齒輪作為重要的傳動零件,在整個機械領(lǐng)域中應(yīng)用極其廣泛,隨著科技技術(shù)的發(fā)展,齒輪的轉(zhuǎn)速和載荷的增高,其運轉(zhuǎn)的平穩(wěn)性受到重視,同時對齒輪的結(jié)構(gòu)要求越來越嚴。齒圈(見圖1)是機械齒輪中較為普遍的一種樣式,為了保證齒輪強度以及相配件的強度,齒圈的內(nèi)外徑尺寸多受限制,導致齒圈輪緣較薄,齒圈直徑與輪緣厚度的比值高達15以上,其內(nèi)圈有兩個用于跟軸連接的對稱鍵槽,為了達到齒圈和軸的配合效果,兩鍵槽對內(nèi)孔有對稱度的位置要求,使得齒圈剛度較差,抗疲勞性差,在加工過程中極其容易使零件變形,導致齒部扭曲,影響齒部載荷分布以及零件的可靠性和穩(wěn)定性。
由于鍵槽齒圈的鍵槽與軸配合工作時,沿其齒內(nèi)圈方向存在較大的切向相對滑動力,因而會產(chǎn)生較大的切向力;另一方面,齒輪鍵槽與鍵接觸時,其接觸應(yīng)力會很大,致使齒輪鍵槽過早被壓饋,使齒輪磨損加劇,如果齒輪的齒面出現(xiàn)不同的齒牙有不同的滲碳層深度,也影響齒輪的抗疲勞性能。所以對于加工精度、齒面粗糙度和滲層深度要求很高的鍵槽齒圈,其加工工藝顯得尤其重要,也就 證明在齒圈加工過程中需要有一個穩(wěn)定的熱處理方式、精確的定位精準進行鍵槽及齒形的加工,保證零件抗疲勞性的同時提高生產(chǎn)效率。
一、帶鍵槽薄壁齒圈的結(jié)構(gòu)特點
本文研究的帶鍵槽薄壁齒圈材料為優(yōu)質(zhì)碳素鋼 12Cr2Ni4A,內(nèi)孔尺寸為 Ø100+0.030,齒數(shù)為 48,模數(shù)為 2.5mm,壓力角20°,齒面粗糙度為 Ra0.4,齒圈最薄處為3.5mm,齒圈直徑與輪緣厚度的比值高達29.8,鍵槽對內(nèi)孔的對稱度為0.03mm,零件熱處理方式為滲碳淬火,齒面硬度為59~63 HRC,芯部硬度 d=3.1-3.55,齒輪精度等級為 GB/T100955.1-2022-6級。
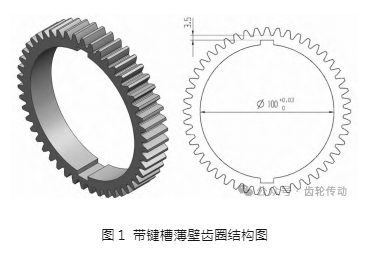
二、工藝方案設(shè)計
此類薄壁齒圈內(nèi)孔有兩對稱鍵槽,輪齒部位作為傳動、內(nèi)孔鍵槽作為固定連接零件,其高轉(zhuǎn)數(shù)和高載荷的使用工況,對其制造工藝提出了較苛刻的要求,由于尺寸和技術(shù)條件的偏離,會導致整個機械系統(tǒng)不能正常工作,使可靠性穩(wěn)定性降低,因此必須考慮提供一種精度高、熱處理穩(wěn)定、不易變形、適用于批量生產(chǎn)的帶鍵槽薄壁齒圈的加工工藝,去保證零件的性能。
零件特點及加工難點分析
分析圖 1 結(jié)構(gòu)及參數(shù),鍵槽對內(nèi)圈的對稱度為 0.03mm,齒圈最薄處為3.5mm,內(nèi)孔尺寸為 Ø100+0.030,尺寸精度和位置精度要求高。帶鍵槽齒圈不同于常用齒圈的是其徑向尺寸與壁厚尺寸相差懸殊,達到29.8倍,剛性差,硬度高(≥HRC59),在車削階段必須采用基準先行的方式,保證內(nèi)孔與外圓的圓軸線同軸度、端面與內(nèi)孔軸線的垂直度以及兩平面的平行度,滿足齒輪粗加工的定位要求和精度要求;精加工內(nèi)孔的夾具設(shè)計也至關(guān)重要,保證經(jīng)過內(nèi)孔(粗插鍵槽后)磨削余量均勻及夾緊力均勻分布,減小裝夾引起的變形;另外需要選擇合適的切削條件,優(yōu)化工藝流程及工藝參數(shù),合理安排加工工序,加工路徑,減小變形及精插鍵槽余量,從而保證薄壁齒圈精度等級,提高加工效率。
高精度齒圈的鍵槽和輪齒加工,需采用粗精加工相結(jié)合的方式,其中齒輪粗加工一般采用滾齒、插齒,齒輪精加工采用磨齒;鍵槽的粗精加工采用插鍵槽的方式??刂苹鶞示?、滲層深度及磨削余量,以保證齒輪齒面滲碳層深度的一致性和表面完整。在保證其他尺寸及技術(shù)條件合格的情況下,齒面滲碳層深度的一致性,一直是行業(yè)領(lǐng)域內(nèi)的關(guān)鍵技術(shù)難題。
在實際加工過程中主要存在以下難點:(1)整體結(jié)構(gòu)方面:薄壁零件易變形,內(nèi)孔精度難以保證。(2)表層方面:齒面滲碳層深度的一致性控制難。(3)表面方面:齒面磨齒后有黑皮現(xiàn)象,齒面表面粗糙度 Ra0.4控制難。
解決制造難點的方案設(shè)計
綜合考慮經(jīng)濟效益、加工難度、人工操作和設(shè)備要求等各方面因素,結(jié)合實際情況,針對以上加工難點,分別提出了解決方案,每個方案并不是相互獨立的,而是相互影響、相互關(guān)聯(lián)的,具體如下。
零件整體結(jié)構(gòu)易變形控制方案設(shè)計:(1)“粗插鍵槽+穩(wěn)定處理、磨內(nèi)孔+以內(nèi)孔為基準精加工鍵槽及齒輪+穩(wěn)定處理”的構(gòu)思
由于零件是薄壁結(jié)構(gòu),鍵槽的加工勢必進一步導致零件的變形,本文創(chuàng)造性地使用粗、精插相結(jié)合,同時在粗、精插工序之間采用穩(wěn)定處理、精磨基準、鍵槽和齒輪的加工基準統(tǒng)一的方式,很好地解決了零件變形的難點。粗插鍵槽去處大部分余量,在對零件進行穩(wěn)定處理(低溫回火時間2.5~3h,溫度145±10 ℃,低溫回火開始時間為粗插鍵槽加工完成后的0~3h),精插時修正尺寸和技術(shù)條件,鍵槽和齒形精加工時采用同一基準,避免基準轉(zhuǎn)換造成的形位誤差的偏離。
(2)采用節(jié)圓夾具以齒牙定位,磨加工內(nèi)孔的方式
圖2中齒圈放置在節(jié)圓夾具的內(nèi)圓孔中,夾具的內(nèi)圓孔并不是圓,而是帶有三等分微小弧度的內(nèi)孔,即等圓心角分布在內(nèi)圓孔表面的三個弧度,然后將3根定位銷(直徑為4.14)均勻放置在齒槽中,利用內(nèi)圓孔的三等分微小弧度自定心的作用,旋轉(zhuǎn)齒圈并固定,這里可以把三個弧度理解為三個弧形缺口,旋轉(zhuǎn)齒圈時定位銷進入該缺口定位,然后采用3塊壓板壓緊齒圈端面,磨加工齒圈的內(nèi)孔,該內(nèi)孔作為鍵槽基準和磨齒基準,使鍵槽和齒部的基準一致,能很好地保證鍵槽與齒部的位置關(guān)系,也能較好地消除熱處理帶來的變形,使磨齒時每個齒牙的去除余量一致,保證齒部的硬度和滲碳層深度。
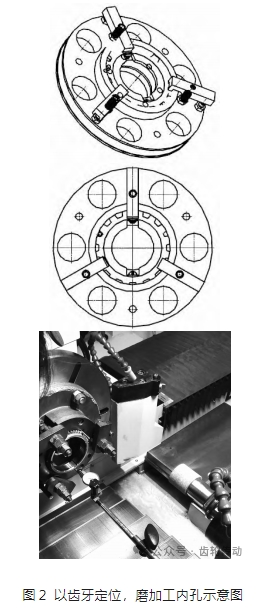
齒輪表層滲碳層深度一致性控制方案設(shè)計:為保證齒面滲碳層深度的一致性,采用滲碳前控制零件精度-滲碳和機械加工時減小零件變形-減小齒輪的磨削余量的方法。(1)滲碳前控制零件精度主要是控制齒厚公差在0.05mm 以內(nèi);(2)考慮零件的抗疲勞性,在加工過程中,應(yīng)盡量多產(chǎn)生殘余壓應(yīng)力,因此齒面的磨削余量一般在滲碳深度的10%~20%;(3)磨齒的齒厚公差控制在0.05mm 以內(nèi)。因此,在工藝編制中,齒輪的磨削余量設(shè)定為:0.15±0.05mm,齒輪在熱處理滲碳工序中,滲碳層深度設(shè)定為1±0.1mm,滾齒加工是齒面的凸起量設(shè)定 為0.2~0.3mm。
通過上面兩方面的控制,在磨齒加工中,最小磨削余量為0.1mm,最大磨削余量為0.2mm,齒面的滲碳層深度得到了控制,齒廓的凸起也得到了保證。
齒輪表面磨齒后局部有黑皮現(xiàn)象及齒面粗糙度 Ra0.4控制方案:(1)齒面磨齒后有黑皮由三方面因素共同引起的,第一是熱處理變形大,導致齒部扭曲;第二是兩對稱鍵槽在加工后,齒圈最薄處為3.5mm,零件的剛性變差,整體產(chǎn)生不規(guī)則變形;第三是由于磨齒余量較小 0.15±0.05。因此在磨齒前做好砂輪的平衡,使砂輪處于一種良好的工作狀態(tài);在零件裝夾時保證零件內(nèi)孔同心于機床的兩頂尖。
(2)齒面粗糙度 Ra0.4一般是在磨齒加工保證,在加工前首先要將磨削砂輪先進行初平衡,砂輪精修整完成后,再次進行砂輪的平衡,以確保砂輪磨削加工的平穩(wěn)性;其次要保證零件的剛性裝夾;最后在磨齒進刀前,機床進行空轉(zhuǎn)20分鐘以上,使機床處于穩(wěn)定的運轉(zhuǎn)狀態(tài)后方進行零件的磨齒加工。
加工工藝路線制定
根據(jù)零件的結(jié)構(gòu)特點和技術(shù)及精度要求,以“粗插鍵槽+穩(wěn)定處理、磨內(nèi)孔+以磨好的內(nèi)孔為基準精加工鍵槽和齒輪+穩(wěn)定處理”的構(gòu)思擬訂以下工藝方案:
(1)粗車外形,該外形作為下一工序的裝夾基準。
(2)精車內(nèi)孔,該內(nèi)孔作為滾齒加工基準。
(3)滾齒,齒厚公差控制在0.05mm 以內(nèi),齒厚留余量0.15±0.05mm 用于磨齒加工。
(4)倒角和去毛刺,齒輪輪廓按 R0.5±0.2加工,其余按 R1±0.5加工。
(5)熱處理,包括滲碳和淬火,保證齒部滲碳層深度設(shè)定為 1±0.1,其余部位沒有滲層,齒面硬度為 59~ 63HRC,芯部硬度d=3.1-3.55。
(6)車加工內(nèi)孔,如采用數(shù)控車床用三爪卡盤裝夾齒頂圓加工時,夾緊力要適中,在加工前需要找正內(nèi)孔跳動在0.1mm 以內(nèi);如果采用節(jié)圓夾具裝夾零件時,需以熱處理后的齒部輪廓為裝夾基準(見圖2)。該工序的目的是消除熱處理后齒圈內(nèi)孔的變形,進而將該內(nèi)孔作為鍵槽粗加工基準。
(7)粗插鍵槽,粗插鍵槽前找正內(nèi)孔在 0.01 mm 以內(nèi),留余量加工。
(8)穩(wěn)定處理(低溫回火);低溫回火開始時間為粗插鍵槽加工完成后的 0~3h,溫度 145±10 ℃,保溫時間2.5~3h。
(9)磨兩端面至設(shè)計尺寸,保證兩端面的平行度在0.015mm 以內(nèi),平面度在0.01mm 以內(nèi)。
(10)穩(wěn)定處理(低溫回火),低溫回火開始時間為磨兩端面加工完成后的 0~3h,溫度 145±10 ℃,保溫時間 2.5~3h。
(11)磨內(nèi)孔,采用節(jié)圓夾具裝夾零件,以齒部輪廓為裝夾基準、端面為定位基準(見圖2),精磨內(nèi)孔至設(shè)計尺寸,該內(nèi)孔將作為鍵槽精加工和齒形精加工的基準。
(12)穩(wěn)定處理(低溫回火),低溫回火開始時間為磨內(nèi)孔加工完成后的 0~3 h,溫度 145±10 ℃,保溫時間2.5~3h。
(13)精插鍵槽,加工前找正內(nèi)孔在0.01mm 以內(nèi),將鍵槽加工至設(shè)計尺寸。
(14)穩(wěn)定處理(低溫回火);低溫回火開始時間為鍵槽加工完成后的 0~3 h,溫度 145±10 ℃,保溫時間2.5~3h。
(15)齒形精加工;機床采用磨齒機床、夾具采用帶錐度芯棒裝夾加工,單面去除余量在0.15±0.05mm 之間, 按齒輪精度等級為 GB/T100955.1-2022-6級加工,齒面進行燒傷檢查,并保證齒面粗糙度 Ra0.4。
(16)穩(wěn)定處理(低溫回火),低溫回火開始時間為磨齒加工完成后的 0~3 h,溫度 145±10 ℃,保溫時間2.5~3h。
(17)拋光齒端面邊緣。
(18)檢驗。
(19)表面處理。
三、結(jié)語
(1)通過帶鍵槽薄壁齒圈的加工試驗研究,以“粗插鍵槽+穩(wěn)定處理、磨內(nèi)孔+以磨好的內(nèi)孔為基準精加工鍵槽和齒輪+穩(wěn)定處理”為構(gòu)思,優(yōu)化了加工方法,得到合理可行的加工工藝。
(2)解決了帶鍵槽薄壁齒圈的變形問題,加工內(nèi)孔時,設(shè)計了節(jié)圓夾具,采用節(jié)圓定位,較好地消除熱處理帶來的變形,使磨齒時每個齒牙的去除余量一致,提高定位精度。
(3)采用滲碳前控制零件精度-滲碳和機械加工時控制零件變形-齒精加工時控制磨削余量的方法,保證齒面滲碳層深度的一致性,提高零件的抗疲勞性能。
參考文獻略.