2019 年 4 月 23 日,格平根 - 對更高能源效率的需求以及對新能源汽車的不斷探索是該行業的主要創新驅動力。舒勒為電動汽車電機與電池殼體的制造提供多種解決方案。近期,舒勒系統業務部在德國格平根總部展示了最新研發的用于自扣電動機鐵芯生產的高速沖Smartlin EV3.8,同時舒勒在中國大連的工廠也生產該設備,并提供與電動汽車相關的其他解決方案。
沖片幾何形狀越來越復雜
舒勒技術日活動的參與者超過了 50 人。舒勒的 Simon Schmidt先生表示,電動汽車現在發展迅猛,汽車制造商紛紛加碼電動汽車產業。為了獲得更高的電動機效率,電動機沖片的幾何形狀變得越來越復雜,因此加工所需的模具長度也變得越來越長:“使用雙排模具進行加工是目前十分先進的技術。舒勒最新的高速沖 Smartline EV 3.8 工作臺長度從 2.7 米增加至 3.7 米,能夠加工最寬 630 mm 的帶料。”
同時,材料厚度也減少到了 0.35 mm 甚至 0.2 mm。“按照汽車行業對于電動汽車的新要求,目前的沖片厚度定義在 0.25 mm 到 0.275 mm。因此,壓力機供應商必須確保滑塊與工作臺擁有精準的定位與平行度。”對此,舒勒早在 15 年前就開發出了一套沖裁深度控制裝置 (PDC),能夠提供完美的滑塊定位與位置重復精度。“通過該裝置我們可以保證對材料進行精準沖裁,從而實現精準的模內自扣。舒勒的 Smartline 系列設備能夠在所有沖裁速度下以 +/-0.01 mm 的精度調節滑塊下死點位置。”
Smartline EV3.8 所配備的 3.7 米長滑塊為設備的設計帶來了很多挑戰。“對于小尺寸的 Smartline 設備,我們曾用激光測量滑塊的下降深度,設備會對沖裁深度進行校正,必要時每個行程都會自動校正。”但是對于 3.7 m 長的滑塊,就必須要考慮到撓度問題。”現在,舒勒在高級版 的沖裁深度控制系統中,我們把一個應變儀安裝到模具的沖頭架里,用來代替激光測量:“從而可以保持壓力恒定,并可以控制滑塊的撓度。無論沖片的形狀如何,都能夠獲得完美的定子和轉子疊壓效果。”
舒勒的目標是憑借 180 年的壓力機制造經驗,為客戶提供可靠、耐用且高精度的設備。 Schmidt 先生說道,“我們的設備能夠以每分鐘 250 沖次的速度全速運行,壓力最高可達 3150 kN,上模最大重量達 6 噸。”壓力機動態與靜態平衡度高,無需特殊的基坑:客戶僅需保證基坑的靜態承重達到 110 噸即可。“由于動態與靜態平衡度高,壓力機在全速運行的情況下,在垂直方向的位移小于 1mm。”因此,滑塊導軌、壓力點、連桿以及主軸承上沒有易損件,最大程度地降低了維護成本。
盡管壓力機的體積和質量都很大,舒勒僅使用了兩個承壓點,而非三個:“我們想要確切知道每個壓力點上的壓力,并確保可以檢測到該壓力。當有三個承壓點時,總會出現較小的偏差,最終出現磨損以及故障只是時間問題。采用兩個承壓點時,預定義的壓力就會達到協調狀態,從而將磨損降至最小。同時還能實現滑塊的高平行度:我們能夠保證從左到右每米的平行度為 0.04 mm。”
得益于 Smartline EV 3.8 采用的高級版 PDC、雙壓力點設計、四個預張緊滑塊導軌以及完美的靜態與動態平衡,模具的壽命能夠延長 30%。
模具生命周期內完成 1.8 億沖次
“對于高速鋼材料,在模具生命周期內能夠完成約 500 萬沖次,”模具制造商 AWBEA 的 Daniel Kittig 說道。“對于粉末冶金材料,能夠實現 3000 萬沖次,而對于碳化合金,則能夠實現約 1.8 億沖次,具體取決于工藝條件與材料特性。”在大多數情況下,AWEBA 的模具工程師首先與客戶溝通,了解客戶的想法。“基于此,我們開始進行設計,同時考量部件的幾何形狀、尺寸、復雜度以及公差。”
客戶要生產的沖片數量是決定采用單排、雙排或多排模具的主要因素,但這也取決于壓力機的性能:“我們的目標是為客戶提供最大程度的靈活性。即可以對工藝和材料問題導致的偏差和變化做出響應。因此我們集成了可調節嵌入功能。”
每個模具都采用獨立的設計。通常,首先通過模具進行預切割,以降低帶料的張力。接下來,逐步切割轉子的形狀,在這個過程中可能需要使用多個不同的工位。“如果僅使用一兩個工位,幾何形狀就會不太穩定。”Kittig 解釋道。
在之后的工位中,通過氣動沖裁對自扣操作進行分片。用于沖片自扣的壓印可以在近軸孔處、成型模之間或近直徑處進行:“我們也會在設計中使用黏膠工藝。”
“由于客戶的期待產量會越來越高,我們還采用了雙排和多排布局,完美適配舒勒的 EV 3.8 壓力機,”Kittig 說道。“這樣會獲得更高的材料利用率。”他說制造這種長度和精度的模具即使對于 AWEBA 也是一個巨大的挑戰:“整個模具的精度需要控制在幾微米內。”
降低電池殼體的制造成本
電池是導致電動汽車比燃油汽車價格更高的主要原因。但是,從現在的發展規模來看,到 2026 年左右這一情況將會發生改變:彭博公布的統計數據顯示,相比 2018 年電池占到總成本的 42%,到那時,這一比例將會降到 24%,電動汽車將比燃油汽車更具經濟性。
“對于現今的電動汽車市場,鋰離子電池的總需求量為 120 GWH,”舒勒的 Rainer Berkefeld 說道。“而到 2022 年,需求量將會超過 400 GWH,大約相當于需要制造 10 億個電池殼體。”根據 fka 與 Roland Berger 的數據顯示,在 2016 年至 2021 年之間,中國的電動汽車電池產能需求為 178 GWH,韓國為 98 GWH,日本為 87 GWH,美國為 74 GWH,德國為 18 GWH。
目前,市場上超過半數的電池采用圓柱形電池殼體(如特斯拉的電動汽車)或方形電池殼體(如豐田、三菱、本田、寶馬、大眾、奧迪、克萊斯勒、比亞迪、福特等廠商所采用的電池)。雖然圓柱形電池價格更低且商品化更成熟,但是需要復雜的電池管理系統。而方形電池則具有最佳的可擴展性,循環壽命更長,但是生產成本仍然很高。
“舒勒已開發出了一種全自動方形電池生產線,比目前的解決方案生產速度快 5 倍,同時還更節省材料,”Berkefeld先生 說道,“采用的是標準化設備以及在全球汽車和包裝行業普遍采用的成熟技術。”原材料采用鋁材料塊通過沖擊擠壓制成。當沖頭擠壓料塊時,材料會向相反方向流動。
之后,從兩側掃描預成形件,以檢測裂縫或變形。超出規格的產品將會被移除,以防在接下來的工藝中導致停機。在下一個步驟中,預成形件將會通過四個通道進入到一臺 300 噸后處理壓力機的一模四件模具中。除了變薄拉伸外,還可以集成精沖或整形校準等功能。
然后,將殼體倒置在切邊機中。剪切頭從內到外以擺動的方式工作,避免內部出現毛刺。在進行清洗、干燥與通過視像檢測后,就可以進行使用了。這臺高速沖設備目前已在一家大型電池制造商的工廠中投入使用,每年能夠生產超過 3000 萬個電池殼體。
舒勒同時也提供用于制造電池蓋的沖裁壓力機。它采用級進模,包含 12 個成形工位,如沖孔、切邊、壓印與分片等。
Internet
網站
www.schulergroup.com/drives_generators
www.schulergroup.com/battery
圖片注釋
關于舒勒集團 – www.schulergroup.com
舒勒為客戶提供從聯網壓力機到沖壓車間規劃的先進成形技術。除壓力機外,舒勒的產品范圍還包括面向整個金屬加工行業的自動化與軟件解決方案、模具、工藝技術以及相關服務。舒勒的客戶不僅包括汽車制造商及零部件供應商,還包括來自鍛造、家用電器和電子工業等諸多行業的公司。舒勒的壓力機為全球超過 180 個國家生產硬幣。作為創新系統解決方案供應商,我們也向全球客戶提供成形技術相關的數字化改造服務。2018 財年舒勒銷售額達到 12.12 億歐元。舒勒股份公司成立于 1839 年,總部位于德國格平根,在歐洲、中國、美國等全球 40 多個國家和地區的員工總數約為 6600 人。奧地利的安德里茨集團持有舒勒的多數股權。
沖片幾何形狀越來越復雜
舒勒技術日活動的參與者超過了 50 人。舒勒的 Simon Schmidt先生表示,電動汽車現在發展迅猛,汽車制造商紛紛加碼電動汽車產業。為了獲得更高的電動機效率,電動機沖片的幾何形狀變得越來越復雜,因此加工所需的模具長度也變得越來越長:“使用雙排模具進行加工是目前十分先進的技術。舒勒最新的高速沖 Smartline EV 3.8 工作臺長度從 2.7 米增加至 3.7 米,能夠加工最寬 630 mm 的帶料。”
同時,材料厚度也減少到了 0.35 mm 甚至 0.2 mm。“按照汽車行業對于電動汽車的新要求,目前的沖片厚度定義在 0.25 mm 到 0.275 mm。因此,壓力機供應商必須確保滑塊與工作臺擁有精準的定位與平行度。”對此,舒勒早在 15 年前就開發出了一套沖裁深度控制裝置 (PDC),能夠提供完美的滑塊定位與位置重復精度。“通過該裝置我們可以保證對材料進行精準沖裁,從而實現精準的模內自扣。舒勒的 Smartline 系列設備能夠在所有沖裁速度下以 +/-0.01 mm 的精度調節滑塊下死點位置。”
Smartline EV3.8 所配備的 3.7 米長滑塊為設備的設計帶來了很多挑戰。“對于小尺寸的 Smartline 設備,我們曾用激光測量滑塊的下降深度,設備會對沖裁深度進行校正,必要時每個行程都會自動校正。”但是對于 3.7 m 長的滑塊,就必須要考慮到撓度問題。”現在,舒勒在高級版 的沖裁深度控制系統中,我們把一個應變儀安裝到模具的沖頭架里,用來代替激光測量:“從而可以保持壓力恒定,并可以控制滑塊的撓度。無論沖片的形狀如何,都能夠獲得完美的定子和轉子疊壓效果。”
舒勒的目標是憑借 180 年的壓力機制造經驗,為客戶提供可靠、耐用且高精度的設備。 Schmidt 先生說道,“我們的設備能夠以每分鐘 250 沖次的速度全速運行,壓力最高可達 3150 kN,上模最大重量達 6 噸。”壓力機動態與靜態平衡度高,無需特殊的基坑:客戶僅需保證基坑的靜態承重達到 110 噸即可。“由于動態與靜態平衡度高,壓力機在全速運行的情況下,在垂直方向的位移小于 1mm。”因此,滑塊導軌、壓力點、連桿以及主軸承上沒有易損件,最大程度地降低了維護成本。
盡管壓力機的體積和質量都很大,舒勒僅使用了兩個承壓點,而非三個:“我們想要確切知道每個壓力點上的壓力,并確保可以檢測到該壓力。當有三個承壓點時,總會出現較小的偏差,最終出現磨損以及故障只是時間問題。采用兩個承壓點時,預定義的壓力就會達到協調狀態,從而將磨損降至最小。同時還能實現滑塊的高平行度:我們能夠保證從左到右每米的平行度為 0.04 mm。”
得益于 Smartline EV 3.8 采用的高級版 PDC、雙壓力點設計、四個預張緊滑塊導軌以及完美的靜態與動態平衡,模具的壽命能夠延長 30%。
模具生命周期內完成 1.8 億沖次
“對于高速鋼材料,在模具生命周期內能夠完成約 500 萬沖次,”模具制造商 AWBEA 的 Daniel Kittig 說道。“對于粉末冶金材料,能夠實現 3000 萬沖次,而對于碳化合金,則能夠實現約 1.8 億沖次,具體取決于工藝條件與材料特性。”在大多數情況下,AWEBA 的模具工程師首先與客戶溝通,了解客戶的想法。“基于此,我們開始進行設計,同時考量部件的幾何形狀、尺寸、復雜度以及公差。”
客戶要生產的沖片數量是決定采用單排、雙排或多排模具的主要因素,但這也取決于壓力機的性能:“我們的目標是為客戶提供最大程度的靈活性。即可以對工藝和材料問題導致的偏差和變化做出響應。因此我們集成了可調節嵌入功能。”
每個模具都采用獨立的設計。通常,首先通過模具進行預切割,以降低帶料的張力。接下來,逐步切割轉子的形狀,在這個過程中可能需要使用多個不同的工位。“如果僅使用一兩個工位,幾何形狀就會不太穩定。”Kittig 解釋道。
在之后的工位中,通過氣動沖裁對自扣操作進行分片。用于沖片自扣的壓印可以在近軸孔處、成型模之間或近直徑處進行:“我們也會在設計中使用黏膠工藝。”
“由于客戶的期待產量會越來越高,我們還采用了雙排和多排布局,完美適配舒勒的 EV 3.8 壓力機,”Kittig 說道。“這樣會獲得更高的材料利用率。”他說制造這種長度和精度的模具即使對于 AWEBA 也是一個巨大的挑戰:“整個模具的精度需要控制在幾微米內。”
降低電池殼體的制造成本
電池是導致電動汽車比燃油汽車價格更高的主要原因。但是,從現在的發展規模來看,到 2026 年左右這一情況將會發生改變:彭博公布的統計數據顯示,相比 2018 年電池占到總成本的 42%,到那時,這一比例將會降到 24%,電動汽車將比燃油汽車更具經濟性。
“對于現今的電動汽車市場,鋰離子電池的總需求量為 120 GWH,”舒勒的 Rainer Berkefeld 說道。“而到 2022 年,需求量將會超過 400 GWH,大約相當于需要制造 10 億個電池殼體。”根據 fka 與 Roland Berger 的數據顯示,在 2016 年至 2021 年之間,中國的電動汽車電池產能需求為 178 GWH,韓國為 98 GWH,日本為 87 GWH,美國為 74 GWH,德國為 18 GWH。
目前,市場上超過半數的電池采用圓柱形電池殼體(如特斯拉的電動汽車)或方形電池殼體(如豐田、三菱、本田、寶馬、大眾、奧迪、克萊斯勒、比亞迪、福特等廠商所采用的電池)。雖然圓柱形電池價格更低且商品化更成熟,但是需要復雜的電池管理系統。而方形電池則具有最佳的可擴展性,循環壽命更長,但是生產成本仍然很高。
“舒勒已開發出了一種全自動方形電池生產線,比目前的解決方案生產速度快 5 倍,同時還更節省材料,”Berkefeld先生 說道,“采用的是標準化設備以及在全球汽車和包裝行業普遍采用的成熟技術。”原材料采用鋁材料塊通過沖擊擠壓制成。當沖頭擠壓料塊時,材料會向相反方向流動。
之后,從兩側掃描預成形件,以檢測裂縫或變形。超出規格的產品將會被移除,以防在接下來的工藝中導致停機。在下一個步驟中,預成形件將會通過四個通道進入到一臺 300 噸后處理壓力機的一模四件模具中。除了變薄拉伸外,還可以集成精沖或整形校準等功能。
然后,將殼體倒置在切邊機中。剪切頭從內到外以擺動的方式工作,避免內部出現毛刺。在進行清洗、干燥與通過視像檢測后,就可以進行使用了。這臺高速沖設備目前已在一家大型電池制造商的工廠中投入使用,每年能夠生產超過 3000 萬個電池殼體。
舒勒同時也提供用于制造電池蓋的沖裁壓力機。它采用級進模,包含 12 個成形工位,如沖孔、切邊、壓印與分片等。
Internet
網站
www.schulergroup.com/drives_generators
www.schulergroup.com/battery
圖片注釋
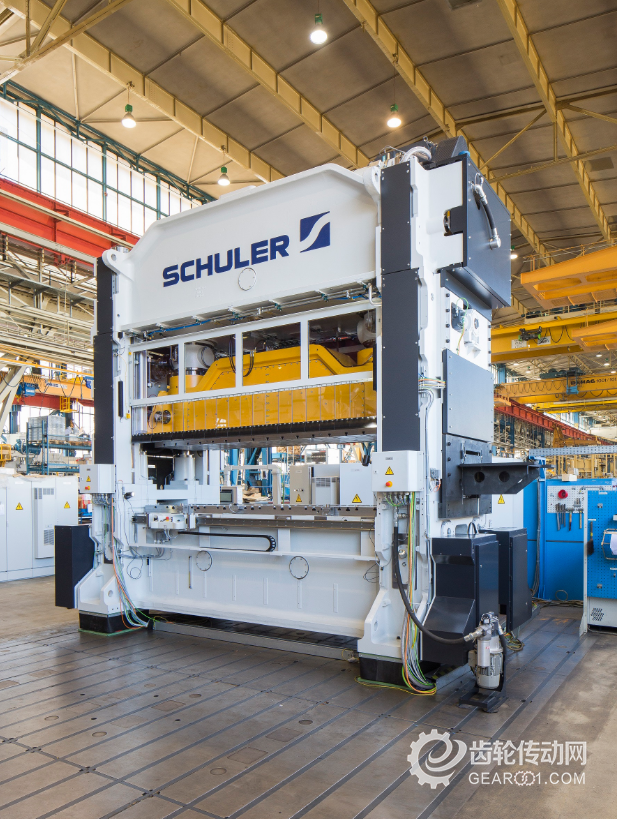
圖1: 舒勒在德國格平根總部展示了最新研發的高速沖 Smartline EV 3.8。
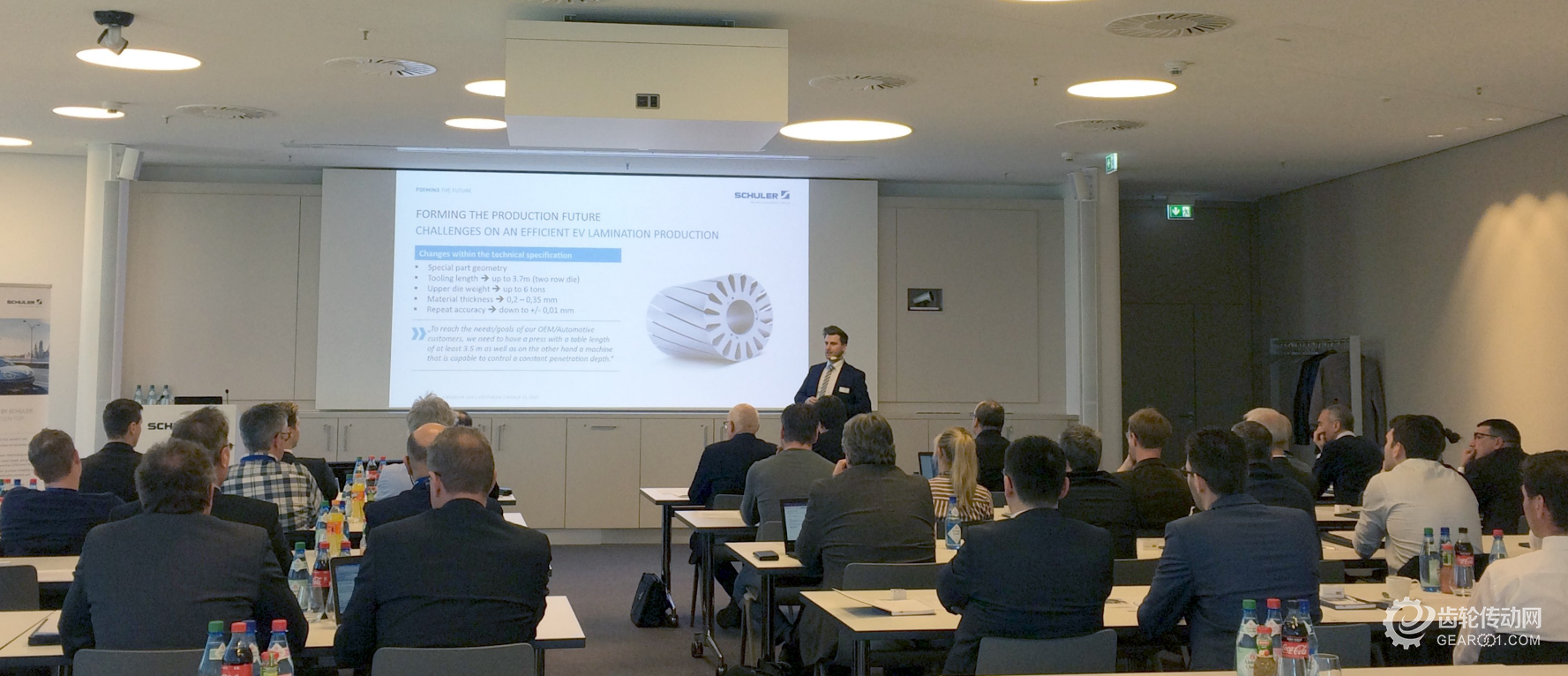
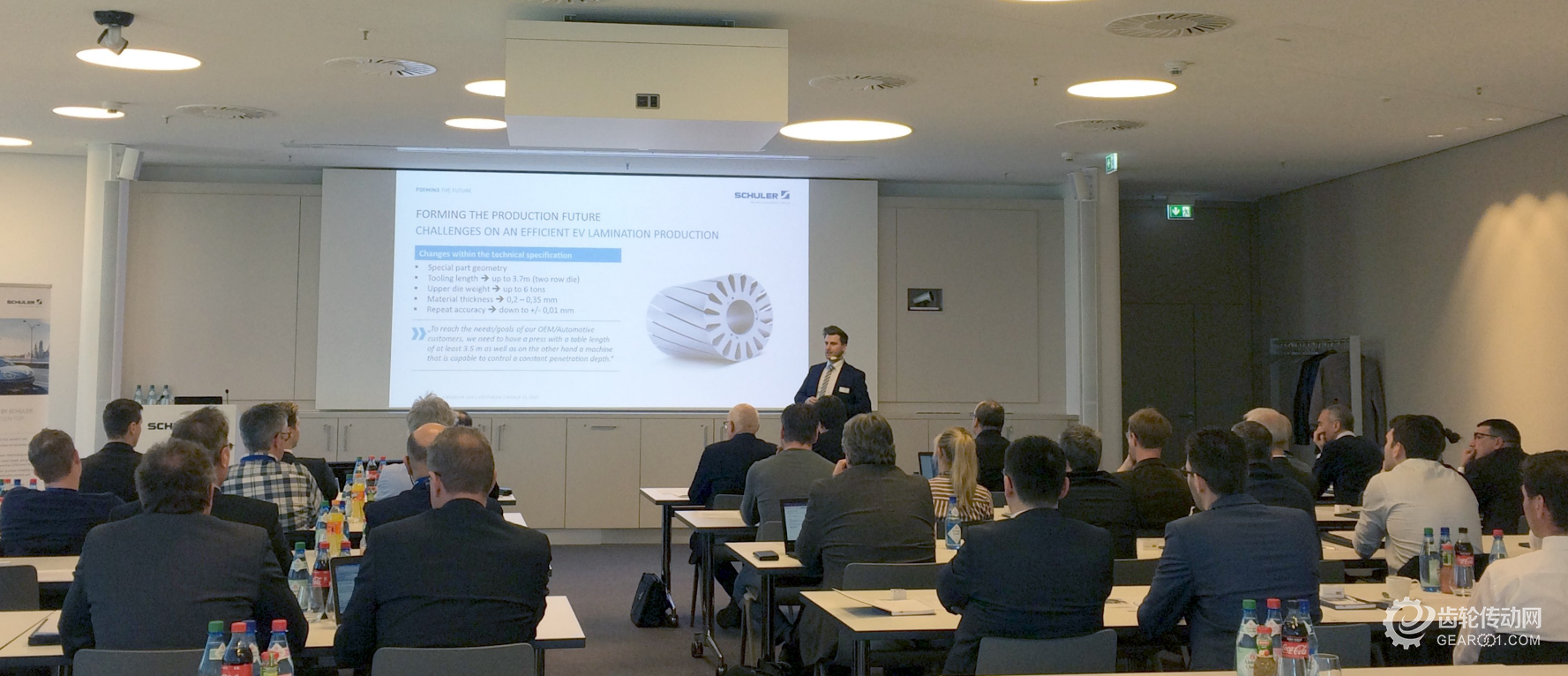
圖2: “舒勒最新的高速沖 Smartline EV 3.8 的工作臺長度從 2.7 米增加至 3.7 米,能夠加工最寬 630 mm 的帶料。”舒勒 Simon Schmidt 說道。
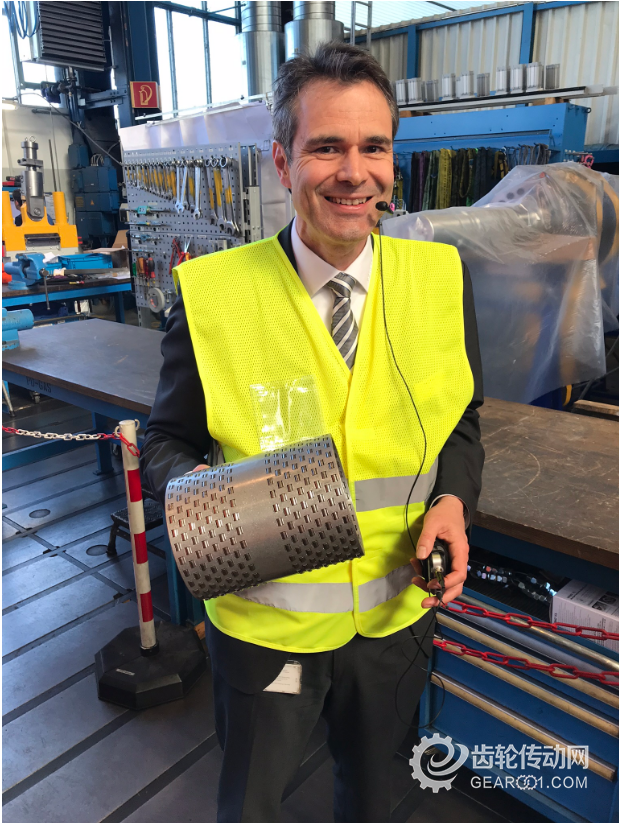
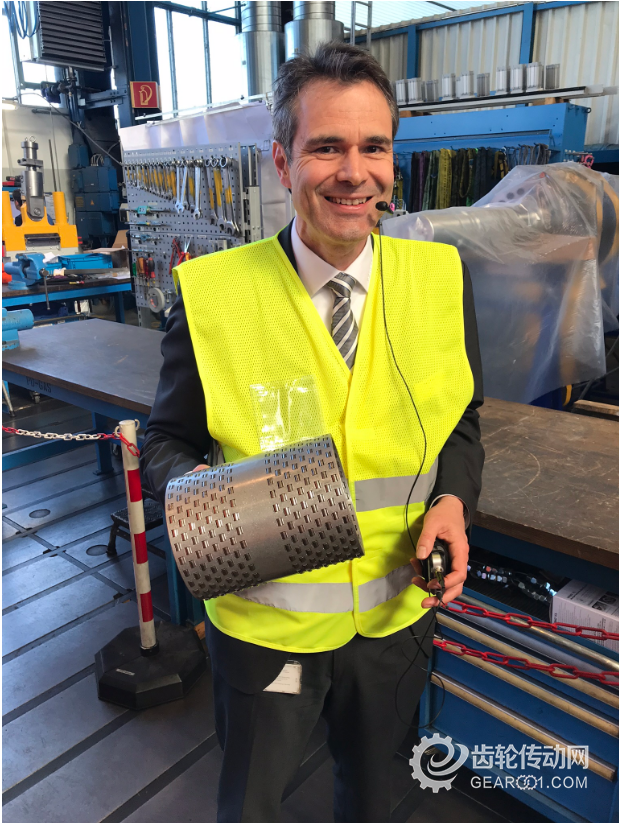
圖3: 舒勒電動汽車相關業務負責人 Markus Roever先生 在展示內部有上千個輥子的滑塊導軌。
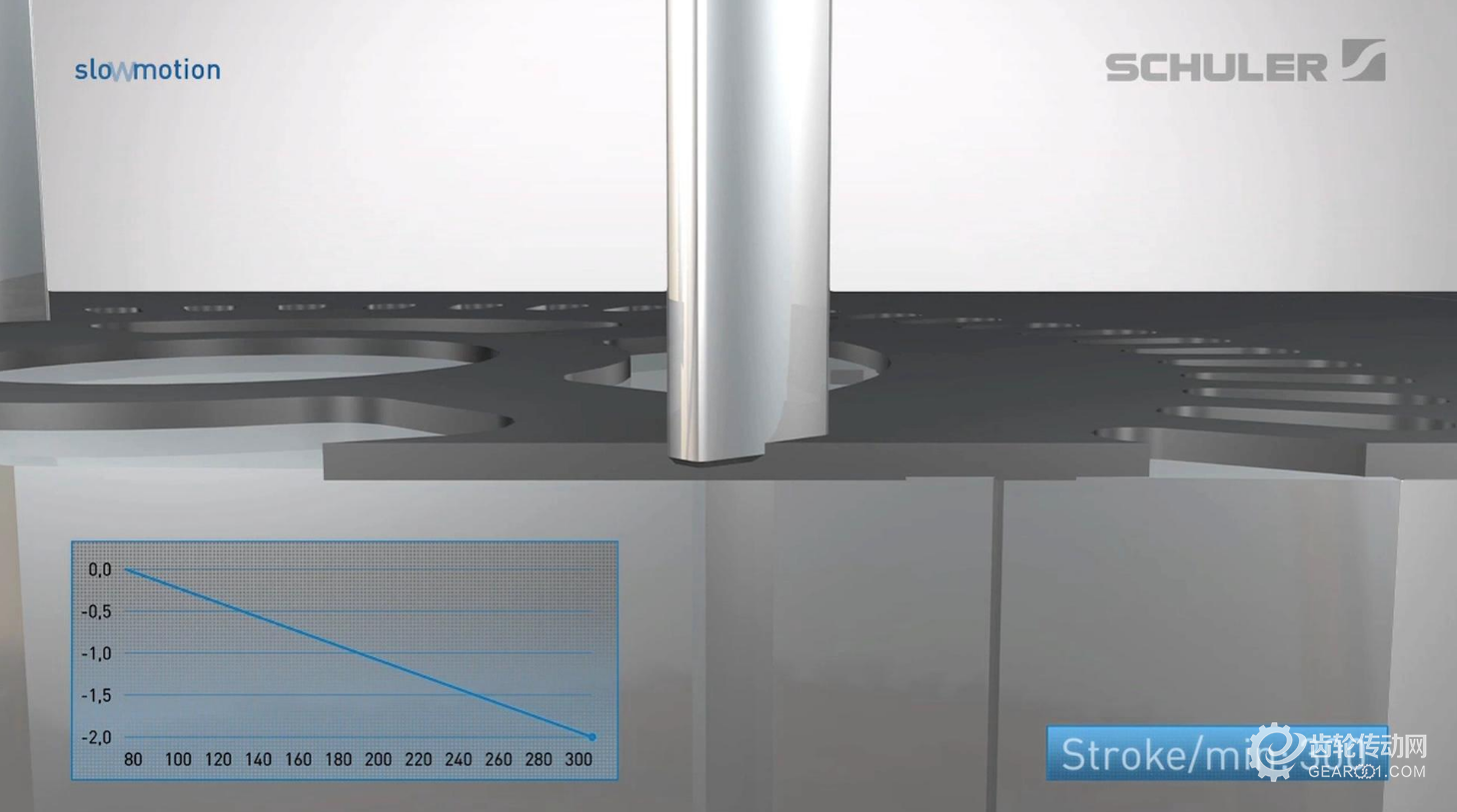
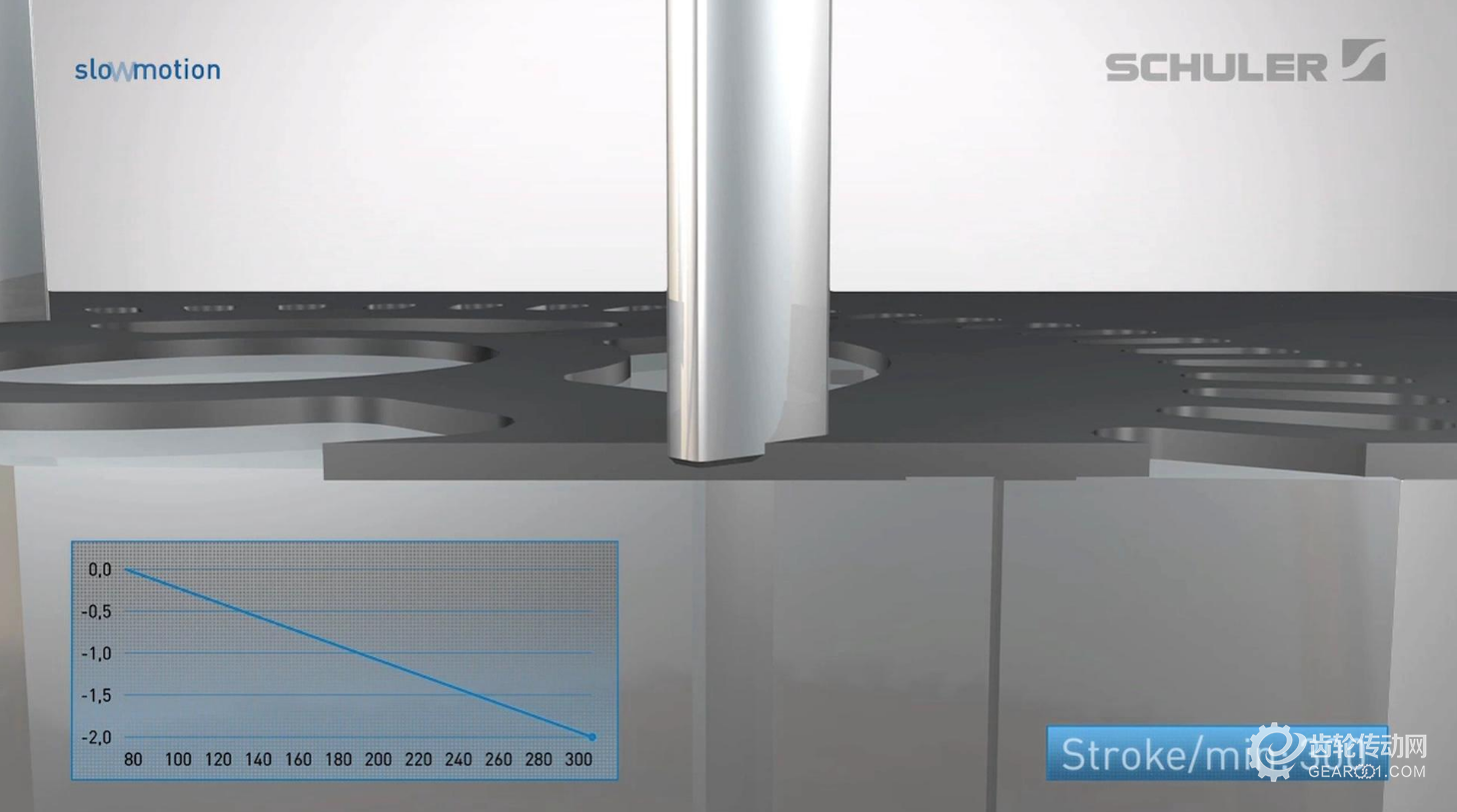
圖4: 舒勒開發出了一套沖裁深度控制裝置 (PDC),保證了滑塊相對于工作臺的重復位置精度。
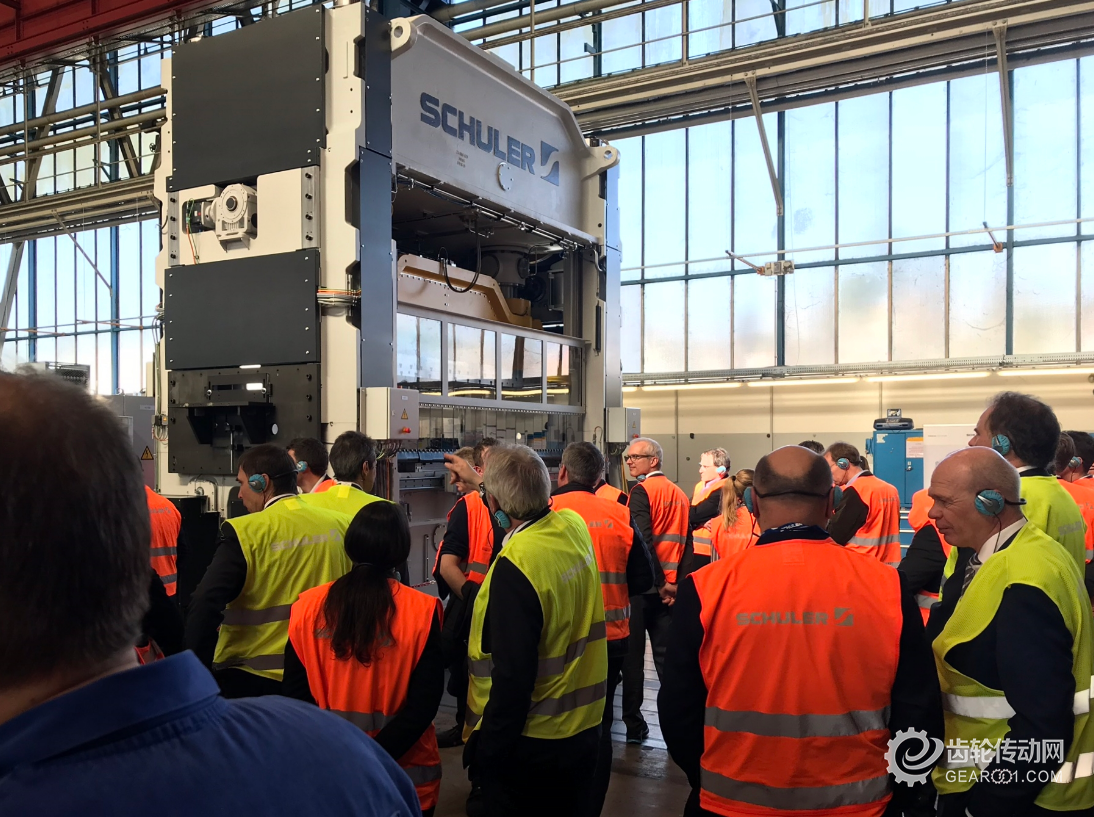
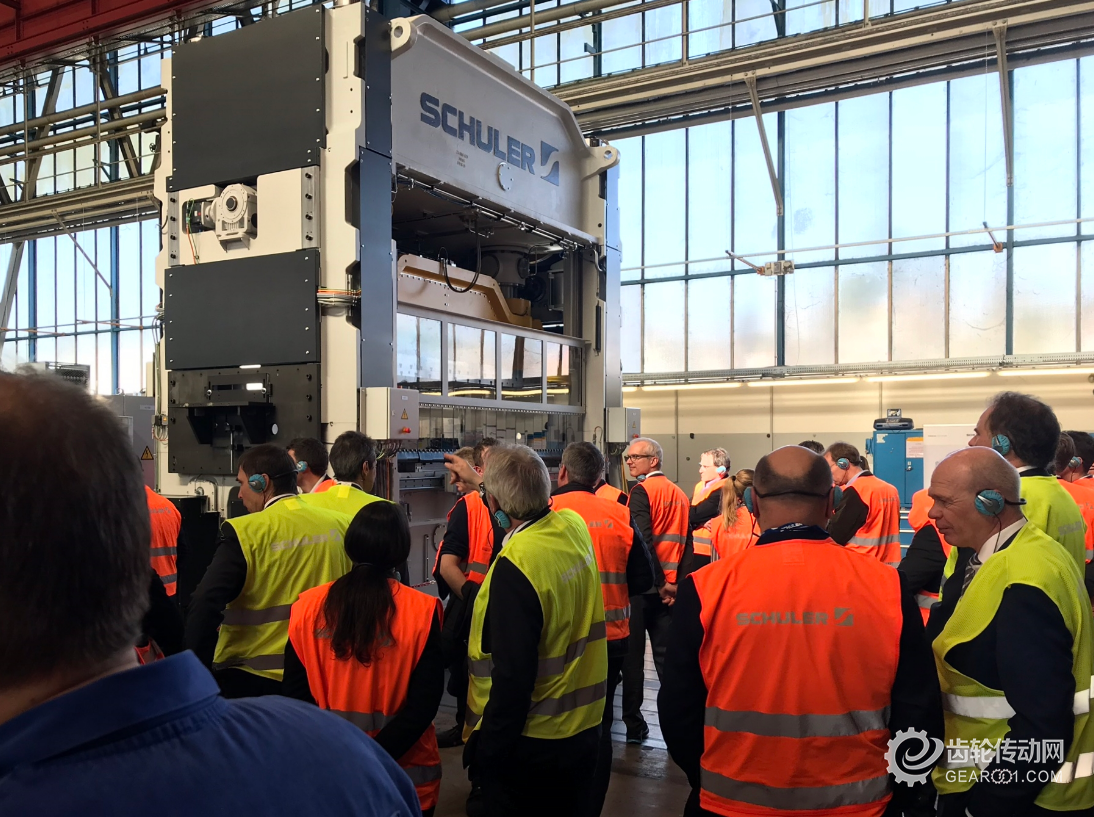
圖5: 舒勒技術日活動的參與者超過了 50 人。
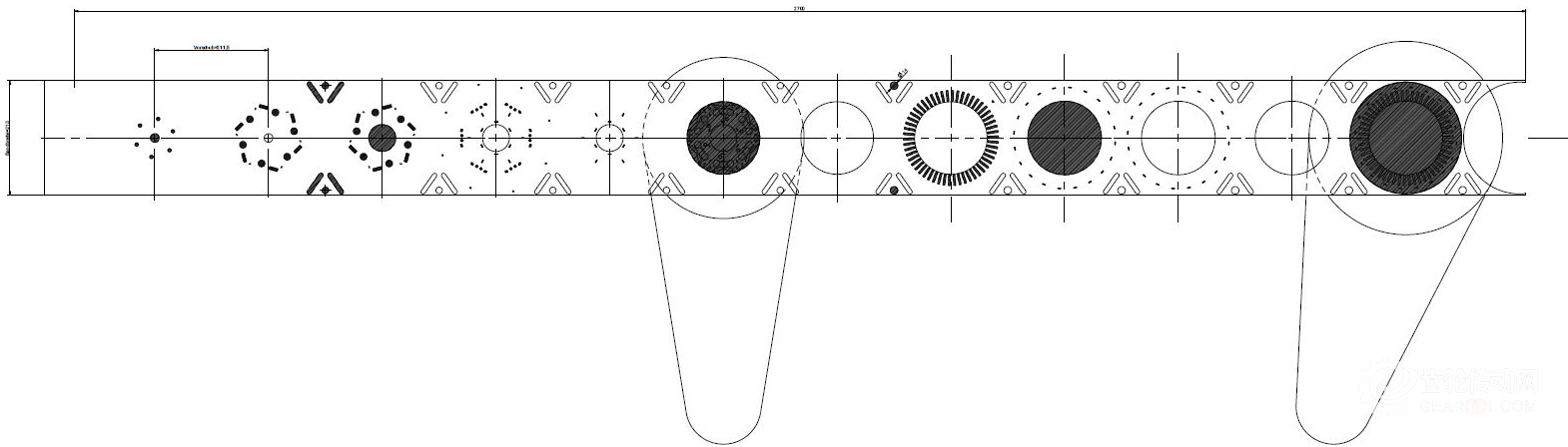
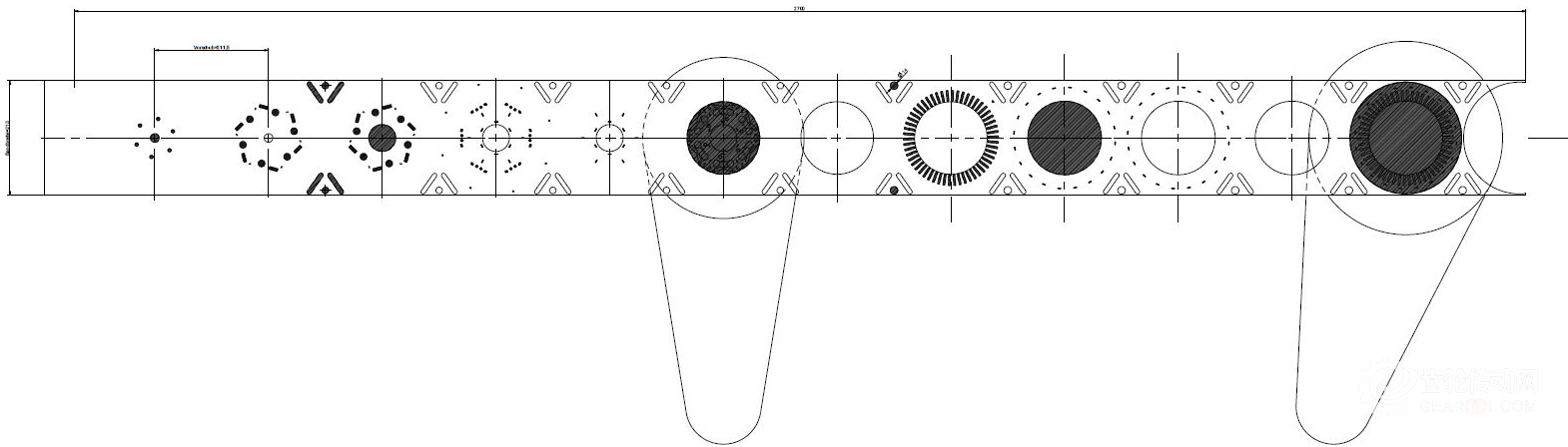
圖6: 客戶要生產的沖片數量是決定采用單排或雙排模具的主要因素。
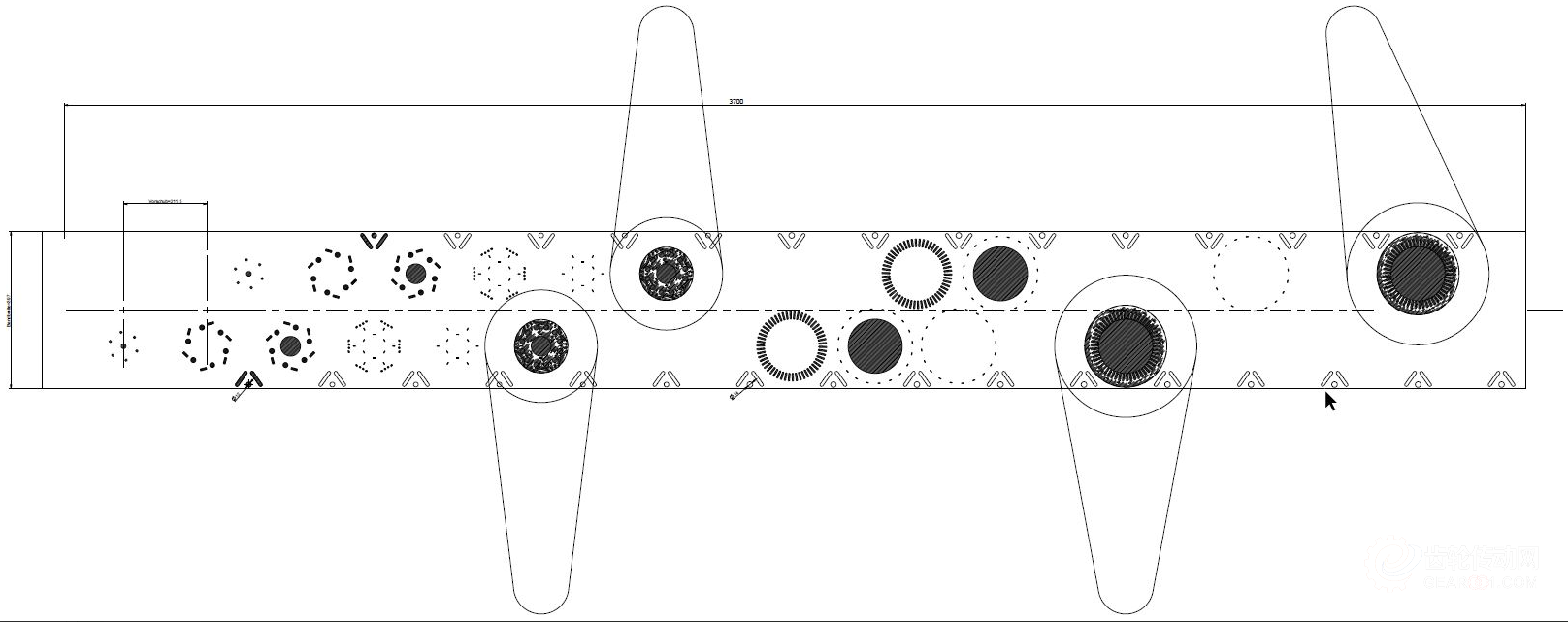
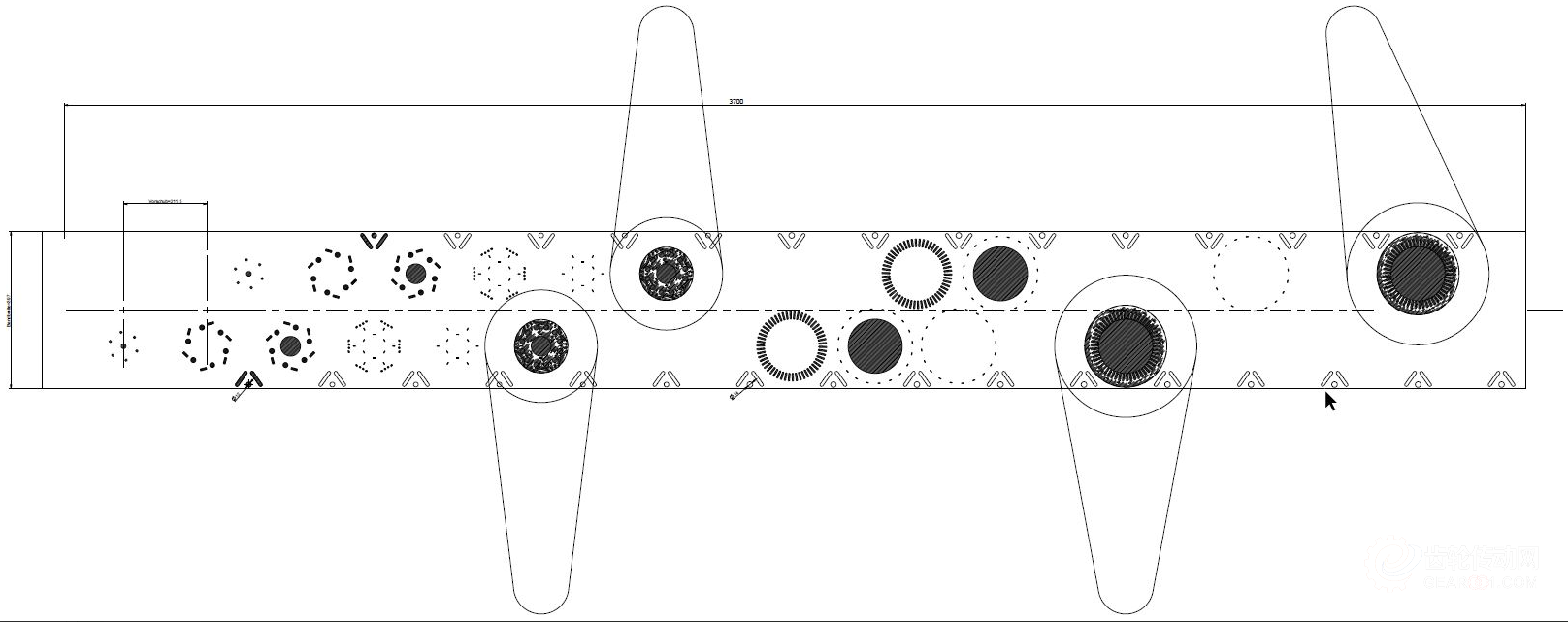
圖7: 針對更高的產能要求,AWEBA 也開發了雙排布局的模具,完美適配舒勒的 Smartline EV 3.8 高速沖。
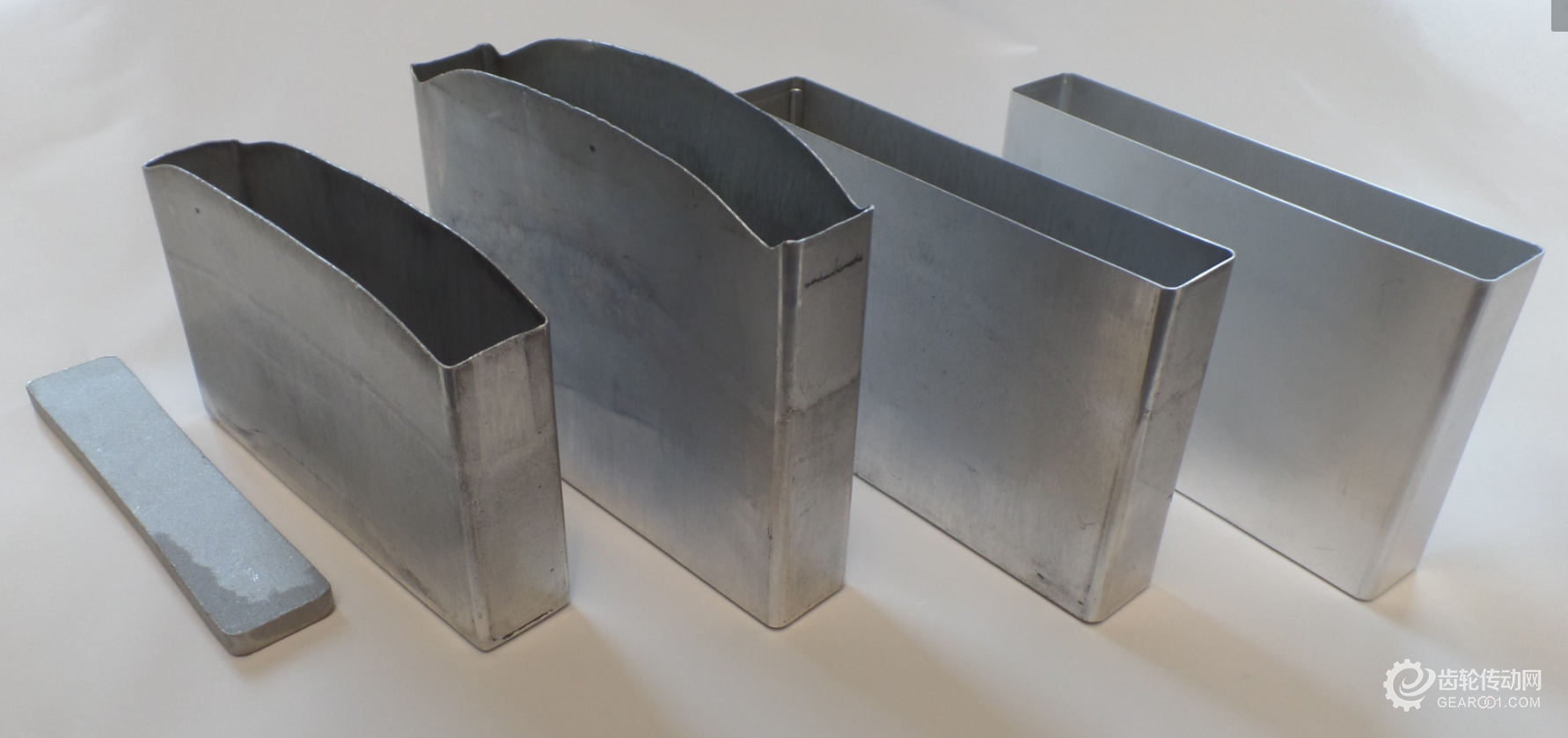
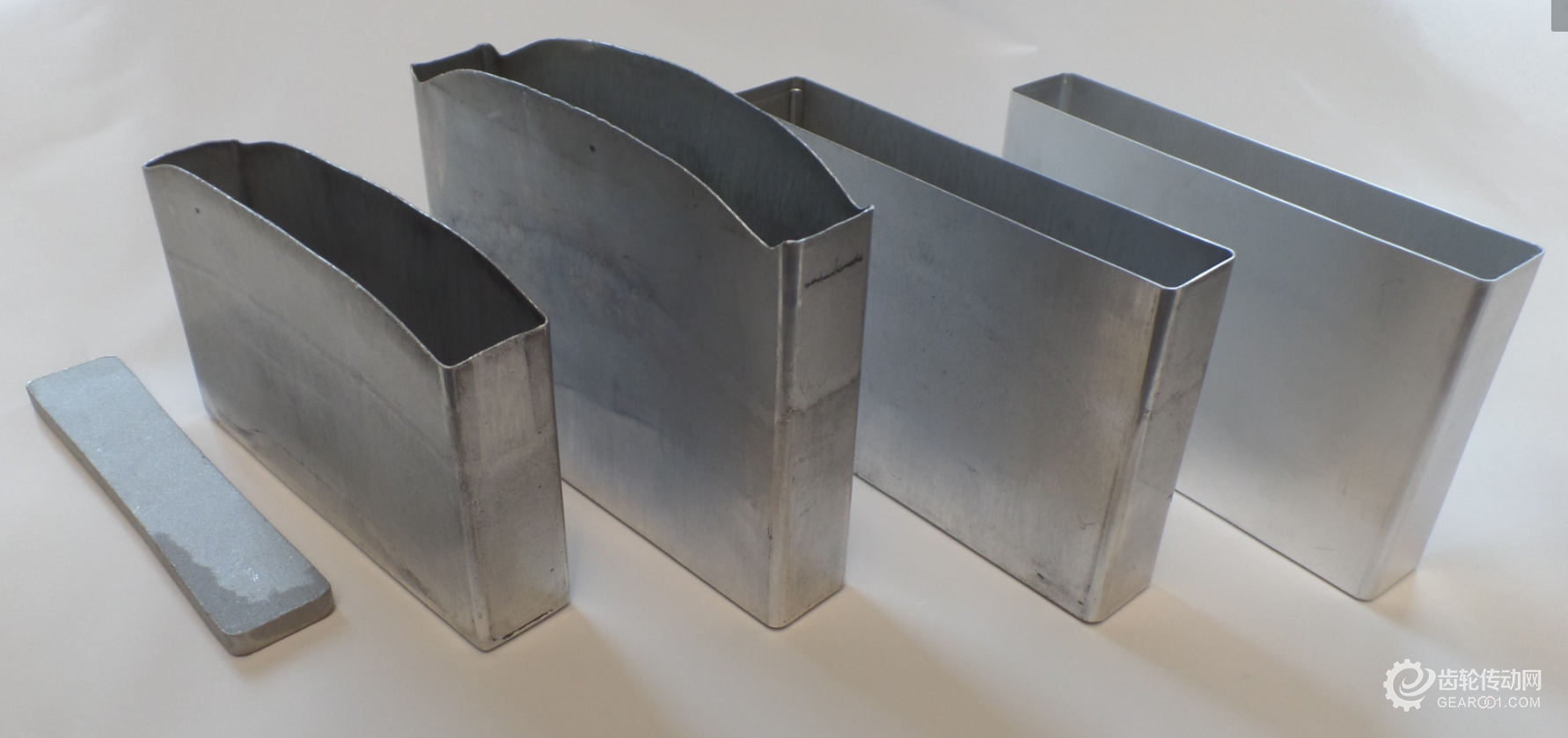
圖8: 電池殼體原材料采用鋁材料塊(左)通過沖擊擠壓制成,并經過成形、處理、切邊、清洗等工藝進行加工。
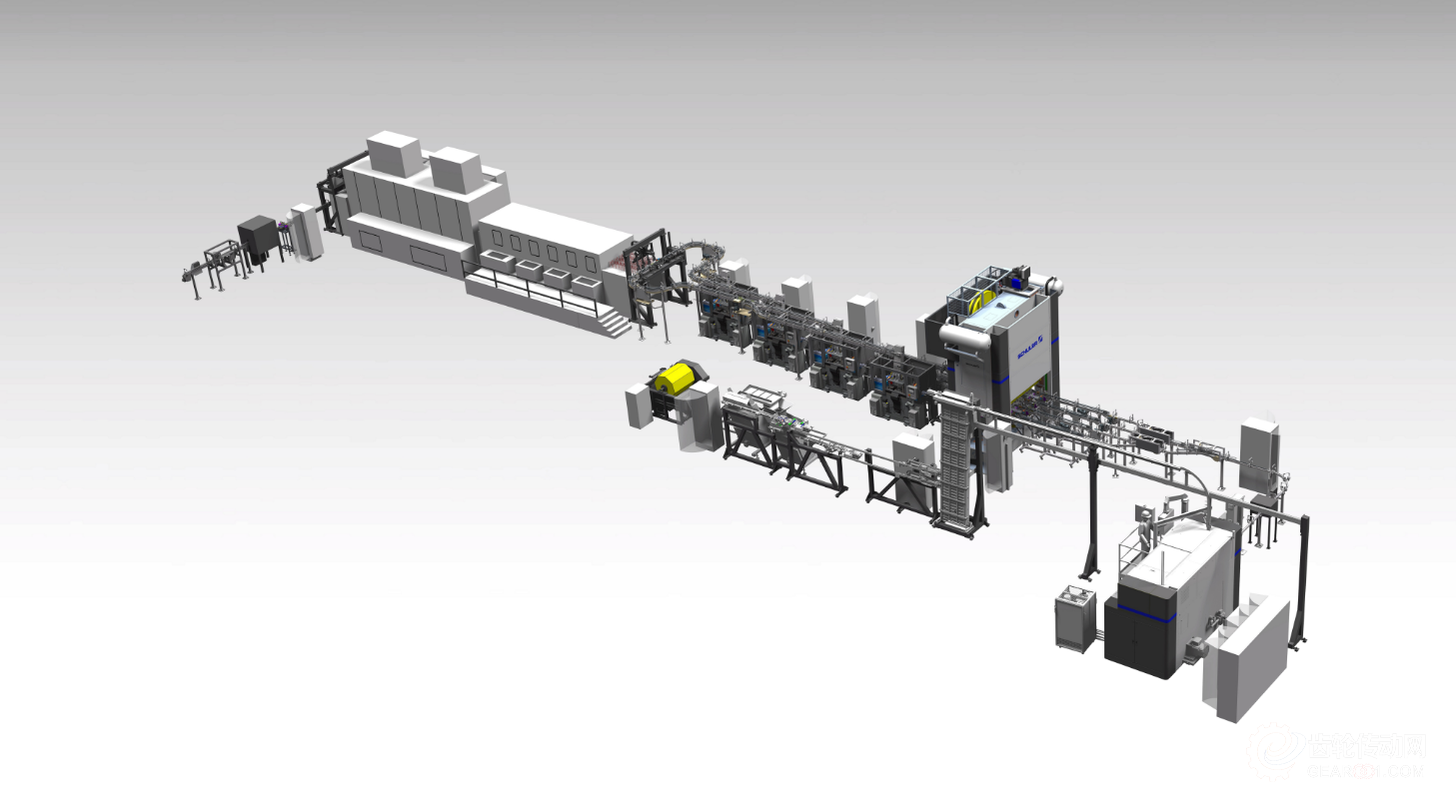
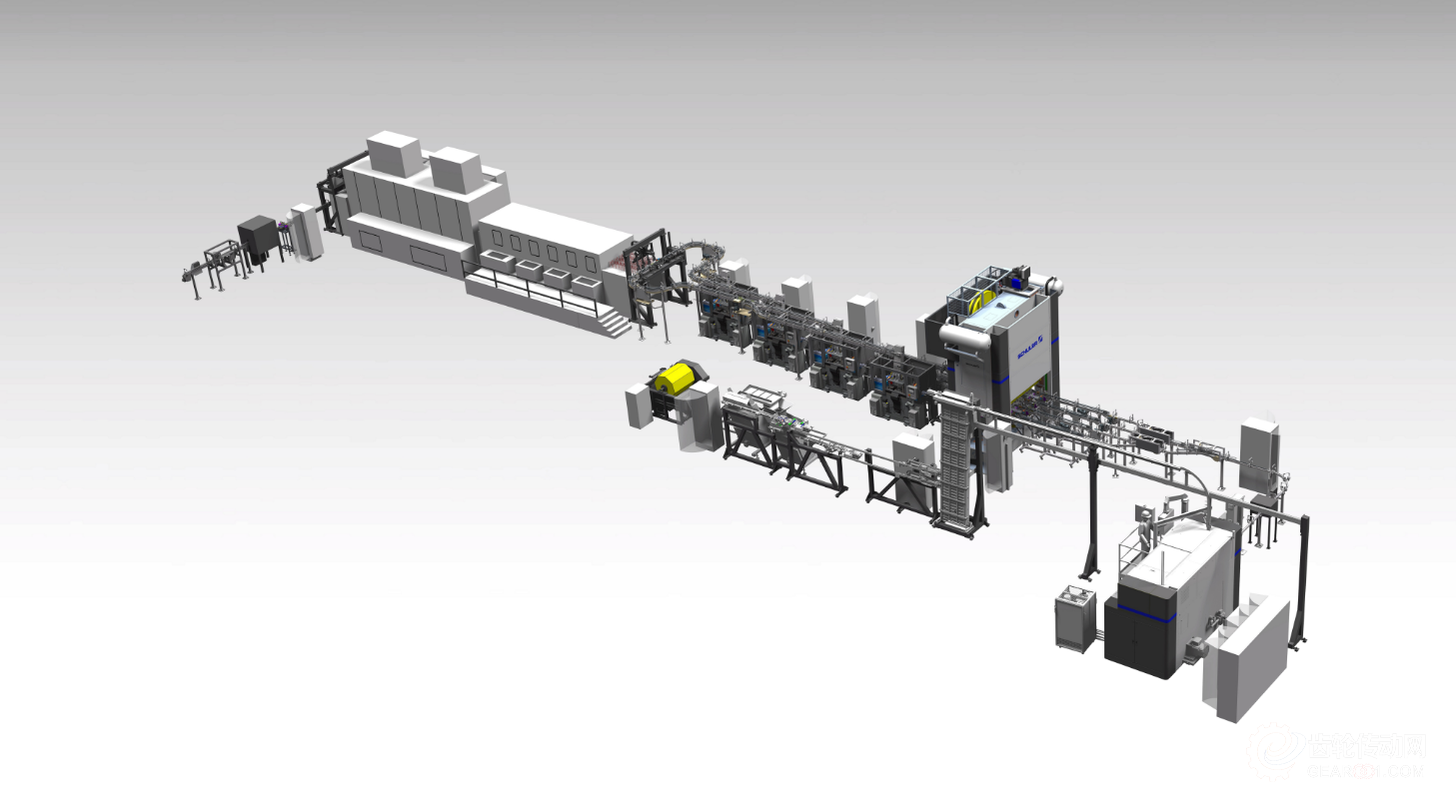
s 圖9: 生產線由沖擊擠壓機(右下)、精沖整形壓力機、切邊機、清洗裝置和烘干裝置組成。
請注明所有照片均出自舒勒。
關于舒勒集團 – www.schulergroup.com
舒勒為客戶提供從聯網壓力機到沖壓車間規劃的先進成形技術。除壓力機外,舒勒的產品范圍還包括面向整個金屬加工行業的自動化與軟件解決方案、模具、工藝技術以及相關服務。舒勒的客戶不僅包括汽車制造商及零部件供應商,還包括來自鍛造、家用電器和電子工業等諸多行業的公司。舒勒的壓力機為全球超過 180 個國家生產硬幣。作為創新系統解決方案供應商,我們也向全球客戶提供成形技術相關的數字化改造服務。2018 財年舒勒銷售額達到 12.12 億歐元。舒勒股份公司成立于 1839 年,總部位于德國格平根,在歐洲、中國、美國等全球 40 多個國家和地區的員工總數約為 6600 人。奧地利的安德里茨集團持有舒勒的多數股權。