μm以內,35% 的產品表面粗糙度在 Ra0.8~Ra1.6 μm 之間。故車削較磨削可得到優良的加工表面質量。
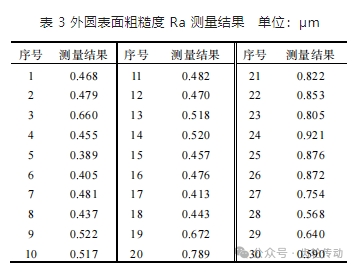
(3)尺寸精度:加工過程中,數控車床按輸入的程序自動完成產品外圓、圓弧及端面的加工,檢測結果如表 4 所示,首件外圓尺寸調整至中差后,連續切削中尺寸變差±0.005 mm,每加工 60 件需對刀補進行精度補償。軸向尺寸經首件調試合格后,過程中變差較小,可在對外圓尺寸精度補償時進行適當調整。外圓根部圓弧通過數控程序控制切削軌跡,圓弧外觀規則,圓滑過渡。故數控加工過程中人為干擾因素減少,使產品質量的一致性明顯提高,質量更加穩定可靠。
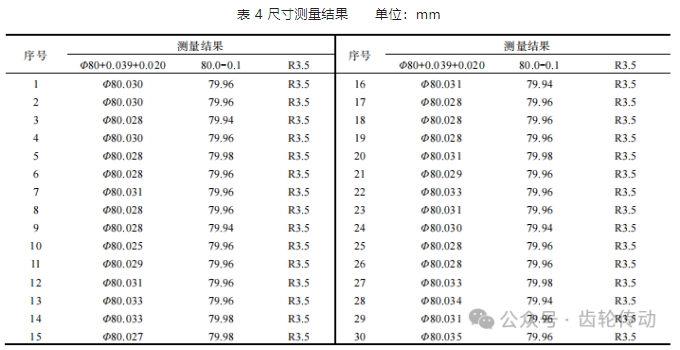
(4)初始過程能力:為了確認過程的穩定性,對外圓尺寸 Φ80+0.039+0.020 mm 連續檢測收集 25 組共 125 個數據,采用均值-極差圖(圖 6、圖 7)對其初始過程能力進行分析研究計算,具體過程如下。
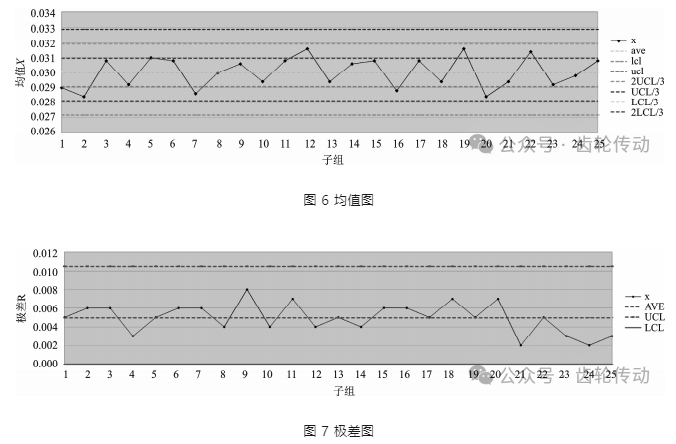
依據式(1)計算標準偏差:

其中,是子組極差的平均值,由圖 7 可知,R =0.005;d2 是隨樣本容量變化的常數。
本文選取 25 組數據,每組樣本容量 5 件,由表 5 可知,d2=2.33,故過程的標準偏差為 δ= R / d2=0.005/2.33=0.002 14。
過程能力按雙向容差計算,過程如下:
單邊上限短期能力指數為

單邊下限短期能力指數為
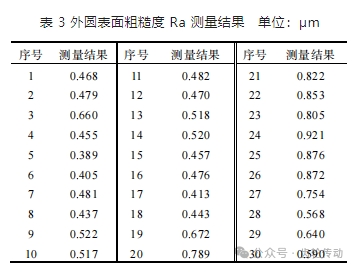
過程能力指數為

式中,USL 為規范上限,即 USL=0.039;LSL 為規范下限,即 LSL=0.020; 為 25 組數據的過程均值,由圖 6 可知,
=0.030。
根據統計過程控制手冊判定標準,當 1.33≤ Cpk≤1.67,說明過程能力正常。本文差速器殼軸承外圓尺寸為 Φ80+0.039+0.020 mm,過程能力指數 Cpk=1.402>1.33,過程指數符合要求。
五、結語
與普通磨床相比,數控車床產品加工質量穩定、效率高,人為干擾少,工藝的兼容性強,經濟效益高。本文差速器殼軸承安裝外圓采用以車代磨工藝方案后,首先不良品數量大幅降低,經統計,因差速器殼軸承外圓、軸向尺寸超差造成不良品數量較 2020 年下降 78%。其次,工序合并后,原磨床崗位配置減少,節省了人員成本;最后,磨床工序取消后,砂輪灰、廢舊砂輪、油泥及廢舊冷卻等環境污染源減少,環保處置費用也得到了節約,為公司創造了經濟效益。
參考文獻略.