KX 300 P 齒輪加工中心的成功案例不勝枚舉,已售出的 500 多臺機器證實了兼具高靈活性和高生產率的成功理念。新推出的 KNG 350 系列將繼續沿襲這一理念。在開發這個新機床平臺的過程中,我們敢于回顧過去,采用經過驗證的解決方案并對其進行進一步優化,同時還徹底消除了現有的不足之處。
由此形成了一個復雜的模塊化系統,能夠在一個基礎上呈現不同的機床設計概念。通過三種不同的刀具和工件驅動器配置,可以最大程度地滿足客戶的要求。
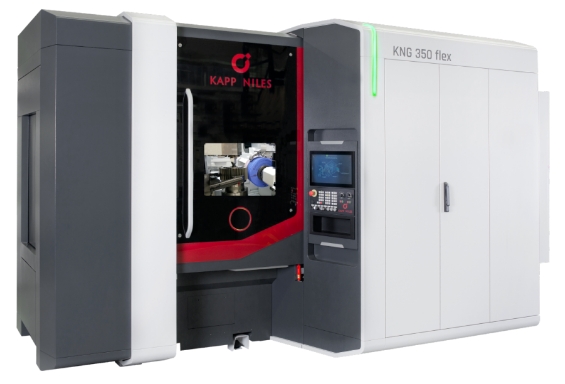
圖 1:齒輪加工中心 KNG 350 Flex
機床設計
KNG 350 系列基于緊湊、優化的機床設計理念,適用于小批量到大批量生產直徑不超過 400 毫米的齒形工件。集成的環形上下料裝置可確保最短(最多 5 秒)的非生產時間,既可加工內孔工件,也可加工長度達600 mm 的軸形工件。
從手動上下料,到簡單的料盤傳送帶,再到復雜的機械手解決方案,該設計為工件上下料提供了充分的靈活性。
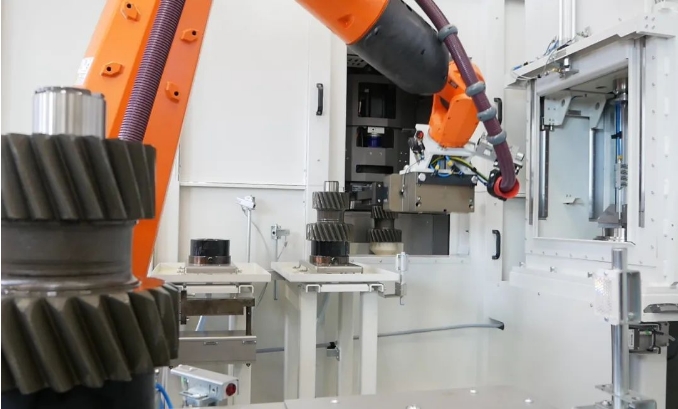
圖 2:靈活的機械手上下料
功能全面且符合人體工程學的機床設計與易于使用的 KN grind 操作界面相結合,為磨削項目的設置和優化提供了支持。減少非生產時間也受到高度重視。因此該系列的特點是換型時間短,這主要是通過智能組件(智能工裝)來實現的。加工過程監控、工件追溯和在線質量保證是符合工業 4.0 標準的加工設備不可或缺的組成部分。
這臺機床不僅因其出色的設計(iF 產品設計獎)而令人印象深刻,而且在節能方面也在不斷進步。液壓功能被減少到最低限度,由一個可控泵裝置覆蓋,氣動功能在很大程度上被電力驅動器所取代。此外,如果考慮到機床的整個生命周期,將床身從鑄鐵改為聚合物混凝土后,機床的總二氧化碳當量也有所降低。這些方面正變得越來越重要,尤其是對原始設備制造商而言。
長期合作伙伴Scania斯堪尼亞公司(位于瑞典斯德哥爾摩省的南泰利耶市)的評估就是一個很好的例子。負責保養的 Anders Urefors 從KX 300 P機床開始就一直關注著它的技術發展。在機床的技術驗收階段,也就是第一次接觸到 KNG 350 的過程中,臉上露出了滿意的神情。過去應客戶要求單獨實現的功能,如高度可調的控制面板,現在已成為標準配置。現在,即使打開操作門,也能更接近工件軸和刀具軸。連同工件特定刀具的快速更換系統,為機床換型設定了新的標準。顯而易見,在開發這款機床時,人體工程學和實用性是其規范中的重中之重。
“Lessons learned”(吸取了教訓),是這位向來謹慎的瑞典人的評論,同時伴隨著輕松的笑容。
沒有比這更值得稱贊的了,所有參與項目的人都很清楚,如果 Anders 滿意,那么 SCANIA 斯堪尼亞公司也會感到滿意!
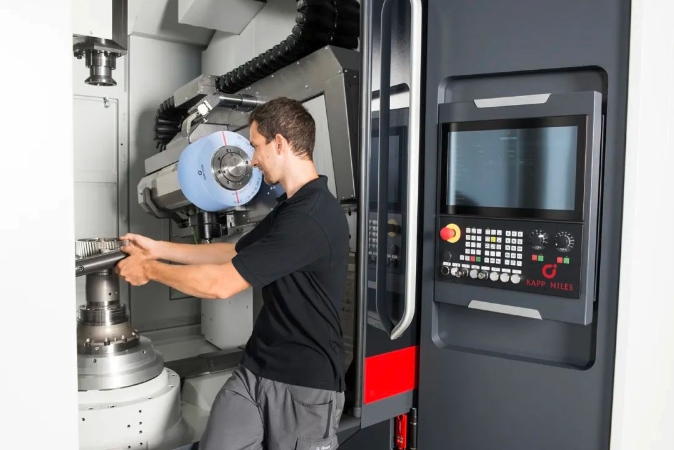
圖 3:最佳的可操作性
KNG 350 expert
新系列的開端是專門用于展成磨削齒輪的 expert(專家)機床。不帶反向支座的磨削主軸設計已經在 DYNAMIC 機床上得到了驗證。自動 HSK接口可實現半自動更換刀具,除了 expert 機型之外,該系列的其他機型也同樣采用了這一技術。
這類機床配備了功能強大的技術選項,例如齒輪的抗扭曲磨削,或通過使用組合磨削蝸桿來滿足更高的表面要求。通過選擇修整工藝,可以經濟地滿足從單件生產(拓撲修整)到批量生產(多槽修整)的所有要求。該系列的所有機床都可配備集成測量裝置,可在機床內進行完整全面的齒輪測量,也可以針對可定義的齒輪特性進行周期性測量。
KNG 350 flex HS
電動汽車給齒輪加工行業帶來了新的挑戰。乘用車領域緊湊安裝空間內的高功率密度以及精密自行車驅動裝置的微型化,往往會導致不利于加工生產的工件幾何形狀。
迄今為止,帶有干擾輪廓齒輪的硬精加工主要是通過不連續的成形磨削或齒輪珩磨來實現的。原因很簡單:對于有干擾輪廓的工件來說,直徑為 300 mm 的普通蝸桿砂輪太大了。
但是與連續展成磨削相比,成形磨削和齒輪珩磨在生產率、經濟效益或質量穩定性方面都存在不同的缺點。然而,只有通過更高的轉速才能實現更小的磨削蝸桿,以便使用更小的刀具直徑實現更高的切削速度。以往的機床設計理念無法滿足刀具驅動和工件驅動的高動態要求。
KNG 350 flex HS 的特點是:即使采用如此小的刀具,也能獲得最高的磨削質量和生產率。由于配備了 25,000 轉/分鐘的高速磨削主軸,可以用直徑55 毫米以上(展成磨削)或 20 毫米以上(成形磨削)的刀具磨削加工帶有干擾輪廓的齒輪。
KNG 350 flex
還能再來一些嗎?
當一個機床生廠商提出這個問題時,肯定與香腸無關。
目前齒輪的直徑范圍正在不斷擴大,特別是在電動商用車輛中。過去傳統卡車的變速箱傳動齒輪直徑約為 300毫米,而現在的工件直徑有時會達到 350 毫米,在個別情況下甚至會達到 400 毫米。機床 KNG 350 flex 通過直徑擴展選項,可以滿足這個范圍的要求。
性能經過優化且帶有反向支座的磨削主軸,專為寬度不超過 200 mm 的大型蝸桿砂輪而設計,切削速度高達 100 m/s。這樣就能實現大模數工件的高效加工,并使用組合蝸桿進行超精磨或拋光磨。
采用標準刀具,在連續展成磨削時可以穩定達到平均粗糙度 Rz = 2.5~3 µm 的表面質量。對于更高的要求,可以采用具有兩個不同區域(一個區域具有標準粒度,另一個區域用于超精磨或拋光磨,具體取決于表面要求)的組合刀具。這也使得 Rz < 1 µm的粗糙度得以實現。因此顯著提高了齒面接觸比率,從而提升齒輪的最大承載能力。這種加工方法的另外一個優點是:它可以集成到“單件流”的自動化工藝鏈中,這在迄今為止常用的光滑打磨工藝中,是無法實現的。Kapp Niles 還有一個獨特之處,將拋光磨作為一項單獨的技術提供,例如在噴丸后才對齒輪進行拋光加工。
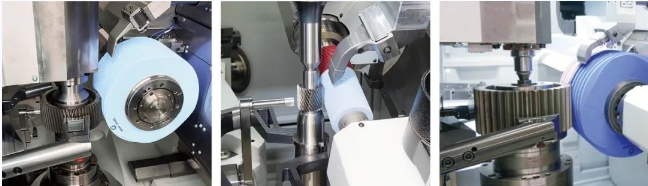
圖 4:KNG 350 系列的不同刀具軸
另外還有兩個亮點凸顯了這款機床的靈活性。
通過磨削輔助軸,使用非常小的成形磨砂輪,最小的齒根圓都可以加工。即使砂輪直徑為 30毫米,集成的速比級也能實現高達 50 m/s 的切削速度。采用內齒磨削裝置,可以加工漸開線內齒齒輪,也可以加工特殊齒形。磨削輔助軸和內磨臂都可以通過新的快速更換接口,直接在刀具主軸上迅速進行安裝。
根據具體應用,使用免修整刀具或可修整刀具,既可以采用展成磨削也可以采用成形磨削來加工小工件和大工件的外齒和內齒。
這種類型的機床是名副其實的“flex”(靈活),在磨削齒輪方面無可挑剔。
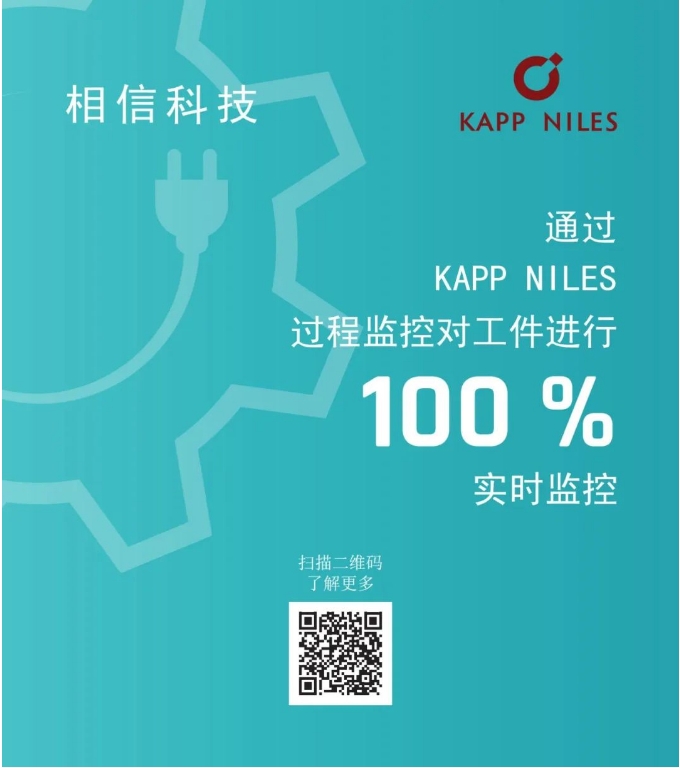
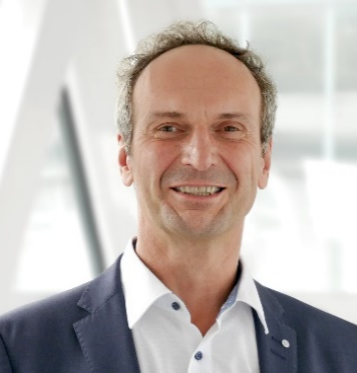
Ralf Dremel
Kapp Niles 技術性產品負責人