有著“工業之母”稱號的模具可謂工業生產的基礎裝備,據統計,75%的粗加工工業的產品零件、50%的精加工零件都依靠模具成型。想象一下,我們生活中隨處可見的各類商品都可能是從五花八門的模具演變而來。
近年來,隨著汽車工業、電子信息、家電、建材及機械等行業的高速發展,中國模具產業也進入了發展快車道。據中商產業研究院發布的《2017-2022年中國模具市場前景調查及投資機會研究報告》預測,2018年中國模具行業銷售總額將超過2,000億元。但是值得留意的是,以精密、復雜、長壽命、大型模具為主的高檔模具目前仍有很大一部分依賴進口,這為模具制造商們留下了一些思考。
高檔模具究竟離“中國制造”有多遠?——通常,這些高檔模具結構復雜,為了保證其壽命,制造精度要求極其苛刻,其加工工藝在經過銑削加工后需要進行電火花加工,才能達標。在這一生產過程中,需要留意一個影響模具精度的關鍵元素——電極(也稱為銅公)。電極一般在加工中心加工完畢后會被移入火花機進行放電。除了模具本身的加工誤差之外,電極也會出現尺寸誤差和中心偏移的問題,因此在放電加工之前,檢測電極的精度和中心偏移也變得十分重要。
無處不在的測量專家
在過去,電極由于數量眾多、形狀各異、檢測程序耗時耗力等問題無疑為高效檢測設置了障礙,那應該如何正確打開電極的自動化檢測方式?答案就是:您需要一個生產現場的測量專家,即可以無疑集成到生產線的自動化檢測。
譬如,可以想象一下這樣的畫面——機械手聽從指令從擺放整齊的電極料庫中進行拾取,旋即放置到檢測定位工裝上,再通過一臺車間型坐標測量機進行電極自動測量。過程中每一環的信息都會被記錄,測量結果反饋給火花機或加工中心實現自動路徑修正……測量系統循環往復從而形成一個閉環。并且,該電極自動化檢測單元完全能夠跟上前端加工中心等設備的加工節拍。這樣一來,以往低效、繁瑣的模具及電極加工及檢測將被徹底顛覆。
其自動化檢測的創新關鍵點包括:首先,將用戶的測量室搬到生產現場——在線型坐標測量機無縫集成到產線,避免耗時費力的運輸與等待;同時也能滿足生產線多產品快速切換生產節拍——機械手自動化更換握爪,用于抓取不同種類的工件和電極,提高零件加工和檢測效率;輕松實現自動測量,并實時監控反饋加工質量:使制造過程和質量更加可靠。
整個測量系統的關鍵除了自動化的集成,還在于ZEISS DuraMax車間型坐標測量機——直接嵌入于生產流水線,該設備受環境等因素影響極小,無需額外外罩或空調,無需壓縮空氣,直接可以無縫集成到自動物流與信息流中。這令檢測真正從實驗室走向車間,實現了在線實時檢測。同時,無需硬件改動,通過自動編程就能快速適應產品變化。
對于精密及超精密模具,ZEISS的另一款產品CONTURA三坐標測量機還可以在實驗室組成自動化檢測單元隨時“待命”。其測量結果及數據能夠自動保存,無縫對接到MES系統,實現加工和檢測信息和數據的實時傳輸和反饋。
1個檢測單元,實現8個自動化
在全面擁抱工業4.0或中國制造的新時代中,我們更享受于智能、自動帶來的便捷,并通過靈活運用大數據實現精準生產。那么,像這樣一個模具及電極的自動化加工、檢測單元,究竟自動化程度有多厲害?相信下列的每一項都會令你迫不急待地想近距離感受一把:
l RFID自動識別:智能識別電極、工件身份信息及料架位置信息
l 自動生成測量程序:根據3D模型在手動或自動選擇測量點,系統自動生成測量程序
l 自動化上下料:系統集成機械手自動上下料至加工中心、火花機、坐標測量機
l 自動化零件測量:加工完成后,上料至三坐標測量機,自動調用對應測量程序并完成測量
l 自動刀具預調:三坐標測量機自動輸出電極偏心,火花機根據電極偏心量自動優化路徑
l 測量設備無縫集成到產線:坐標測量機直接嵌入于生產流水線,實現在線自動化測量
l 自動分揀:根據檢測結果自動進行合格、不合格產品分揀
l 自動安全檢查:機械手在上下料和裝夾過程中都會進行自動安全檢查
近年來,隨著汽車工業、電子信息、家電、建材及機械等行業的高速發展,中國模具產業也進入了發展快車道。據中商產業研究院發布的《2017-2022年中國模具市場前景調查及投資機會研究報告》預測,2018年中國模具行業銷售總額將超過2,000億元。但是值得留意的是,以精密、復雜、長壽命、大型模具為主的高檔模具目前仍有很大一部分依賴進口,這為模具制造商們留下了一些思考。
高檔模具究竟離“中國制造”有多遠?——通常,這些高檔模具結構復雜,為了保證其壽命,制造精度要求極其苛刻,其加工工藝在經過銑削加工后需要進行電火花加工,才能達標。在這一生產過程中,需要留意一個影響模具精度的關鍵元素——電極(也稱為銅公)。電極一般在加工中心加工完畢后會被移入火花機進行放電。除了模具本身的加工誤差之外,電極也會出現尺寸誤差和中心偏移的問題,因此在放電加工之前,檢測電極的精度和中心偏移也變得十分重要。
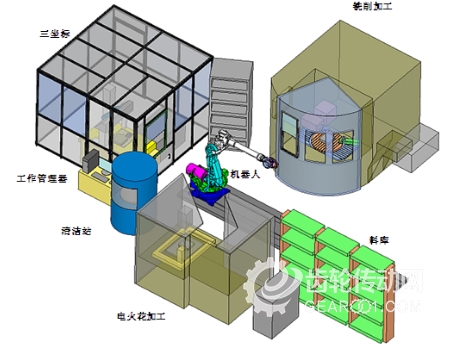
圖:整個模具生產的環節會經過三道不同的工序:加工中心加工模具和電極——三坐標測量機檢測工件及電極、實現刀具的預調——電火花機放電加工模具
無處不在的測量專家
在過去,電極由于數量眾多、形狀各異、檢測程序耗時耗力等問題無疑為高效檢測設置了障礙,那應該如何正確打開電極的自動化檢測方式?答案就是:您需要一個生產現場的測量專家,即可以無疑集成到生產線的自動化檢測。
譬如,可以想象一下這樣的畫面——機械手聽從指令從擺放整齊的電極料庫中進行拾取,旋即放置到檢測定位工裝上,再通過一臺車間型坐標測量機進行電極自動測量。過程中每一環的信息都會被記錄,測量結果反饋給火花機或加工中心實現自動路徑修正……測量系統循環往復從而形成一個閉環。并且,該電極自動化檢測單元完全能夠跟上前端加工中心等設備的加工節拍。這樣一來,以往低效、繁瑣的模具及電極加工及檢測將被徹底顛覆。
其自動化檢測的創新關鍵點包括:首先,將用戶的測量室搬到生產現場——在線型坐標測量機無縫集成到產線,避免耗時費力的運輸與等待;同時也能滿足生產線多產品快速切換生產節拍——機械手自動化更換握爪,用于抓取不同種類的工件和電極,提高零件加工和檢測效率;輕松實現自動測量,并實時監控反饋加工質量:使制造過程和質量更加可靠。
整個測量系統的關鍵除了自動化的集成,還在于ZEISS DuraMax車間型坐標測量機——直接嵌入于生產流水線,該設備受環境等因素影響極小,無需額外外罩或空調,無需壓縮空氣,直接可以無縫集成到自動物流與信息流中。這令檢測真正從實驗室走向車間,實現了在線實時檢測。同時,無需硬件改動,通過自動編程就能快速適應產品變化。
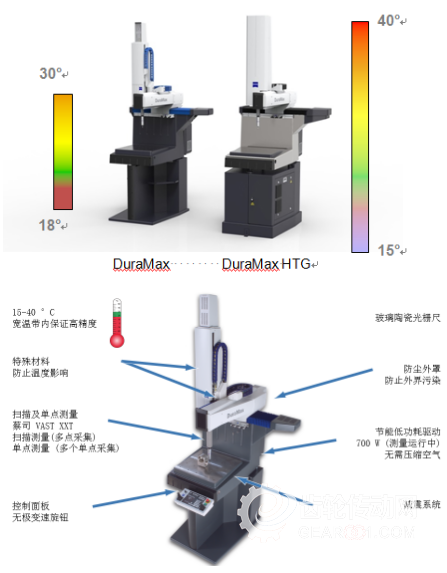
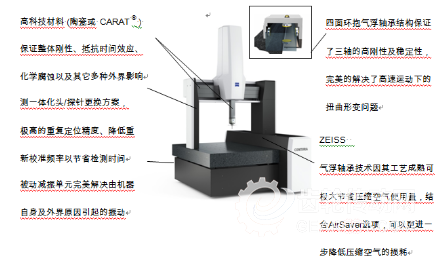
圖:ZEISSMM CONTURA 精密模具自動化檢測單元
1個檢測單元,實現8個自動化
在全面擁抱工業4.0或中國制造的新時代中,我們更享受于智能、自動帶來的便捷,并通過靈活運用大數據實現精準生產。那么,像這樣一個模具及電極的自動化加工、檢測單元,究竟自動化程度有多厲害?相信下列的每一項都會令你迫不急待地想近距離感受一把:
l RFID自動識別:智能識別電極、工件身份信息及料架位置信息
l 自動生成測量程序:根據3D模型在手動或自動選擇測量點,系統自動生成測量程序
l 自動化上下料:系統集成機械手自動上下料至加工中心、火花機、坐標測量機
l 自動化零件測量:加工完成后,上料至三坐標測量機,自動調用對應測量程序并完成測量
l 自動刀具預調:三坐標測量機自動輸出電極偏心,火花機根據電極偏心量自動優化路徑
l 測量設備無縫集成到產線:坐標測量機直接嵌入于生產流水線,實現在線自動化測量
l 自動分揀:根據檢測結果自動進行合格、不合格產品分揀
l 自動安全檢查:機械手在上下料和裝夾過程中都會進行自動安全檢查