大型工程機械設備是由多種部件構成,每個部件是否能夠穩定運行均影響著工程機械的性能發揮,尤其是齒輪部件?,F今,工程機械設備正在向著高性能、高強度、大型化、高可靠性等方向發展,使得齒輪傳動在設備中承擔的任務愈來愈重,伴隨著工程機械設備應用時間的增加,齒輪內部接觸疲勞逐漸累積,致使齒輪出現裂紋,裂紋擴展范圍過大會發生斷裂現象,造成齒輪失效,威脅著工程機械設備的安全運行。齒輪內部疲勞斷裂可靠性很難進行直接監測,而數值模擬方法為其提供了有力的手段支撐,能夠預測齒輪內部疲勞斷裂可靠性相關數值,為工程機械的穩定運行提供支撐。
文獻以齒輪材料強度退化理論與應力強度模糊干涉函數為基礎,聯合齒輪疲勞準則構建齒輪內部疲勞斷裂可靠性分析模型,探究并計算多種因素對于齒輪內部疲勞斷裂的影響程度,以此為依據,對齒輪進行優化設計,提升齒輪內部疲勞斷裂可靠性;文獻以 20CrMnTi 作為研究對象,在試驗機上進行疲勞斷裂試驗,應用數值模擬軟件對齒輪內部疲勞斷裂過程進行數值模擬,為齒輪優化設計提供有力的支撐;文獻采用 Monte-Carlo 模擬齒輪內部疲勞斷裂過程,并依據齒輪內部疲勞斷裂模擬數值與實際數值之間的誤差對數值模擬過程進行不斷的優化與調整。上述三種方法雖然能夠實現齒輪內部疲勞斷裂數值模擬功能,但是均存在著模擬數值與實際數值之間誤差較大的缺陷,無法滿足工程機械的應用需求,故提出新的工程機械齒輪內部疲勞斷裂可靠性數值模擬方法。
一、疲勞斷裂可靠性數值模擬方法設計
工程機械齒輪模型構建
為了更好地進行齒輪內部疲勞斷裂可靠性數值模擬,獲取更加精準的數值模擬結果,首要環節就是構建工程機械齒輪模型,為后續研究奠定堅實的基礎。工程機械齒輪模型如圖 1 所示。
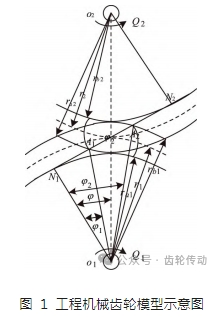
如圖 1 所示,o1 與 o2 表示的是主動齒輪與從動齒輪的中心;Q1 與 Q2 表示的是主動齒輪與從動齒輪的運動方向;N1 與 N2 連線表示的是齒輪副理論嚙合線;A1 與 A2 連線表示的是齒輪副實際嚙合線;r1 、ra1與 rb1分別表示的是主動齒輪對應的分度圓半徑、齒頂圓半徑與基圓半徑;r2 、ra2與 rb2分別表示的是從動齒輪對應的分度圓半徑、齒頂圓半徑與基圓半徑;φ 表示的是齒輪的壓力角;φ1 與 φ2 表示的是主動齒輪與從動齒輪對應的壓力角。齒輪基圓,分度圓和齒頂圓對應的半徑數值如下式所示:
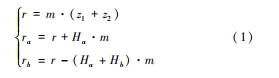
式(1)中,r、ra 與 rb 表示的是齒輪基圓、分度圓與齒頂圓的半徑;m 表示的是齒輪模數;z1 與 z2 表示的是主動齒輪與從動齒輪對應的齒數;Ha 表示的是齒頂高系數;Hb 表示的是頂隙系數。
齒輪重合度好壞是影響其磨損大小的關鍵因素,以齒輪重合度理論為基礎,得到齒輪重合度計算公式:

式(2)中,ζ 表示的是齒輪重合度數值。
一般情況下,齒輪瞬時壓力角是確定理論接觸線的主要依據,其計算公式為:

式(3)中,φt 表示的是齒輪瞬時壓力角;φ1,n與 φ2,n表示的是主動齒輪與從動齒輪對應的瞬時壓力角。
以式(3)計算結果為依據,即可確定齒輪的理論接觸線,具體確定流程如圖 2 所示。
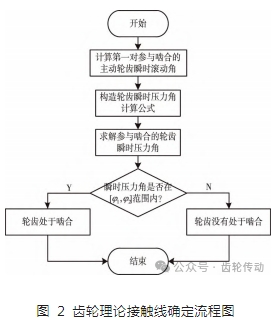
上述過程完成了工程機械齒輪模型的構建,并給出了齒輪理論接觸線的確定流程,為齒輪內部力學特性分析提供支撐。
齒輪內部力學特性分析
以上述構建工程機械齒輪模型為基礎,利用邊界元法求解齒輪內部應力強度因子,分析齒輪內部力學特性,為后續齒輪內部疲勞斷裂可靠性模型搭建提供數據基礎。
由線性斷裂力學分析可知,齒輪內部疲勞裂紋前緣應力場與應變場存在著一定的奇異性,為了更加精準的分析齒輪內部力學特性,利用奇異性邊界元法獲取齒輪內部疲勞裂紋邊界應變性質,以此為基礎,計算齒輪內部疲勞裂紋應力強度因子,為后續研究提供數據支撐。其中,采用八節點等參元方法對齒輪內部疲勞裂紋邊界進行處理,其插值函數表達式為:
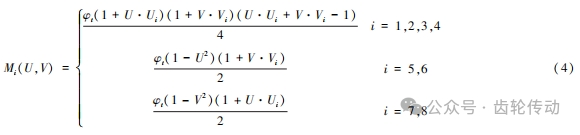
式(4)中,Mi(U,V)表示的是齒輪內部疲勞裂紋邊界插值函數。其中,U 與 V 表示的是橫向與縱向對應的應力數值;Ui 與 Vi 表示的是第 i 個插值點對應的橫向與縱向應力數值。
八節點等參元與等參奇性元如圖 3 所示。
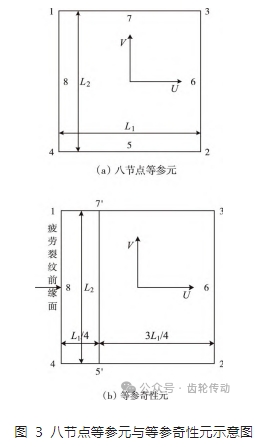
如圖 3 所示,利用等參變換方法確定插值點連線之間的橫軸坐標信息(以插值點 1 與插值點 2 連線為例),計算公式為:

式(5)中,X 表示的是插值點 1 與插值點 2 連線的橫軸坐標信息;X1 、X2 表示的是插值點 1、插值點 2 對應的橫坐標信息。
基于雅可比式原理,結合式(5)計算結果,即可確定齒輪內部疲勞裂紋邊界應變數值,其表達式為:
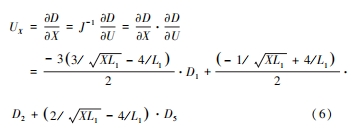
式(6)中,UX 表示的是橫軸方向對應的齒輪內部疲勞裂紋邊界應變數值;D 表示的是位移數值;J-1表示的是雅可比式輔助因子,其取值范圍為[0,1];L1 表示的是齒輪內部疲勞裂紋的長度;D1 、D2 與 D5 表示的是插值點 1、插值點 2 與插值點 5 對應的位移數值。
根據實際情況將齒輪內部疲勞裂紋看作為半橢圓形,即疲勞裂紋前緣參數方程可以寫為:

式(7)中,x 與 y 表示的是疲勞裂紋前緣坐標信息;Vy 表示的是縱軸方向對應的齒輪內部疲勞裂紋邊界應變數值;θ 表示的是半橢圓形裂紋內角。
以柱坐標系為標準來展示疲勞裂紋單元,具體如圖 4 所示。
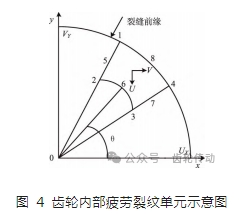
如圖 4 所示,齒輪內部疲勞裂紋位移與應力強度因子之間存在著緊密的聯系,表達式為:

式(8)中,是每循環的裂紋擴展長度;C 是常數;K 是應力強度因子;Kth是裂紋開始擴展所需的最小應力強度因子。
通過求解公式(8)即可獲得齒輪內部力學特性———齒輪內部疲勞裂紋應力強度因子 K,為后續研究提供支撐。
齒輪內部疲勞斷裂可靠性模型搭建
以上述齒輪內部力學特性分析結果為基礎,融合齒輪內部極限狀態,搭建齒輪內部疲勞斷裂可靠性模型,為最終數值模擬實現提供依據。
一般情況下,齒輪內部失效存在一個模糊漸變區,其隸屬函數表達式為:
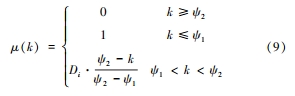
式(9)中,μ(k)表示的是齒輪內部失效模糊漸變區隸屬度數值,k 表示的是模糊數;ψ1 與 ψ2 表示的是模糊上界與下界。
以式(9)計算結果為依據,即可獲得齒輪內部疲勞斷裂可靠性數值,表達式為:
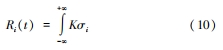
式(10)中,Ri(t)的取值范圍為 0~ 1;σi 表示的是齒輪內部的應力均值。
上述過程完成了齒輪內部疲勞斷裂可靠性的計算,為研究目標的實現提供支撐。
齒輪內部疲勞斷裂可靠性數值模擬
以 2. 1 節構建的工程機械齒輪模型為基底,以 2. 2 節計算獲得的應力強度因子與 2. 3 節搭建的齒輪內部疲勞斷裂可靠性模型為依據,建立齒輪內部疲勞裂紋動態擴展模型,以此為依據,對齒輪內部疲勞斷裂全過程進行數值模擬。
在數值模擬過程中,首要環節就是確定工程機械齒輪內部載荷情況與邊界條件,以此為基礎,應用 ABAQUS 軟件對齒輪進行有限元劃分,具體如圖 5 所示。
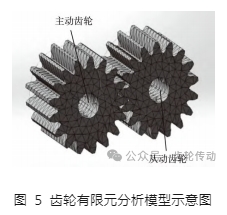
以圖 5 為依據,建立齒輪內部疲勞裂紋動態擴展模型,表達式為:

式(11)中,g(t)表示的是疲勞裂紋動態擴展模型;G[·]表示的是齒輪內部狀態函數;υi(t)表示的是齒輪內部疲勞裂紋的擴展速率。
依據式(11)對齒輪內部疲勞斷裂過程進行數值模擬,為齒輪狀態監測提供有效的方法支撐。
二、實驗與結果分析
設置風電滲碳齒輪內部疲勞斷裂可靠性研究、20CrMnTi 齒輪鋼疲勞裂紋擴展試驗與數值模擬研究為對比方法 1、對比方法 2,聯合提出方法共同進行工程機械齒輪內部疲勞斷裂可靠性數值模擬對比實驗,以此來驗證提出方法的應用性能。
實驗設備選取
依據對比實驗需求,選取疲勞試驗機與齒輪夾具作為主要實驗設備,具體如圖 6 所示。
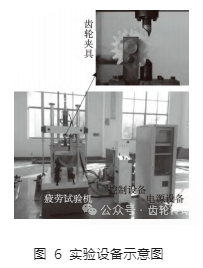
選取的疲勞試驗機實質上是一種機械共振材料試驗設備,頻率范圍為 80~ 250Hz,標準頻率計算公式為:

式(12)中,fo 表示的是疲勞試驗機的標準頻率;Ctotal 表示的是疲勞試驗機的總剛度;Mtotal 表示的是疲勞試驗機的總質量。
依據實驗需求對疲勞試驗機其它參數進行設置,具體如表 1 所示。

上述過程完成了實驗設備———疲勞試驗機與齒輪夾具的選取任務,為實驗的順利進行提供了一定的便利。
實驗結果分析
以上述選取的實驗設備為工具,進行工程機械齒輪內部疲勞斷裂可靠性數值模擬對比實驗,通過齒輪內部疲勞裂紋擴展速率數值模擬結果與齒輪內部疲勞斷裂可靠性數值模擬結果驗證提出方法的應用性能。
通過實驗獲得齒輪內部疲勞裂紋擴展速率數值模擬結果如圖 7 所示。
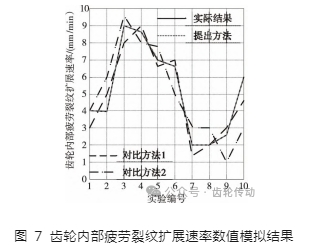
如圖 7 所示,應用提出方法獲得的齒輪內部疲勞裂紋擴展速率數值模擬結果與實際結果基本保持一致,而對比方法 1 與對比方法 2 應用后獲得的齒輪內部疲勞裂紋擴展速率數值模擬結果與實際結果存在著一定的偏差。說明提出方法的模擬結果更加可靠,可以為齒輪狀態分析提供精準的數據基礎。
通過實驗獲得齒輪內部疲勞斷裂可靠性數值模擬結果如圖 8 所示。
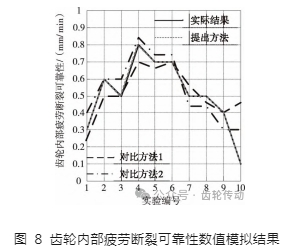
如圖 8 所示,應用提出方法獲得的齒輪內部疲勞斷裂可靠性數值模擬結果與實際結果基本保持一致,而對比方法 1 與對比方法 2 應用后獲得的齒輪內部疲勞斷裂可靠性數值模擬結果與實際結果存在著一定的偏差。由此進一步驗證了提出方法的應用效果,其具備較高模擬精度,有利于保障工程機械設備運行穩定性與安全性。
三、結束語
隨著工程機械設備應用頻率的升高,其應用缺陷逐漸顯現,尤其是齒輪內部疲勞斷裂故障,直接威脅著工程機械能否繼續運行,其直接監測難以實現,故提出工程機械齒輪內部疲勞斷裂可靠性數值模擬方法。實驗結果顯示:提出方法應用后獲得的數值模擬結果與實際結果基本相同,表明提出方法數值模擬精度較高,能為工程機械穩定運行提供有效的保障。
參考文獻略.