近日,中國東方電氣集團有限公司自主研制的15兆瓦重型燃氣輪機(代號“G15”)在四川德陽下線。這是東方汽輪機繼50兆瓦重型燃氣輪機(代號“G50”)后又一成功下線的自主燃機系列產品,也是今年以來國產重型燃氣輪機研制傳來的又一個好消息。今年2月,我國自主研制的最大功率重型燃氣輪機——300兆瓦F級重型燃氣輪機首臺樣機完成總裝下線。
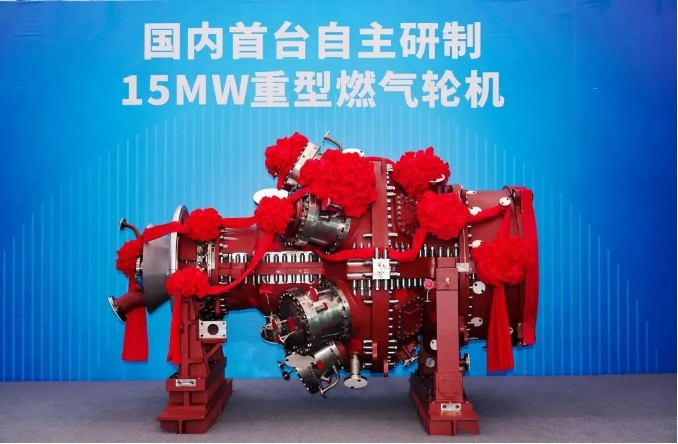
▲國內首臺自主研制15MW重型燃氣輪機(來源:東方汽輪機)
中國科學院高級工程師、工信部規劃司入庫評委、國家民航局適航司電傳飛控崗位專家翟冬青在接受中國工業報記者采訪時表示,50兆瓦燃氣輪機的誕生是一次跨越式的發展,是動力工業的重大突破。這意味著我國在火電機組汽輪機,航空發動機、船用燃氣輪機等動力技術都將同時上到新的臺階。同時,東方電氣作為與上海電氣、哈爾濱電氣并稱的“三大電氣公司”,取得這樣的成就十分不易。東方電氣地處在我國的西部四川德陽,對國家戰略工業實力的積累來說更具有意義,公司曾經在汶川地震時期遭受了重大損失,經過十幾年的拼搏攻堅下50兆瓦燃氣輪這個高地。“給他們掛勛章都不為過。” 翟冬青認為。
攻克裝備領域“皇冠上的明珠”
重型燃氣輪機是迄今為止效率最高的熱-功轉換類發電設備,是發電和驅動領域的核心設備,可在高溫、高應力、高腐蝕環境下長時間運行,廣泛應用于地面發電和電網調峰。據悉,重型燃氣輪機涉及多物理場耦合、多學科技術集成,設計、制造、材料、測試等技術挑戰極高,整機技術集成和系統性能匹配難度極大,體現了一個國家的工業水平,被譽為裝備制造業“皇冠上的明珠”。
資料顯示,我國從20世紀50年代末開始發展燃氣輪機技術,通過仿制和研制,到20世紀70年代初,國內廠家研制出了若干車用和發電用燃氣輪機,為我國燃氣輪機工業打下基礎。從20世紀80年代至20世紀末期間,受限于國內油氣供應短缺,燃氣、燃油發電行業進入低潮期,我國與國際燃氣輪機先進水平的差距被迅速拉大。
從2002年7月起,國家發展和改革委員會先后組織了3次F級和E級燃氣輪機的“打捆招標”工作。通過這種方式,我國燃氣輪機制造企業均引進了國外先進的燃氣輪機制造技術,獲得了包括制造圖紙、技術規范、工藝規范、材料規范、采購規范、質保體系以及裝配、調試、運行維護等技術資料。但在技術引進和轉讓過程中,燃氣輪機的設計技術、核心部件(燃燒器部件、高溫透平葉片部件)的制造和維修技術、試驗技術仍然掌握在外方手中,沒有進行技術轉讓。
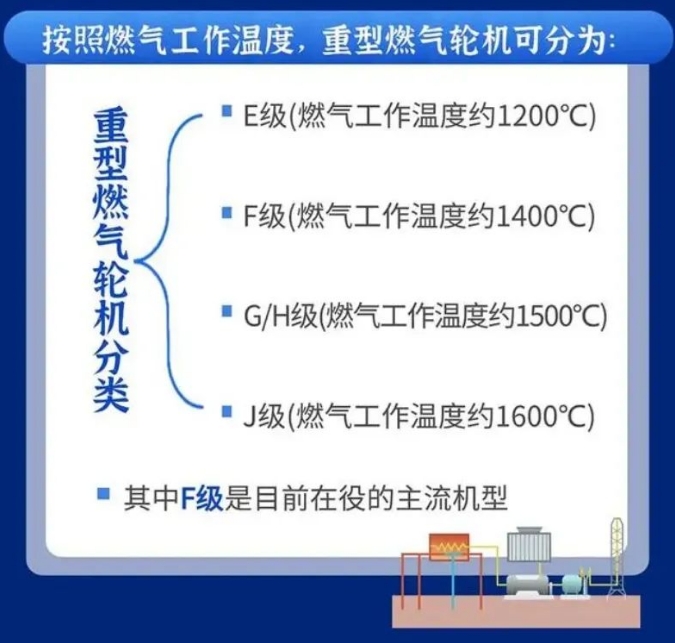
東方電氣集團作為中國能源裝備制造領域的“老字號”央企,長期致力于通過科技創新引領能源裝備產業發展。從1967年開始,東方汽輪機開啟自主研制燃氣輪機的步伐,至今已積淀近60年。其中,國內首臺全國產化F級50兆瓦重型燃氣輪機(簡稱“G50”)于2009年開始推動。具體來看:
2009年,東方電氣開始50兆瓦重型燃氣輪機自主研發。
2013年,完成總體結構設計。
2016年,建成國內首批壓氣機、燃燒器、透平部件級試驗臺。
2018年,壓氣機、燃燒器相繼研制成功,同年建成目前國內最大功率的燃氣輪機整機試驗臺。
2019年,整機透平葉片精密鑄造、加工完成,實現全部高溫部件的100%自主制造;整機點火試驗一次成功。
2020年,F級50兆瓦重型燃氣輪機首次運行至100%負荷。
2022年,實現滿負荷連續運行24+72小時,標志著該型號燃氣輪機完整地具備了商業化條件。
2022年11月25日,東方電氣完全自主知識產權F級50兆瓦重型燃氣輪機正式發運,打通了自主燃機從攻關走向應用的“最后一公里”,即將開啟中國自主燃氣輪機產業高質量發展的新篇章。
2023年3月8日,我國首臺全國產化F級50兆瓦重型燃氣輪機商業示范機組正式投入商業運行。
2024年3月16日,“G50”在中電德陽經開區分布式能源站投用,標志著商業化應用更加成熟。
經過15年奮戰,東方汽輪機自主燃機實現了從試驗臺平臺的建立到自主燃機關鍵技術的突破,從自主燃機關鍵部件的成型到包含高溫部件在內的完整燃機制造體系建立。據悉,下一步,東方汽輪機將在80兆瓦重型燃氣輪機、摻氫燃氣輪機、純氫燃氣輪機等方面持續發力。
從“1到N”還有幾步要走?
熱端部件是重型燃機研制實現國產化的關鍵和核心。一方面,熱端部件具有更高的經濟價值;另一方面,也面臨更大的“卡脖子”問題。據了解,在重型燃機的眾多零部件中,熱端部件僅占到10%左右,但其經濟價值占到30%-40%左右。
而要想真正實現國產替代,從“0到1”跨越到“1到N”,還有一段漫長的路需要走。
首先,市場對于新產品的嘗試往往比較謹慎。從國外廠商的重型燃氣輪機替換到國產重型燃氣輪機,發電廠商要承擔不小的風險。為此,近年來,一個個示范項目正在全國各地鋪開,其運行效果也逐漸得到市場的認可。據悉,近日,國內首批商業化G50燃機訂單——濟南熱電華山聯合循環項目正式簽約。“正是因為有示范項目在正常運行,我們才有信心。”濟南熱電集團有限公司副總經理阮磊表示,與國外廠商的燃機相比,國產燃機在價格、應急響應、售后服務等方面更具有優勢。
此外,翟冬青介紹,實際上,火電機組的汽輪機、航空發動機、船用燃氣輪機這三種動力系統的核心燃燒室是一樣的,被稱為“核心機”。
什么是“核心機”?資料上顯示,為縮短新機研制周期、提高可靠性或發展各種類型的燃氣渦輪發動機而研制的由壓氣機、燃燒室和渦輪組成的發動機核心部件,稱之為“(燃機動力)核心機”。
翟冬青說,核心機需要在1000-2000度的高溫下持續高速旋轉,保持金屬材料的高可靠、不變形,這項技術是國家戰略性技術,和芯片的重要性一樣,而50兆瓦燃氣輪機技術的突破,也證明了我國在“核心機”這項核心技術上也取得了重大的突破。
翟冬青認為,雖然在長達幾十年的努力下,我國動力技術沒有耽誤發展進程,但直至今日仍然沒有獨立的動力行業,即專門研發“(燃機動力)核心機”的企業。目前,航空發動機是中國航發、中國商發等集團在研發,東方電氣、上海電氣、哈電氣、杭州汽輪機廠研發船用動力燃機和火電機組的汽輪機。但所有燃機動力最終的技術核心在“核心機”這個領域。因此,翟冬青建議,“核心機”領域需要專門開設出一個“動力行業”進行技術攻堅。只要這個“動力行業”領域取得更快的突破,動力涉及的航空、船舶、軍工等行業的動力系統都將會發展得的更快。展望未來,有一天70兆瓦或100兆瓦的燃氣輪機中國都會取得突破,這個臺階一旦上去就會走在全世界前面。