尼得科株式會社的集團公司尼得科機床株式會社(以下簡稱 “本公司”)開發出量產用內齒輪拋光(研磨)工藝,用于高精度精加工汽車驅動裝置和變速箱,機器人關節中使用的行星齒輪機構等的內齒輪。雖然用于高精度精加工外齒輪的批量生產拋光方法已經確定,但用于內齒輪的加工方法還未確定,現在的研究集中在這一點上,并取得了適用于精密和批量生產的良好成果,這是傳統的磨削、珩磨和車齒加工所無法實現的。
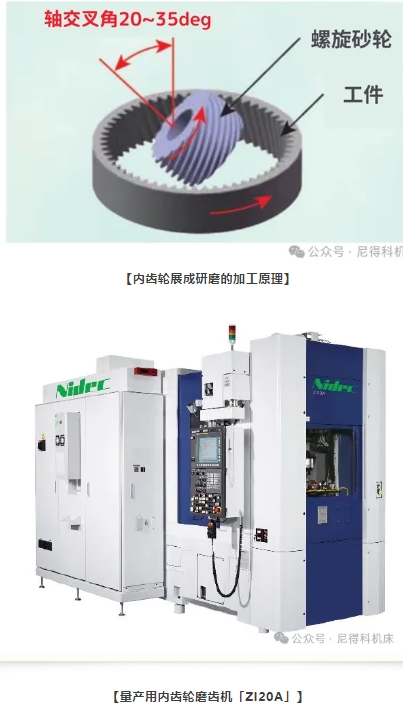
行星齒輪機構具有高效率、高承載能力和結構緊湊等優點,但齒輪的細微變形都會影響齒輪的耐用性和傳動效率,并產生噪音和振動,因此對齒輪的品質要求很高。隨著電動化和自動化的發展,對高精度齒輪的需求進一步增加,而本加工方法的早日實現和市場投入將有助于提高齒輪的耐用性、 傳動效率和 NVH(噪聲Noise、振動Vibration和粗糙度Harshness)性能。
在本次研發工作中,根據本公司的加工機和加工技術,確定并得出了特定的加工條件。這也是與德國亞琛工業大學聯合研究的部分成果。更多信息,請參閱所附論文。
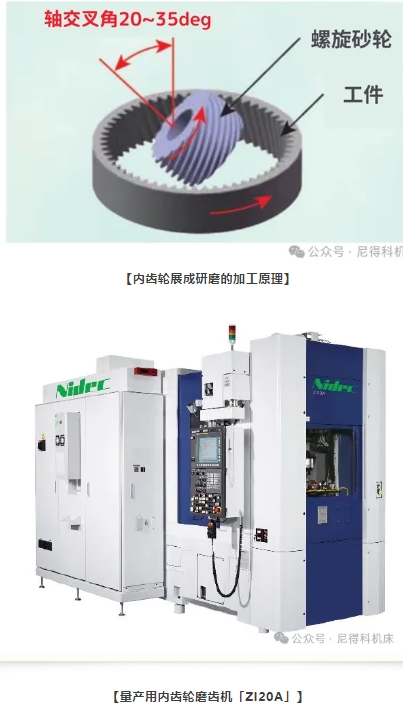
加工機:本公司于 2009 年開售的量產用內齒輪磨齒機( ZI20A),可應對內齒輪的量產需求,對內齒輪進行高精度加工。
砂輪的選擇:事先對作為消耗品的砂輪的可獲取性、經濟性和自動運轉的適用性進行評估。
確定加工條件:以表面粗糙度 Ra 0.1 µm 和 Rz 1.0 µm 以下為目標(這是拋光的常用指標),并在磨削后保持 ISO 3-5 級齒輪精度的同時,推導出不會導致磨削燒傷的高效加工條件。
尼得科機床采用世界一流的齒輪加工技術,提供機床、刀具和加工解決方案,為解決社會課題做出貢獻。