風能作為分布范圍最廣、發展最迅速的可再生清潔能源之一,在世界范圍內已經大規模應用。在“雙碳”目標背景下,國內風電行業迎來巨大規模的發展。風電齒輪箱作為風力發電機的重要組成部分之一,其功率密度一直是制約著大兆瓦級風機發展的卡脖子技術。某商用風機功率從 2 MW 增加到 5 MW,齒輪箱質量增加約 170 %。如何在增大齒輪箱功率的同時,保證最優化的齒輪箱結構與質量,是目前雙饋與半直驅風機的一個難題。此外,受風速影響,齒輪箱長期遭受齒輪與軸承的時變載荷沖擊,復雜的承載環境使得箱體需要具備足夠的強度與剛度,以防止傳動過程受載過大導致箱體產生變形、開裂。以往箱體設計大都以經驗為主導,多工況復雜條件下,箱體強度與質量分配難以均衡,存在局部強度不足以及材料冗余等情況。針對上述問題,輕量化設計在各個領域已經取得了很好的應用;因此,對風電齒輪箱箱體進行多工況輕量化設計,不僅關乎風機的成本,更與風機性能提升密切相關。
機械設備往往服役工況復雜,為避免單工況優化的局限性,導致某一工況下的優化性能不佳,孟亮等人以 2 種極限工況下航空發動機支架柔順度為目標,采用增材制造材料橫觀各向同性模型對支架進行優化設計,使支架質量減少了 15 %。邢廣鵬等人以多工況下總柔度為目標函數,以體積為約束函數對某發動機支架進行基于變密度法拓撲優化設計。趙瑞杰等人針對潛望式激光通信裝置,對發射和在軌 2 種工況下的固有頻率進行了優化設計,實現了結構性能的提升。韓明軒等人考慮碰撞載荷作用下的多工況田間,對混動客車車架進行了輕量化設計,優化后車架減重 5.02 %。為保證優化模型準確性,LIANG 等人通過振動響應試驗驗證箱體有限元模型的準確性,并以動態激勵為載荷邊界對箱體進行了輕量化設計。彭顯昌等人通過模態試驗驗證了變速箱有限元模型的準確性,根據靜動態多目標拓撲優化結果對箱體進行結構改進,最終提升了箱體的抗振性能。對于風電齒輪箱優化設計,毛范海等人基于多位置工況,利用拓撲優化和尺寸優化方法得到箱體前機體最優尺寸。雷林等人以質量、應力及變形量最小為多優化目標,基于響應曲面法對行星架進行拓撲優化,提升了行星架的綜合性能。陶立壯等人綜合考慮各級行星輪、太陽輪、齒圈以及傳動軸體積,基于遺傳算法分析了增速比、行星輪數目及排布方式對風電齒輪箱總體的影響,最終得出箱體最小體積設計方案。
綜上所述,目前風電齒輪箱的優化設計大都只考慮了單一額定工況,對于多種極限載荷共同作用下的箱體輕量化研究較少;因此本文以極端服役多工況下箱體最大應力作為風電齒輪箱體輕量化設計的多約束條件,將輪轂處極限載荷等效計算到齒輪箱各軸承處,同時對模型(有限元模型)進行合理簡化和邊界條件等效處理;通過模態試驗驗證有限元模型準確性的基礎上,對箱體進行了多工況輕量化設計與分析結果對比,優化后的箱體可以保證在不降低箱體性能的基礎上減少制造成本。
一、箱體精細化模型建立與有限元分析
箱體精細化模型
以功率為 3.3 MW 的半直驅型風電齒輪箱為研究對象,在 Ansys Workbench 軟件中完成箱體精細化模型構建,箱體主要由驅動殼、扭力臂、主殼體、過渡板和后殼體等組成。為提高計算效率的同時便于網格劃分,對模型通孔、螺栓孔、部分小倒角、凸臺和內齒圈等非關鍵部位進行簡化處理,對齒輪箱主要承載部位和參與優化的扭力臂、驅動殼和過渡板的網格進行精細處理,最終共得到 395 366 個四面體單元,806 016個節點。箱體材料為 QT400,彈性模量 E= 169 GPa,泊松比 μ = 0.275,密度 ρ =7.1×103 kg/m3 ,屈服強度為 230 MPa。
圖 1 所示為箱體三維模型及網格劃分。箱體支撐方式采用三點支撐,分別為主軸軸承前支撐以及扭力臂雙耳孔(見圖 1 的①②)處后支撐。為了考慮輪轂處彎矩對箱體的作用,將主軸等效連接到箱體上,主軸軸承支撐處采用遠端位移約束,約束除主軸轉動方向的其余 5 個自由度。扭力臂雙耳孔處支撐采用 3 個方向彈簧單元等效耳孔內壁襯套的彈性支承。此外,主軸與驅動殼之間由連接件鎖緊盤連接,鎖緊盤的壓力直接影響到傳動系統傳遞扭矩和運轉的穩定性,因此在主軸與驅動殼連接處采用初始壓力等效鎖緊盤的實際作用。驅動殼與箱體之間為軸承連接,采用 4 個方向彈簧單元等效,同時還考慮重力對箱體作用。
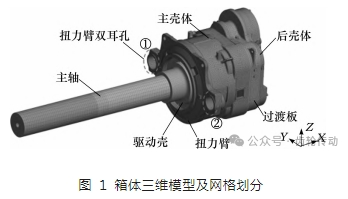
模型有限元仿真
風電齒輪箱實際服役工況包含外部環境激勵與內部載荷激勵,由德國勞埃德(GL)規范可知,齒輪箱的設計需要滿足極端條件下載荷情況,極端載荷情況通常由極限載荷譜描述。風機極限載荷譜是指在規定的設計壽命期間,風機在不同工況下(例如不同風速、風向和溫度等)所承受的最大載荷值,包括靜載荷和動載荷等。載荷譜由設計壽命期間實際工作條件和規定的設計安全系數,按照一定的方法和原則得出,是風機設計優化的重要條件之一。
表 1 所示為風場實時采集的風機輪轂處極限載荷譜,該載荷坐標系為輪轂處固定坐標系,風機輪轂坐標系如圖 2 所示。表 1 中列出了坐標系中各個方向的力與扭矩的極限值,FX 、FY 、FZ 、MX 、MY 和 MZ 分別為 X、Y 和 Z 方向的力和扭矩;共 12 種工況,每 2 種工況覆蓋了某個方向負載的全部范圍,劃線數據為該方向載荷的最大、最小極限值。由圖 2 的輪轂坐標系可知,箱體所受載荷主要為繞 X 方向(主軸方向)的扭矩與 X 方向的力,因此需要重點關注 X 方向工況。
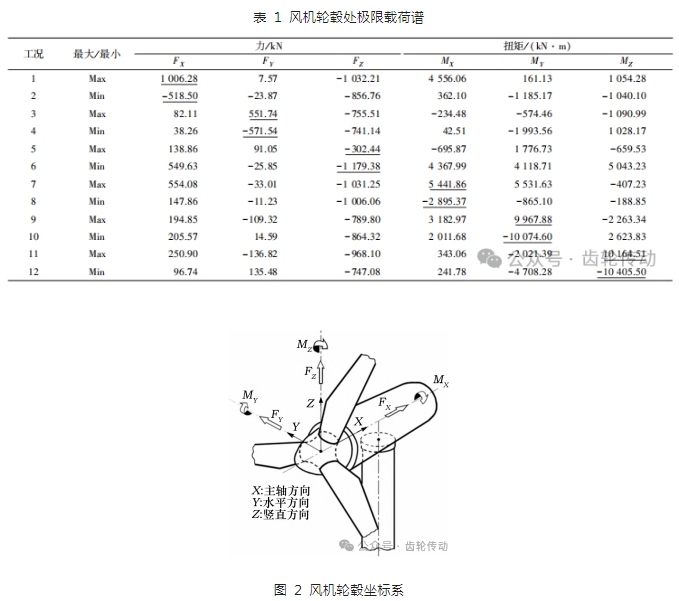
由于極端載荷工況作用于風機輪轂處,箱體內部實際受載部位為各個軸承孔;因此采用文獻中方法對箱體內部載荷進行等效計算。對傳動系統各級齒輪載荷進行計算,并由空間力系平衡方程求得部分工況下箱體內 8 個軸承位置處的載荷(力),如表 2 所示。表 2 中,軸向為 X 方向;徑向為Y、Z合力方向。
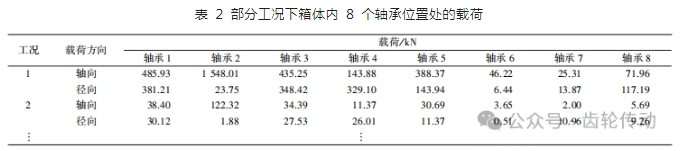
在 Ansys Workbench 軟件中對箱體進行 12 種極端載荷工況下的有限元分析。依據 GL 規范,采用等效應力、位移作為評估箱體強度與剛度的性能指標,許用應力安全系數須大于 1.1。對優化前箱體強度與剛度影響最大的 2 種工況(工況 1:主軸軸向作用力最大;工況 7:主軸扭矩最大;見表 1)下的有限元仿真結果進行分析,優化前箱體位移與應力云圖如圖 3 所示。圖 3 中左側為箱體總體位移結果,右側為等效應力結果。
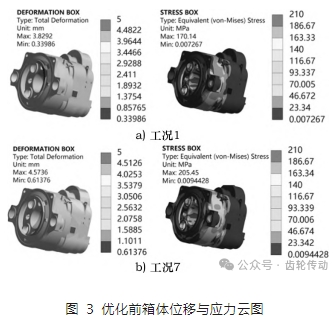
由圖 3 可知,極端載荷工況作用下,箱體整體位移與應力分布不均勻,應力變化主要集中在主殼體,移變化主要集中在扭力臂和后殼體。該結果表明箱體可以進一步優化,使得箱體整體受力均勻,避免應力集中,從而避免箱體發生局部過大變形或破壞。根據有限元仿真結果,選取工況 1 和工況 7 作為箱體后續優化邊界條件。
二、扭力臂模態試驗
為進一步驗證有限元仿真模型(即有限元模型)與實體模型的一致性,確保簡化后模型能夠真實反映實體模型,對有限元模型進行自由模態分析,并將有限元模態分析結果與試驗結果進行對比,以此評估有限元模型的準確性。扭力臂作為箱體關鍵組件之一,即是齒輪箱與驅動殼的連接部位,又是箱體承載的支撐部位,起著承受和傳遞主軸扭矩、支撐和固定齒輪箱等多種作用。故選用扭力臂作為試驗對象,并對其模態進行分析對比。
試驗方案
試驗前采用有限元模態預試驗分析,得到箱體扭力臂前 10 階模態頻率、阻尼和振型,并根據有限元結果初步對試驗測點、激勵方向以及頻率范圍進行判定,從而提高試驗精度與效率。試驗儀器主要由沖擊力錘、LMS多通道采集前端、三向加速度傳感器和工作站組成。
由于測試物(扭力臂)為大型結構,故采用安裝方便、移動性強的多參考點錘擊法進行測試,為達到試驗自由邊界要求的 20 %,試驗分別采用四點軟支撐、兩點彈性繩懸掛支撐及兩點軟支撐這 3 種支撐方式做對比,根據結果選取滿足要求的支撐方式。同時為確保激勵充分,選用測量范圍為 60 kN 的 ICP 型沖擊力錘,分別對 3 種支撐方式下的扭力臂采用尼龍與橡膠這 2 種不同硬度的錘頭進行對比試驗,根據結果選取滿足要求的激勵方式。每組試驗結果取 5 次平均值,模態試驗分析流程如圖 4 所示。
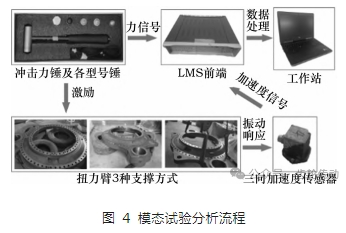
試驗結果
基于本文第 2.1 節的試驗方案,共進行 6 組試驗。提取試驗結果,即提取與有限元模態分析對應的扭力臂前 10 階模態的試驗結果,并對每組試驗進行支承剛度驗證。扭力臂前 4 階彈性模態與最高階剛體模態頻率如表 3 所示。
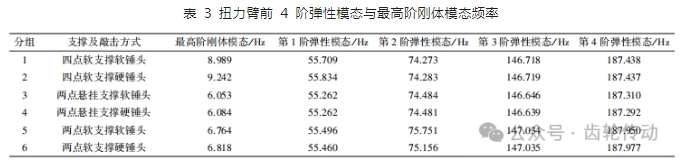
由表 3 可知,6 組試驗均滿足最高階剛體模態頻率小于第 1 階彈性模態頻率 20 %的要求,表明測試支撐剛度在合理范圍內。
為避免試驗結果提取到不屬于結構本身的干擾模態,通過模態置信準則(Model Assurance Criterion,MAC)對試驗數據的準確性與可靠性進行評估。MAC 是評估模態振型相關性的重要判據,模態 A 和模態 B 的置信準則 MAC(A,B)的表達式見式(1)。

式中:ФA 、ФB 分別為模態 A 和模態 B 的振型向量。
MAC 計算得到的標量值位于 0 ~ 1 之間,或者采用百分數表示。MAC 值越小,表明這 2 個振型向量之間相關性越小;MAC 值越大,表明振型向量彼此平行或相似度越高,識別的結果越準確。理想的模態分析結果中,振型相關矩陣除了主對角元素,其他元素值都非常小,表明各階模態振型相互獨立。
對比 6 組試驗可知,第 3 組試驗最高階剛體模態頻率與第 1 階彈性模態頻率比值最小,邊界支撐效果最佳,因此選取第 3 組試驗結果進一步分析。試驗模態 MAC 矩陣如圖 5 所示。圖 5 給出了第 3 組試驗的前 4 階彈性模態 MAC 矩陣結果,對應有限元自由模態分析的第 1 ~ 第 4 階彈性模態。圖 5 中主對角線元素為前 4 階彈性模態自身的點積,接近于 1,非對角元素接近于 0,表明各階模態振型彼此相互獨立,模態參考點位置與數量選擇均合理,試驗結果并無虛假模態。第 3 組模態試驗與有限元仿真結果對比如表 4 所示。
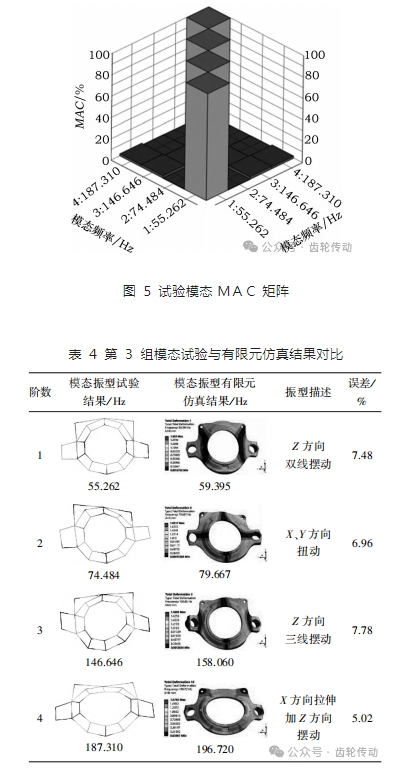
由表 4 可知,試驗測得固有頻率與仿真結果的固有頻率相對誤差均小于 10 %,有限元模態頻率相較于試驗頻率偏大,這是由于有限元模型對扭力臂螺紋孔的簡化增大了結構計算剛度,從而使得有限元計算結果較大,但整體誤差在允許范圍內,并且試驗與有限元仿真模態振型完全一致,驗證了有限元模型和仿真結果的準確性。
三、多工況拓撲優化
基于變密度法的多工況拓撲優化數學模型
拓撲優化旨在找到結構材料的最優分布,將困難拓撲問題轉化為簡單材料分配問題。目前對于結構拓撲優化,已形成比較成熟的方法有:均勻法、變密度法和漸進結構優化法等。本文基于變密度法對齒 輪箱箱體進行拓撲優化。變密度法假設優化部位材 料為各向同性材料,人為引入一種假想單元密度變化范圍在 0~1 之間插值的可變材料,單元相對密度采用 SIMP插值模型進行懲罰,當密度為 0 時表示單元材料被刪除,當密度為 1 時表示單元材料保留。
本文基于變密度法與 SIMP 插值模型,最終得到以箱體質量最小為目標的多種極端工況拓撲優化數學模型,即:
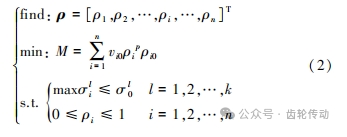
式中:ρ 為密度向量;ρi 為第 i 個單元的相對密度;p 為插值模型引入的懲罰因子,一般取 p = 3;M 為優化后箱體總質量;vi0為第 i 個單元充滿材料的體積;ρi0為第 i 個單元的初始密度;σli 為第 l 個極限工況下箱體優 化后單元的應力;σl0 為第 l 個極限工況下箱體初始結構的最大等效應力,即約束的最大上限值;k 為工況個數;n 為有限元單元的個數。
箱體優化流程與結果
由 Ansys Workbench 軟件對箱體進行優化,拓撲優化分析流程如圖 6 所示。

拓撲優化過程中,首先需要確定優化區域與非優化區域,考慮箱體裝配、安裝要求,箱體加載、連接、約束、吊裝及支撐部位不參與優化,為保證足夠的拓撲優化區域,不考慮箱體的密封性,箱體各部件優化區域如圖 7 所示,深色(圖 7 中靠右端)部位表示可優化區域,淺色部位表示非優化區域。以不同極端載荷工況下箱體各部件有限元仿真最大應力為約束條件,箱體質量最小為優化目標,最終得到箱體拓撲結構,并依據拓撲區域對箱體進行優化設計。主軸、驅動殼與扭力臂分別為連接件與支撐部件,不參與箱體優化,優化部位主要是主殼體、過渡板與后殼體。
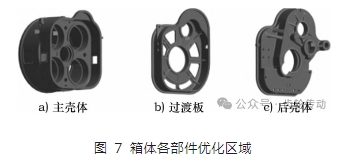
為保證優化結果的準確性和可靠性,且優化條件更接近實際工作條件,選取對箱體受力與位移影響最大的工況 1 與工況 7,分別進行單工況與多工況拓撲優化分析。收斂準則是以 2 次迭代之間質量的相對變化閾值作為迭代結束條件,閾值取 0.001,收斂精度取 10 %。得到不同工況下箱體各部件拓撲優化結果,如圖 8 所示。工況 1 與工況 7 單獨作用下箱體各部分優化后的拓撲結構見圖 8a)、圖 8b),工況 1 與工況 7 組合作用下箱體各部分優化后拓撲結構見圖 8c)。

圖 8 中,相對密度小于 0.4 的區域為材料移除區域,相對密度在 0.4~0.6 之間的區域為邊緣區域,相對密度在 0.6~1.0 之間的區域為材料保留區域。
不同工況下箱體各部件拓撲質量對比如圖 9 所示。由圖 9 可知,單工況與多工況作用下,箱體各部件優化趨勢大體相同,主殼體主要優化了箱體內壁中間連接處與減重孔等非受力區域,過渡板優化了內部軸承孔與箱體整體筋板結構,后殼體優化了下半部分殼體與輸出軸加強筋處殼體。拓撲優化結果中,工況 1、工況 7 和工況 1 與工況 7 組合下的主殼體、過渡板和后殼體的總質量分別減少了 38.88 %、39.47 %和39.84 %。究其原因,單工況優化結果只在該工況作用下達到了局部最優解,而多工況優化結果更全面考慮了多方向載荷共同作用下箱體承載能力的均衡性,達到了最佳的優化結果。
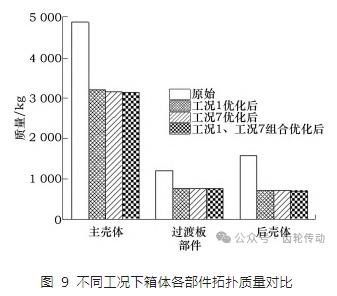
箱體模型重構
圖 8 的優化結果是在沒有考慮箱體密封及可制造性的前提下進行的,最大程度地優化了箱體質量,但是優化結果并不能直接用于設計制造。為使得優化結果與實際生產相結合,基于多工況拓撲優化分析結果,對箱體進行結構重新設計,設計過程中綜合考慮箱體材料、承載性能以及制造工藝等要求。
為此,需要考慮主殼體與后殼體箱體潤滑油的密封與流通,對拓撲優化結果中完全去除材料區域進行減厚與擴孔處理,同時需要滿足鑄造工藝上的最小厚度要求(20 mm);過渡板為主殼體與后殼體的連接件,整體結構可重新構形,為便于實際生產加工,結合拓撲優化結構與原模型,對過渡板進行材料去除。
箱體各部件結構優化設計如圖 10 所示。優化后箱體總質量與原始模型相比減小了 549.8 kg,優化后箱體的質量減小了 4.7 %。
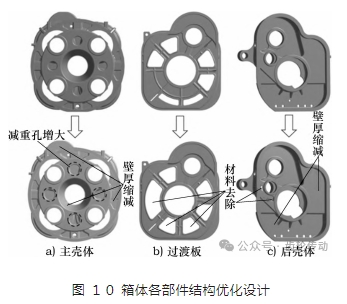
為驗證所設計的重構模型的合理性,對優化后的模型進行有限元仿真校核,優化后箱體整體位移與應力云圖如圖 11 所示。優化前后箱體各部件應力對比如圖 12 所示。優化前后箱體及各部件最大位移與應力對比如圖 13 所示。
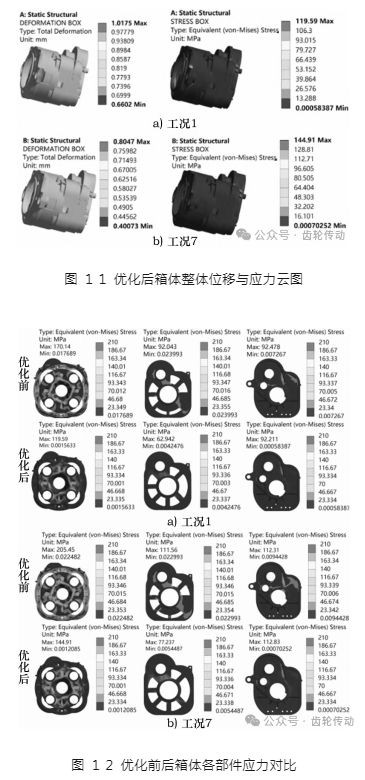
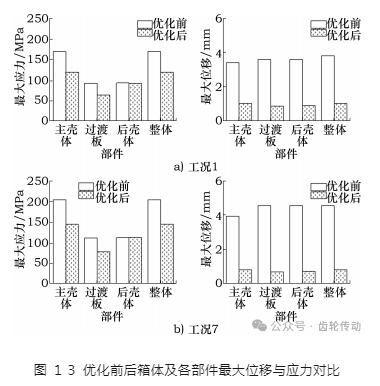
由圖 11~圖 13 可知,優化后箱體整體及各部件等效應力與位移均有較大改善,優化后箱體整體最大應力較原始結構降低了 29.7 %,最大位移較原始結構降低了 82.4 %,且應力與位移云圖分布更均勻。表明優化后的箱體具有更好的承載能力,提高了箱體的強度與剛度,優化結構合理,在減重的同時增強了箱體力學性能。
四、結語
本文針對風電齒輪箱箱體優化設計過程中工況覆蓋不全面、材料利用率低及模型簡化不合理等問題,對箱體進行了輕量化設計。在風電齒輪箱箱體精細化模型的基礎上,分別對 12 種極限載荷工況作用下箱體力學性能進行有限元仿真;結果表明主軸扭矩最大(工況 7)和主軸軸向作用力最大時(工況 1),對箱體應力與位移影響較明顯,且高應力區域主要集中在主殼體上,高位移區域主要集中在扭力臂與后殼體上;箱體整體應力和位移分布都不均勻,需要選取對箱體性能影響最大的工況 1 和工況 7 進行組合分析,進而對箱體進行合理性優化設計。
通過箱體模態試驗與有限元前 10 階模態分析對比,證明有限元模型與實體模型固有頻率的誤差均小于 10 %,振型完全一致,驗證了有限元模型的準確性。基于變密度拓撲優化數學模型對箱體進行輕量化設計,對比單工況與多工況優化結果,認為考慮齒輪箱極端載荷多工況條件的優化結果更合理,更符合實際受載情況。優化后箱體力學性能得到大幅度提升,箱體質量減小了 4.7 %(549.8 kg),達到了箱體輕量化設計的優化目標,對箱體的設計開發、成本降低、功率密度以及可靠性提升均有重要意義。
參考文獻略.