一直以來,航空發動機始終是我國飛機制造業的短板。為此,我國于2016年成立中國航空發動機集團,舉全國之力攻克此項難題。作為航空發動機的核心零件-葉片,對發動機的性能起著至關重要的作用,隨著航空發動機性能的要求越來越苛刻,對于葉片的要求也越來越高,目前幾乎所有的葉片都要求100%全檢,對于每個葉片幾乎都是全型面檢測,這樣就給葉片的檢測精度和檢測效率提出了更高的要求。
某型葉片的基本特征:
該型葉片共計需要測量11個檔位,其中中間檔位的出氣邊(Trailing Edge)R僅為0.13mm,角向定位面的寬度僅為2.5mm。
通常客戶采用三坐標接觸式掃描測頭(SP25)測量。由于角向定位面很小,客戶一般要借助輔助夾具來實現角向的定位。此種測法有諸多弊端:
a) 測量效率低(掃描速度約為10MM/S);
b) 掃描截面時存在余弦誤差(cosine error);
c) 角向定位誤差大;
d) 另外,由于掃描測頭只有在恒定速率下,測量值才穩定,所以在測頭加速和減速時數值需要剔除掉,為此測頭必須提前開始掃描曲線,結束時也需要多掃一段,以便保證測量型面時的速度是恒定不變的,但同時也增加了無謂的測量時間。
測量完此類葉片(含裝夾,建基準,出報告)單片大約需要15分鐘。
為此我們為客戶提供了非接觸式白光測量解決方案(CORE-DS)
Ø 首先測量效率高:掃描速度高達100mm/s以該型葉片為例,白光測量僅需6分40秒(含裝夾,建基準,出報告)。
Ø 測頭校正時間短,測頭一次校正,所有的角度都可以使用。
Ø 不存在掃描測頭加速和減速時的不穩定性
Ø 沒有余弦誤差,光點直徑僅為35um,直接測得截面實際值,不存在測球半徑補償。
余弦誤差示意圖:接觸式接觸的是圖中的7點,測頭補償(4)后得到實測點3和4的交點,而白光直接測得就是圖示6點。所以不存在3余弦誤差(cosine error)
Ø 無需輔助定位夾具,所有基準元素均為直接測量,提高了坐標系的精度。
Ø 六點預定位,使掃描更加準確。在掃描葉型前,會預先在葉盆,葉背,前尾圓采6點,然后根據實際的葉型狀況,來調整葉型的掃描路徑(平移、旋轉,甚至縮緊或者擴張)。
Ø 自動根據曲率變化來分布控制點的疏密。(前尾圓加密,盆背稀疏)
Ø 多種類型的報告可供客戶選擇
另外,客戶根據自己的實際需求定制自己喜歡的報告樣式。
Ø 一鍵式測量界面
OPEN_DMIS的Xecute 界面模式是我們專門為操作者而開發的。用戶只需點擊對應被測零件的圖標,程序即可自動運行,全程看不到程序代碼,保障了程序的安全和測量的高效。
為了進一步提高客戶運行程序的效率,我們將輸入工件名稱,爐號,工件號這些在程序運行中必須輸入的信息移動到了運行程序外面,客戶可以把下一片即將測量的號碼預先寫入到一個TXT內,程序運行時自動調取。節省了機器的等待時間,此項為客戶節省約10S。
為客戶盡可能節省時間,提高效率,是我們不斷追求的目標……
某型葉片的基本特征:
該型葉片共計需要測量11個檔位,其中中間檔位的出氣邊(Trailing Edge)R僅為0.13mm,角向定位面的寬度僅為2.5mm。
通常客戶采用三坐標接觸式掃描測頭(SP25)測量。由于角向定位面很小,客戶一般要借助輔助夾具來實現角向的定位。此種測法有諸多弊端:
a) 測量效率低(掃描速度約為10MM/S);
b) 掃描截面時存在余弦誤差(cosine error);
c) 角向定位誤差大;
d) 另外,由于掃描測頭只有在恒定速率下,測量值才穩定,所以在測頭加速和減速時數值需要剔除掉,為此測頭必須提前開始掃描曲線,結束時也需要多掃一段,以便保證測量型面時的速度是恒定不變的,但同時也增加了無謂的測量時間。
測量完此類葉片(含裝夾,建基準,出報告)單片大約需要15分鐘。
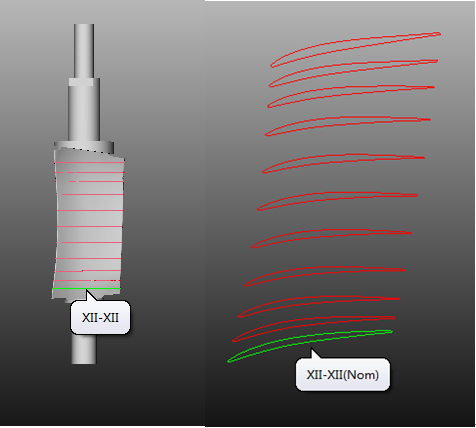
為此我們為客戶提供了非接觸式白光測量解決方案(CORE-DS)
Ø 首先測量效率高:掃描速度高達100mm/s以該型葉片為例,白光測量僅需6分40秒(含裝夾,建基準,出報告)。
Ø 測頭校正時間短,測頭一次校正,所有的角度都可以使用。
Ø 不存在掃描測頭加速和減速時的不穩定性
Ø 沒有余弦誤差,光點直徑僅為35um,直接測得截面實際值,不存在測球半徑補償。
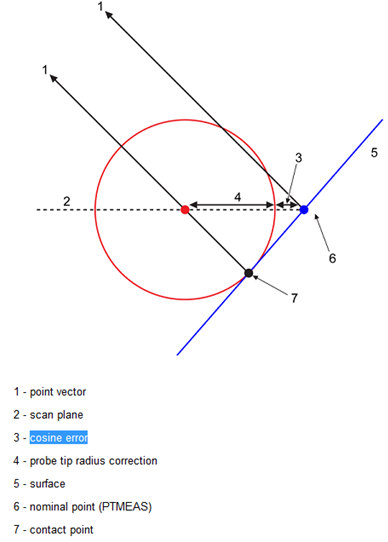
余弦誤差示意圖:接觸式接觸的是圖中的7點,測頭補償(4)后得到實測點3和4的交點,而白光直接測得就是圖示6點。所以不存在3余弦誤差(cosine error)
Ø 無需輔助定位夾具,所有基準元素均為直接測量,提高了坐標系的精度。
Ø 六點預定位,使掃描更加準確。在掃描葉型前,會預先在葉盆,葉背,前尾圓采6點,然后根據實際的葉型狀況,來調整葉型的掃描路徑(平移、旋轉,甚至縮緊或者擴張)。
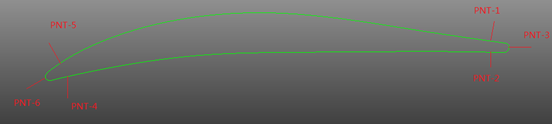
Ø 自動根據曲率變化來分布控制點的疏密。(前尾圓加密,盆背稀疏)
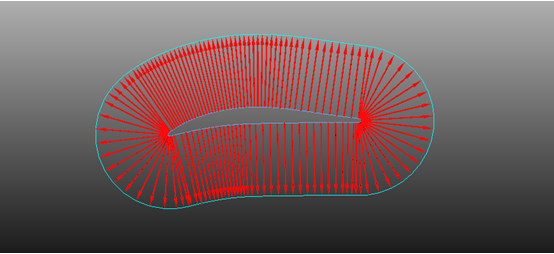
Ø 多種類型的報告可供客戶選擇
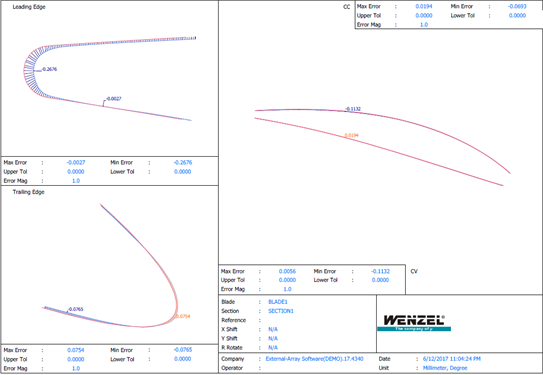
另外,客戶根據自己的實際需求定制自己喜歡的報告樣式。
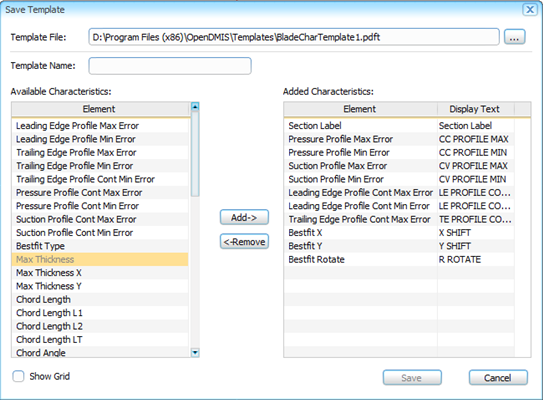
Ø 一鍵式測量界面
OPEN_DMIS的Xecute 界面模式是我們專門為操作者而開發的。用戶只需點擊對應被測零件的圖標,程序即可自動運行,全程看不到程序代碼,保障了程序的安全和測量的高效。
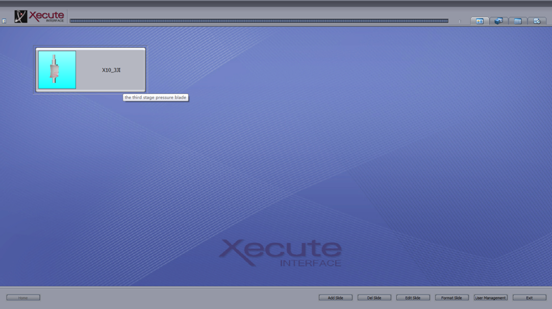
為了進一步提高客戶運行程序的效率,我們將輸入工件名稱,爐號,工件號這些在程序運行中必須輸入的信息移動到了運行程序外面,客戶可以把下一片即將測量的號碼預先寫入到一個TXT內,程序運行時自動調取。節省了機器的等待時間,此項為客戶節省約10S。
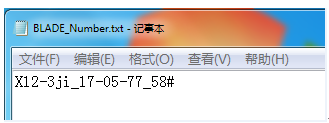
為客戶盡可能節省時間,提高效率,是我們不斷追求的目標……