在西安法士特高智新公司,看不到工業企業“粗、大、笨、重”的傳統印記。目及之處,機器與機器之間有條不紊地交流信息、配合默契地協同作業,伴隨一條條跳動的程序指令,智能化無人生產一氣呵成:“躺”在設計圖紙上的齒輪、軸、殼體等零部件從飛濺的切削液和金屬屑里誕生,它們被組裝成一臺臺重卡變速器,走向全球市場。
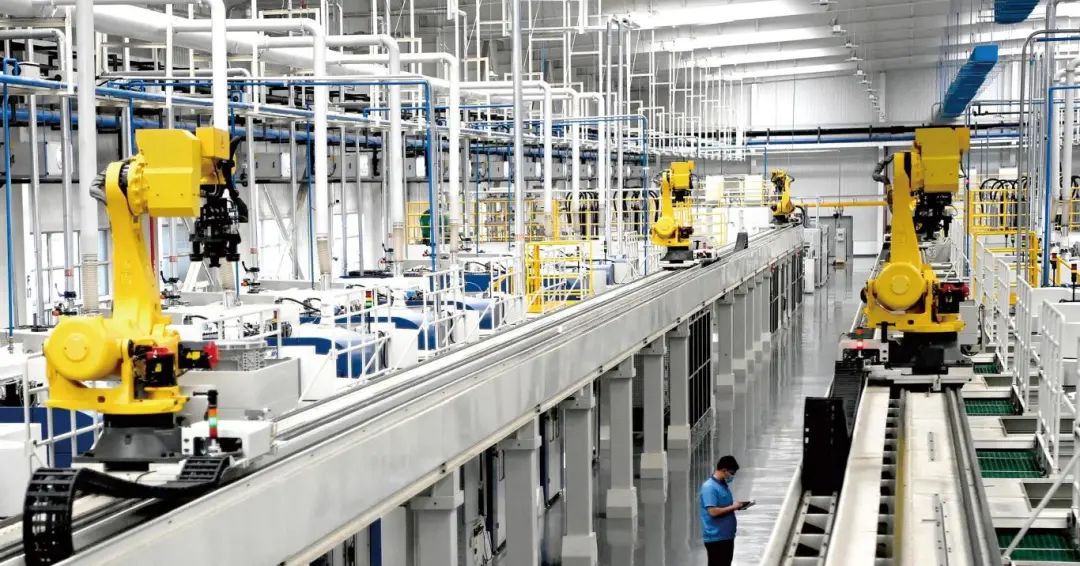
法士特西安高智新公司變速器零件數字化生產線 新華社/供圖
“在5G、工業互聯網等新技術加持下,我們的關鍵設備100%實現了身份識別和數字化管理,從毛坯上料、零部件加工到搬運均無人作業,全天候、全時段、全流程自動化生產,可以實現連續6小時無人‘黑燈生產’。”在法士特高智新公司總經理趙建林看來,“黑燈工廠”的內涵遠不止字面上這么簡單,不僅喻示著高度智能化的作業方式,更是一種顛覆傳統生產管理模式的系統性創新。
身負“老軍工、老國企、老三線”標簽的法士特,前身是陜西汽車齒輪總廠。如今,在數實融合的浪潮中,法士特“智造”的齒輪正加速轉動:生產效率提高72%、能源消耗降低14%、產品交付周期縮短20%,高智新工廠入選國家首批“數字領航”企業名單。2023年,法士特銷售變速器等各類總成產品83.8萬臺,同比增長42%,重型汽車變速器年產銷量連續18年穩居世界第一。
“高智新”工廠的誕生
“如果說工業機器人是手,AGV小車是腿,自動化立體倉庫、運輸軌道是血管,那么智慧管理系統就是工廠的數字心臟和大腦,能夠自主識別、判斷、控制、指揮整座工廠全流程調度。”談及智慧工廠,趙建林打了一個形象的比喻,“5G實現了所有部位的全連接,它們各司其職,卻又實時交流信息、相互協作。
”機器與機器高效“對話”,完成自檢、修復甚至追溯等工作。這背后,站著一個200余人的研發團隊,以及他們自主研究,在核心工藝、技術、算法等方面形成的289項專利、標準和軟件著作權。
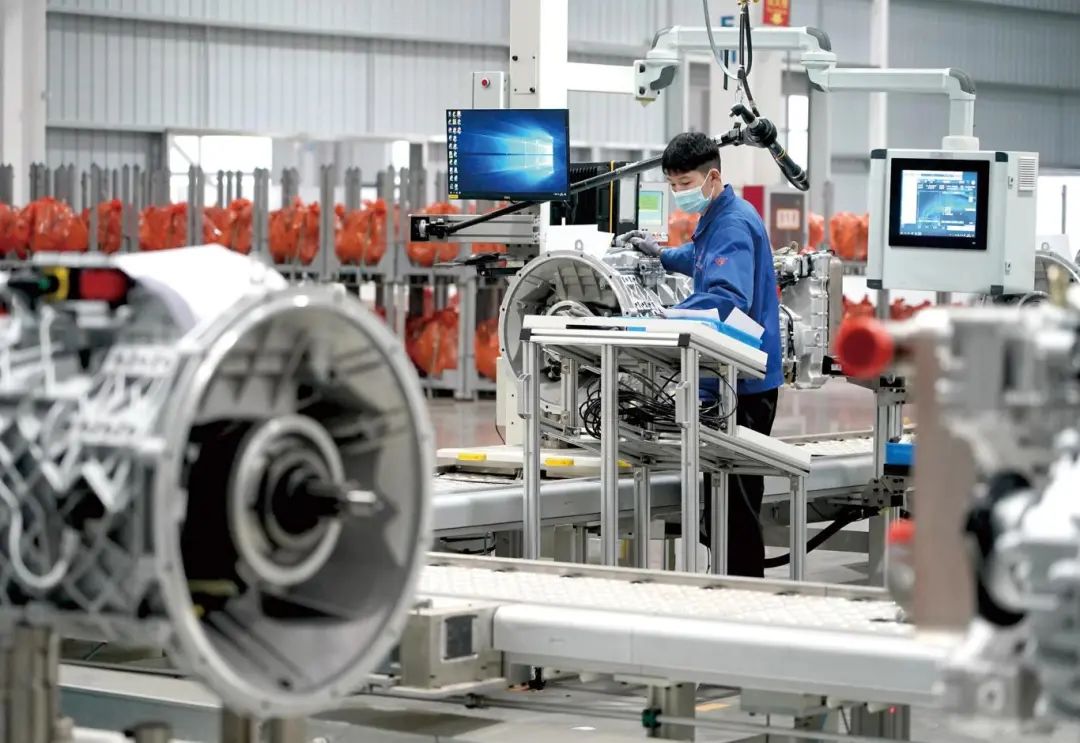
工人在法士特高智新工廠項目車間內檢測變速器成品 新華社/供圖
2021年,裝配工藝工程師于明加入建廠的“先遣部隊”——在實際工廠落成之前,他們負責搭建出一個模擬工廠。
“整體設備部署、連接,甚至生產線布局,都是從零做起。”于明坦言,這是一個“燒腦”的過程,僅裝配線技術協議和車間平面布局圖,就各自修訂了百余版。
“我們大量應用建模仿真和數字孿生等工業4.0關鍵核心技術,在虛擬空間模擬工廠實際生產活動,完成機加、物流、裝配等生產環節的節拍驗證和虛擬調試。”于明說,借助AR等技術手段打開生產過程“黑盒子”,整個工廠生產制造環節變得透明:哪些程序出錯了,哪些流程還可以改進,哪些環節潛伏著新的潛力和商機,都一目了然。
產品質量穩定性、生產連續性和加工過程安全性,這些是“黑燈工廠”順利運行的關鍵。為保證在2022年順利投產,“先遣部隊”準備了將近一年時間。
“每道工序,都要比對各項參數反復試驗,將技術經驗轉化成標準數據,輸入系統智能終端,還要與設備廠家一起調試機械系統,確保各項參數符合生產標準。關于零部件的抓取點位、機械臂的動作軌跡、AGV小車和產線的交互,我們進行了上千次調試。”跟于明一樣,技術總監王朝清也見證了高智新工廠的誕生。
毛坯上料,機器人通過工業相機識別位置,機械臂接收信號后抓取,抓取誤差需控制在0.2毫米以內,工業相機如何根據光線的強弱自動調整曝光度,機械臂的動作軌跡是直線還是曲線,怎樣實現“手眼協調”?一條生產線700余把刀具,刀具磨損需要人工換刀,如何“預知”刀具使用壽命,并根據生產任務和刀具狀態,智能分配調度刀具資源,拉長“黑燈”時間?
“沒有捷徑,只能反復調試論證。”王朝清說,這是一個“笨辦法”,好在,經過不斷優化,每天的產能從最開始200臺份,提高到300臺份,到現在達產400臺份,“黑燈”時間可延長到6個小時。
一臺變速箱由300多種物料組裝而成,AGV小車負責這些物料的精準配送。“根據目前的產線節拍,每75秒下一個齒輪,150秒下一個殼體,下線軌道長度有限,不及時拉走就會憋停產線,不能讓零件等車,所以需要合理規劃58輛AGV小車的行駛路線,通過程序指令讓它們第一時間就位。”王朝清將這一過程比喻為“打車”。
“AGV小車的容量為兩垛,但原先的調度系統只能拉一垛,我們優化了半年,終于找到最優路線,實現了‘拼車’。”王朝清告訴記者,一輛AGV小車平均每天跑20公里,全部小車加起來1000多公里,相當于北京到上海的直線距離。
一點點打通堵點、一次次技術攻關、一步步優化工藝,“黑燈工廠”全面投產后實現年產自動變速器20萬臺,產值62億元。
“1個人干以前5個人的活”
機器“當家”,少人化,乃至無人化,是“黑燈工廠”最為直觀的一個變化。
3.3萬平方米的機加車間內,12名工人分散在23條生產線上,“操控”著123臺工業機器人、207臺數控機床以及58輛AGV小車。“1個人能干以前5個人的活。”機加車間生產計調員常恒臣介紹,高智新公司人均產值提升了5.2倍,從接到訂單到成品交付,比傳統工廠快4天。
常恒臣每天上班第一件事,制定當天的生產計劃。他說,以前人工排產,生產計劃人員要先去倉庫查看物料,再到車間了解實際生產情況,需要人工收集、整理和分析大量數據,很多時候都是憑經驗,效率低不說,還很容易出錯。
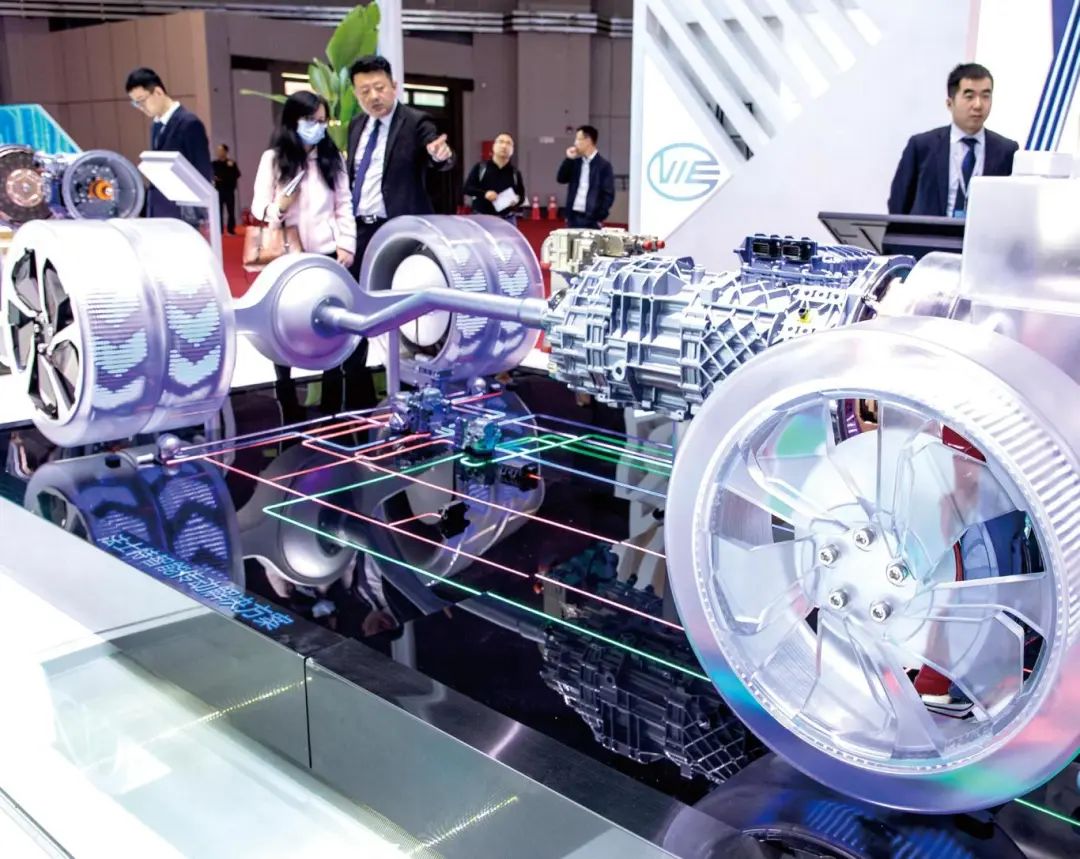
上海車展,法士特展示的智能傳動解決方案。
如今,常恒臣依托生產操作、倉儲管理等十幾個智慧平臺開展智能排產,只需根據集團制造總部的裝配裝箱需求輸入指令,系統會基于車間產能、生產負荷自動生成排產計劃,明確每條產線生產的零件品種、數量,成品入庫時間,物料補充計劃,高效且清晰。
智能化產線操作工成勇干過12年磨齒工,曾一個人管2臺機床,每天困在方寸之地重復作業。現在,他的“管轄領域”擴大到整條生產線,除去產線上的9臺數控機床、15塊顯示屏,還要兼顧機器人、電柜、AGV小車交互信號等。此外,徒弟馮樂那條產線也要他“坐鎮”。
“雖然工作量大了,活卻輕省不少。”成勇說,傳統工廠的工人除了管機床,還有很多搬搬扛扛的體力活,給機床加注機油、清理加工廢渣廢屑、搬運物料,又臟又累。
“黑燈工廠”的每臺機床都連著集中供液、供油裝置,霧化的油液集中回收,削磨的金屬廢屑直接壓制成金屬塊,回爐再利用。車間干凈明亮,聽不見機器轟鳴的噪音,聞不到機油揮發的刺鼻氣味,也沒有金屬零件刨銑削切后的廢渣,工人們徹底告別了往日粉塵彌漫的作業環境。
智能生產線改變了以往生產工序“一個蘿卜一個坑”的崗位劃分,原來分布在生產線上不同位置的多個工種被集中到一個崗位上,對工人技能水平的要求自然更高。
成勇日常負責監控產線運行,密切關注顯示屏、設備狀態指示燈,隨時排除產線異常,基本都是腦力活。這不僅要求他懂技術,還得熟悉工業機器人的“秉性”,了解信息化系統和自動化產線。
“智能化工作場景拓展了我們的思路,不斷適應、學習的過程,提升了我們創新創效的能力。”轉崗后,成勇反復實操練習智能化操作流程,從頭學習機器人編程、產線改造,個人成長按下“加速鍵”。
“經過精確的效率、成本控制,我們把高強度體力勞動、危險勞動、重復性勞動等低附加值勞動全部交給機器,最終實現合理的人機協作,人歇、設備不歇。”趙建林表示,“機器換人”后,缺的還是人,是能夠調試、操作、維修、保養設備的高技能復合型產業工人,他們將成為法士特換擋超車的“變速器”。
“模范生”領跑新賽道
2023年5月,陜西發布25個數字經濟典型示范案例。作為領域內數字化轉型升級的先行先試者,法士特“商用車傳動系統制造智慧工廠”名列其中。這是陜西在全省范圍內的首次評選,上榜的企業皆為行業翹楚。
事實上,法士特此前十幾年一直在智能制造領域深耕。“從自動化單元到自動化產線,再到智能車間、‘黑燈工廠’,這是一個循序漸進的過程。”陜西法士特汽車傳動集團公司副總經理寇植達認為,在數字經濟大潮中,數字化轉型已不是企業的“選修課”,而是關乎企業生存和長遠發展的“必修課”。
生產端改造傳統流水線生產邏輯,極大解放生產力的同時,法士特“黑燈工廠”也顛覆了以往的管理模式——沒有廠長、車間主任、班組長,“一竿子”插到底,縱向打通層級阻隔;傳統制造中的管理、命令和審批全部實現數字化智能化,全員通過數據來驅動,進行自我管理,橫向打破行政壁壘。
“表面上,‘黑燈工廠’只是一個單純的技術攻關項目,實際是一個復雜的系統工程,數字化轉型的成功落地不能僅僅依靠技術層面的突破,更需要一次從戰略、組織貫穿到企業經營各環節的管理變革。”寇植達舉例,以往的管理對象主要是“人”或者現實物理設備,現在重點關注生產數據指標。
在他看來,依托數字化,帶來的變化不止于企業內部,在貫通企業內部數據的同時,更可聯通產業上下游兩端,有力提升產業鏈數字化協同水平。“數字化轉型對企業智能制造團隊和市場服務提出更高的要求,需要充分開放合作,構建社會化的服務協作生態。
”在法士特“黑燈工廠”,80%的齒輪生產設備來自秦川機床。法士特是陜西重卡產業鏈“鏈主”,而處于產業鏈上游的秦川機床則是數控機床產業鏈“鏈主”。
肩負“鏈主”職責,法士特在苦練內功之余,勤修外功,領跑數字經濟新賽道。
2023年7月,陜西法士特集團科技創新有限責任公司入駐秦創原,主營業務覆蓋三大方向,分別是智能制造、智能駕駛、汽車電子,深度關聯法士特的核心業務。新平臺手握“黑燈工廠”核心技術,將目光投向法士特數百家上下游相關配套企業,借勢秦創原創新驅動平臺輸出智能制造成功經驗,融合創新、聯合孵化,帶動全產業鏈協同發展。
“我國的制造業已經從組織數字化、業務數字化的階段,邁入企業大協同、產業鏈數字化的新階段。數字化轉型,絕非只是龍頭企業或者頭部企業的數字化,而是連點成線,是產業鏈上上下下、大中小微企業一同參與、共同成長的數字化。”寇植達說。