伴隨著對噪音、振動和聲振粗糙度(Noise, Vibration and Harshness, NVH)要求的提高,行業內 NVH 開發的研究中指出,項目開發過程中需要持續對 NVH 進行測量和優化,需要大量的周期和資源,如初始的 NVH 基底設計較差,后期優化可能無法規避風險。為了降低系統的 NVH 風險,需要從設計之初便考慮 NVH 的系統設計。
一、概念設計階段
齒輪作為變速器中主要的傳動部件,最重要的就是滿足傳動需求,包括傳動的形式、傳動級數的設計、傳動比要求等。概念設計階段的交付物有:1)一份包含系統框架、方案選型、邊界、性能、強度校核以及風險識別的設計校核報告;2)初版包絡的 3D 數模;3)包含精度等級、工藝要求、清潔度要求等用于初始報價的 2D 圖紙;4)零件的物料清單(Bill Of Material, BOM)以及初始的設計失效模式與影響分析(Design Failure Mode and Effects Analysis, DFMEA)。齒輪階次噪音的“DNA”設計,是從設計之初就規定與傳動系統性能表現相關指標的方法,不僅僅滿足于階次噪音的需求,而且全面充分地考慮從性能到可靠性,從加工到成本,從周期到平臺化等需求。為了同時滿足以上各方面的需求,需要借助一些決策工具,如表 1 所示,采用決策矩陣幫助進行決策。根據需求給對標應用、性能、重量、可靠性、工藝、平臺化、成本、周期等賦予不同的權重,通過比較各個方案的效果,給出評分,由權重×評分的方式,得到各個方案最終的加權總分,以幫助我們對方案進行比較及選擇。為了便于區分和拉大差距,權重可按 2、5、8 設計,權重的取值可根據項目的需求調整,方案評分按方案和方案一(基準均為 5 分)的差異按 1、3、5、7、9 設計。
1)對標應用:評估行業內標桿的、成熟的應用;2)性能:評估傳動系統的階次偏離度、重合度、軸系撓度、嚙合錯位、傳遞誤差、效率等;3)重量:評估整個方案的重量差異,應包含關聯部件的重量;4)可靠性:評估安全系數、軸承損傷率、最大應力等;5)關聯變更:評估更改可能引起其他零件的性能、強度、接口和空間的匹配;6)工藝:評估零件加工生產工藝的可行性和裝配工藝的可行性;7)平臺化:評估當前設計方案的通用性;8)成本:評估方案的總體成本,包括零件自身變化帶來的成本變更,以及關聯變更帶來的成本變更,裝配工藝的成本變更,可能產生的修模費用和報廢費用;9)周期:評估方案的生產制造周期,驗證周期是否能夠滿足項目要求。具體決策矩陣如表 1 所示。
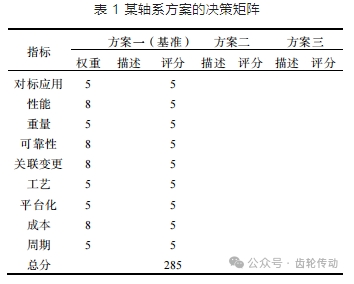
1.齒輪階次噪音的來源
齒輪的階次噪音的產生,主要來源于齒面嚙合時的沖擊。沖擊產生的振動由齒面傳遞至齒體,由齒體傳遞至軸,最終由軸上的軸承傳遞至變速器殼體,引起殼體表面的振動,從而發出我們能夠聽到的齒輪階次噪音。
2.嚙合次數的優化
齒輪每秒鐘嚙合的次數多,其產生的頻率會高,如果次數過多就會引起主觀感受上的“嘯叫聲”或“口哨聲”。優化嚙合次數,可以從降低齒輪轉速及齒數入手。
與電機連接的一級齒輪通常與電機同轉速,轉速高達 16 000 r/min,且有更高速化的發展趨勢。在滿足傳動比需求的前提下,選取齒數時盡量選取較低的齒數,來避免引起更高頻率噪音。同時,還需要避免齒數<17 齒,引起齒輪的根切,導致齒輪強度的下降。
擁有多級傳動的變速器中,下一級傳動的齒數比也尤為重要。除了每級的傳動產生的嚙合階次,還需要注意避開電機的槽、極階次。一階及其倍數階次需要與不同部件的一階及其倍數階次存在階次偏離度(>7%或更高),避免階次相同的振動源在嚙合時產生相同的頻率,引起共振問題。如圖 1 所示,某變速器中與電機直連的 P3 軸齒輪,其齒數為 26 齒,其主階次為 26 階,需要關注其與電機 8 階及其倍階的校核,按當前經驗需要在 5 倍階次內都滿足>7%的偏離要求,超過 5 倍階后,由于能量下降可不再重點關注。
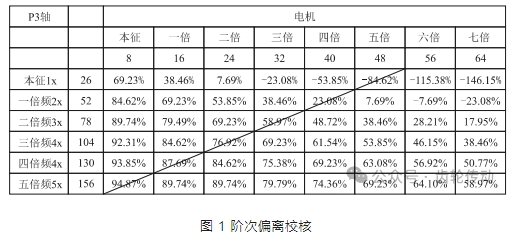
3.嚙合沖擊能量的降低
除了通過優化嚙合次數來降低過高的嚙合頻率外,還需要降低嚙合時沖擊的能量,以此來降低振動的幅值。齒輪副嚙合時,主動齒推動被動齒,可看作對主動齒的減速,以及對被動齒的加速。零側隙工作時,齒面保持常嚙合狀態,不會產生額外沖擊能量。但實際應用時,需要預留潤滑油進入的間隙,包容零件加工誤差和裝配誤差,設計時需要保留一定的工作側隙。文獻基于接觸動力學相關理論建立齒輪嚙合接觸沖擊模型。因此,在非嚙合接觸時,主動齒面進行加速,沖擊的能量可近似理解為

式中,m 為工作齒的質量;v 為主動齒接觸時的相對被動齒的速度。

當扭矩一定時,齒的加速度 a 為一定值,故其沖擊大小 E 與加速的時間 Δt 有關。因此想要降低沖擊時的能量,可以通過縮小齒側間隙來縮小加速時間 Δt,還可以通過降低從動齒輪的回轉慣量,降低相對速度 v 值。
上文已經提到,通過保證齒面常嚙合也可以保證振動能量的下降,因此,引入了齒輪的另一設計指標——重合度。重合度的概念在齒輪設計行業內已經廣泛普及,在本文中不再贅述。重合度的增加可以降低沖擊,但設計時,不僅需要關注法向重合度 εα 和軸向重合度 εβ 的分配關系,如文獻所示。需要注意過分追求高法向重合度 εα 時,齒頂部寬度過小,熱處理后硬脆崩落的風險。
4.優良的支撐定位結構
由上文可知,振動沖擊的幅值,來源于沖擊。齒輪副的不對中情況,包含了沿軸向的、徑向的及夾角,實際上也是改變了嚙合齒輪副的間隙以及重合度,即引入了沖擊的能量的波動,使得運轉趨于不平穩,增大了階次噪音的表現。
齒輪的軸向定位,需要選用縮小竄動量的方案,來避免沿軸向的齒側間隙波動。同時,需要留有足夠的嚙合余量來保證齒輪竄動及安裝后的重合度,通常保證單側≥1.5 mm。后續在詳細設計階段時,還需要通過尺寸鏈校核這一嚙合余量是否滿足。
齒輪的徑向定位,需要盡量選用同軸度最高的方案,來保證沿法向的齒側間隙和重合度的波動,即確保齒輪嚙合時的中心距。
除此以外,還需要選定支撐剛度高的結構,優化軸承匹配,通過降低支撐軸的變形,縮小軸齒輪副之間的嚙合夾角。如選用懸臂結構時,盡量縮短懸臂長度,來優化對齒輪的支撐剛度。選用高強度的材料,并設定與之相符的熱處理要求。
5.高精度的加工工藝
齒輪加工時,通常采用滾/剃齒-熱處理-磨齒/珩齒,齒的形狀是連續加工的。由于既不是一次成型的,也不是同時完成整周的加工,導致了每個齒自身形狀的誤差,齒與齒之間的形狀誤差,以及圓周上的齒側間隙會存在誤差,即單齒距偏差和齒距偏差累計。這些誤差,會影響齒側間隙,最終引起沖擊能量的波動。內齒圈雖然可通過拉齒一次性加工出全部齒的形狀,但是也需要進行熱處理,且由于熱后加工難度大,熱處理后基本不再進行加工,所以常常采用氮化這種熱處理變形小的方式,也會存在誤差的問題。
隨著電機高速化的發展,輸入齒輪副的精度要求會越來越高,甚至粗糙度導致的齒側間隙波動也會導致明顯的感知差異。所以,當設計時,需要考慮零件加工的工藝性,提高裝夾定位精度,規整零件的形狀來降低熱處理變形,在利于加工的同時,也利于降低加工誤差。
6.概念設計總結
在概念設計階段,往往由于齒輪的“DNA” 設計的不好,詳細設計階段很多宏觀的優化無法按部就班的進行,或者優化的效果十分有限。故除了確保基本的強度以外,以上的內容也需要考慮。
二、詳細設計階段
詳細設計階段,除了對概念設計進行補充完善,提供接口單,完善 3D 數模和 2D 圖紙,梳理關鍵特性清單和試驗大綱,還需要建立一個系統級的模型,對整個傳動系統進行仿真,而不是僅僅針對齒輪自身。借助如 MASTA 或 ROMAX這樣的仿真軟件建立出一個相對準確的模型,有助于后續對 NVH 設計指標的確認,需要搭建詳細的軸系的結構、齒和軸的連接狀態,軸承的安裝配合、限位、預緊,對異形的結構如差速器殼體還需要進行有限元剛度導入,最后還需要導入變速器殼體的剛度矩陣并與軸承連接。
1.階次噪音的宏觀優化
宏觀上,需要確認齒輪的嚙合錯位量,表現為一對嚙合齒輪副,實際嚙合位置和理想嚙合位置的偏差,此值越低表示兩個齒輪的嚙合狀況更良好。針對嚙合錯位量,首先需要關注的是齒輪自身輪緣和腹板,輪緣厚度或腹板厚度過薄時,在齒輪力作用下會產生較大的變形,增大錯位量。其次,需要關注軸的撓度,齒輪布置位置遠離在軸上支撐點,采用較長的懸臂結構也會增大軸系變形,從而加大錯位量。最后,需要關注軸承的游隙,以及軸承的限位,錐軸承在未給定軸向預緊時,其軸系撓度會有較大的下降。
宏觀的優化不能完全消除錯位量帶來的影響,變形只會減小不會完全消失,還需要通過微觀層面進一步優化。
2.階次噪音的微觀優化
微觀層面,需要確認齒輪的傳遞誤差以及接觸斑點仿真。通過部件的剛度導入,使軸承座的支撐剛度接近實物,可以提升仿真精度。我們可以通過齒輪修形優化齒輪的接觸,如增加法向、軸向的鼓形,壓力角或螺旋角方向的微調修形。修形參數設定時,需要確認規定的左右齒面、實際接觸的齒面、圖紙規定的齒面、加工和檢測的齒面,五者相同,避免設計落地時出現偏差。
通過設定多種梯度相同的正向扭矩工況模擬車輛前進,設定負扭矩的工況模擬拖曳、能量回收和倒車,可以得到如表 2 所示的不同工況下的傳遞誤差峰峰值(Peak to Peak Transmission Error, PPTE),及如圖 2 和圖 3 所示的接觸斑點。
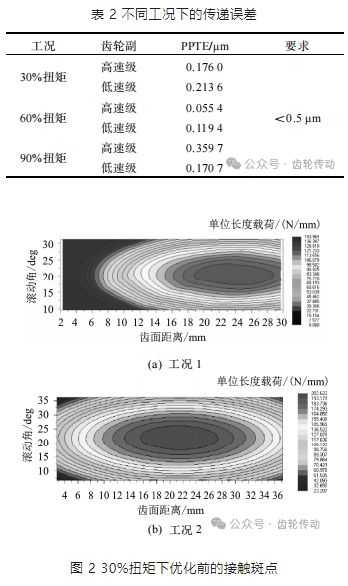
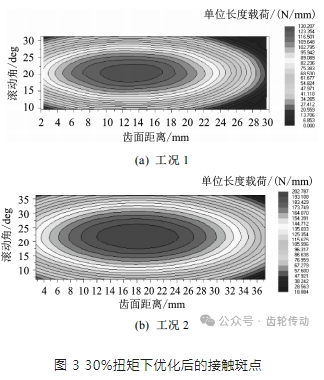
借助試驗設計(Design Of Experiment, DOE)的方法,以齒輪修形參數為因子,以公差偏差及中值為水平,以傳遞誤差為響應值,進行修形參數的全因子設計如表 3 所示,并通過效應分析,可以得到每種修形在不同工況下的效應圖,如圖 4 和圖 5 所示。可以看出圖 4 中,高速級對修形參數的變化比較敏感,圖 5 中低速級對修形參數的變化相對不敏感。通過這種方法,可以確認設計值的中值以及公差帶范圍,并且針對將來可能出現不同扭矩下的階次噪音問題,已經獲得了零件的修形傾向,極大地增強了設計的魯棒性。
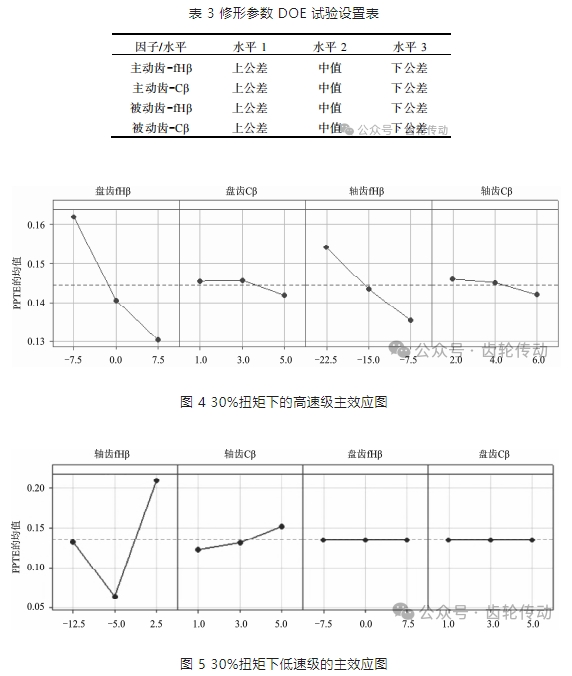
對已經獲得的修形參數及范圍,需要與加工確認是否可實現。如精度過高,無法滿足時,需要重新確認整體設計的魯棒性,檢查對微觀修形影響較大的宏觀設計。
三、設計驗證
通過制樣及樣機建造,進行相關的測試,如耐久測試、階次噪音測試、齒輪嚙合斑點試驗,對設計進行確認,并幫助我們修正模型,提高仿真精度。
通過耐久試驗后,使用齒輪測量機對齒輪進行檢測,觀察齒形齒向上的嚙合情況,測量結果如圖 6 所示。可看出未出現由于偏載帶來的嚙合凹陷,齒面接觸狀態良好,齒面狀態與新件接近。
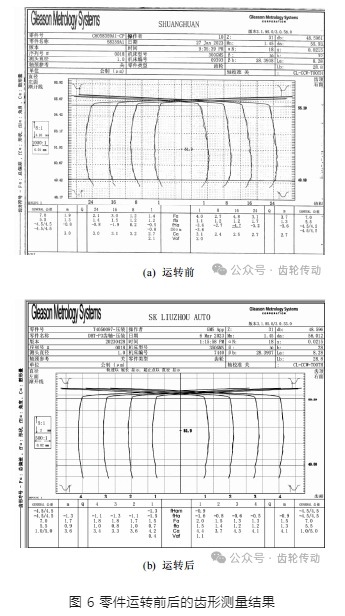
通過階次噪音測試,獲得測試的瀑布圖如圖 7 所示,切片信息如圖 8 所示。臺架及整車上均未發現明顯的齒輪階次線,且階次的切片低于總聲壓級 30 dB 值左右,表現良好。
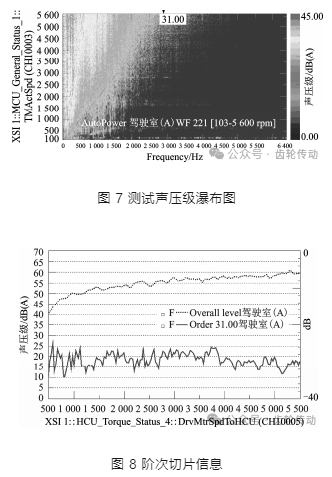
對已有的齒輪,按仿真的載荷開展嚙合斑點試驗,并與仿真的接觸形狀比對,所獲得的斑點如圖 9 所示。未觀察到有偏載現象,與仿真結果基本一致。
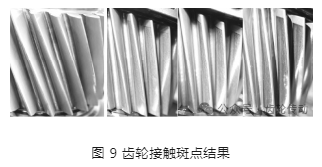
四、總結
采用“DNA”設計的理念,在概念設計階段確認了輸入及邊界,明確了設計需求及性能指標需求,后續通過詳細設計進行細化優化,運用 DOE 分析提升魯棒性,并在首次建造時便能通過試驗測試。說明此方法開發的產品,可靠性良好,成功率高,且能夠縮短產品開發的周期,降低開發的成本。
參考文獻略.