現階段,測量技術在得到不斷的發展后,被運用于數控機械加工領域中,不僅有效地提升了測量結果的精確性,還能有效地規避加工精準度不達標而產生的二次加工問題。顯然,測量技術的特點具有可操控性、精準度高等,在數控機械加工領域中運用測量技術,可為數控加工行業帶來一定的經濟效益。因此,針對在機測量技術展開分析,合理地將其運用到數控機械加工的各個環節之中承擔技術后盾的作用,從而引領數控加工行業走出一條數字化、智能化發展的道路。
一、在機測量技術的工作原理
在機測量技術主要是借助測量工具,使用測量技術或者構建測量系統,針對機床硬件加工的情況開展實時的測量,結合被測產品坐標能對產品集合的特征進行判斷,進而在為之后的加工工藝提供一定的參考價值。
在機測量技術使用時,測頭的位置朝向機床位置移動,在移動過程中所加工的產品會與測頭接觸,在等到一段時間后,測頭內部的觸點便會出現脫開的情況。這時測頭借助無線電通過接收器的傳播,將所獲取的信號發送到機床,機床在收到指令后,會在第一時間內停止運行、跳轉運行、保持運行等。并且,機床中還會將所記錄的一些坐標值、坐標系、相關數據等傳送到系統中,系統進行保存和管理。其中在傳輸過程中,程序會通過所增設的 RS232 串口進行數據的識別、傳輸等,進而結合程序中提到的要求,對所加工的產品進行測量。RS232 串口起到了輔助的功效,可在完成數控系統的任務中將坐標的數據進行傳輸,測量軟件中獲取相應數據。這些數據再根據該軟件中的分類儲量點以及計算誤差補償,詳細記錄用戶所需要的結果報告,進而為后續工作提供指導和參考。以下針對在線測量技術進行了分析(如圖 1)。
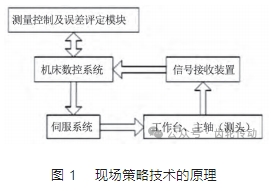
二、在機測量技術在數控機械加工中的應用對策
探測信號的應用,測量航空工件
數控系統測量功能的實現,離不開信號端口的建設。在機測量技術應用時需要以信號端口為依托,開放信號端口,使其測量功能實現最大化。數控系統、測量設備端口的兼容性,一定程度上促使測量設備的精度相對較高,這也是傳感器應用的最大特點。例如,一旦測量功能發出之后,機床就能對發出的信號進行獲取,進而第一時間對信號要求進行掌控,并進行規范化的執行和測量工作。檢測的程序在制定時,質檢中心要與提供的材料進行保持聯系,輔助在機測量技術開展自動化的計算,創建參數矩陣。在得出一些數據后進行刪選,并針對影響因子最大的項作為關注的重點,形成可供參考的加工要點。
檢測程序中可進行多項工作,使用多種方法,這些方法包括中心均值法、平面內三等,構成了該程序的主要應用功能。例如,針對圓角工件(加工參數為 80mm×100mm)開展檢測時,會結合順序移動的情況,對每個檢測點進行檢測,保存檢測的結果,再結合自動化的計算設備或者系統將角度進行旋轉,嚴格對系統中的命令進行執行。而執行指令的發出會與系統中的檢測系統進行碰撞,協調相關的信息,進而對出現的偏差進行及時糾正和輸出。對于圓角工件而言,圓角工件的輪廓可以判斷出角的位置,例如,做好輪廓分析可以采用倒角的方式,夾具也在工作流程的指導下被有效地固定,其最后的結果就是產生了一定的偏差,這些偏差主要體現在角度上和中心的偏移距離上。對于每個要探測的點,結合其數量情況構建坐標。需要引起注意的是每次的測量,其檢測程序都最終歸于初始化的狀態,通過觀看其移動的情況,保留每個檢測點的檢測結果;角度確定時,需要結合計算機設備進行嚴密的計算。
補償程序的設計和運用,解決批量作業誤差
補償程序的設計和運用對于保障各項數據的一致性、精確度高等具有一定的優勢。例如,批量加工作業之中,技術人員采用了刀具半徑補償的方式,這一方式運用后起到的效果為:測頭進行自動的測量時,其尺寸會產生一定的偏差,針對這一情況,適當的運用補償措施,可使產品設計的尺寸與實際生產出來的尺寸差距較小,數據能夠均在一個水平面上。再進行對數控機床刀具進行測量時,會利用試切法的方式,即借助機外測量功能實現刀儀器的測量。相對于手工測量而言,這種方式雖然很常見,但是其煩瑣的工作,將會大大降低工作的效率,還會對最終的測量結果產生一定的偏差。因此,為了克服以上出現的問題,一些學者提到刀具在加工過程中進行測量,其可以根據結果的差值判斷出的刀磨損的問題,主要依據為相鄰測量結果。而機床的探測系統在運用過程中,主要針對的是現有程序可能對后續加工流程進行的測量,在產生一定的尺寸偏差時應用輪廓補償程序,通過機床的探測系統使得整個實驗結果更具可靠性、針對性。
對于一些普通的機床而言,其仿型功能難以得到充分的體現,例如,仿型過程中會產生很多的代碼、復雜的編碼等,編程過程中結合產品的特征,完成探測,做出最終的判斷依據,即反映出了倒角路徑輪廓的情況,在進行補償輪廓時,可以對探點位置進行明確,再對角的尺寸進行確定。因此,探測工作尤為重要,能夠保障所探測位置出現的較大偏差,無法為后續的加工工作提供支持。
輪廓點上的探點,其在編號時需按照連續編號的方式。系統中對探點進行識別,確定探點位置。這樣的方式可以有效避免編碼出現混亂、缺少的問題。在系統的輔助下可以在最快的速度之下將輪廓補償的情況進行識別,并做出報警信息,只有這樣,管理人員才能結合輪廓補償的情況,能對加工現場所出現的各種情況有更深的理解和判斷。因此,在之后的測量過程中,還應對針對輪廓所對應的參考曲線進行探索,這一曲線所展現出的探點離散情況、覆蓋范圍內形成的一條曲線等,這些都可用作參考曲線。加工產品過程中,對于所出現的小概率事件,即加工程序、初始路徑出現了重合的情況,在這一情況下,技術人員可靈活使用調試法針對加工情況進行調試,待到其結束之后程序就會進行重新的編寫。
葉片工序間加工余量優化分配
本文主要結合航空葉片工序間加工余量進行的優化和分配,選用在機測量軟件,其功能需求滿足了以下幾點。
(1)三維模型導入和顯示模塊的運用。該模塊中的數據格式文件具有國際標準數據交換格式,其格式名稱為:STEP 和 IGS,這些數據格式文件可用于導入。在運用這一模塊時,可使用 OpenCASCADE 進行數據的轉換,并能將相關函數進行顯示。
(2)三維測量點選取與測量路徑規劃模塊的建立。在進行三維模型的建立時,可對待測零件做好幾何拓撲處理。經過處理后在機測量點會顯示出來,然后進行測量路徑的規劃。OpenCASCADE 中的幾何拓撲處理中所體現函數類型。
(3)在機測量綜合誤差補償模塊,建立誤差數學模型。
(4)在機測量報告的輸出模塊。數據得出后應根據規定的格式規范輸出相關數據。
針對三維測量點和測量路徑規劃模塊的構建
航空發動機葉片表現所展現出的幾何特征為:曲率、扭轉角呈現的狀態為不斷變化的狀態;平均曲率較大主要體現在前緣和后緣;平均曲率較小的體現在盆地和后緣的位置。通過對這些地方進行檢測點的設置,能夠大幅提升航空發動機葉片的測量精度,也會影響之后的加工效率。接觸式的在機測量,進行精度評價時會根據檢測點中所獲取的自由曲面上的各個坐標方向進行評價,對于離散的測量點,CAD 重造自由曲面,取代幾何體。曲面在重造后達到一定的精確值,可對制造曲面中的測量點重建曲面,精確表示出物理制造曲面,再比較采樣點生成的曲面、設計模型等,能對相關曲面產生的參數進行評估。例如,曲面的峰谷高度誤差、曲面的均方根高度誤差,對加工曲面的公差進行驗證,并及時了解加工曲面的誤差分布。當自由曲面中確定測量多個精確點后,在機檢測的質量相對較高。但是,針對表面上的點的進行檢測,會造成較大的經濟損失。針對這一情況,可使用在機測量技術,應用在機測量采樣點的對策,將自由曲面上結合實際的情況合理布置采樣點,從而在達到降低測量成本、縮短測量時間的基礎上保障重建的制造曲面精度滿足條件。
葉片加工余量的優化分配
本研究中主要使用 PCA+ 改進 ICP+SQP 方法對葉片工序之間加工產生的余量進行了分配和優化,將采用這一方法能對產生的余糧誤差進行補充和消除。借助 SQP 方法準確計算出帶約束的余量問題,不僅使得求解的結果精度更高,還能提升余量求解的效率。例如,以某航空葉片在機測量為例,該案例中所使用的機床為五軸機床,通過構建逆運動學模型,求取機床運動學逆解,利用廣義雅可比矩陣的方式和齊次變換求解,了解機床每一個軸的運動調整量,從而針對機床端加工余量的有效配置和優化。在進行仿真實驗后,其結果顯示:葉片半精加工之后,對葉片加工余量開展分配和優化,葉片半精加工后,其毛坯 MAE 和 RMSE 值相同,即為 0.1μm,在進行優化分配前,其值降低了 99.4% 和 99.8%。精加工后葉片輪廓誤差控制在 1.2μm 左右,相比優化分配前其降低值為 99.8%。葉片的輪廓誤差值為 160.45%,相比分配之前降低 78%。在了解其實驗中產生的數據和仿真的數據,其具有較好的一致性,利用這一方法開展對葉片加工余量的檢測、分配等,可以更好地進行葉片之后的加工工作,使得葉片在加工時,其精度得到不斷的提高,還能借助這一方法,針對葉片加工開展全過程的管理和控制。
齒輪制造在機測量
在機測量技術不僅用于航空工件的測量、葉片的測量,還可以用于齒輪的測量。齒輪在機測量過程中主要用于對齒輪的尺寸測量、齒形檢測和齒面質量評估。其中,齒輪的尺寸測量過程中通過使用光學原理,借助光學投影儀、激光測量和視覺系統開展實時的測量,測量屏幕上的圖像能夠將齒輪的齒廓曲線進行顯示。通過測量軟對齒輪齒廓曲線進行數據采集,這些數據包括齒距、齒頂高、齒底高。在計算齒輪的尺寸、幾何特征和相對位置等參數時,可使用齒距(Pitch)=2πR/Z,其中 R 是齒輪的半徑,Z 是齒輪的齒數;齒頂高(Addendum)=m×(1+x),其中 m 是模數,x 是齒輪齒形修正系數等進行尺寸的計算,在最后的評估階段,一旦出現齒輪尺寸、幾何特征等與相關標準不符,那么就需要對其尺寸進行調整和修正。在機測量技術在應用時,同樣還可以利用光學原理針對航空齒輪齒面的質量進行測量。例如:技術人員針對需要測試的齒輪放置到光學投影儀的底座上,保障齒輪與投影儀的光源垂直對齊。調整投影儀的焦距和放大倍數,將齒輪的齒面放大投射到屏幕上,并使用視覺系統對齒輪齒面所出現的磨損、裂紋、變形程度等進行圖像處理計算,確定齒輪齒面是否出現一定的缺陷。
三、結語
航天航空領域中應用在機測量技術,其為推動航天事業的發展起到了一定的助力作用。本文研究在機測量技術具有一定的意義和作用。尤其是航天領域對于加工技術的精密度有著較高的要求,在機測量技術憑借其高精度、非接觸、自動化優勢,將在今后的一段時間內受到更多行業的認可,未來,在機測量技術也會使用得更加廣泛,從而賦予數控技術智能化的功能。
參考文獻略.