齒輪制造的專業性要求不再像以前那么高。這一說法來自一個機床工具生產商,據說它提供世界上第一個能夠進行強力刮齒的臥式加工中心,加工中心采用嚴格的齒塑形工藝,即工件和工具按照持續接觸的方式,以接近完美的形式同步旋轉,并且保持精確定義的嚙合角。加上臥式配置能夠顯著減少設置工作量,據說這種刮齒工藝能在一次設置后加工出最完美的齒輪。
JTEKT Toyoda Americas公司和豐田汽車公司起源于同一家企業,在制造汽車部件的機械齒輪方面有著很深的根基。在GS系列強力刮齒HMC中,這些經驗體現在了一種控制裝置中,但裝置目前只能用于凸輪軸和曲軸研磨專用的機床。提到剛性HMC平臺和GC70數控加工機床的高速主軸同步功能的結合時,生產經理William Terry表示:“我們將一項經過證實的技術與另一項經過證實的技術組合起來。”
與墓碑式夾具或其他固定工具不同,GS系列HMC采用能夠在270°范圍內調整的工件夾緊主軸,確保刮削工具和工件之間形成合適的夾角。采用這種可調整主軸,還可以通過操作兩根主軸方便機床在40位置自動換刀裝置,包括端銑刀、鉆頭、開槽工具和進行對稱圓形車削的單點工具接觸到零件。這種機床配置加強了通常由10臺或更多專用設備組成的生產線,幫助制造商高精度確定關鍵零件的特性,無論是設備相互之間或相對于任何其他關鍵基準的特性數據。“我們至少可以切割五種大多數工藝無法切割的機床。”Terry說道。實際上,使用單個夾持裝置可以對齒輪進行撤銷、內部和外部刮齒、外圍研磨或鉆孔,甚至倒角和去毛刺工藝,而這些工藝可能需要專業設備才能完成。“這意味著層壓結構誤差為零,每種特性、每個尺寸、每個容差都是同心的。”
圖1 作為一項保持接觸的工藝,強力刮齒比齒輪塑形更為高效,兩者均是采用相似的多齒工具在切口內外振動進行加工。強力刮齒比滾齒更靈活,兩種工藝類似,但滾齒僅局限在外部齒輪的齒和單件刀具。相比之下,GS系列機床40種位置的ATC可以容納多個車齒刀、鉆頭、端銑刀和其他工具
從精度上講,測試證明機床能夠可靠地重復生產符合美國齒輪制造商協會(AGMA)Q11質量標準的齒輪。Terry表示,該標準并非強制規定,業內的用戶必須在質量和生產率之間自己找到平衡。“如果您要求每個零件都符合AGMA 14或15標準,不希望在粗加工工藝上浪費時間,可以直接將零件從機床上取下來,然后放到研磨機上。如果您對工具壽命和周期時間要求較高,可以將機床加工過的齒輪直接作為成品。”
無論用戶的要求如何,有效的刮齒都是從保證剛度開始。多齒工具和工件寬邊保持接觸可以產生“巨大的力”。即便實際情況不是這樣,兩個快速旋轉、相互配合的主軸也不會允許刮削工具的夾角和進料速率與規定值發生太大偏差。輕微的顫動就足以導致幾何形狀與規范不符。
“為了避免顫動,你要使用巖石或鐵對固定零件的所有裝置進行包覆固定。”Terry提到所有公司的HMC通用的鑄鐵結構時說。與它們所基于的FH-J模型類似,GS系列HMC也在主軸前后使用兩行陶瓷軸承,并在所有軸上使用大號滾子軸承。事實上,除了采用工件夾緊主軸和缺少托盤系統之外,GS系列機床與FH-J系列設備的最顯著區別在于玻璃分劃尺和高質量軸驅動。
同步兩個快速旋轉的主軸主要由GC70數控加工機床和機床的Toyopuc可編程邏輯控制器完成。“重點在于加工速度——在完全同步的環境下控制多個軸的能力。”Terry提到這些系統的組合時說,“我們在等待要去除的材料,而不是在等待能夠捕捉物理學特性的電子裝置。”
快速加工對于確保正確同步和在實現HMC刮削成本效益的速度下完成同步非常重要。對于零件,GS系列提供的工件旋轉速度達到3000?r/min,而工具旋轉速度達到6000?r/min。Terry強調,這一轉速足夠快,可以使用硬質合金工具,而非高速鋼。同時,設備具有靈活性,不僅能提升工作效率,還能選擇齒輪質量和生產速度的平衡。耐用的硬質合金工具在較低進料速率下進行切割會花費更多時間,加工出更為平整的表面。
數控加工機床還使用了專門針對(僅用于)刮削功能的會話編程接口。系統通過一系列的角度和幾何圖形問題提示用戶輸入足夠多的信息,從而準確確定任何花鍵或螺旋或直齒輪(斜面齒輪、準雙曲面齒輪和蝸輪需要其他加工方案)。HMC除了具備靈活性之外,還能避免購買專用軟件,讓控制自己齒輪制造的任何操作變得更加簡單。“機床適用于大規模生產,但也非常適合加工車間。”Terry說。
JTEKT Toyoda Americas公司和豐田汽車公司起源于同一家企業,在制造汽車部件的機械齒輪方面有著很深的根基。在GS系列強力刮齒HMC中,這些經驗體現在了一種控制裝置中,但裝置目前只能用于凸輪軸和曲軸研磨專用的機床。提到剛性HMC平臺和GC70數控加工機床的高速主軸同步功能的結合時,生產經理William Terry表示:“我們將一項經過證實的技術與另一項經過證實的技術組合起來。”
與墓碑式夾具或其他固定工具不同,GS系列HMC采用能夠在270°范圍內調整的工件夾緊主軸,確保刮削工具和工件之間形成合適的夾角。采用這種可調整主軸,還可以通過操作兩根主軸方便機床在40位置自動換刀裝置,包括端銑刀、鉆頭、開槽工具和進行對稱圓形車削的單點工具接觸到零件。這種機床配置加強了通常由10臺或更多專用設備組成的生產線,幫助制造商高精度確定關鍵零件的特性,無論是設備相互之間或相對于任何其他關鍵基準的特性數據。“我們至少可以切割五種大多數工藝無法切割的機床。”Terry說道。實際上,使用單個夾持裝置可以對齒輪進行撤銷、內部和外部刮齒、外圍研磨或鉆孔,甚至倒角和去毛刺工藝,而這些工藝可能需要專業設備才能完成。“這意味著層壓結構誤差為零,每種特性、每個尺寸、每個容差都是同心的。”
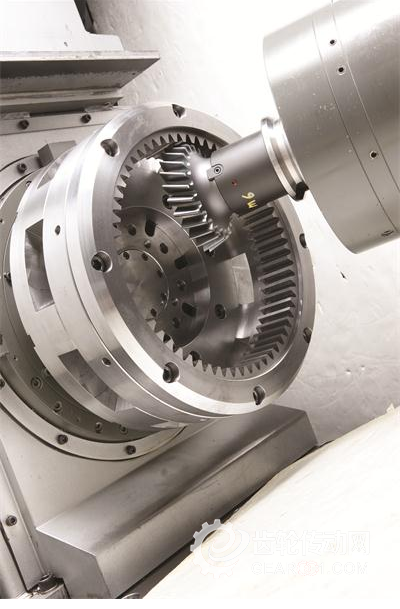
從精度上講,測試證明機床能夠可靠地重復生產符合美國齒輪制造商協會(AGMA)Q11質量標準的齒輪。Terry表示,該標準并非強制規定,業內的用戶必須在質量和生產率之間自己找到平衡。“如果您要求每個零件都符合AGMA 14或15標準,不希望在粗加工工藝上浪費時間,可以直接將零件從機床上取下來,然后放到研磨機上。如果您對工具壽命和周期時間要求較高,可以將機床加工過的齒輪直接作為成品。”
無論用戶的要求如何,有效的刮齒都是從保證剛度開始。多齒工具和工件寬邊保持接觸可以產生“巨大的力”。即便實際情況不是這樣,兩個快速旋轉、相互配合的主軸也不會允許刮削工具的夾角和進料速率與規定值發生太大偏差。輕微的顫動就足以導致幾何形狀與規范不符。
“為了避免顫動,你要使用巖石或鐵對固定零件的所有裝置進行包覆固定。”Terry提到所有公司的HMC通用的鑄鐵結構時說。與它們所基于的FH-J模型類似,GS系列HMC也在主軸前后使用兩行陶瓷軸承,并在所有軸上使用大號滾子軸承。事實上,除了采用工件夾緊主軸和缺少托盤系統之外,GS系列機床與FH-J系列設備的最顯著區別在于玻璃分劃尺和高質量軸驅動。
同步兩個快速旋轉的主軸主要由GC70數控加工機床和機床的Toyopuc可編程邏輯控制器完成。“重點在于加工速度——在完全同步的環境下控制多個軸的能力。”Terry提到這些系統的組合時說,“我們在等待要去除的材料,而不是在等待能夠捕捉物理學特性的電子裝置。”
快速加工對于確保正確同步和在實現HMC刮削成本效益的速度下完成同步非常重要。對于零件,GS系列提供的工件旋轉速度達到3000?r/min,而工具旋轉速度達到6000?r/min。Terry強調,這一轉速足夠快,可以使用硬質合金工具,而非高速鋼。同時,設備具有靈活性,不僅能提升工作效率,還能選擇齒輪質量和生產速度的平衡。耐用的硬質合金工具在較低進料速率下進行切割會花費更多時間,加工出更為平整的表面。
數控加工機床還使用了專門針對(僅用于)刮削功能的會話編程接口。系統通過一系列的角度和幾何圖形問題提示用戶輸入足夠多的信息,從而準確確定任何花鍵或螺旋或直齒輪(斜面齒輪、準雙曲面齒輪和蝸輪需要其他加工方案)。HMC除了具備靈活性之外,還能避免購買專用軟件,讓控制自己齒輪制造的任何操作變得更加簡單。“機床適用于大規模生產,但也非常適合加工車間。”Terry說。