純電驅動的新能源車輛具有零排放、低噪聲等優點,沒有了發動機的背景噪聲,使其對整體的噪聲質量要求更高,減速器作為電驅動車輛的重要組成部分,需要具備低噪聲、高效率、壽命長等特性,減速器的關鍵結構傳動齒輪應具備足夠的強度和平順的嚙合傳動性能,以保證足夠的壽命、較低的噪聲。齒輪在傳動過程中嚙合產生的振幅和波動為主要的振動噪聲源,在齒輪的設計中可以通過齒輪宏觀參數的選擇和微觀參數的修形,減少齒輪嚙合沖擊提高嚙合性改善嚙合應力分布,延長齒輪的工作壽命,提升齒輪傳遞效率,降低工作噪聲。
目前,齒輪設計一般采用經驗法設計,這具有較大不足:1)需要設計人員擁有大量的經驗積累,并且其知識的傳承性較差,使得專業設計人才匱乏;2)在方案的設計過程中涉及的計算量較大,容易出現偏差,設計后的試驗成本也較高。隨著有限元設計仿真軟件的不斷完善,軟件對齒輪的設計方案進行仿真計算,得出齒輪齒根彎曲疲勞強度、修形齒面載荷分布的接觸斑點、齒輪膠合安全系數、齒輪傳動誤差幅值、齒輪嚙合錯位量等客觀評價指標,通過計算出的指標參數,設計人員可選擇最優的齒輪參數進行加工,從而減少了設計成本。
一、齒輪模型建立
采用 Romax 軟件建立齒輪裝配模型,本文以一對傳動齒輪為例進行參數優化設計,建模時采用詳細齒輪設計模塊,通過軟件中詳細齒輪設計模塊可分析齒輪的微觀幾何和制造公差對齒輪強度及振動方面的影響。具體齒輪參數見表 1,建立三維模型見圖 1。
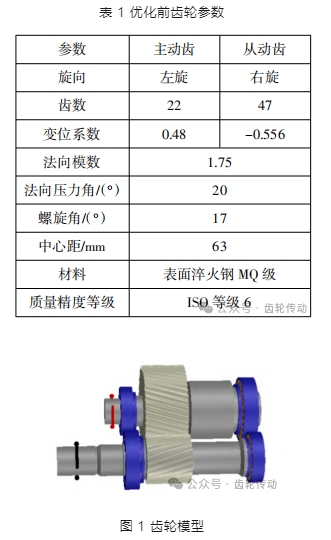
齒輪材料選擇 ISO6336 標準中推薦的 MQ 級熱處理低碳鋼,其參數見表 2。
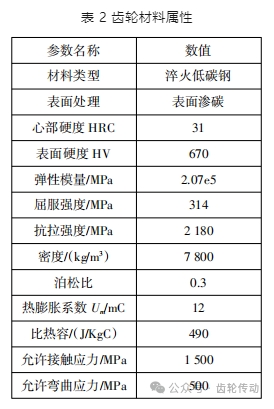
為了使軸承耐滾動疲勞的能力最大,以避免因軸承失效影響齒輪分析的結果,從 Romax 軟件的軸承數據庫中選擇同尺寸規格中動載荷較大的軸承裝配到傳動軸上。軸承類型為圓錐滾子軸承,安裝時參考實際安裝情況在一端設計軸承安裝預緊量 0.05 mm,如圖 2 所示。
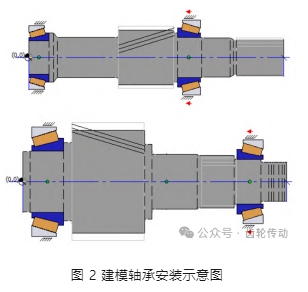
采用材料的 S-N(應力—壽命)曲線假定法將實際運行工況的疲勞總時間縮聚為一個高轉矩低循環次數的循環工況,形成的循環工況滿足與原始數據同樣的零件損傷度和損傷模式,通過產生同樣的零件損傷度值將原始工作數據等效轉換為單載荷循環的計算用載荷譜,形成的工作載荷譜如表 3 所示。
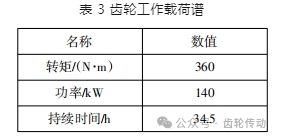
通過 Romax 軟件仿真計算,得出齒輪強度指標如表 4 所示。
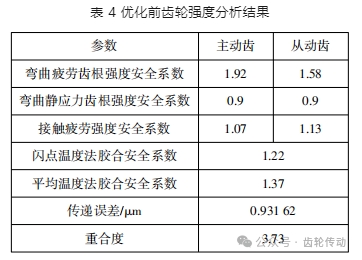
對初始模型進行仿真,主要校核齒輪的強度及傳遞誤差,傳遞誤差線性圖見圖 3,圖 3 中表示的是嚙合線上的位移,最大位移值與最小位移值的差值就是齒輪運行時的傳遞誤差。根據這些參數初步判斷此套齒輪在強度及平順性上的優劣。
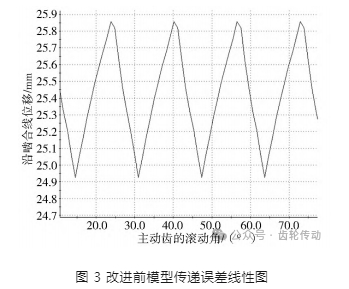
根據軟件仿真計算的結果可知此套齒輪強度部分安全系數值小于推薦指標,存在一定概率的失效風險,須進一步優化;傳遞誤差值相對并不高,可在下一步優化中繼續探究是否有優化的空間。
二、齒輪參數優化設計
宏觀參數優化
通過 Romax 軟件中的全因子試驗設計研究模塊,其模塊的原理為對所有設置為變量的因子進行排列組合,并對所有組合都進行 1 次試驗方案測算;分析時定義的步數是指每個變量在其限定范圍內的取樣個數,相鄰的每兩個值之間增量相等。全因子法本身并不會執行最優化分析,但可以通過設置期望目標鎖定最佳方案的范圍。以壓力角為變量,以彎曲和接觸安全系數以及傳遞誤差為目標,計算結果如圖 4 所示;繼續逐步將模數、螺旋角設置為變量計算形成最終齒輪參數方案,見表 5。
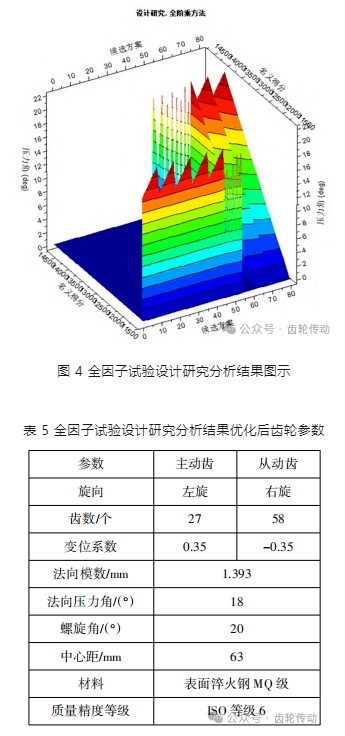
參數的改進方向主要為增加齒數,降低壓力角,提高重合度,增加嚙合線的長度,使齒輪嚙合應力分布更加均勻,運行更加平順,提高整體的接觸強度和減小傳遞誤差,優化后齒輪分析指標結果見表 6,傳遞誤差線性圖見圖 5,傳遞誤差優化較為明顯,提升幅值達 42.3%。
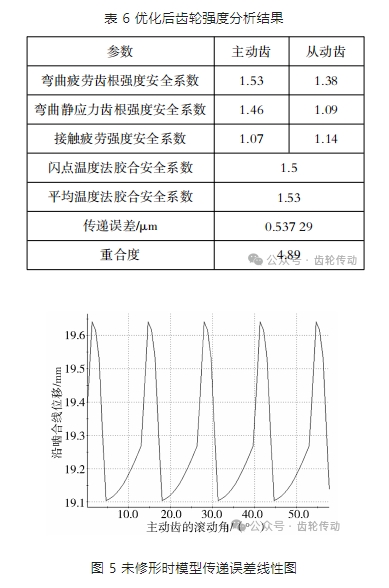
微觀參數設計
齒輪的微觀參數設計一般指齒輪的修形,主要涉及齒向鼓形量、齒向傾斜量、漸開線鼓形量和漸開線傾斜量。齒輪修形可進一步降低齒輪的傳遞誤差,由圖 6 齒面應力載荷分布的接觸斑可看出,齒面上載荷最大值為 224.1 N/mm,齒輪嚙合工作中載荷應力偏移至齒邊緣,這樣的載荷分布易使齒輪產生偏磨,齒輪齒頂與邊緣較其他部位更為脆弱,存在邊緣斷裂或剝落的可能,從而容易降低齒輪壽命,同時也會使齒輪嚙合過程中噪聲和振動增大。需通過修形改善齒輪接觸時的載荷分布,以達到降低由偏磨產生的潛在隱患。
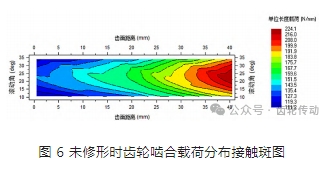
齒向鼓形量:鼓形量一般通過經驗值設定或經驗公式計算:
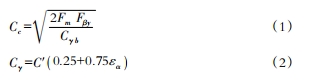
式中:b 為工作齒寬,mm;Fm 為齒輪傳遞的圓周力,N;Fβy 為嚙合錯位量,μm;C'為配對齒輪的共軛剛度,GPa;Cγ 為輪齒綜合剛度,GPa;εα 為重合度;Cc 為齒向鼓形量。計算可得,齒向鼓形量為 8.31 μm。
在軟件中可模擬齒輪嚙合過程,獲得一個嚙合周期中由嚙合接觸線重合度變化形成的動態嚙合剛度,如圖 7 所示,可從中獲得齒輪綜合剛度 Cγ 為 60.7 GPa。

漸開線鼓形量: 根據 ISO6336 的經驗公式:

式中:KA 為使用系數,取值為 1.25;Ft為齒輪分度圓上作用的端面切向力,N。計算可得,漸開線鼓形量 Δmax 為 1.76μm。
傾斜量:齒向傾斜量主要是彌補齒輪間的錯位量,其值一般按經驗選取,等于錯位量的大小。
漸開線傾斜量一般用于針對制造過程中出現的輪齒扭曲等復雜現象時,進行三維修形時參與的設計參數,設計中一般設置為 0。
經過經驗公式的初步估算,確定微觀參數的設置值及研究公差范圍后,通過 Romax 軟件的全因子試驗設計研究模塊中的算法可獲得一組修形量,如表 7 所示,修形后傳遞誤差降低至 0.218 83 μm,線性圖見圖 8,降幅達 59.2%,且接觸斑點應力集中在齒面中部,見圖 9,但其齒輪載荷最大值為 244 N/mm,考慮其對齒輪強度的影響,再次計算齒輪強度系數,結果見表 8。從強度上看,雖然修形后局部載荷增加,但齒面上載荷分局均勻、承力面增加使得齒輪總體的安全系數均有提升。
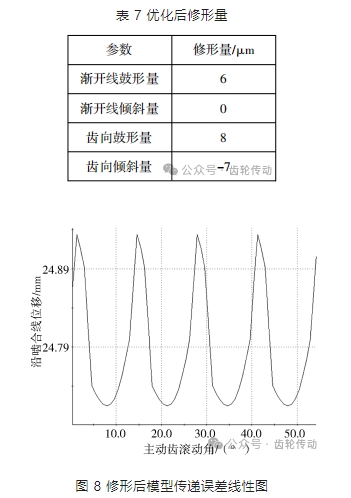
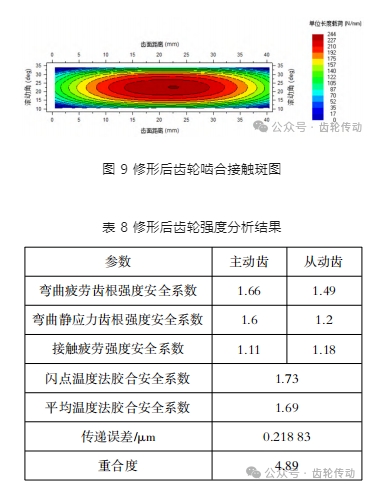
三、結果分析
采用上述兩個方案的減速器搭載到驅動橋上,實測噪聲結果如圖 10 所示。可看出通過優化噪聲階次有明顯轉移,出現最大噪聲峰值的階次有所減少,整體上優化后方案在噪聲方面起到了明顯的優化作用。
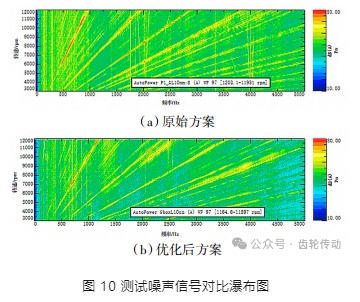
通過試驗及計算分析總結如下:
(1)通過齒輪宏觀參數可大幅度地調整齒輪強度安全系數及重合度的指標,在安全系數的選擇上以滿足最低要求且留有適當安全余量為佳;重合度越大代表了傳遞穩定性越好,在設計時優選考慮重合度高的,其不僅能提升強度,而且在噪聲和傳動誤差方面具有較大的貢獻度。
(2)通過齒輪微觀參數的調整可有效降低傳遞誤差,從理論上使齒輪運行的穩定性獲得一定程度的提升,有利于降低齒輪傳動系統的振動,并同步降低因振動產生的階次噪聲,從圖 10 的試驗測試結果可看出噪聲階次的變化及最大 dB 值范圍的減少。
(3)齒輪宏觀參數及微觀參數均能降低齒輪傳遞誤差,其中,從微觀方面的優化作用效果提升度要大于宏觀參數方面的優化,且微觀參數的調整在整體上變動較小,使得加工工藝易于實現,是一種很好的降低噪聲的改善手段。
(4)齒輪微觀參數修形中增加了鼓形量,使齒輪呈一定凸起的弧面實現將齒輪嚙合時的載荷應力集中在齒面中心,從接觸斑的應力圖可看出,增加鼓形量后,齒面最大的單位長度載荷量也會同步增加。因此,在齒輪修形時,選擇修形量應適量,不宜過大。
(5)通過優化過程中各階段的強度分析結果可看到,膠合安全系數也隨著齒輪重合度增加而增強,說明增加齒面的有效接觸對齒輪接觸溫度也會有所改善。
四、結論
本文通過 Romax 的仿真計算對齒輪實現了方案優化,實現彎曲靜應力齒根強度安全系數提升 33%,接觸疲勞強度安全系數提升 37%,閃點溫度法膠合安全系數提升 41.8%,平均溫度法膠合安全系數 23%,傳遞誤差減少 76%,重合度提高 31%,其中,彎曲疲勞齒根強度安全系數有所下降,但均滿足最低安全系數指標且留有余量。綜上,實現了齒輪傳動系統的優化,與齒輪設計的傳統工程設計經驗法相比,通過 Romax 軟件提供的仿真算法可設計出一套綜合性能較高的齒輪傳動系統,為齒輪的復雜設計過程提供了一種簡便的有數據依據的設計方法。簡化設計不僅能縮短設計周期,節約直接可見的資源,還能間接減少企業開發項目的管理及試驗驗證成本。
參考文獻略.