來自德國的知名汽車零部件企業施洛特集團(SCHLOTE)采取了這樣一種策略:選擇最優秀的加工設備,高度自動化,在更短的時間內生產出高質量的產品——效率意味著更多的利潤。
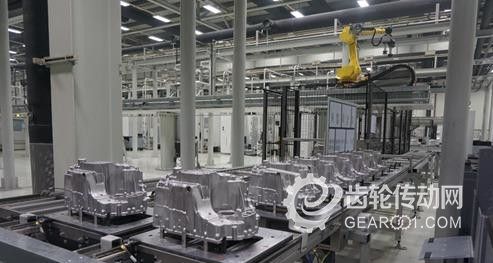
黃金搭檔
成立于1969年的施洛特集團是一家專業致力于汽車領域復雜發動機、底盤及傳動組件機械加工的汽車零部件供應企業,主要生產排氣歧管、傳動裝置箱體、搖擺軸承等產品。在公司成立的四十余年時間里,施洛特憑借優異的技術水準和絕佳的產品質量贏得了包括大眾、寶馬、奧迪、保時捷等在內的眾多知名汽車企業的信任,并成為他們的一級供貨商。為了與客戶形成更緊密的聯系,同時為了拓展中國這一全球最大的汽車市場,2013年,施洛特正式在天津成立了生產工廠。盡管正式落戶中國的時間并不長,但施洛特甫一亮相就快速嶄露頭角:其不僅成功完成了既有客戶的龐大訂單,而且開始贏得一批中國新客戶的信賴。施洛特加工能力之強大,某種程度上跟它所使用的那把“利劍”不無關系--這把“利劍”就是德國埃斯維機床有限公司(簡稱SW公司)所提供的高高度自動化、高性能加工生產線。
事實上,施洛特集團很早便與SW展開了密切的合作。以施洛特的一位重要客戶--大眾汽車為例,大眾每年要生產900萬輛汽車,而施洛特要為其供應大約90萬個齒輪箱。面對如此龐大的生產量,要想高質、高效地完成生產任務,必須要采用性能強大的加工設備,必須提升自動化水平和生產效率。“施洛特最拿手的是生產汽車零部件中最難的部分,例如變速箱。而我們最強大的競爭力就是能夠保證在更短的時間內生產出更高質量的產品。”施洛特天津工廠廠長 Heiko Thuene先生不無自豪地說道。因此,當施洛特落戶天津時,他們毫不猶豫地再次選擇了SW的解決方案--這對早已默契配合的搭檔再次珠聯璧合,以勢不可擋之姿“殺入”了競爭已呈白熱化的中國汽車市場。
那么話說回來,SW的設備究竟有何突出的性能?其與施洛特又是怎樣配合的呢?
在回答這個問題之前,我們先來回看一下這家近年來發展異常迅猛的企業:SW公司成立于1981年,其前身是以生產高精度武器而享譽世界的Heckler & Koch公司。1984年,SW開始生產多主軸機床,并將其作為自己的核心產品。從彼時起,SW進行了密集的研發與創新,逐漸形成了一系列獨有的核心技術,如整體框架式專利設計、矩形橫梁式工作臺設計、搖籃式雙橫梁工作臺設計等等。這些優勢技術融合精益生產打磨所誕生的機床產品具備強大的性能,尤為適用于復雜工件的大批量生產,在提升工件加工效率、降低單件成本方面更是具備極強的競爭優勢。踏著汽車業大發展的節拍,SW僅用幾十年時間就與那些百年企業并駕齊驅,躋身全球優秀設備供應商前列。迄今,SW的業務已遍及全球35個國家和地區。
工藝專家
Thomas Maentele先生是SW公司大客戶專員,他告訴我們,施洛特天津工廠采用了SW公司的兩款機床產品--BAW06-22和BAOne6, 共48臺。SW以其多主軸機床聞名于世,而BAW06-22正是一款“雙主軸+雙工作臺”產品,其快速移動速度達120米/分,加速度可達3g,是目前市場上同等尺寸機床產品中最快的。相比市場上的單主軸產品,它可以在兩個裝夾位置完成一個工件所有面的加工;工裝夾具可直接安裝在橫梁式工作臺上,每個子工作臺由力矩電機驅動,并帶有自身的直接位移測量系統,而且可在任何時候擴展。BAW06-22不僅具備極高的加工精度和動態特性,還能避免多次裝夾,節省了人員操作,由此降低了成本。
“通常機床只有一個主軸,加工起來很耗時;而SW的雙主軸機床極大地提升了效率,例如普通機床生產一個零件需要5分鐘的話,SW僅需要2分半!對于我們來說,效率就意味著更多的利潤。”施洛特天津生產經理 Christian Hirche先生和生產經理助理 Martin Hausmann先生對細節了如指掌。同時, 因其節約了占地面積和能耗,降低了使用維護費和勞動力成本,綜合流程和盈利性計算,平均到工件的單件制造成本也實現了極其可觀的下降幅度。
BAOne6是SW少數的單主軸機床之一,主要用來配合BAW06-22,某種程度上可以說是專門針對施洛特設計的。其主軸轉速可達17500 轉/分,加速到最高轉速所需時間低于0.7秒。這款產品也融入了SW另一項重要技術--搖籃式橫梁工作臺。搖籃式雙工作臺的設計理念可實現在加工的同時在另外一個工作臺進行工件的裝卸,同時可避免在裝卸毛坯和已經加工工件時停機,還可以直接操作自動裝卸裝置。這樣既做到了穩定可靠,又提升了加工效率。
“自動化零件制造行業的競爭極為激烈,利用生產周期來贏得大項目變得越來越重要。不過,更重要的是降低每個零件的成本。SW還跟施洛特在計算零件成本方面進行了緊密合作。”Thuene先生說道。
Christian Hirche先生補充道,客戶告訴施洛特一年所需的零件數量后,他們就開始計算生產時間。這種計算十分精細,甚至確定到了每天、每分鐘--舉例來說,如果一年要生產的零件數量是1萬件,施洛特與SW會計算好生產總共需要花費多少天,而每天又需要花費多少分鐘。為了完成這種精細計算后的加工任務,加工生產節拍必須與自動生產節拍高度融合在一起。對于一般的設備供應商來說,這無疑是一項巨大的挑戰;但SW不僅能提供高性能的加工中心,還能提供自動化整體解決方案!
2015年初,SW并購了自動化專家Bartsch公司。Bartsch專門從事生產自動化設備的研發、制造及其跟蹤服務,其內容包括了從配備執行加工任務的機器人單元到裝配設備,到提供裝配中心、生產中心及加工中心的配套組合鏈等獨立的自動化設備。SW與Bartsch通力合作,可為客戶制定從原料到成品的全套生產程序計劃。
具體來說,通過在加工中心前封閉式裝載門上方配備工作臺毛坯件輸送線,可用于加工中心加的直接裝卸,而雙軸龍門起重機也對組件直接進行裝卸;內置真空夾具可將組件自動堆垛,自動碼放至塑材中間夾層位置;通過加裝精調機器人可進行毛刺排除、裝配、氣密檢驗、清洗檢查等等。不僅如此,SW還跟Bartsch緊密合作,在工業4.0方面進行了大力拓展,現已能向用戶提供整體智能解決方案,而且打通了生產數據與MES的接口,走在了工業4.0發展的最前端。
SW的加工設備與自動化系統為施洛特帶來怎樣的效果呢?Thuene先生告訴我們,SW的機床在保證高精度加工的同時帶來了極高的加工效率,加工一個極其復雜的零件僅需50分鐘;而從鑄件到最后的可視化檢測,共有7個生產步驟,但已經實現了高度自動化,整條生產線上目前僅有兩個工位需要人工。
SW與施洛特這對“黃金搭檔”的合作還體現在其他諸多方面。SW的德國工程師經常會來到天津工廠為員工進行培訓,對編程進行更新完善、對設備進行及時維護……這些周到的服務充分保障了施洛特的安全、高效生產。此外,SW與施洛特還密切配合,持續致力于提升生產效率。施洛特的目標是在下一個項目中將生產周期縮短15%。“我們有遠大的目標,要在中國這個不斷上升的市場中成為集團中最大的工廠。所以我們要和我們的‘好搭檔’齊頭并進。”Thuene先生笑了笑,充滿信心地說道。
SW蘇州工廠投入使用,標志著這位“工藝專家”在中國市場上的發展進入了嶄新階段;而在未來5年內,施洛特位于天津的工廠也將進行二期建設,占地6萬平方米。這對“黃金搭檔”在中國市場上的根正越扎越深,他們將攜手并進,迎來更廣闊的天空。
整條生產線僅有兩工位需要人工
施洛特集團是一家專業致力于汽車領域復雜發動機、底盤及傳動組件機械加工的汽車零部件供應企業。
施洛特天津工廠采用了SW公司的兩款機床產品--BAW06-22和BAOne6, 共48臺。
SW的雙主軸機床極大地提升了效率,同時, 節約了占地面積和能耗,降低了使用維護費和勞動力成本,平均到工件的單件制造成本大幅下降。
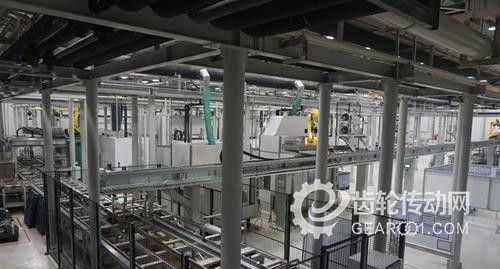
從鑄件到最后的可視化檢測,共有7個生產步驟,已經實現了高度自動化,整條生產線上目前僅有兩個工位需要人工。